Editor
- FMA
- The Fabricator
- FABTECH
- Canadian Metalworking
Bridging the engineering/fabricating divide at the University of PEI
Hands-on approach at UPEI’s Faculty of Sustainable Design Engineering helps students build communication skills with the trades
- By Rob Colman
- August 22, 2018
- Article
- Fabricating
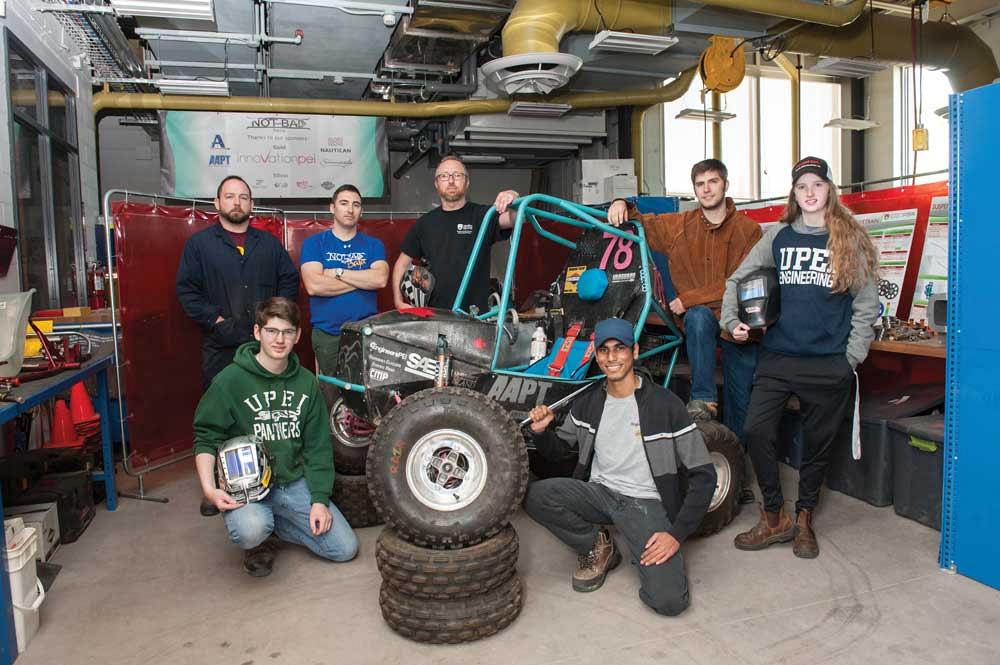
UPEI's Baja SAE team, which includes: (back, l to r) staff members Andrew Townshend, Jeff Bowser, and Sandy Doucette, and students Tim Reeves and Payton Brown; (front) Brendan Gordon and Tharuka Kuruppu. Brown too the initiative to learn GTAW from Doucette ahead of this year's competition and ended up being the primary welder for the team.
The relationship between design engineers and fabricators can be a fractious one. As impressive as any engineered object can be, making its fabrication processes as efficient as possible isn’t always the first thing on a designer’s mind. The University of Prince Edward Island’s Faculty of Sustainable Design Engineering’s (FSDE) approach to hands-on learning may provide a model that bridges that communication gap.
The FSDE at UPEI was created three years ago. Previously the university offered students a two-year engineering diploma, after which point they would have to go to another institution to finish the degree. The new program doesn’t simply tack on two years to a standard engineering degree, however. Instead, it gives students the chance to work on real community- and industry-based projects in every semester of their program through an applied project-based professional practice (PBPP) approach to learning. In their third and fourth years, students enter one of three focus areas: mechatronics, sustainable energy, or bioresources.
Teaching Communication
The hands-on approach of the faculty is reflected in the 2-year-old building it occupies: The whole building has only two standard classrooms. The rest of the facility houses design studios, student labs, and workshops.
That approach is also reflected in the fact that both a Red Seal welder and a Red Seal machinist are on staff. The welder is Sandy Doucette, the fabrication and assembly tech in the program. The first interaction he has with first-year students is the first month of the school year when he talks to them about safety, reviews safety procedures, and basically makes sure safety is everyone’s first priority. “This ensures students of all years keep safety in mind as they do their builds throughout the school year, and hopefully they keep safety as part of their daily routine in their careers as well,” said Doucette.
The first interaction Doucette has with second- and third-year students is often in a materials course that includes welding.
