- FMA
- The Fabricator
- FABTECH
- Canadian Metalworking
Drilling With High Pressure
Drill quickly with better hole quality and lower tool cost
- August 1, 2009
- Article
- Metalworking
Much of the underlying science of drilling is still not understood by metal cutting professionals.
Many people with decades of experience drilling holes are even shocked when they see what a high-pressure, fully optimized drilling operation looks like.
When using a high-pressure coolant system, one of the benefits is a longer tool life. To find out why, we must look at what happens during the drilling process.
With low-pressure coolant there is typically recutting of chips as they fall back into the point of the tool and side-wall scoring from long, inconsistent chips. Needless interaction between the chips and the drill results in a lot of noise.
With high-pressure coolant, the chips formed are small, thin, and consistent. This means that you are removing heat as a variable.
If you follow the rules listed below, you will have enough coolant to absorb and transport heat and chips away from the cutting edges of the drill. The constant impact damage from chips banging on the edge of the drill is virtually eliminated with high-pressure coolant, and the edge of the tool wears out instead of failing from unnecessary damage that can occur with low-pressure or dry drilling. In manufacturing, random is bad.
The Two Rules
Follow one of these two rules when applying high-pressure coolant:
- Use 10 GPM per inch of tool diameter.
- Supply 0.5 GPM per horsepower.
Do both calculations and use the higher volume number. Even if drilling aluminum doesn’t use a lot of energy, you still need the 10 GPM per inch of diameter. When you drill INCONEL® alloy, you probably will need a lot of energy and therefore use the HP calculation.
Faster Speed
According to high-pressure coolant system manufacturer ChipBLASTER, it is normal to drill five to 20 times as many holes per minute with high pressure than with low pressure.
With low-pressure coolant, chip recutting creates spikes in the torque required to drive the drill (see Why Tools Break). This has meant running the drill slowly enough so that it won’t break even when a chip randomly wedges between the drill tip and the bottom of the hole.
Think about cutting mild steel on an engine lathe. Every operator has a “hook” to manually pull long, stringy chips away from the chip/tool interface to prevent them from breaking the tool and destroying parts. ChipBLASTER testing has shown that the force of the volume and pressure moves the chips away from the cutting edge and out of the hole without significant contact with the drill. There is no torque spike to break the drill, so it can be run at higher speeds.
Temperature control is also an important factor in drill performance. Simply stated: Speed causes heat.
Every watt of energy the drill motor uses becomes 3.4 BTU of heat in the drilling process. Most of this heat is converted from mechanical energy into heat at the tip of the drill. Properly applied coolant, in sufficient volume, controls the temperature at the tip.
The lower temperature causes a shortening of the primary shear zone ahead of the cutting edge that makes the chip much thinner. You can increase feed per revolution by up to 50 percent and still have a thin, consistent chip.
According to ChipBLASTER, coolant at 1,000 PSI is suitable for 95 percent of applications. However, if you are cutting exotics or very difficult-to-chip materials, you may need up to 3,000 PSI.
Hole Quality
With high-pressure drilling, the sides of the hole aren’t scored or damaged from heat or work-hardened, and the hole size is more consistent. This reduced surface hardening and size predictability can also result in longer tool life on subsequent tapping, boring, or reaming operations.
This is due to the small, thin, consistent chips that are formed from the cutting edge of the drill without being recut and their flow out of the hole through the flutes without catching on the margins of the drill.
The finish problems associated with low-pressure or dry cutting from chips dragging across the surface of the hole are eliminated with high-pressure coolant. High temperatures that make materials plastic and cause built-up edges are also eliminated.
The following three factors can contribute to successful drilling:
1. Look at your drill. Coolant hole size has to be big enough to pass enough coolant. If the holes in the drill are not big enough to pass 10 GPM per inch of diameter, it won’t work.
2. Look at your toolholder. The toolholder has to seal the drill so that coolant comes out only where it is supposed to.
3. Look at your coolant. Drilling requires proper lubrication. In solid carbide or cobalt twist drill applications, you should have at least 8 percent coolant concentration. The relatively large surface areas of the drill points will fail prematurely with inadequate lubricity. Also, the coolant must be filtered. Pumping abrasives at high pressure through your drill is a really bad idea.
For more information, visit www.chipblaster.com.
subscribe now
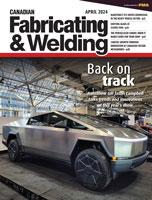
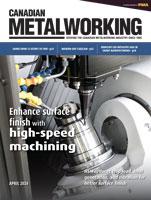
Keep up to date with the latest news, events, and technology for all things metal from our pair of monthly magazines written specifically for Canadian manufacturers!
Start Your Free Subscription- Trending Articles
- Industry Events
MME Winnipeg
- April 30, 2024
- Winnipeg, ON Canada
CTMA Economic Uncertainty: Helping You Navigate Windsor Seminar
- April 30, 2024
- Windsor, ON Canada
CTMA Economic Uncertainty: Helping You Navigate Kitchener Seminar
- May 2, 2024
- Kitchener, ON Canada
Automate 2024
- May 6 - 9, 2024
- Chicago, IL
ANCA Open House
- May 7 - 8, 2024
- Wixom, MI