- FMA
- The Fabricator
- FABTECH
- Canadian Metalworking
Electric Press Brakes Can Double Bending Productivity, Increase Accuracy, and Save Dollars
Going electric can double bending productivity, increase accuracy, and save power
- By Sue Roberts
- February 15, 2013
- Article
- Cutting Tools
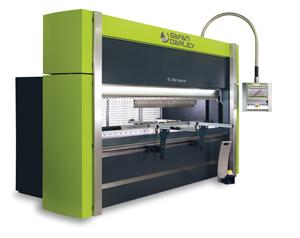
SafanDarley’s 100 percent electric brakes are available from 20 to 300 tons and from 2 to 13 feet. Photo courtesy of SafanDarley.
New, faster technologies like the fiber laser are doubling the number of parts that can be cut per hour. That's great for production, right? Maybe. It depends on whether or not the downstream processes can keep up. What about those pallets of WIP sitting in front of the press brake?
A half dozen years ago eliminating that bending bottleneck probably would have meant adding another piece of hydraulic equipment to the shop floor along with a dedicated operator. Today shop owners have an option that just might eliminate bending wait time, improve accuracy, reduce equipment maintenance, and save on ratcheting-up power costs. That option is going electric.
A Well-vetted Technology
Electric brakes have come of age. Hesitations about moving from hydraulic brakes to electric as production equipment, not simply complementary machines, are disappearing. Shops are finding that innovations and vetting over the past few years have resulted in electric brakes as a viable choice to increase bending capacity in high-mix, low-volume shops as well as operations dealing in large runs.
"With a press brake, the majority of time is spent waiting for the operator to make the bend and the hydraulic motors are whirring away, drawing energy," said Paul Croft, bending product manager for Prima Power North America, Arlington Heights, Ill. "Electric brakes like our eP-series draw very limited power during idle time, about 50 percent less than a hydraulic brake, and draw less power than the hydraulics during the stroke because the servo drives are far more energy-efficient.
"In the original stages of electric brake development, we could make the machine only so big without being extremely costly—the newness of the technology limited the machine size. But once manufacturers got to that 10-ft., 100-ton machine, probably considered today's industry standard, sales took off."
Although still considered new, electric brake technology has moved through the mechanical and hydraulic stages to electric to become more practical and cost-effective. Capacities have been expanded to meet diverse production needs. Now the SafanDarley line of E-Brakes includes models from 20 to 300 metric tons with working lengths up to 13 ft. Cycle times of the electric brakes are quoted as being 2 to 2.5 times those of their hydraulic counterparts without adversely affecting operator safety.
Long on Accuracy
Accuracy with electric brakes is also very high. "When using hydraulic cylinders where the tonnage is located on the far left- and right-hand sides of the machine," Croft said, "you have to compensate for the fact that the tonnage is going to be slightly limited in the center and correct with some kind of crowning device.
"The belt and pulley system, the No. 1 difference between electric brakes like ours and hydraulic brakes, saves power and time but also virtually eliminates crowning and its adjustments and measurements."
Mauricio Gutierrez Matta, area export manager for SafanDarley equipment, distributed in Canada by Westway Machinery, Mississauga, Ont., explained that the series of belts and pulleys located across the length of the beam work in combination with servomotors to move the top beam down. The servomotors are synchronized with linear encoders on both sides of the upper beam (Y1 and Y2) and generate force through the pulleys and belts. This allows for increased acceleration and speed transitions without the lag time associated with hydraulics. Springs located on either side of the brake return the beam without using energy.
"The pulleys are spaced across the length of the beam, allowing an equal distribution of the bending force, which eliminates the need for a crowning table in 95 percent of jobs," said Matta. "The 5 percent exception is when a user wants to bend with an extreme load, for example, when V-width is less than eight times the sheet thickness."
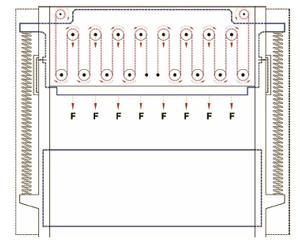
A belt and pulley system distributes force evenly across the ram, eliminating the need for crowning tables in the majority of jobs. Illustration courtesy of Safan-Darley.
Manufacturers consistently quote electric brake cycle time savings of 30 percent or more while energy use is cut in half, lowering production costs and the company's carbon footprint.
SafanDarley has introduced its third generation of 100 percent electric brakes. Its electrical press brakes have been in shops, particularly in Europe, for 17 years. A trio of the synchronized motors, the control, and the light guard increases ram acceleration and deceleration, resulting in substantial cycle time reduction. "The light curtain can be used in different modes and programmed to allow the upper beam to move within 1 mm above the sheet in milliseconds prior to bending," Matta said. "There is no dead time. The E-Brake can be automatically ready for the next step."
Bystronic's Xcite 80 E brake uses the Force Dynamic Drive system to bend within a tolerance of ±25 arcminutes. Repeatability is quoted at ±0.000098 in. It has 88 U.S. tons of bending power and an 80-in. bending length.
Rigid O-frame designs used for the construction of many models minimize the twisting and yawing that can occur to reduce horizontal displacement and increase accurate tool alignment over the machine's entire working length.
Keeping up With Cutting
"There are manufacturers who have had electric brakes out for a while," said Frank J. Arteaga, Bystronic's head of product marketing, NAFTA Region, Elgin, Ill. "The Xcite 80 E has technology that enables high-speed bending and can cut bending time in half. Current laser cutting technology is producing two parts in the time it used to take to cut one. We have to match that productivity with increased productivity in bending. The time for this electric brake technology is now."
Simplified Programming, Maintenance
Ease of operation is being built into electric brakes. Touch control screens are designed to be intuitive so little operator training is required, but options are included that give experienced operators the freedom to create and adjust programs at the machine. For example, Bystronic's ByVision control package was developed following a series of interviews with novice and experienced operators to learn what options would be most useful and what interactions could be automated, eliminating several steps in the process.
The lack of hydraulic fluid and gear pumps reduces maintenance and removes the need for hydraulic oil disposal. Typically, the electric brakes have fewer critical components so less time and money are spent on maintenance.
"People need to be more educated in the benefits of electric brakes," Arteaga said. "There are definitely major advantages for the right applications. Bending ¼-in. material is efficient, but 1⁄8-in. and under is where we see the higher volumes being produced and the most benefit on the electric brakes."
As with hydraulic press brakes, choosing the most efficient electric press brake requires knowing the applications. Match the tonnage with the applications and look for easy setup, programming, and accuracy. Savings will follow.
"I don't know of any of our customers who have bought an electric machine and gone back to hydraulic," Croft said. "That's the ultimate testimony. There is really no downside."
subscribe now
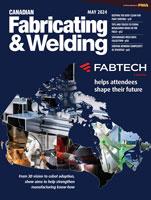
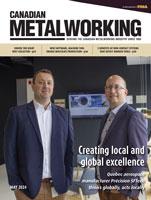
Keep up to date with the latest news, events, and technology for all things metal from our pair of monthly magazines written specifically for Canadian manufacturers!
Start Your Free Subscription- Trending Articles
- Industry Events
MME Saskatoon
- May 28, 2024
- Saskatoon, SK Canada
CME's Health & Safety Symposium for Manufacturers
- May 29, 2024
- Mississauga, ON Canada
DiPaolo Machine Tools Open House 2024
- June 4 - 5, 2024
- Mississauga, ON Canada
FABTECH Canada
- June 11 - 13, 2024
- Toronto, ON Canada
Zoller Open House & Technology Days 2024
- June 12 - 13, 2024
- Ann Arbor, MI