“There aren’t many classes dedicated to welding, but I introduce them to GMAW [gas metal arc welding],” said Doucette. “They get to try welding. I want them to learn not to be frustrated with the process and to appreciate how difficult it can be. I explain to them how important joint prep is, your choice of weld, and why it’s important to keep that in mind when you are designing.”
Doucette is usually busy helping students make their designs a reality.
“The students will usually develop a design in SolidWorks, and then [machinist] Andrew Townshend, [machinist/3-D printing expert] Jeff Bowser, and I will meet with them and say, ‘Is this feasible?’” said Doucette. “We review their choice of material and discuss any issues we see with the design. We look at how everything goes together, all the details, including joint design, making more readable blueprints, and bolts/hardware/fasteners. If anything doesn’t fit together like it should, we hand the drawings back to the students so they can make them better. This puts the students in a great place to learn all about their design and ultimately build a great project.” The main thing that Doucette, Townshend, and Bowser teach is communication at every stage of a project.
“When a student needs metal for a part, we have them visit a local supplier with their drawing to explain to them what they need,” said Townshend. “That supplier is very old-school; that’s the only way you’re going to reach them. But it’s a great learning experience for the students. They get to explain in person the nature of their project and the supplies they need. They also see how that shop works and they learn how to communicate on the shop’s terms.”
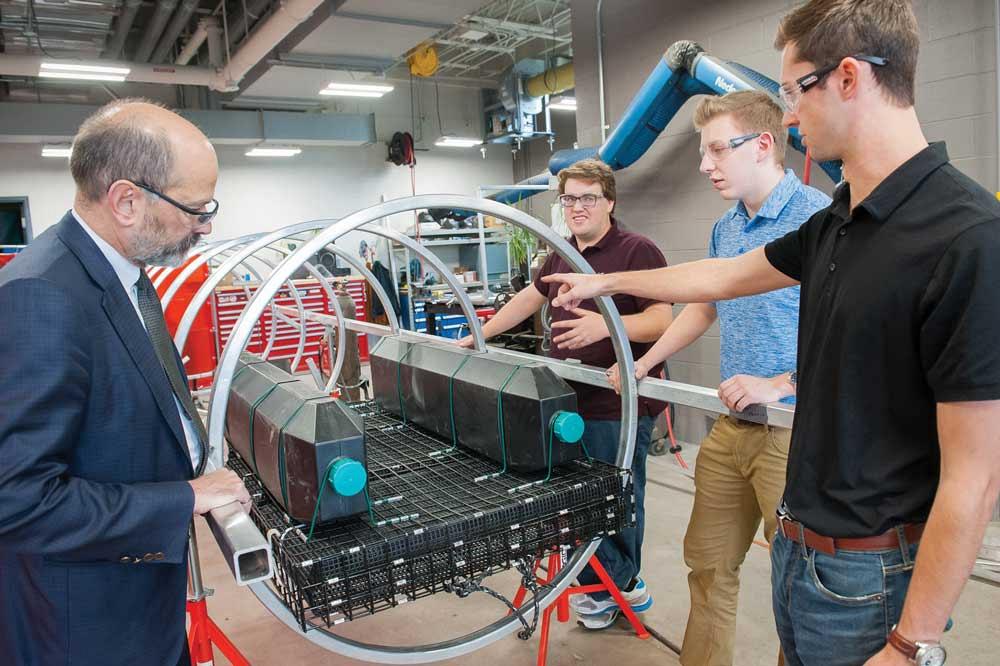
One interesting project that has since been patented by UPEI students in conjunction with the university is an oyster cage flipper. Oyster cages have to be flipped regularly to ensure the oysters remain healthy, but this is labour intensive. The students invented a helical structure pulled by a boat that does the process automatically. Here we see the dean of the faculty, Nick Krouglicof, discussing the cage flipper while it is in mid-fabrication.
Doucette understands that this is crucial for making any product work for the people it is designed for.
“The projects that students are doing are related directly to industry,” he explained. “They are solving problems for companies, dealing with technicians at companies like Irving and Cavendish Farms, to name two of many. One of my proudest moments so far at the school was when I took some students to a customer’s to discuss the redesign of one of its main product lines. When we went into the shop, one of the students went right over to an employee running one of these machines and asked them what they liked about it, what they didn’t like about it, and precisely how they used it so that they would understand how an operator feels it can be improved.”
Ultimately, Doucette and Townshend are an important part of what makes it possible for the school to stand out from the crowd.
