- FMA
- The Fabricator
- FABTECH
- Canadian Metalworking
Machining Technology
A look inside today's milling equipment
- June 6, 2011
- Article
- Metalworking
Milling — Adjustable Gantry
MAG has added a new dimension to its universal gantry mills with an adjustable-rail W axis.
The new U6 gantry mill series can be configured with a cross rail (Y axis) up to 29.5 ft., while the adjustable W axis has up to 16.4 ft. of vertical travel to complement the maximum 8.2-ft. movement in the Z-axis ram. The design allows the cross rail to be positioned close to the part for machining with minimal ram extension and maximum stiffness for best accuracy results.
The combination of WZ and Y axes offers a height and width range up to 24.6 by 29.5 ft. to accommodate machining at the limits of the work zone, or to provide clearance to maneuver over tall workpieces. The Z-axis ram has a 25.6- by 29.5-in. rectangular cross section and supports multiple head configurations and spindle power options. Linear feed rates up to 787 IPM can be achieved.
It is available in bridge-type and rail-type platforms. The bridge-type gantry uses a stationary support and optional X-axis pallet shuttle system that moves the part to coordinates on linear guideways with rack-and-pinion drives for precise movement at high thrust levels. The rail style offers unlimited X-axis travel and is expandable to fit the application.
For more information, visit www.mag-ias.com.
Milling — Palletization
The correct pallet setup is always the one that matches the needs of the shop and its workers.
In addition to increasing productivity, integrating a pallet system can aid in job planning while improving quality control, and with no additional operator involvement needed.
“Lights-out operation is very quickly becoming a must-have for Canadian manufacturers,” explained Elliott-Matsuura Vice President of Sales and Marketing Frank Bolieiro. “This means that some sort of palletization is necessary for today’s machining centers.”
In developing the MAM72 series of five-axis vertical machining centers (VMC), Matsuura wanted to satisfy customer requirements for a unique pallet storage system. Pallets are transferred among the intermediate transfer station, storage positions, and work table by a central pick-and-place robot. The operator’s workstation also has a rotatable platen to simplify loading. The system is available with horizontal pallets or with a vertical storage setup (shown here).
Transfer time for the 130-mm pallets is 25 seconds.
“The 72 in the machine’s name stands for how many hours the machine can run unattended,” said Bolieiro. “This means that a machine can easily be loaded on a Friday afternoon and work through the weekend.”
According to the company, one key to economic and effective pallet management in multimachine installations is a pallet IC system, which has an IC memory chip on the pallet base. This chip stores the pallet number and part size information.
For more information, visit www.elliottmachinery.com.
Milling — Roller Guide
Today’s manufacturers often are called upon to mill material that is beyond the capabilities of older, less robust equipment. The new hard machining package available on the Mazak NEXUS 6800-II horizontal machining center (HMC) was designed with a high-torque, low-speed spindle head built for heavy-duty milling of tough materials.
However, it is the company’s new MX Roller Guide System that provides rigidity during milling and increases the thrust force available.
This system increases vibration dampening to extend tool life, handles higher load capacities, accelerates and decelerates faster to shorten cycle times, consumes less oil for “greener” operations, and lasts longer with less required maintenance, the company reports.
This machine also has a new 6,000-RPM, 50-HP, integral motor spindle that delivers 898 ft.-lbs. of maximum cutting torque and high-pressure coolant. Machine pallet size is 24.8 by 24.8 in., with a maximum load capacity of 3,307 lbs. The machine’s X-, Y-, and Z-axis travels measure 41.34, 35.4, and 38.5 in., respectively.
A two-pallet changer is standard.
For more information, visit www.mazakusa.com.
Milling — Rotary Options
Part quality begins at the spindle. Minimal overhang from the spindle bearings help to ensure that spindle accuracy is transferred directly to the part being machined. Most rotary tables use a collet adaptation chuck, moving the cutting several inches away from the spindle bearings.
“Back in 2008 Hardinge introduced a low-profile rotary table as a standard, no-frills unit to compete against other 210-mm tables on the market,” said Rotary Product Manager Al Comstock. “Now, by customer demand, we’ve redesigned the model to include the ... Hardinge collet-ready 16C spindle that provides the high-precision gripping options ...We’ve also extended the spindle nose for additional tooling clearance.”
What does this mean to the programmer and machine operator? According to the manufacturer, higher-accuracy jobs can be run with less tooling interference, better length control, internal gripping ability, and no fixturing time.
The table uses up to 233 ft.-lbs. of clamping torque for off-center drilling, cross-axis milling, and other high-force cutting applications.
It can operate with a servo control or be integrated with the machine via the fourth axis. Options include a left- or right-hand motor mount, pneumatic collet closer, tailstock, and a plate or cube trunnion for machining multiple parts.
For more information, visit www.hardingeus.com.
Milling — Spindle
“Makino’s ongoing titanium R&D continues to offer the most effective process solutions for a wide variety of today’s aerospace structural and engine components,” said Makino Titanium Process R&D Manager Mark Larson.
The T2 with ADVANTiGE technology was designed from the ground up for high-efficiency titanium part production. It reduces hazardous vibration and thermal conditions traditionally associated with titanium machining.
One way this machine handles vibration is through the use of new spindle technology.
Its HSK-A125 is the company’s most powerful spindle to date, delivering higher torque, horsepower, and clamping force than its predecessors. Its compact design combines the latest induction motor with twin-inverter-drive technology for 740 ft.-lbs., 133 HP continuous; 1,100 ft.-lbs., 200 HP peak.
The spindle is supported by roller bearings, which reduces the energy loss to half that of conventional gear-driven spindles, the company reports.
The spindle delivers a maximum speed of 4,000 RPM. The A and C axes improve part accessibility with a ±110-degree A-axis rotation and a 360-degree continuous C-axis rotation.
For more information, visit www.makino.com.
subscribe now
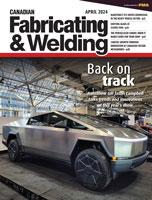
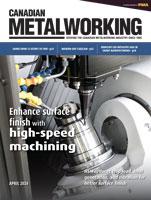
Keep up to date with the latest news, events, and technology for all things metal from our pair of monthly magazines written specifically for Canadian manufacturers!
Start Your Free Subscription- Trending Articles
- Industry Events
MME Winnipeg
- April 30, 2024
- Winnipeg, ON Canada
CTMA Economic Uncertainty: Helping You Navigate Windsor Seminar
- April 30, 2024
- Windsor, ON Canada
CTMA Economic Uncertainty: Helping You Navigate Kitchener Seminar
- May 2, 2024
- Kitchener, ON Canada
Automate 2024
- May 6 - 9, 2024
- Chicago, IL
ANCA Open House
- May 7 - 8, 2024
- Wixom, MI