- FMA
- The Fabricator
- FABTECH
- Canadian Metalworking
Maritime Hydraulic Designs and Manufactures Equipment for Extreme Conditions
Manufacturing for Extreme Conditions
- By Sue Roberts
- June 13, 2013
- Article
- Made In Canada
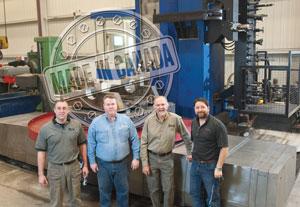
Maritime Hydraulic owners focus company efforts on the heavy industrial and oil field export markets. Shown with their new boring mill, left to right: Bert Sonier, vice president of manufacturing; Warren Fowler, quality control supervisor; Kim Carruthers, president; and Marcel Bourque, welding manager. Shareholder Gary Highfield, stockroom supervisor, is not shown.
Stabilizing pipes at 10,000 feet below the sea’s surface. Positioning rockets for space journeys. Delving into the earth for land-based oil extraction. Sounds like musings from a Jules Verne novel, but a staff of 100 at Maritime Hydraulic in Moncton, New Brunswick, designs,engineers, and produces hydraulic equipment and metal structures to accomplish these missions.
Creating hydraulics for extreme applications is only one of the company’s specialties. Custom equipment manufacturing, fabrication, CNC and conventional machining, and industrial repairs are also on the daily docket. Five facilities, clustered in and around the Caledonia Industrial Estates in Moncton, cover over 60,000 square feet. They house complete systems for heavy machining, welding, fabricating, painting, assembly, testing, and hard chrome plating.
One location, Maritime Industrial Rubber, was acquired in 2008 to fulfill the company’s need for hydraulic and industrial hoses and fittings.
MHD Offshore Group, Houston, Texas, is the company’s U.S. operation providing sales, engineering, and servicing for offshore products. A newly established Malaysian office is gearing up to perform similar duties for the Asian market.
Engineering is shared by staff in the Moncton and Houston locations, where finite element analysis ensures that there will be no stress-related issues with component specifications. Manufacturing is completed in one of the Moncton facilities.
Finished products are shipped worldwide in complete, self-contained kits. Installation and commissioning processes for the systems are also handled by Maritime Hydraulic.
“Our products are usually custom-designed and manufactured in small quantities. Most big custom cylinders are in quantities of two or four,” said Kim Carruthers, company president. “The maximum might be when we are doing a complete riser tensioner system, which might include 12 or 24 packages and require well over 200 cylinder assemblies.”
Specialization Equals Growth
Maritime Hydraulic started as a two-man operation repairing hydraulic cylinders in a New Brunswick backyard garage in the 1960s. By 1984, when Carruthers was hired to manage the company, it operated from a small facility in Fox Creek. Employee count was 25 when it moved to a new, modernized shop in 2000.
“We didn’t manufacture much in the way of product or equipment when I started with Maritime. It was just hydraulic repair,” Carruthers said. “There were numerous competitors around all chasing the same business, so it was difficult to really grow. We decided to focus on something everybody else couldn’t easily do. In late 2005 we secured our first export contract with a company in Katy, Texas. It was for telescoping hydraulic cylinders and power unit equipment. That got us in as a supplier for land-based oil rigs.”
In 2007 Maritime Hydraulic teamed up with three executives from the Houston area to form the MHD Offshore Group. “We talked with a Houston firm that was looking for riser tensioning equipment. We bid the complete system one week, they accepted it the next, and that was our entry into the offshore drilling and production industry.
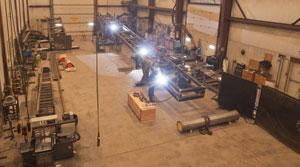
WB-qualified welders perform FCAW, GMAW, SMAW, and GTAW processes in the CWB-certified shop. Stainless steel and aluminum welding processes are segregated.
“We had never designed and manufactured anything like that before, and it was a little difficult to get the project underway. But since then they have ordered more cylinders and we still do business with them today,” Carruthers said.
A year later, in 2008, Carruthers and four others purchased the company. The business plan was straightforward: “Grow.” Each of the five stockholders contributes his own area of expertise. Bert Sonier is vice president of manufacturing, Marcel Bourque is welding manager, Gary Highfield is stockroom supervisor, and Warren Fowler is quality control supervisor.
The company charged after new business in the heavy industrial and oil field export markets, quickly gaining experience, capabilities, employees, shop floor footage, additional equipment, and sales. Growth happened fast. “In eight years we’ve gone from 25 to100 people and from $3 million in annual sales to in excess of $15 million. It’s a good story,” said Carruthers.
Reliability Is Crucial
Those first riser tensioners have been operating in about 4,000 ft. of water on a rig in the Gulf of Mexico for over three years. In each system four hydraulic cylinders push up to keep a constant tension on the drilling or production riser while it is in service.
Carruthers said, “Oil flows up the pipe that extends to the sea floor. Our equipment surrounds the pipe and keeps it from falling to the sea bed like a piece of spaghetti. Typical capacity on these systems is about 1.6 million pounds of thrust. The certifying bodies consider it one of the most critical pieces of equipment on the rig.”
