- FMA
- The Fabricator
- FABTECH
- Canadian Metalworking
Coatings Explained
New textured coatings can help shops successfully take on advanced materials
- January 1, 2011
- Article
- Management
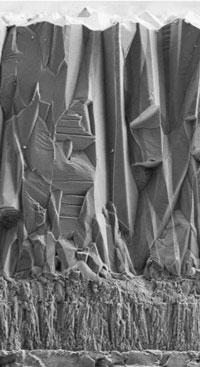
Engineer's at Seco Tools can alter the crystalline structure of aluminum oxide layer to produce a textured coating.
The materials found in shops today can be far more difficult to machine than the materials of even five years ago. These new materials reduce tool life, and failures become more common. As the properties of materials change to meet the demands of manufacturers, tooling needs to keep pace.
While coated tooling has been popular since the early 1970s, new engineering techniques have allowed coatings to change, becoming thinner, smoother, and more heat-resistant.
Coated tooling can help shops save money in day-to-day operations in a number of ways.
- Jobs can be run at higher speeds, which increases productivity, something that is essential when competing in a global marketplace.
- Tool life can be lengthened. While tool life may not have the most dramatic effect on part cost, it is worth optimizing. When compared to increases in productivity, however, it’s not as important.
- Reducing on-hand tooling inventory, when added to productivity gains and longer tool life, can achieve the ultimate goal: reducing the cost of the final part.
Thickness, smoothness, structural integrity, chemical composition, and even crystal orientation at the atomic level are some of the variables cutting tool developers can control. These can all be engineered to improve cutting tool coatings.
Many different types of coating can be found on inserts and solid-carbide tooling, such as chemical vapor deposition (CVD), physical vapor deposition (PVD), spray-on coatings, electrodeposited coatings, and organic coatings. The majority of coatings that are applied to carbide tools for use in the metal cutting industry are either CVD or PVD.
The strengths and weaknesses of these two types of popular coatings enable machinists to match their coating choice with the materials they are working with.
For example, CVD-coated tools are recommended for cutting steels and cast irons.
“CVD coatings are thicker than PVD coatings,” explained Seco Tools Turning Products Manager Don Graham. “Additionally, they incorporate a layer of aluminum oxide, which resists heat very well.”
Heat resistance is particularly critical in two aspects cutting.
“The advantage of heat resistance manifests itself in two different ways,” said Graham. “No. 1, it acts as an insulator, keeping heat out of the substrate. No. 2, the aluminum oxide is very stable chemically. This resists the particular failure mode that we refer to as cratering.”
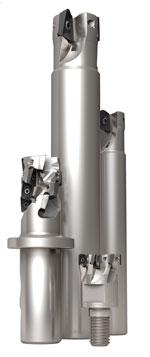
These square shoulder milling cutters feature a nickle-phosphide surface coating on their cutter bodies for longer life, better chip evacuation, and a more durable surface.
Cratering, a heat-related phenomenon, is essentially the dissolution of the insert itself. According to Graham, cratering will not occur if heat is not present.
“By keeping heat out of the substrate, it is kept harder and more wear-resistant,” said Graham. “Heat is the enemy when you are cutting steel, but it is also a very important factor when cutting other materials.”
If an aluminum oxide is present in the coating, then heat is generally transferred to the chip. The aluminum oxide will remain stable even when in the presence of high temperature.
Textured Coatings
One of the newest technologies in aluminum oxide, CVD coatings is the process of texturing.
Engineers at Seco Tools are now able to control the crystal structure—the growth of the aluminum oxide coating —to generate a smoother surface.
“We are making a smoother surface to create less friction and grabbing and promote better chip flow,” said Graham. “The difference is created because the facet of the crystal is now parallel to the insert’s surface. We are trying to orient the crystal of the aluminum oxide layer in such a way to minimize friction.”
This engineering of the coating at the atomic level achieves three goals, according to Graham:
- Textured coating is about 15 percent tougher than a nontextured, traditional coating.
- The textured coating is 10 percent harder than a conventional coating.
- The texturing process produces a better insulating property.
“When all of the advantages are put together, we believe that the end result, on average, is about a 30 percent improvement in tool life,” said Graham. “These textured coatings also cover a broader application range. A job shop that cuts a variety of ferrous materials can find advantage using one of these products because it doesn’t have to inventory as many inserts.”
PVD Coatings
High-temperature alloys, such as INCONEL®, Waspaloy®, and precipitation-hardening (PH) stainless steels, are all recommended to be cut with PVD- coated tools.
This is because with these types of metals, the predominant failure mode for a turning tool is notching – either depth of cut line notching or notching at the tip. For drills and milling inserts, the majority of failures are caused by built-up edges (BUE) and chipping.
“PVD coatings are thinner than CVD coatings and they do not reduce the toughness of the cutting edge as much as a CVD coating will. This means that less cratering and chipping will occur,” said Graham.
Achieving the most wear resistance while increasing cutting speeds without compromising toughness are the reasons for using coated tooling in an application.
Every tooling supplier offers tools that are coated. How suppliers differentiate themselves is the manner in which the layers of the coating are stacked.
For example, Seco has a coating that, while only 3 microns thick, is comprised of more than 50 layers.
“While coatings for turning and milling applications are similar, when an application calls for a solid-carbide endmill, a more exotic, special-purpose coating should be used,” said Graham.
Coated Tool Bodies
Coatings are not singularly limited to areas with cutting edges.
Seco Tools has a new nickel-based surface coating that approaches a Vickers hardness of 700 on prehardened steel cutter bodies.
“This nickel-phosphide coating is very hard and very slick. It makes the cutter bodies last longer and improve chip evacuation,” said Graham.
Future of Coatings
As materials change, the tools that cut them must change as well.
The current market trends offer a glimpse of what will be machined five years from now. Materials with a high strength-to-weight ratio will continue to be popular, and new tooling, machine tools, and techniques must provide the necessary results.
“Reducing cost per part and improving productivity are the only ways that work will remain in our factories,” said Graham. “And the best solution is a judicious selection of the best new, emerging technologies. The best new technologies provide increased productivity, thereby keeping part costs down and keeping a local factory or job shop viable.”
For more information, visit www.secotools.com.
Related Companies
subscribe now
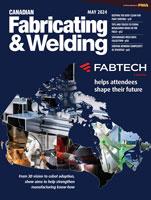
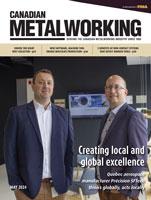
Keep up to date with the latest news, events, and technology for all things metal from our pair of monthly magazines written specifically for Canadian manufacturers!
Start Your Free Subscription- Trending Articles
- Industry Events
MME Saskatoon
- May 28, 2024
- Saskatoon, SK Canada
CME's Health & Safety Symposium for Manufacturers
- May 29, 2024
- Mississauga, ON Canada
DiPaolo Machine Tools Open House 2024
- June 4 - 5, 2024
- Mississauga, ON Canada
FABTECH Canada
- June 11 - 13, 2024
- Toronto, ON Canada
Zoller Open House & Technology Days 2024
- June 12 - 13, 2024
- Ann Arbor, MI