- FMA
- The Fabricator
- FABTECH
- Canadian Metalworking
Where are your robots?
Is your shop ready for a robot invasion?
- By Nestor Gula
- January 1, 2015
- Article
- Automation and Software
The promise of robotic automation has been around for several decades but this revolution has come at us more like evolution. There have been various reasons why adoption of automation has been slow in the North American manufacturing sector — but the time is nigh, and robots are definitely on our doorstep.
“The last two years have been record levels for the robot industry as manufacturers adapt to a shortage of skilled workers and competing with off-shore companies,” said Chris Anderson, Product Marketing Manager — Welding at Yaskawa America.
“Robots have become more powerful in control technology, and speed while not increasing in price.” The use of robotics has improved because of speed, ease of use, productivity, reliability, and safety according to Michael Sharpe, Staff Engineer at Fanuc Robotics. “In the last three years we have seen a resurgence in reshoring, and this is one of the key things that is causing the recent economic growth. Automation has evolved quite a bit.”
The use of robots in manufacturing has replaced “the rigid, and expensive special machines – that were still customary 15 years ago – with highly flexible automation solutions,” noted Wolfgang Meisen, head of corporate communications for Kuka Robotics GmbH in Germany.
“The use of industrial robots has increased steadily in recent years. For Kuka’s customers, automation ‘made by Kuka Roboter’ is the decisive key to higher productivity and greater cost-effectiveness. It improves product quality, reduces cost-intensive use of materials and minimizes the consumption of dwindling energy resources.”
The robots that a manufacturer can acquire these days are much smarter and generally more adaptable than they were just a few years ago. “Robots are easy to operate,” said Sharpe. “It has really been brought down to that almost GameBoy/Nintendo type level where you can easily run it. It’s not difficult to program the motions, because you have pre-jogging, and the ability to visualise the 4D graphics. This reduces the risk of crashing the robot, or getting it into the wrong area. But as far as just point teaching the robots, we have really come a long way in the area of simplification.”
One reason for the robots getting smarter is the added ability for robots to “see” what they are doing. “The integration of cameras and sensors has become ‘tighter’ while the cost of electronics has come down,” said Anderson.
“This provides higher level capability for the robot to do less structured tasks. In addition, robot design and sensors are combining to provide human scale ergonomics and perception to perform more assembly type applications.”
The integration of sensors and safety enables increasing production flexibility.
“Multi-functional robot controls can take over additional tasks which are needed for a complete robot-based automation solution, like process control, motion control of additional axis, NC-motion, logic control, safety control,” said Meisen.
“Integrated solutions reduce investment costs, reduce the communication effort between the different components, lead to an improved process quality (since motion and process control are optimally synchronized), and facilitate configuration, and diagnosis since the operator has only one user-interface.
Simplified configuration, programming, and engineering reduce set-up times due to powerful, integrated engineering tools. Compliant and sensor-based motion enables programming of complex assembly tasks in significantly shorter times than programming with position-controlled approaches. Moreover, compliant motion in combination with safety enables teaching by manually guiding the robot.”
A new development, Kinetiq Teaching, makes the robot “smart” by interpreting the forces generated by a programmer gripping the robot’s welding torch and guiding it into proper location. Designed mostly for welding, “No in-depth programming knowledge is now required to program a robot,” says Guy Robert, Marketing Director of Robotiq.
Combined with a simplified graphic interface on the touch screen, the robot can be programmed in less time, and requires less skill/training. This can help job shops justify robotics by reducing the set-up time for new parts and allowing the programming task to be performed by the robot operator. In the past, industrial robots were used almost exclusively in the automotive sector, and in series production.
Robotics are now more flexible, and can be adapted to nearly any task. “You are seeing more robots in press brake, and forming applications,” says Sharpe. “There are new sensors, and the integration of these sensors to the robot motion path to allow the robot to follow the path or the bend of the tube off a tube bender or sheet metal off a press brake.”
With the expansion into new industries and areas of robotic automation, there are new requirements for the development of robots. “Thanks to the systematic, ongoing development of robot, and control technology, KUKA robots have now become established in many other sectors besides the automotive industry,” said Meisen.
[gallery type="slideshow" ids="101032,100662,100520,96261"]
“The primary objective here is the development of applications in new markets – particularly in the fields of foodstuffs, plastics, metalworking, foundry, electronics, medical technology, and the entertainment industry.”
Robots, and even the control units, are becoming smaller and more compact, which minimizes required floor space and offers opportunities to integrate more robots, and increase the productivity.
“With energy-efficient controls, and weight reduction of the robots, energy consumption can be reduced,” he said.
Mobile platforms lead to more flexible production concepts since the robot can move to the place where it is needed, instead of being fixed to the ground.
“More flexible logistics concepts can be realized with mobile platforms in industrial production compared to inflexible conveyor solutions,” said Meisen.
“Industrial production benefits from the optimal integration of robots in the production system. Robots can be programmed in the same manner like other machines, namely with a PLC, and adequate function blocks.”
The increase use of robots in manufacturing means less labour force is needed, and implies there could be a resurgence of manufacturing in Canada and North America.
“Manufacturing output has continued to rise over recent decades without a corresponding rise in labour,” according to Anderson.
“Global competition, and rising healthcare costs have increased the pressure to increase output with lower costs. The aging workforce population is resulting in a shortage of the labour pool for skilled manufacturing workers.”
Sharpe states that, “robotics haven’t really displaced many workers, but it has changed or shifted what their application is, and what they are doing on the job site.”
“When purchasing a new piece of fabricating equipment, it is best to look at robotic or automated load/unload of the machine at that time,” said Anderson.
“When looking at current operations, such as welding, adding a robotic welder to increase capacity may be a more practical investment than hiring more welders. Several companies have indicated they are adding robotic welders simply because they can not fill manual welder positions.”
About the Author
subscribe now
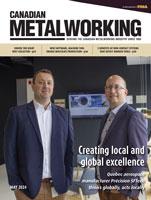
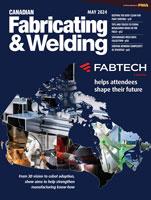
Keep up to date with the latest news, events, and technology for all things metal from our pair of monthly magazines written specifically for Canadian manufacturers!
Start Your Free Subscription- Industry Events
MME Saskatoon
- May 28, 2024
- Saskatoon, SK Canada
CME's Health & Safety Symposium for Manufacturers
- May 29, 2024
- Mississauga, ON Canada
DiPaolo Machine Tools Open House 2024
- June 4 - 5, 2024
- Mississauga, ON Canada
FABTECH Canada
- June 11 - 13, 2024
- Toronto, ON Canada
Zoller Open House & Technology Days 2024
- June 12 - 13, 2024
- Ann Arbor, MI