- FMA
- The Fabricator
- FABTECH
- Canadian Metalworking
A guide to titanium-based coatings
A look at the properties and characteristics of TiN, TiCN, TiAlN, and AlTiN
- January 28, 2019
- Article
- Cutting Tools
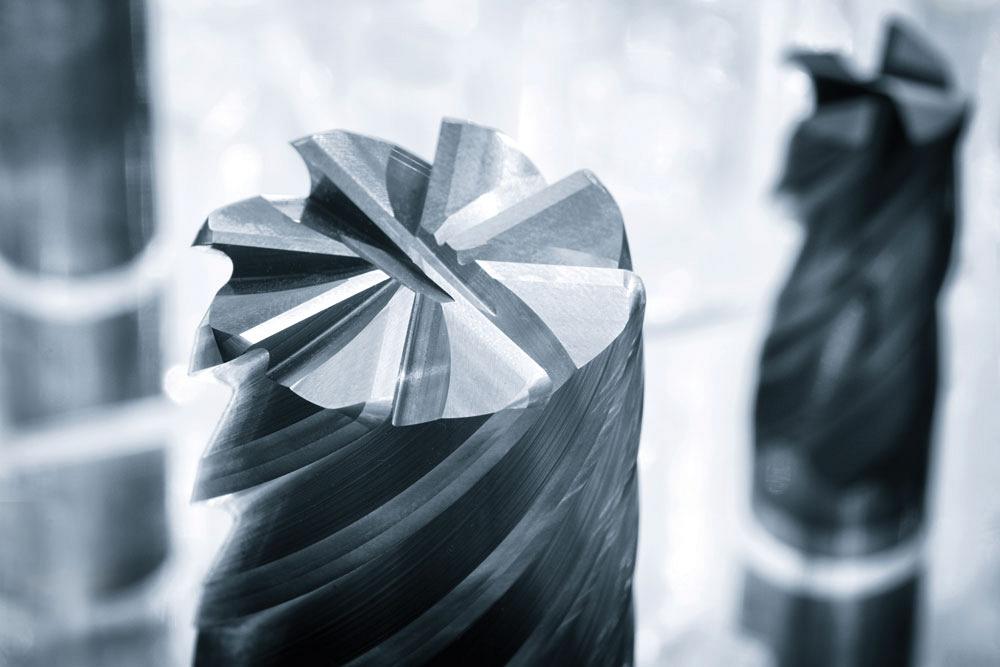
Titanium carbonitride (TiCN) is the second iteration after the development of TiN and is bluish-grey in colour with a Vickers hardness of up to 3,000.
Coatings help extend the life of cutting tools, provide better thermal protection, and increase lubricity to lessen material galling. Coatings have gone through a series of developments over the last couple of decades, particularly in response to the increasing demands of the manufacturing sector. With more and more machine shops venturing into high-speed machining, dry machining, and machining of difficult-to-cut alloys, cutting tool coatings have become increasingly necessary.
EARLY DEVELOPMENTS
Physical vapour deposition (PVD) coatings originated around titanium in the early 1970s and ’80s. At that time titanium nitride (TiN) was brought to market. The coating is a titanium base coating with nitrogen being the carrier combining with titanium after it’s been vapourized in a vacuum chamber. The two combined elements provide additional wear resistance.
TiN was harder than the typical high-speed steels that were being coated at the time, giving it better thermal characteristics and higher temperatures before there were issues with the substrate. It is one of the most common coatings for general-purpose tools. TiN has a coating thickness of 2 to 4 microns and a Vickers hardness of up to 2,100. This coating has a low coefficient of friction (0.4) and an operating temperature of approximately 1,100 degrees F.
TiN is considered a general-purpose coating, with an amber-gold colour, and is still common on the market for most general-use cutting tools, something that can be used in about any material. It has good wear and thermal resistance, but not as good as other titanium coating options.
More prominent today is the use of carbide substrates in a cutting tool as opposed to high-speed steel or high-speed cobalt steel. For carbide substrates, variations of titanium coatings with aluminum content are used.
A number of titanium-based coatings are available, which for the most part have over 50 per cent titanium content. Here is a look at four common coatings and their characteristics.
TITANIUM CARBONITRIDE (TiCN)
TiCN is a titanium-based coating with carbon added to it. The second iteration of TiN, it came to market in the late 1980s. It is bluish-grey in colour and has a Vickers hardness of up to 3,000. It has an operating temperature of approximately 750 degrees, even lower than TiN’s, which means that it can be used only in applications for which high temperatures aren’t an issue. It is for this reason that coolant should be applied correctly to control the temperature of the cutting edge to prevent premature wear.
This coating typically is used for softer materials such as aluminum and non-ferrous materials, which benefit from the additional wear resistance from the hardness of the coating, but only when there is no concern about the thermal properties of these soft materials.
TiCN, which has a coating thickness of 2 to 4 microns, offers high hardness, excellent abrasive resistance, and improved toughness.
TITANIUM ALUMINUM NITRIDE (TiALN)
Both TiAlN and AlTiN are titanium-based coatings, but they have aluminum content added to this composition. For the most part, TiAlN tends to have over 50 per cent titanium content, and in some cases up to 55 per cent, with 40 per cent aluminum and 5 per cent nitrogen. The nitrogen is used in the coating process to help as a curative agent and brings the other elements together to the surface of the tools. TiAlN has a coating thickness of 1 to 3 microns and is typically violet-grey in colour.
