- FMA
- The Fabricator
- FABTECH
- Canadian Metalworking
Parts Picking Is Up
Automated options speed up punched part removal
- By Sue Roberts
- May 15, 2013
- Article
- Fabricating
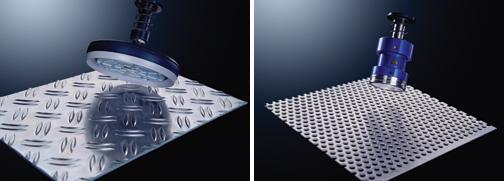
(Left)Specially designed vacuum cups are available to securely lift parts cut from textured materials like tread plate. (Right)Magnets can offload hole-intensive parts produced from ferrous material. Photos courtesy of TRUMPF.
Punches are powering through metal at ever-increasing speeds, producing more parts in less time. Those parts need to be removed from the punch press. Quickly.
Automated material handling, once viewed as an option for high-production operations, is gaining ground in job shops. And individual part picking has become faster and more versatile, making it a viable, cost-effective choice.
"Ten years ago I would have said that only high-production customers making repetitive parts would invest in automation, but now, because we can offload parts faster with a variety of options, we're seeing customers that run many different parts and small lots buying automation," said Mike Kroll, product manager for TRUMPF, Farmington, Conn.
Automatically removing parts from a punch press can add a few seconds to total process time, but that slight increase is being justified by faster overall production and the ability of punch presses to add more features in one operation.
"Picking systems tend to land with the more feature-rich products because of value-adding options. We have a turret press with a tool changer that provides bending operations," said Dan McIntyre, punch press product sales manager for LVD Strippit, Akron, N.Y. "As you have potential to add more value to the part in one operation, it makes sense to pick it even if picking slows the overall process."
Tim Brady, product manager at Amada, Buena Park, Calif., agreed that picking is an up-and-coming thing. "Automation for the picking process is definitely an important feature of our systems. Manual parts picking can be labor-intensive and injury-prone."
Staying Connected
Punching microjointed parts within a large sheet of material, a step up from using cut-to-size blanks, remains an effective way to produce and remove parts, particularly for large production runs. Part size and the amount of material left after the punching process don't come into play.
"With a turret press many manufacturers are specifically looking for volumes of parts, and many of them are still satisfied running tabbed material and using a load/unload system with a tower," said McIntyre. "The automation loads the material then pulls the sheets of tabbed parts off and places them on a pallet." A second operation is required to shake and break the parts and stack them before they move on.
Drop, Trap, or Chute?
Drop, trap, or chute. The terminology varies when referring to the hinged door, now standard on many punch presses, that opens to offload parts that are punched free of the sheets. Size of the drop doors, and in turn the size of parts that can slide through them, depends on the machine make and model.
"The beauty of the drop door is that it can remove parts that you do not want to tab because of edge quality, radius corners, or if they are aesthetically better punched and not tabbed," said McIntyre. "Using a drop door can eliminate potential secondary operations."
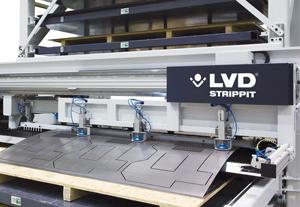
A material handling system loads material and unloads sheets of tabbed parts. Although finished sheets can be returned to the tower for storage, focus on just-in-time production is reducing the use of that option. Photo courtesy of LVD Strippit.
This parts removal method can add up to five seconds to overall processing time as the punching process halts, the door opens to evacuate the part, then closes so punching can resume. Parts drop into a bin or onto a conveyor system that clears them from the machine to make them accessible for immediate use or feeds them into a sophisticated sort system that deposits dissimilar parts into designated bins.
"Automation operates continuously," said Brady. "It doesn't take breaks, and operators don't need to be present for continuous offloading. An operator can load the machine, leave, and come back to a pallet or bin full of parts run over a break, overnight, or over the weekend. We've seen green-light time go up dramatically when this automation was added."
