- FMA
- The Fabricator
- FABTECH
- Canadian Metalworking
Plasma unleashed
New technologies have greatly enhanced plasma cutting capability.
- By Nestor Gula
- May 6, 2015
- Article
- Fabricating
It is more than likely most of us heard of the term plasma while watching the original series of Star Trek. Yes, they had their handheld Phasers, set to stun, but the plasma cannons were more or less standard star ship armaments used by both the Starfleet Federation (Captain Kirk and company) and the dreaded Romulan Star Empire.
In the real world, plasma refers to a process of cutting metal where a gas—usually shop air, but for specific purposes can be pure oxygen or other gases—is blown out of a nozzle at high speed while an electric arc is formed simultaneously with the work surface through this gas turning the latter into a plasma. The plasma becomes hot enough to cut metal, and the speed of the air pushes all the molten bits of metal away.
“One of the fantastic things about plasma is its versatility,” says Michelle Avila, public relations manager for Hypertherm. “Generally though, plasma is considered ideal when cutting any electrically conductive material greater than 1/4-inch in thickness but less than two inches.”
This isn’t to say plasma isn’t good at cutting thicknesses outside that range. It is; although, there are other methods in addition to plasma to consider.
Plasma cutting was developed in the 1960s and came to its fore in the ‘80s and ‘90s when the plasma cutting heads were mounted to CNC machines to produce accurate and repeatable cuts on sheet metal. With new technologies emerging, like water jet and laser cutting, plasma cutting has been facing competition in the sheet metal cutting sector.
Plasma cutting can be the best solution depending on the individual application.
“Plasma offers an optimal blend of cut quality, productivity, operating cost and versatility,” says Douglas Shuda, director of marketing, global cutting technologies at ESAB Welding & Cutting Products. The process delivers a very good cut quality combined with high productivity, coming from high cut speeds and rapid cut-to-cut cycle times. Plasma also handles a broad range of material types and thicknesses when compared with other cutting technologies, Shuda explains. “In addition, the initial cost of a plasma system is lower than a laser or water jet.”
One of the earliest drawbacks of the plasma cutting systems was the cut quality and the accumulation of molten metal on the bottom of the cut, known as dross.
“Dross on the underside of the cut material may require a secondary cleaning process. This is very easy to remove with a chipping handle,” says Steve Hidden, business development manager, Miller Electric Mfg. Co. “Dross build up can be minimized by accurate speed compensation for the amperage of machine versus the thickness of materials.”
Newer plasma technology has reduced the amount of dross that is left behind. “With high density plasmas, dross is kept to a minimum and if the material is cut at the proper speed you will only find slow speed dross around holes and corners,” says Mark Osowski, director global sales at Burny & Kaliburn, a Lincoln Electric Company. “This slow speed dross can be easily chipped off and does not require a grinding operation. With high density plasma, you should have smooth and square cuts.”
Since there is a lot of heat generated when plasma cutting the cut edges might get warped and a bluing of the metal might occur, leading to secondary cleaning processes before the part can go forward in the fabrication process. “A small heat affected zone exists after cutting with plasma and may need to be addressed,” says Hidden.
With a high quality plasma system and supporting items like the right CNC, a torch height control, software, etc. and a table with good motion capabilities, then no secondary processes are needed, explains Avila. “You can get good, clean cuts on the first pass. But there are some caveats. You need to follow book specifications—have the right amperage, correct cutting speeds, torch to work piece distance, etc. If you find yourself having to do a lot of secondary work, then something is wrong and it’s time to start troubleshooting.”
There is a remarkable difference between today’s plasma cutting systems compared with systems from the ‘80s. This will be apparent to anybody who has used an older and newer machine. “Hypertherm alone has made dozens of major advances starting in 1993 with our introduction of HyDefinition plasma,” says Avila. “It significantly narrowed the gap between plasma and laser cut quality. The introduction of HyPerformance plasma a decade later only narrowed this gap even more by adding faster cut speeds and twice the consumable life. Actually, consumable life has increased 10 fold during the past 30 years. Add in newer advances like True Hole technology for cutting bolt-ready holes, True Bevel for more consistent beveled edges, and Rapid Part technology for reduced non-cutting (or cut-to-cut cycle) time and the capabilities of today’s plasma is nothing like the systems of old.”
Where older machines were large cumbersome and the plasma arc made a noise like a howling dervish, modern machines are civilized compact and more powerful. “Inverter technology has enabled Miller to reduce the size of a plasma cutter and still offer extreme cutting power in smaller, portable packages weighing less than 20 lbs.” says Hidden. “Torch and consumable technology offers increased precision of the cut. Some companies offer high definition cutting on CNC tables and the quality of the cut is very good.”