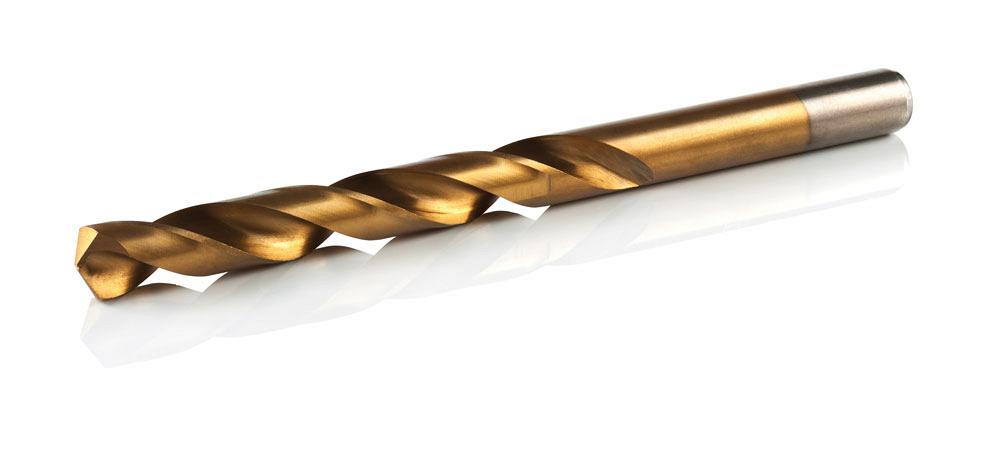
Titanium nitride (TiN) has an amber-gold colour and is common on the market for most general-use cutting tools.
TiAlN was the third iteration of coatings, developed in the early to mid-1990s, and has a Vickers hardness of 3,500, the highest of any of the four common titanium-based coatings. It has an operating temperature of approximately 1,470 degrees. It has a slightly higher wear resistance than AlTiN.
This coating typically was used to machine hard materials such as alloy steels in a prehardened condition. TiAlN can be used to easily machine up to a 45 Rockwell with a cobalt based high-speed steel or a 50 Rockwell with a carbide substrate.
ALUMINUM TITANIUM NITRIDE (ALTiN)
Unlike the other coatings, AlTiN has more aluminum than titanium, with aluminum making up around 60 to 65 per cent, titanium approximately 30 per cent, and nitrogen still making up 5 per cent. It typically comes in a blue-violet, purple colour.
AlTiN was the fourth iteration of coatings, developed in the late 1990s to early 2000s, and has a Vickers hardness of 3,300, making it slightly softer than TiAlN. It has an operating temperature of approximately 1,650 degrees.
This coating’s parameters are fairly close to TiAlN’s, and it has the same coating thickness (1 to 3 microns), but where it really shines is its heat resistance. It has the highest thermal capability of these coatings and typically can be used for applications in which there are high temperature concerns, such as the machining of titanium and heat-treated steels up to 62 Rockwell C.
It also can be used for heat-treated materials, and typically it is seen in the die and mould industry where a mould is heat-treated and then finish-machined afterward. Also, with some tool types, this coating allows a heat-treated block to be machined completely.
GENERAL INFORMATION
When deciding on the right coating, it’s important to know your material, machining conditions, and equipment being used. Each of the titanium coatings offers unique characteristics and provides appropriate parameters, whatever your cutting needs.
A general-purpose high-speed steel or cobalt tool will most likely have a standard TiN coating. For aluminum or non-ferrous material, it will generally have a TiCN coating regardless of what the substrate material is. For general-purpose carbide tools, the coating will probably be the standard TiAlN. With some of the more high-performance cutting tools that are designed for specific material groups, it is common to have a higher-end coating like the AlTiN.
Beyond these four options, a number of variations are available on the market, albeit less common. For example, a four-element coating, titanium aluminum carbonitride (TiAlCN), is an option. However, the more exotic coatings tend to be designed for very specific uses.
When it comes to deciding if a coating is worth investing in, it’s really all about the cost-to-performance ratio. Typically, coatings add 10 to 20 per cent to the cost of the tool. Yet a coated tool can average two to three times the lifespan of a non-coated tool. Coatings also allow you to machine at higher speed and feed rates. These are the main reasons that these coatings are used today.
Dennis Noland is the senior R&D engineer at Niagara Cutter, a subsidiary of Seco Tools, 150 South Fifth St., Reynoldsville, PA 15851, 814-653-7156, www.niagaracutter.com.
Related Companies
subscribe now
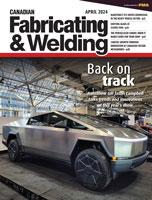
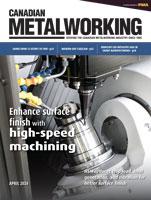
Keep up to date with the latest news, events, and technology for all things metal from our pair of monthly magazines written specifically for Canadian manufacturers!
Start Your Free Subscription- Trending Articles
Automating additive manufacturing
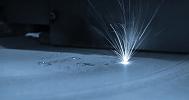
Identifying the hallmarks of a modern CNC
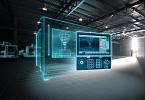
CTMA launches another round of Career-Ready program
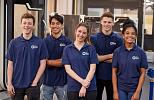
Collet chuck provides accuracy in small diameter cutting
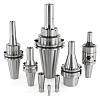
Sandvik Coromant hosts workforce development event empowering young women in manufacturing
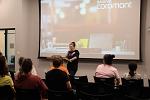
- Industry Events
MME Winnipeg
- April 30, 2024
- Winnipeg, ON Canada
CTMA Economic Uncertainty: Helping You Navigate Windsor Seminar
- April 30, 2024
- Windsor, ON Canada
CTMA Economic Uncertainty: Helping You Navigate Kitchener Seminar
- May 2, 2024
- Kitchener, ON Canada
Automate 2024
- May 6 - 9, 2024
- Chicago, IL
ANCA Open House
- May 7 - 8, 2024
- Wixom, MI