- FMA
- The Fabricator
- FABTECH
- Canadian Metalworking
Digital Readouts
- February 1, 2010
- Article
- Automation and Software
Operator error is, for all practical purposes, eliminated with a digital readout (DRO), according to the experts. Calculations are performed automatically by the system, and the required positions automatically prompted on the screen.
In some cases, a DRO can even increase the productivity of a manual machine by 200 percent or more.
“Most customers find they can do twice as much with a DRO-equipped manual machine, yet reduce scrap by more than half,” explained Fagor Automation Marketing Manager Todd Drane. “Studies have shown a manual DRO will pay for itself in as little as a week or two, and most do not take generated scrap into account. In many cases, a DRO system pays for itself in a single day of manufacturing.”
When working just with the machine’s dials, operators encounter backlash and therefore have to go the same direction all of the time and keep track of revolutions. This means there is a bigger chance of making a mistake, and operators have to do much more thinking during the process.
A DRO eliminates guesswork, increases reliability, and lessens the chance of making a mistake.
A DRO-equipped machine is also faster because operators don’t have to creep up to the number they need to reach. Instead they can very quickly go right to it.
Part quality also can be greatly improved in part because of the feed rate display. This feature displays the actual axis feed rate, enabling spindle speeds to be adjusted on-the-fly. These quick and easy cutting speed adjustments ensure a smooth and accurate cut.
“In addition, with the precision of a DRO system, the right cut is always made, thus eliminating recuts due to inaccuracies,” said Drane.
Less scrap is also created because operators no longer have to count revolutions.
Benefits to the Operator
Aside from the fact that the DRO does a lot of the calculations for the operator, safety is also improved on machines that are equipped with a DRO.
“One primary safety feature is automatic detection of the feedback system that totally eliminates any setup error by the maintenance department,” said Drane. “With a Fagor DRO, you are automatically going to be counting your position correctly, which instantly makes your machine safer. We also have a positional, visual bar graph that shows the operator how much farther he has to go before reaching the programmed position.”
This helps eliminate overshooting, which can cause dangerous tool breakage.
“In addition, for safety alone, we added a buzzer to our Innova 40i TrueVision DRO that instantly alarms the operator of various errors, such as travel limits being passed,” said Drane.
Improved graphics in the latest generation of DROs has had an impact on productivity.
In the past, if the DRO was mounted on the headstock of a machine, an operator at the tailstock often could not see the LED display. This meant that the operator could not see his axes position and would have to stop and start to continually check on the position.
“The real value is in the ability to bring the technology in a more simplistic method to the user,” said Drane. “With a LCD TFT monitor, we can bring a bolt-hole cycle to the customer in a conversational-type display with an intuitive color graphic help screen right on the display.”
Efficiency increases when an operator is spending more time cutting and less time working with the DRO, he added.
Programming and Cycles
Many different types of cycles today come with a DRO. Depending on the type of machine (mill, lathe, grinder, CMM) that the readout is attached to, these can include threading, bolt-hole, linear-hole, grid-hole, and taper cycles.
These cycles are a necessity simply because if they are not present, the operator must spend nonmachining time calculating the positions and then keying them in. With these cycles, the DRO automatically calculates the positions based on a few variables.
To do an operation such as a bolt-hole pattern without a cycle could take an operator three or four times longer than with the feature.
“A customer, from first power-on of the DRO, can have a bolt-hole cycle programmed and physically be cutting within two minutes with the DRO bolt-hole cycle,” said Drane. “Without it, the setup process is capable of taking anywhere from 10 minutes to even hours before they even begin cutting.”
Needed Skill Set
When dealing with the mathematics of machining, even the slightest miscalculation can lead to wasted time, material, and money.
“Most employers assume that their workers can do the necessary calculations, but simply by adding a DRO to the machine, they can reduce any human error however unlikely,” explained Scott Warner, Canadian regional manager for HEIDENHAIN Corp.
With a DRO on their manual machine, shops can even compete with more difficult work because of the new features.
“The big advancement in the past five to 10 years has been in the ease of use of these features,” said Warner. “With new graphical displays, your work is literally in front of your eyes. This graphical nature of the new DROs makes it much easier to set up an operation.”
DROs are not limited to these features in terms of productivity improvement, part quality improvement, and cost reduction.
Tool compensation technology enables the DRO to automatically calculate the correct tool path based on the tool variables, which can greatly simplify the operator’s programming thought process.
Also, multiple work offsets allow the operator to change coordinate systems quickly for different operations on the same part or separate, side-by-side parts.
All of these features increase not just efficiency and speed by allowing the DRO to calculate items such as the tool diameter, they also allow the machine to stop while in operation and rezero a part for a new part or feature.
Inspection and Quality
New tools for DROs also allow this technology to be used to speed operations such as edge finding.
The HEIDENHAIN KT accessory, for example, is a 3-D triggering edge finder. The cylindrical stylus is spring-mounted and is deflected when it comes in contact with the workpiece, and the edge finder sends a signal to the DRO.
This allows the operator to set reference points very quickly and without worrying about over travel. This allows the operator to be more consistent.
“There is more value added to the part when it has been accurately measured,” said Warner. “Smaller companies that need to be more competitive in their industry can find this tool very useful for speeding up the finding datum and workpiece centerpoints.”
With this device operators do not have to slow down when they are approaching the edge because the probe detects the edge and sends the data back to the DRO. This replaces slow and mechanical edge finders especially useful for determining the edge of circles.
“Operators no longer need to move slowly as they approach the edge and physically make contact,” said Warner. “This really helps to produce better repeatability for each and every job.”
A DRO also can be used on manual coordinate measuring machines (CMMs) and can capture 2-D and 3-D features with its measuring computer functionality.
Many older CMMs are known to be in good mechanical condition, but are constrained by outdated software. By adding a DRO such as the HEIDENHAIN ND 1400 Quadra-Chek, these CMMs can still have a long life span.
This DRO offers predefined features (point, line, circle, slot, rectangle, plane, cylinder, cone, sphere, distance, and angle) within its system. A program also selects the feature which best matches the shape implied by the points probed. For features such as cones, the screen displays the feature in three dimensions. Also, this system allows operators to create or automatically record measuring programs for repeated same-part measurements, graphically taking the operator to the next measurement position during the program run.
For more information, visit www.fagorautomation.com and www.heidenhain.com.
subscribe now
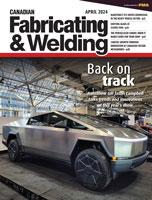
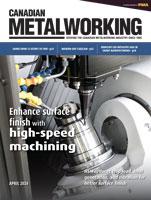
Keep up to date with the latest news, events, and technology for all things metal from our pair of monthly magazines written specifically for Canadian manufacturers!
Start Your Free Subscription- Trending Articles
- Industry Events
MME Winnipeg
- April 30, 2024
- Winnipeg, ON Canada
CTMA Economic Uncertainty: Helping You Navigate Windsor Seminar
- April 30, 2024
- Windsor, ON Canada
CTMA Economic Uncertainty: Helping You Navigate Kitchener Seminar
- May 2, 2024
- Kitchener, ON Canada
Automate 2024
- May 6 - 9, 2024
- Chicago, IL
ANCA Open House
- May 7 - 8, 2024
- Wixom, MI