- FMA
- The Fabricator
- FABTECH
- Canadian Metalworking
Advancing equipment care
A PdM service steps closer to eliminating any machine downtime
- By Sue Roberts
- November 15, 2017
- Article
- Fabricating
Preventive maintenance (PM) programs have proven that the time spent on scheduled cleaning, checking processes, and replacing wear parts pays off in fewer performance problems, little or no unanticipated downtime, and more productivity. So, it may be time to enter another phase of machine care by squeezing a d in between the P and M—to move from preventive to predictive maintenance (PdM).
Think of it like OnStar® for a car, which uses various diagnostic programs to monitor key vehicle components in real time every day and report back to the manufacturer. If something is not performing at its best, an alert is sent to the vehicle owner and/or dealer. This enables a repair or part replacement to be handled before the driver is stranded on the side of the road.
Chris Jarrell, technical products coordinator for business systems at MC Machinery Systems Inc., talked about how the capabilities of Remote 360 machine monitoring can act like OnStar for the company’s laser cutting equipment. The service also is available for the wire EDM and sinker EDM product lines and will be offered for additional machine tools in the future.
CFW: What do manufacturers want—and need—to know to go to the next step in improving productivity?
Chris Jarrell: Manufacturers want their machines to notify them not just if something fails, but if something begins to perform at a less-than-optimum level. We’re getting close to that point with the Remote 360 that communicates directly with machines and then with humans via the internet of things (IoT). The service monitors the current status of the machine, making it possible to identify when it is not running at its peak and to predict a future problem.
In addition to sending out a notice when there is an alarm, work stoppage, or items are scheduled for maintenance, the system has a variety of sensors that monitor different components on the equipment while it is in production and share the results with us. On a laser those components include the machine tool, controller, and resonator units. We can go to certain pages that track diagnostic data on that specific machine tool and share the results with the manufacturer. Any alerts are sent out via email or pushed out through a free app.
The service also tracks and charts machine productivity and what the machine is consuming, like gas, nozzles, and focal lenses, and provides a program run history. The run history is exportable to an Excel file for additional analysis.
CFW: How do you determine if a particular component of the machine in production requires attention?
Jarrell: Results from sensors placed throughout the machine tool are displayed on diagnostic screens. That information allows us to determine if the component is allowing the machine to operate as it should. If not, the data helps us determine what part of the machine is not performing properly. Our technicians can see what needs attention to avoid an increase in production costs, loss of productivity, or an eventual shutdown.
For example, the power supply for the laser unit itself needs a certain amount of amperage to generate the desired output power. The resonator will automatically run self-diagnostics checks to determine if the correct amount of power is being generated. The results of this test help to determine if the resonator needs attention. It hasn’t failed yet, but the test can identify if the power supply is working harder than it should to achieve the required levels of output power. The remedy may be something as easy as cleaning a part, or it may be a part that is in pre-failure mode and needs replacement.
We evaluate the information and make recommendations as to what is needed to get that resonator back to running at its peak while using the appropriate amount of energy.
Reports from the machine sensors help us predict a problem and make a correction before it drastically impacts production. They can save the manufacturer money and side-step a potential equipment failure.
CFW: In addition to keeping the equipment operating at its full potential, how does remote monitoring help you help the manufacturers?
Jarrell: Having us remotely connected to the machine is like having a technician standing in front of the machine. About the only thing we cannot do is start and stop a process because of safety issues.
Many times our technicians can remotely go into the parameter settings of the controller and make adjustments without going on-site. That saves the customer money that could have been spent on a service call and they don’t have to wait for a technician to arrive.
If a service call is needed, many times we can do enough remote troubleshooting so the technician knows what the problem is before arriving at the shop and he might be able to carry any repair parts with him. This can reduce the downtime needed to make the repair or replace a part and save the manufacturer money.
CFW: Are there advantages in addition to predicting mechanical problems?
Jarrell: Yes. Lost time is not necessarily due to something failing on the machine. One of the common things that reduces actual run-time performance on a laser is a head crash. Maybe it was a problem with the setup or programming. We can see how the programs are being created and run, remotely connect to the machine, and recommend adjustments to avoid the problem in the future.
CFW:What capabilities are coming next?
Jarrell: In addition to adding features, we plan on introducing Remote 360 for more product lines so that our technicians and customers can be more productive. Features such as new alerts, more available data points, and new diagnostic functions are areas we are currently focusing on.
More features and sensors allow us to monitor the life of machine components and their performance.
MC Machinery Systems Inc., 630-616-5900, www.mcmachinery.com
About the Author
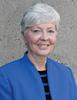
Sue Roberts
2135 Point Blvd
Elgin, IL 60123
815-227-8241
Sue Roberts, associate editor, contributes to both Canadian Metalworking and Canadian Fabricating & Welding. A metalworking industry veteran, she has contributed to marketing communications efforts and written B2B articles for the metal forming and fabricating, agriculture, food, financial, and regional tourism industries.
Roberts is a Northern Illinois University journalism graduate.
subscribe now
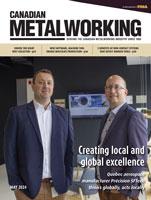
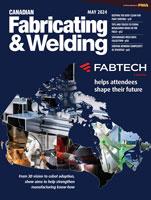
Keep up to date with the latest news, events, and technology for all things metal from our pair of monthly magazines written specifically for Canadian manufacturers!
Start Your Free Subscription- Trending Articles
Aluminum MIG welding wire upgraded with a proprietary and patented surface treatment technology
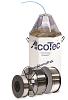
Hypertherm Associates partners with Rapyuta Robotics
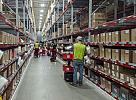
Protected and productive: welding helmet tech
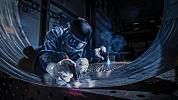
HGG Profiling Equipment BV names Western Canada area sales manager
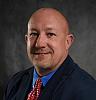
Compact weld camera monitors TIG, plasma processes
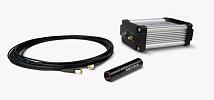
- Industry Events
CTMA Economic Uncertainty: Helping You Navigate Kitchener Seminar
- May 2, 2024
- Kitchener, ON Canada
Automate 2024
- May 6 - 9, 2024
- Chicago, IL
ANCA Open House
- May 7 - 8, 2024
- Wixom, MI
17th annual Joint Open House
- May 8 - 9, 2024
- Oakville and Mississauga, ON Canada
MME Saskatoon
- May 28, 2024
- Saskatoon, SK Canada