Editor
- FMA
- The Fabricator
- FABTECH
- Canadian Metalworking
Self-reliance creates a clean winner
Easy Kleen continues to grow its product line by bringing more fabricating processes in-house
- By Rob Colman
- January 16, 2018
- Article
- Fabricating
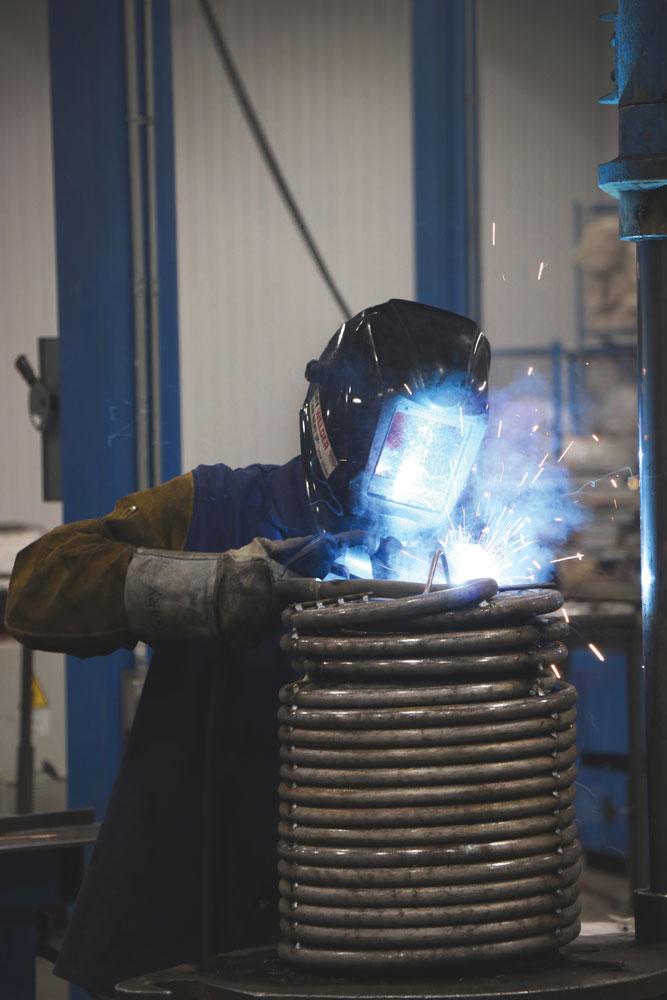
A welder welds additional bracing onto a heating coil at Easy Kleen Pressure Systems Ltd. Images courtesy of Easy Kleen.
Easy Kleen Pressure Systems Ltd. is a Sussex Corner, N.B.-based pressure washer manufacturer. Until recently the company focused primarily on the assembly of its products, outsourcing heating coils for its hot-water machines. However, in the interests of shortening delivery times and opening customization opportunities, the company has now brought coil fabrication in-house. In the process, it has greatly expanded its fabricating capabilities, its facilities, and its staff.
Designing a Better Product
Easy Kleen was founded in 1982 by Fred Howland, who felt at the time that he could provide a better product than what was available in the local market. That attention to quality continues today, with Fred’s son Brad at the company’s helm, and a number of third-generation family members now working there as well. The Easy Kleen product, meanwhile, is being shipped around the world.
The engineering and design team sources parts from manufacturers with worldwide recognition and support so that no matter where an order comes from, the customer can easily obtain parts as necessary.
While Brad Howland was satisfied with the quality of the hot-water coils he was outsourcing, the expense was considerable, and having to order the product risked delivery delays.
Never one to shy away from a challenge, Brad and his team researched the viability of building the coils in-house. He found that it would involve new welding expertise, plenty of new equipment, and more space, but the independence it would give the company seemed more than worth it.
Pipe Dreams – Getting the Coil Right
Pressure washing equipment comes in a wide range of sizes, from small cold-water machines you can use to clean the siding on your house to 11,500-PSI, diesel units for industrial applications. For industrial washers, time is money, which is why they use hot-water units.