The riser tensioners are built to specifications stringent enough to support the pipes and withstand movement caused by the high winds and raging waves of a thousand-year hurricane. Even the paint on the cylinders meets stringent standards. According to Sonier, the system’s surface finish is formulated to last 50 years while submerged in corrosive saltwater. A NACE-certified industrial paint engineer is on the Maritime staff at all times.
In 2010 the company supplemented manufacturing capacity with another 30,000-sq.-ft. building. The upper floors are dedicated to research, development, design, and engineering; the shop is devoted to heavy fabrication, machining, assembly, testing, and finish systems.
New equipment covers much of the shop floor. “With the expansion, we started looking at some CNC equipment because of efficiencies,” said Carruthers.
The company’s traditional machines were joined by a mix of CNC machining and fabricating equipment selected to handle large-component production: one brake; three lathes; three mills; and the newest boring mill with a 78-in. cross travel (196-in. vertical and 138-in. longitudinal), 5-in. spindle diameter, and 15-ton rotary table capacity.
“We stepped up to the plate with the automated machines,” Sonier said. “That equipment has increased our capacity tenfold, and we keep it running 18 hours a day. The boring mill was our last purchase, and it gives us more flexibility and more accuracy.”
An order for 18 production riser tensioner systems for Shell Energy North America’s Mars B project in the Gulf of Mexico is nearing completion of a three-year contract. A staff of Shell quality representatives, on-site full-time, monitors production and safety practices and conducts ongoing inspections.
“Before we received the Shell order we had to prove our concept by building a full-size mock-up of the well-bay area, where the riser goes through to the sea bottom. Shell still uses the working cardboard and PVC pipe structure at our facility to train technicians going into the field,” said Carruthers.
The weld shop is diversified and boasts a lengthy list of certifications and compliance capability, including the Canadian Welding Bureau under CSA W47.1, Division 2, and AWS
D 1.1. Various products and equipment packages have been designed and certified to the American Bureau of Shipping, DNV (Det Norske Veritas), Lloyd’s Register, and the ASME Section VIII for Boiler and Pressure Vessels. Welders are trained to perform all standard welding processes on a variety of materials.
“For the Shell project,” Bourque said, “I have to do visual inspection on every inch of weld. And for every inch I inspect, there has to be a Shell inspector with me.
“We do a lot of NDE [nondestructive examination], particularly ultrasound, to ensure the integrity of our work. Take, for example, two huge cylinders we recently manufactured. They have 3,000 pounds of weld wire in them with full-penetration welds. Not one repair.”
Precise Positioning
Orbital Sciences, working with NASA to deliver cargo to resupply the International Space Station, chose Maritime Hydraulic to provide the cylinders to raise the Antares rocket, launched in April, into position.
“Our cylinders hook underneath the rocket’s transport sled and tip it up to the vertical position. They are about 24 inches in diameter, about 25 feet long, and produce close to 1 million pounds of thrust,” said Carruthers. “It was a complex project with numerous players from the industrial sector, as well as various space, air force, and military agencies.”
Business and boundaries keep expanding. Carruthers recently closed on a contract in the Congo, visited Hyundai Corp. in Korea to discuss shipyard contracts, and worked a tradeshow in Kuala Lumpur, Malaysia.
“The Gulf of Mexico is still active but growth is slowing. A lot of the activity there now is service-related. We are setting up some agents in Korea, China, and Singapore, people who are directly involved in the shipyards,” said Carruthers. “Our Malaysian office is open and the company is ready. We’re just tapping the edge of the Asian market right now. That’s where a lot of the new work is going to be in the next 10 to 20 years.”
Another 25 percent plant expansion is being planned to keep up with the influx of projects. In the welding department, Bourque anticipates growth with the addition of sub-arc welding, more capacity, or volume welding.
“When we built the new facility we allowed for a paint shop on the back, but we’ve been so busy that it is full of machinery and material, and currently our finishing facility is off-site. Our goal is to pull the whole manufacturing operation under one roof,” Carruthers said.
“We’ll probably allow for additional square footage for another CNC boring mill or CNC equipment of some sort, depending on the contracts. We know that in the next five years we are going to need it.”
Photos, unless otherwise noted, by Marty Melanson, InColor Photographics.
subscribe now
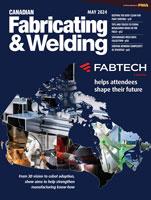
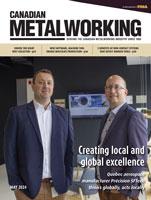
Keep up to date with the latest news, events, and technology for all things metal from our pair of monthly magazines written specifically for Canadian manufacturers!
Start Your Free Subscription- Trending Articles
- Industry Events
MME Saskatoon
- May 28, 2024
- Saskatoon, SK Canada
CME's Health & Safety Symposium for Manufacturers
- May 29, 2024
- Mississauga, ON Canada
DiPaolo Machine Tools Open House 2024
- June 4 - 5, 2024
- Mississauga, ON Canada
FABTECH Canada
- June 11 - 13, 2024
- Toronto, ON Canada
Zoller Open House & Technology Days 2024
- June 12 - 13, 2024
- Ann Arbor, MI