Programming can mix offload methods to accommodate a nest with a variety of part sizes. Size-appropriate parts can slide down the chute, while parts with large dimensions can be tabbed for removal with the skeleton or punched free and individually removed with a part picker.
Pick-and-Place Options
"A robot that individually picks off parts allows you to automatically offload different size parts. And a big advantage is that the parts are neatly stacked without operator intervention and ready for the next operation," said McIntyre.
Vacuum cups and/or magnets can adorn a robotic arm that reaches into the punch press to grab an individual part as it is punched free from the sheet. The cups and magnets are programmed and activated for picking according to part geometry and nest location.
Magnets will pick any part configuration but are limited to ferrous stock and can magnetize the material. Attention also has to be given to the magnetic power to avoid picking more than one sheet of material when loading and latching on to the machine tool table when offloading.
Cups will pick parts from any material, but their use may be limited when offloading small or hole-intensive components.
If a part does not offer a large enough flat surface, or landing area, to accommodate the circumference of the cup, a secure seal for lifting may not occur. Creative programming, however, can provide a workaround. Kroll offered one option: "Some users will program a border around hole-intensive parts to create a landing area and tab the part to the border."
Parts that are too small to be individually picked by vacuum cups can be joined together to form a piece large enough for vacuum cup removal. "The programming software has the ability to make a mini-nest out of small parts," said Brady. "Say four, eight, or 10 parts are tabbed together, then the arm picks out the entire nest."
Various cup sizes can be mixed, matched, and interchanged on a robotic arm. Specialty cups can be added to the picking mix to handle challenging materials. For example, cups with a textured surface are designed to securely adhere to material with a textured surface, like tread plate, where creating a vacuum seal can be challenging.

Software programs initiate the use of vacuum cups to remove and stack parts according to part and nesting geometries. Photo courtesy of Amada.
Kroll pointed out two considerations when adding offloading automation: Work with flat material to ensure a good vacuum seal or secure magnetic hold, and be aware of material thickness. "We prefer not to use automation with material less than about 0.020 in. thick because the integrity of the material makes it difficult to work with the sensors that give you a reliable process."
Control the Offload
Software to control loading/unloading and picking automation is complex in the way it interacts with the equipment, and it is becoming more responsive to overall shop needs.
"We have software that integrates material handling with the punch and other equipment on the floor. It will monitor jobs coming through and open time on the machines so we can decide in the programming station what machine a part should go to," said McIntyre.
Kroll said that software also ensures safety: "We control acceleration as to how fast the material moves. If we were to lose vacuum, the inertia would carry the material wherever it wanted to go. So as materials get thicker and heavier, the automation unit will slow down accordingly."
"Our software is highly automated, but there is a bit of a learning curve," said Brady. "Knowing the proper placement of parts and the proper methods for nesting helps you get the most from the automation. The trend is definitely toward parts separation."
Related Companies
subscribe now
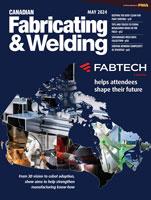
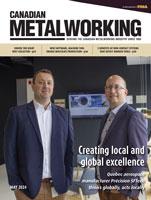
Keep up to date with the latest news, events, and technology for all things metal from our pair of monthly magazines written specifically for Canadian manufacturers!
Start Your Free Subscription- Trending Articles
- Industry Events
MME Saskatoon
- May 28, 2024
- Saskatoon, SK Canada
CME's Health & Safety Symposium for Manufacturers
- May 29, 2024
- Mississauga, ON Canada
DiPaolo Machine Tools Open House 2024
- June 4 - 5, 2024
- Mississauga, ON Canada
FABTECH Canada
- June 11 - 13, 2024
- Toronto, ON Canada
Zoller Open House & Technology Days 2024
- June 12 - 13, 2024
- Ann Arbor, MI