The most complex part of making a coil water heater is welding and coiling the pipe. Most of the welding done in the Easy Kleen shop is straightforward gas metal arc welding (GTAW). The coil, however, requires GTAW butt-welded joints, which demand a steady, skilled hand – failure is not an option.
“The coil itself could be made up of 400 ft. of pipe, depending on the model,” said Jeffrey Graham, Easy Kleen’s weld shop manager. “The pipe is butt-welded end to end. As it is welded, it is fed into a tunnel that extends underground outside our building. Once the pipe is the correct length, it gets fed back inside and run through an 11-axis pipe manoeuvring machine that coils it as required.”
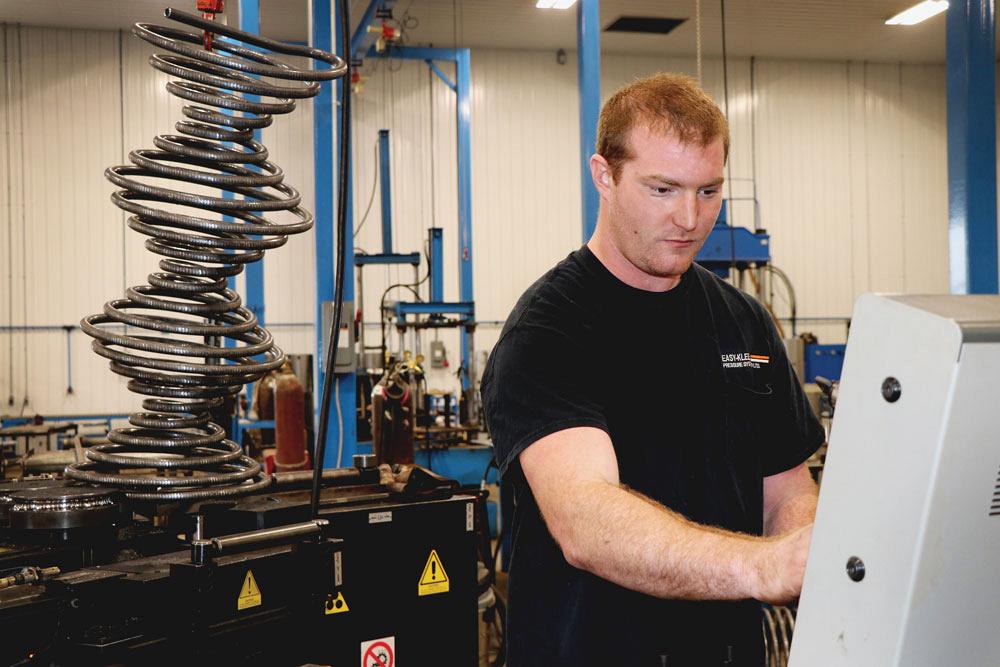
Jeffrey Graham, Easy Kleen’s weld shop manager, at the controls of an 11-axis pipe manoeuvring machine that is used to process the coils for the company’s hot water heaters.
The standard pipe Easy Kleen uses for its most popular model is a Schedule 80 steel, but size and makeup vary depending on the application. For instance, Sch. 160, XXS, and stainless steel are used for higher-PSI applications, up to 12,500 PSI.
The company now tries to run about 50 coils a day in production, but as Graham noted, it took a while to get to that point.
“This was a new process for us, so initially we did everything the hard way,” he said. “The main thing with any process is getting the flow right, and that takes time. We are always improving our efficiencies.”
Once the pipe is completely welded, it is then tested to ensure it can withstand the pressure it is rated for. It is then coiled, compressed, and welded with additional bracing to maintain the integrity of the form. Next it is fitted with an insulated stainless steel housing.
Graham believes that they’ve now set up the assembly and welding of the coil pretty much the way they want it.