Good examples of this were on display in the bioresources lab, where Industry Research Assistant Chuck Terrio explained a solids separator built by the UPEI team.
“This is all stainless steel,” Terrio said. “This is a three-stage C-channel solids separator, which includes a fluidized bed reactor. A high-temperature, high-pressure reaction happens, and we’re generating a gas from which solids have to be removed. This particular project will be validated this summer by two PhD students. There is already another researcher at another university waiting for the validation of this. Our in-house technical staff being able to build this for us gives us that added edge to get our research done faster. And whilst we’re teaching the students to design, they have to communicate with Sandy and Andrew to ensure that it’s possible.”
The students also take on the responsibility of going outside the school to get professional support for the weld analysis, getting the pressure welds evaluated from a certified shop.
Baja Building
Doucette’s road to UPEI wasn’t a straight-up job interview. His introduction to the engineering program was a local TV news item.
“Three years ago I saw that the UPEI engineering students were entering the Baja Buggy competition for the first time,” he explained.
The Baja SAE is an intercollegiate design competition run by the Society of Automotive Engineers (SAE). Students from universities all over the world design and build small off-road cars.
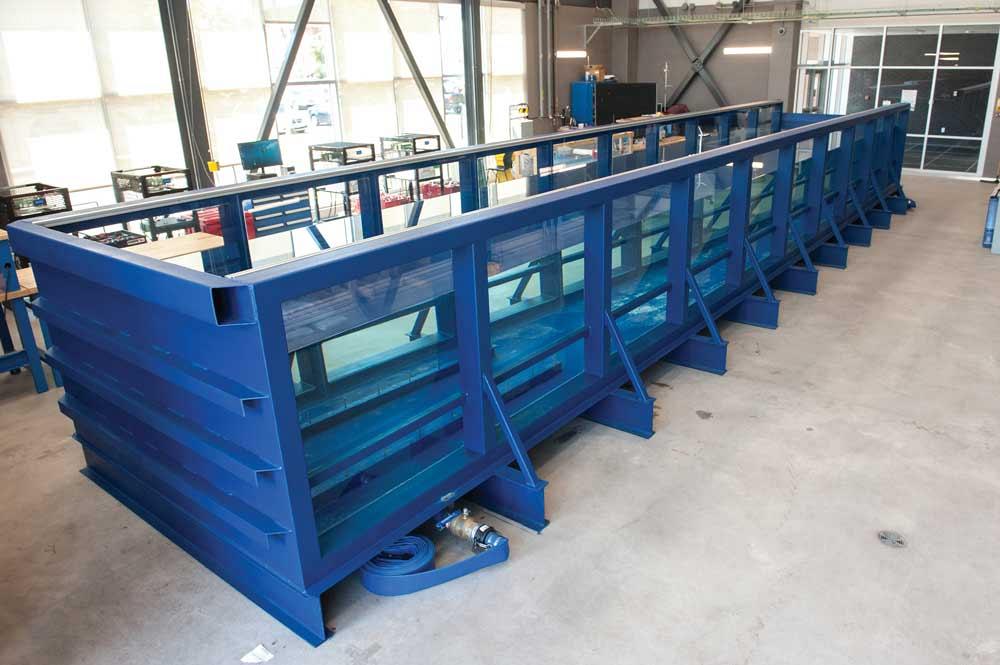
Although his main job is to work with students on the development of their projects, Fabrication and Assembly Tech Sandy Doucette has also been called upon to help with one or two faculty projects, the most substantial being a wave tank. The tank was designed in-house and fabricated and welded by Doucette. It is a 40-ft. by 10-ft. tank that holds 50,000 lbs. of water. “It required about 8,000 lbs. of steel,” said Doucette. “I was a little concerned about the seal, so I did a first pass with a stick weld, then finished it off with flux core. The other challenge was welding it together in a room with large windows. Safety is a big concern for us, so someone feeling they’ve experienced an arc flash is just as bad as when it does happen, so ensuring there was no risk of that was key.” The tank has already been tested and the welds have held. “We will be testing floating structures and how they react to waves in the tank,” said Dr. Matthew Hall, an assistant professor working on wind and offshore renewable energy. “This is important for research on marine vessels and offshore wind turbines. It is the first of its kind in the province.”
“I thought, ‘They’ll need a welder,’ so I called Jeff Bowser, the person who was leading the team, and volunteered my time. The students had the best of intentions, but no experience with fabricating. And yet we finished the buggy in three weeks, whereas most teams would take nine months.”
