- FMA
- The Fabricator
- FABTECH
- Canadian Metalworking
Custom Fenestration Systems Bring Daylight Inside
Measuring Systems Up Cut-Off Production by 40 Percent
- By Sue Roberts
- June 17, 2013
- Article
- Fabricating
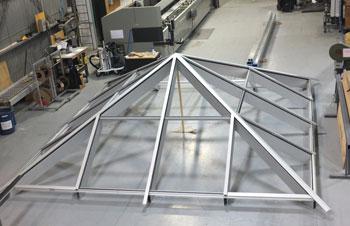
Exacting cuts were needed for proper assembly of this fenestration component. Photo courtesy of A.T. Fabrication.
It’s not hard to find studies that tout the advantages of windows in a place of business. Daylighting, the practice of arranging, proportioning, and designing windows and other openings to allow for natural lighting, is credited with saving energy, increasing employee productivity, and contributing to an overall feeling of contentment. Coupled with the beauty that exterior glass design can bring to a building, curtain walls featuring large percentages of glass panes adorn structures along the highways.
In a building designed to capture sunlight, chances are good that hundreds of shiny lengths of profiled aluminum hold the panes in place. This is good for business at A.T. Fabrication in Bois-des-Filion, Quebec, where custom, cut-to-length profiles and assemblies for the glass industry are produced and partially assembled. The majority of the company’s fenestrations go into curtain walls, but windows, greenhouses, and skylights complement the product mix.
Automate for More Parts
Architects pride themselves on being creative with their designs. A.T. Fabrication, founded by André Therrien in 2001, specializes in providing the framework to bring curtain wall conceptions from blueprint to reality. For production, that means every shift has a unique set of aluminum profile lengths to be cut on miter or double-head saws and fed to assembly for fenestration systems.
A.T. Fabrication grew quickly. Rapidly increasing contracts drove the decision to move to a larger facility within the Bois-des-Filion industrial park shortly after the company opened its doors. The customer base, initially limited to Quebec, has expanded into Ontario and now includes 30 regular customers. Production had to pick up to keep up.
“Our batches can have a few pieces up to hundreds to process,” said Anne-Marie Ayotte, company manager. “We used to measure our profiles with a tape, use a metal angle and vise grip to secure the profiles, cut the material, then measure the length again. All this took time.
“In 2006 we added our first automatic measuring system to reduce our cutting time. Since then we’ve added two more to our equipment. We punch in the dimensions and the quantities on the keypad and begin the cut process. All measurements are stored in the system so if we have a repeat, we just ask for the program and the measurement system moves to its new position. We’ve increased our cutoff production by about 40 percent.”
Maximize the Money-Maker Spot
Dominick Olavarria, marketing and communication specialist at TigerStop, described how a basic automated measurement system can contribute to fenestration production: “A basic positioner can be adapted to almost any saw or cutoff device. Operators don’t need to set and reset manual stops, use tape measures, or mark the material before sawing, so accuracy is increased as well as speed. Depending on the weight of the material—the TigerStop will push up to 120 lbs.—the material can be positioned at speeds up to 180 FPM with an accuracy of ±0.004 in.
“Operator time is also saved when a system’s keypad is located near the sawing operation. Instead of having to go down and manually set the stop and slide the material against it, he just keys in the numbers and the positioner moves along the rail, pushing the material into place for an accurate cut. The operator doesn’t have to leave the money-maker spot, which is right where the saw is. A label can also be produced at the time of each cut so the operator doesn’t have to mark each piece.”
A Good Fit
Accuracy is important at A.T. Fabrication. Each cut length of aluminum profile, up to 24 ft. long, needs to fit snugly with its counterparts to meet architectural design specifications while ensuring a tight fit that stands up to winds and rain.
“The products can be partly assembled here, depending on the size of the frames and the type of truck picking them up. The rest of assembly is done in the field,” said Ayotte. “If the aluminum length is not cut to the right size, we have to redo the cutting to optimize the material. If it is too short, we need to start with a new length. So, increased accuracy from the addition of the automatic measuring system is very important. It has reduced our waste of material. The aluminum bars can be worth up to $400, so this is definitely a financial issue.”
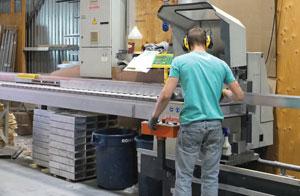
The measuring system eliminated the need for the operator to leave the saw area to measure and mark lengths of aluminum prior to cutting. Photo courtesy of A.T. Fabrication.
Taking automatic measuring for sawing systems a step beyond the cutoff process, software included in some systems accepts plans downloaded from design programs, generates estimates and proposals, and invoices completed jobs.
“The fenestration industry is using end-to-end cutoff automation to handle cut list workflow beginning at order entry and tying into the bills of material, which are usually pretty dynamic. Then the software can generate billing paperwork,” said Olavarria. “Some software is preconfigured with specific designs from manufacturers, and the dimensions or other parameters are customizable. We have systems that function solely as stops and some that will push over a ton of material.”
“We’re working on some new projects,” said Ayotte, “and we may need additional saws. If we add cutoff equipment, it will have automatic stop/gauge and push systems.”
subscribe now
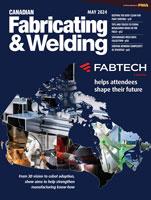
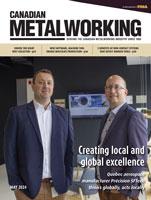
Keep up to date with the latest news, events, and technology for all things metal from our pair of monthly magazines written specifically for Canadian manufacturers!
Start Your Free Subscription- Trending Articles
- Industry Events
MME Saskatoon
- May 28, 2024
- Saskatoon, SK Canada
CME's Health & Safety Symposium for Manufacturers
- May 29, 2024
- Mississauga, ON Canada
DiPaolo Machine Tools Open House 2024
- June 4 - 5, 2024
- Mississauga, ON Canada
FABTECH Canada
- June 11 - 13, 2024
- Toronto, ON Canada
Zoller Open House & Technology Days 2024
- June 12 - 13, 2024
- Ann Arbor, MI