High definition type plasma cutting systems have greatly improved the quality of the cut and “get closer to laser cutting,” says Tass Hamstra, territory manager for Machitech Automation. “Things like Hypertherm’s True Hole Technology have improved hole cutting quality of plasma in recent years.” The capabilities of plasma and the CNC machines have also seen great strides. “The other big improvement is five-axis bevel cutting,” he says. “We have had great success with these in the past few years, allowing our customers to weld prep bevel right on the machine, eliminating handling and manual grinding or torch cutting for weld prep. All types of bevels are able to be programmed including K bevel and countersink holes.”
With significant improvements in cut quality, the plasma systems have also made great strides in plasma process technology, gas management, and the cutting application process technology.
Modern plasma systems are also more automated. “Piercing, cutting holes and beveling are all operations that are vastly improved in capability and consistency,” says Shuda. “Today we can cut thicker materials and the cut quality is significantly better in terms of angularity, surface finish, top edge rounding, and levels of dross.”
Shuda explains that they have also advanced plasma cutting by further automating and integrating the process technology so that there’s less reliance on the operator to get an optimal result. Applications like cutting hole slots have become more automated and the automated process ensures consistent, high quality results. This is also true with bevel cutting.
“Plasma cutting is more automated, which means that the outcome of the process is less dependent on the skill and knowledge of the operator,” he says.
With a much improved cut edge, plasma cutting systems can compete with other cutting systems. Plasma cutting is faster than other methods on thicker material. “Plasma is definitely the fastest, most productive of all the processes when cutting metal greater than ¼-inch but less than 2-inch,” says Avila. “In addition, its ability to cut a wide variety of electrically conductive materials provides great versatility.” Quicker cutting means greater productivity. “It’s also a cleaner process than water jet, which requires an underwater garnet and high clean up. These are two key advantages that plasma has over water jet. Compared to laser cutting, plasma offers a lower total cost of ownership,” adds Shuda.
Generally speaking, a plasma system provides higher reliability and requires less maintenance and troubleshooting than a typical CO2 laser. When compared to oxy-fuel, plasma cutting generally provides a better cut quality and higher cutting speeds torch to torch, which means more productivity. And, plasma can handle a wider range of materials where oxy-fuel will not cut non-carbon steel, Shuda explains.
Plasma cutting systems have evolved into sophisticated machines able to cut a wide variety of shapes into metal. “We can cut fairly intricate shapes but there are limitations, kerf widths of .03 to .08 inches are typical depending on the process,” says Hamstra. “True Hole technology allows us to cut holes of 1:1 inches MS up to 1-inch thick. Hypertherm also has HDi technology for intricate cutting on stainless. Plasma as a process does not have the same tolerances as laser or water jet, that’s why we manufacture machines with all of these technologies, the right machine for the right application.”
Choosing between a handheld plasma system and an automated one is really not an issue as many, if not most, machines can work in either scenario. “Some conventional mechanized plasma systems can be converted to manual/handheld by changing out the torch leads and torch head,” says Osowski.
High density plasmas are normally dedicated automation systems and cannot be converted. Smaller shops may want to initially invest in a handheld system and adapt it later with a CNC-driven table.
“You can adapt a hand torch for machine use, but we do not recommend it. One reason is safety. All hand torches have a safety switch,” says Jim Colt, applications technology manager for Hypertherm. He explains, in order to make the hand torch work on a machine you’d have to break into the torch assembly to bypass the safety trigger. Machine torches, at least for Hypertherm Powermax systems, interface directly to the rear panel CPC interface connector. The start signal on this connector will not work with a hand torch for safety reasons.
Another reason not to adapt the hand torch for machine use is torch life. “A hand torch mounted on a machine will not last as long as a machine torch because blow back and spatter is sure to stick to the handle and switch. Machine torches are smooth and straight for a reason. Also, it is much harder to square a hand torch to the plate because the hand torch doesn’t have the same mounting brackets,” says Colt. “Now, this does not mean you need to buy a dedicated plasma unit. All Powermax systems—with the exception of our Powermax30 series—come with a quick disconnect feature so you can easily switch between the two torch types. You can keep your machine torch mounted to the table for CNC jobs, and easily plug in a hand torch for hand cutting jobs when needed.”
About the Author
subscribe now
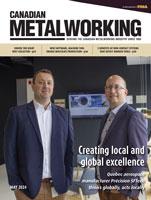
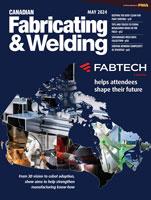
Keep up to date with the latest news, events, and technology for all things metal from our pair of monthly magazines written specifically for Canadian manufacturers!
Start Your Free Subscription- Industry Events
MME Saskatoon
- May 28, 2024
- Saskatoon, SK Canada
CME's Health & Safety Symposium for Manufacturers
- May 29, 2024
- Mississauga, ON Canada
DiPaolo Machine Tools Open House 2024
- June 4 - 5, 2024
- Mississauga, ON Canada
FABTECH Canada
- June 11 - 13, 2024
- Toronto, ON Canada
Zoller Open House & Technology Days 2024
- June 12 - 13, 2024
- Ann Arbor, MI