“The key is, we don’t want anyone standing around waiting for work,” he said. “We’ve now reached a point where we’ve created sufficient storage space between each station so that when the first person in the process has finished all his work, the last person on the line still has two days of work ahead of him.”
Manage Cut Quality and Quantity
At the same time the shop invested in custom-made coil processing equipment, a 400-ton press, and a tube bender, it also upgraded its sheet metal cutting capabilities, purchasing an Ferric Ermak Fibermak Momentum Gen-3 2-kW fibre laser cutting table and an Ermaksan Speed-Bend Pro press brake from local distributor Rogers Electric & Machine.
“We used to get all of our body frames in precut sheets and just cut holes in them on a small plasma table we have,” said Graham. “Now we can get 6- by 12-ft. sheets delivered and don’t have to have anything precut for our frames. Also, there is no cleaning time involved, which was necessary when we cut holes out with the plasma. There are also fewer opportunities for error. When we had to line up our cuts by hand on the plasma, it was very easy for errors to occur. And if a hole was cut wrong, that’s a whole cart body going to scrap. We don’t have that problem anymore.”
The plasma table is now primarily being used to cut the housings for the coils.
“Because we can weld only one coil skin at a time, it’s easy to throw one small sheet on the plasma table to process it,” said Graham.
Having the laser, however, helps the team manage the company’s growing list of model numbers efficiently and cost-effectively.
“We have more than 300 models just in our catalogue, and that doesn’t take into account all of the custom work we’ve done,” said Graham. “We probably get four custom requests a day. With this new equipment, we can build whatever model we want faster.”
Graham noted that as of June they were still programming the laser for some of the larger models, but most of the work had been done to make it run efficiently in the shop.
“There are small changes we had to work out,” said Graham. “For instance, all parts on the laser are nested in the office, and we’ve had to tweak the nesting so that smaller parts are nested on the plate closest to where we remove them from the table. But these are minor things you fix as you go.”
Expansion Continues
Easy Kleen is growing as it becomes more self-reliant. In less than two years it has grown from a team of less than 50 to more than 80 people strong.
And the growth hasn’t finished. The company is working on yet another 16,000-sq.-ft. expansion of its facility, introducing a new paint facility; an automated Cosen band saw; and a new 80-ton, dual-operated ironworker.
“Paint is our bottleneck at the moment,” said Graham. “Currently we can build more than we can paint. And right now our product moves back and forth through the facility as it nears completion. Ultimately we want to have the facility arranged so that raw materials go in at one end of the building and a finished, painted product comes out the other end. We also have a goal of having 1,000 of our hot-water units in stock at all times to meet customer demand.”