As the university planned for the expansion of the faculty, Doucette was encouraged to apply. The faculty’s third buggy recently went into competition.
“We did the first buggy using just regular steel, but this year it was TIG welded using 4130 chromoly steel tubing. It’s tough to weld because it’s so thin walled. We have the steel coped and bent by a company for us. We brought other welders in from industry to help us with the construction, which was a great chance for the students to learn from others out in the field.”
One of the students, Payton Brown, took the initiative to learn TIG welding from Doucette ahead of this year’s competition. She worked hard and ended up being the primary welder for the team. In fact, at the recent competition in Oregon she completed approximately eight hours of welding repairs and modifications on the frame.
“She wanted to be sure she could make any repairs to the buggy while they are away at competition,” Doucette explained. “The TIG welding she has done has been really impressive.”
“This competition is my favourite part about working at UPEI,” said Bowser, faculty adviser for the UPEI Baja SAE team. “Being able to see the students apply their knowledge to a real-life problem makes it worth all the many hours put into this project. The opportunity these young engineers receive through racing and building gives them job-ready skills that will allow them to get on the shop floor and actually have a clue about how to make things and how to ask the right questions.”
Patent Projects
Although Doucette’s proud of how he’s able to help the students, most of his enthusiasm is reserved for the impressive projects the students have championed. This has included a wheelchair designed for a girl who couldn’t be provided with a chair small enough for her. The students not only made a chair to fit her needs now, but can also grow with her.
“The frame was built here out of stainless steel, and the body panels were 3-D printed in ABS plastic with our Fortus 380mc additive manufacturing system,” said Doucette. “All electrics and wiring were done by our other, very talented technicians at the school.”
Another interesting project that has since been patented by the students in conjunction with the university is an oyster cage flipper. Oyster cages have to be flipped regularly to ensure the oysters remain healthy, but this is a labour-intensive process. The students invented a helical structure pulled by a boat that does the process automatically while still allowing the rope that holds the trap to the sea floor remain secure. The oyster cage flipper was originally a second-year project that turned out so well, the students were encouraged to patent it.
“It was made using aluminum to keep the weight down,” said Doucette.
The school encourages industry looking for assistance with real-world challenges to contact them. It’s an opportunity to see the future in action.
Editor Robert Colman can be reached at rcolman@canadianfabweld.com.
UPEI FSDE, www.upei.ca/science/engineeringAbout the Author
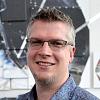
Rob Colman
1154 Warden Avenue
Toronto, M1R 0A1 Canada
905-235-0471
Robert Colman has worked as a writer and editor for more than 25 years, covering the needs of a variety of trades. He has been dedicated to the metalworking industry for the past 13 years, serving as editor for Metalworking Production & Purchasing (MP&P) and, since January 2016, the editor of Canadian Fabricating & Welding. He graduated with a B.A. degree from McGill University and a Master’s degree from UBC.
subscribe now
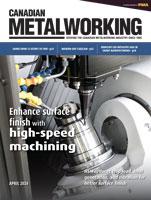
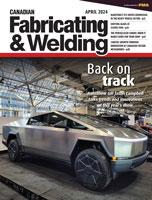
Keep up to date with the latest news, events, and technology for all things metal from our pair of monthly magazines written specifically for Canadian manufacturers!
Start Your Free Subscription- Trending Articles
Aluminum MIG welding wire upgraded with a proprietary and patented surface treatment technology
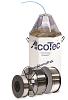
CWB Group launches full-cycle assessment and training program
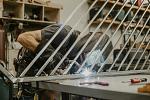
Achieving success with mechanized plasma cutting
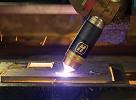
Hypertherm Associates partners with Rapyuta Robotics
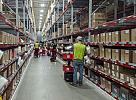
Brushless copper tubing cutter adjusts to ODs up to 2-1/8 in.
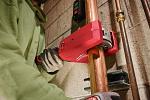
- Industry Events
MME Winnipeg
- April 30, 2024
- Winnipeg, ON Canada
CTMA Economic Uncertainty: Helping You Navigate Windsor Seminar
- April 30, 2024
- Windsor, ON Canada
CTMA Economic Uncertainty: Helping You Navigate Kitchener Seminar
- May 2, 2024
- Kitchener, ON Canada
Automate 2024
- May 6 - 9, 2024
- Chicago, IL
ANCA Open House
- May 7 - 8, 2024
- Wixom, MI