As for future investments beyond these, Graham believes that there may eventually be some investment in automation.
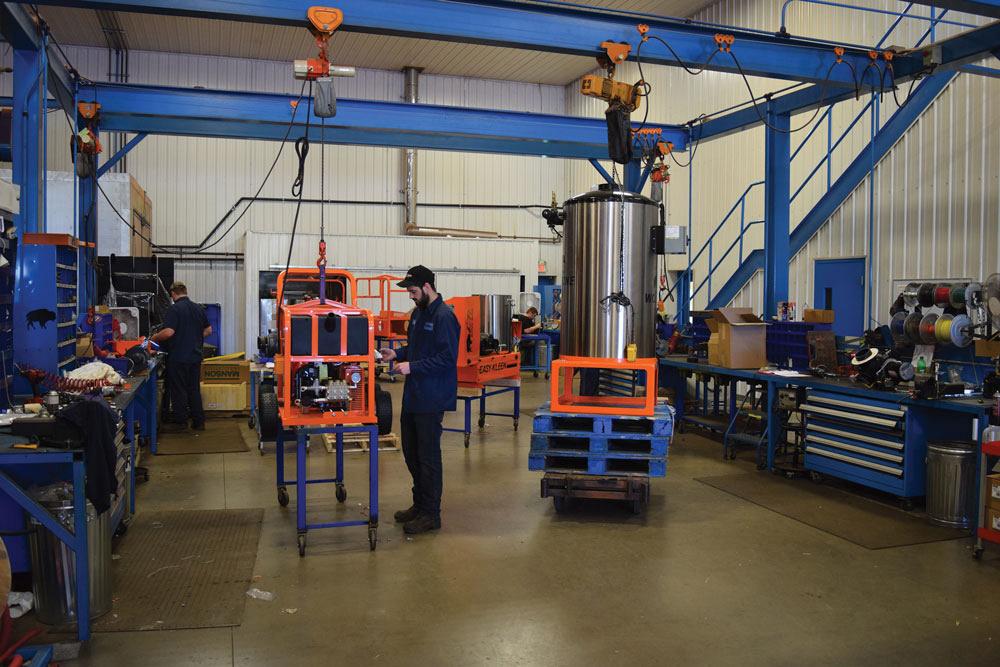
Easy Kleen employees put the finishing touches onto the assembly of one of the company’s pressure washers
“There has been a lot of growth in the weld shop, where we currently have around 15 people,” said Graham. “The challenge we have is that a lot of our welds are very repetitive. To build most of our carts involves only about 5 minutes of weld time, and most of that is just tacking. We have a lot of guys who come here straight out of school so that we can train them the way we want them to do the work. But ultimately we are interested in automating some of that work if we can. It is very repetitive.”
Brad Howland isn’t one to say no to a customer. He likes a challenge and encourages a similar enthusiasm in his team. Like his father, he knows that quality will win over the most challenging prospect. This dedication keeps Easy Kleen busy and growing, and will no doubt continue to do so.
Editor Robert Colman can be reached at rcolman@canadianfabweld.com.
Easy Kleen Pressure Systems Ltd., www.easykleen.com
Ferric Machinery Inc, www.ferricmachinery.com
Rogers Electric & Machine, www.rogerselectricmachine.ca
About the Author
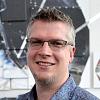
Rob Colman
1154 Warden Avenue
Toronto, M1R 0A1 Canada
905-235-0471
Robert Colman has worked as a writer and editor for more than 25 years, covering the needs of a variety of trades. He has been dedicated to the metalworking industry for the past 13 years, serving as editor for Metalworking Production & Purchasing (MP&P) and, since January 2016, the editor of Canadian Fabricating & Welding. He graduated with a B.A. degree from McGill University and a Master’s degree from UBC.
subscribe now
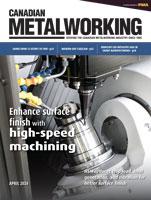
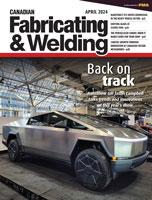
Keep up to date with the latest news, events, and technology for all things metal from our pair of monthly magazines written specifically for Canadian manufacturers!
Start Your Free Subscription- Trending Articles
Aluminum MIG welding wire upgraded with a proprietary and patented surface treatment technology
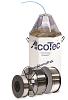
CWB Group launches full-cycle assessment and training program
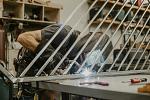
Achieving success with mechanized plasma cutting
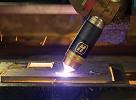
Hypertherm Associates partners with Rapyuta Robotics
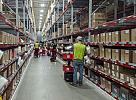
Brushless copper tubing cutter adjusts to ODs up to 2-1/8 in.
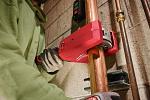
- Industry Events
MME Winnipeg
- April 30, 2024
- Winnipeg, ON Canada
CTMA Economic Uncertainty: Helping You Navigate Windsor Seminar
- April 30, 2024
- Windsor, ON Canada
CTMA Economic Uncertainty: Helping You Navigate Kitchener Seminar
- May 2, 2024
- Kitchener, ON Canada
Automate 2024
- May 6 - 9, 2024
- Chicago, IL
ANCA Open House
- May 7 - 8, 2024
- Wixom, MI