- FMA
- The Fabricator
- FABTECH
- Canadian Metalworking
Wesgar continues to innovate with Finn-Power punch presses
Port Coquitlam, BC-At Wesgar Industries Ltd., Port Coquitlam, B. C., art meets science, and several pieces of Finn-Power equipment are helping the precision sheet metal manufacturer to bridge that gap."Our people add the art of manufacturing to the science of metal work," explains Wesgar President John Thwaites. "The value we can provide our customers is a result of our continuous innovation in manufacturing."Perhaps the most telling aspect of Wesgar's operational philosophy is its unusual corporate slogan-Artistry in Metal. Wesgar backs up this lofty goal with its well-deserved reputation for quality products and excellent customer service earned during its 40 years of operation. Its customers include many major players in the electronics, power supply, telecommunications, medical, environmental control, and radio frequency industries in markets throughout Canada, Europe, the United States, and Mexico.In its early days, Wesgar was involved in manufacturing more traditional industrial products. Through the years the company has evolved into a premiere precision sheet metal fabricator with 135 employees housed in a 55,000 sq. ft. facility. By 2000, the company's sheet metal fabrication's capacity was concentrated in three stand alone mechanical turret punch presses.
- May 25, 2005
- News Release
- Fabricating
Wesgar management decided it was time for a change in both manufacturing philosophy and equipment. A technical team was organized and a thorough search for fabrication equipment that would best meet Wesgar's current and future needs was launched. "We wanted to increase our capacity, efficiency, and quality," explains Thwaites.Wesgar chose the F6 Express Flexible Manufacturing Unit (FMU) from Finn-Power International Inc., Schaumburg, IL (finnpower.com) as the system that best fit its needs. The F6 Express FMU automatically loads full-sized sheets onto the table of the turret punch press, punches and forms the sheet metal, and then unloads the fabricated sheet. The F6 Express dramatically increased Wesgar's productivity by putting through up to 50% more total volume with less than half the people. Being able to run full-sized sheets also eliminated a great deal of shearing and material handling. "The automation provided by the Finn-Power F6 Express has allowed us to reallocate those key employees to work centers where they can multi-level their skills and disciplines."In mid-2004, Wesgar was ready to replace its two remaining mechanical turret punch presses and once again turned to Finn-Power for equipment. "It was time to add capacity, tighten up tolerances, and to consolidate programming software and tooling," says Thwaites. "Running two types of OEM punching technology was not an efficient way to run the plant."Wesgar management formed a second technical team to review production requirements, the current customer base, and what current and future fabrication processes would be. "We had selected Finn-Power as the equipment OEM of the future," explains Thwaites. "But we had to decide on what type of punching product we needed within the Finn-Power family." By utilizing a single manufacturer, Wesgar was able to simplify its operator training and ensure that all its operators could run all of the turret punch presses. According to Moe Sadain, production manager with Wesgar, after months of self-examination, which included lean manufacturing training from an outside consultant, the company found that its needs were not in the area of high-volume punching. "We discovered that we needed a smaller machine that was more flexible for both small and occasional large volume jobs, as well as forming capabilities." Adds Al Purdey, manager, quality and continuous improvement, "An analysis of the jobs going through our plant showed that 60-70% of them required one or two blanks. While we were pleased with the F6 Express, we were running 80% of our volume on one machine. We wanted to spread this work over three machines with shared tooling and programming." Having the three machines gives Wesgar the ability to insert customer rush jobs without disrupting the production schedule and also provides for quick turnaround on customer prototypes.In mid-2004, Wesgar decided to purchase two C5 hydraulic turret punch presses from Finn-Power. The 20-station, 33-ton C5 hydraulic turret punch press has a maximum sheet capacity of 50 in x 100 in. (1270 mm x 2500 mm) and is available with either Siemens or Fanuc controls.Tooling flexibility is also important to Wesgar. Up to 10 auto-index and Multi-Tool holders may be installed in a Finn-Power turret. Wesgar has four Multi-Tool cassettes in both C5 turret punch presses-two 24 stations, one 10 station, and an 8 station. Wesgar also has four full tonnage auto-index stations and two indexable upforming stations in each turret, for a total of 82 tools in each machine. Unique to the C5 turret punch press, full tonnage indexable upforming allows complex forming operations to be made quickly by using a single forming tool. An index mechanism is used to turn the forming tool into an NC programmed angle.Finn-Power's upforming feature provides a precise process for knock-outs, louvers, and other forming. Finn-Power resolved the conventional problem of the die height impeding free sheet movement. Finn-Power's design allows forming heights up to 0.62 in. (16 mm) with the forms made by the die moving upwards and then retracting, allowing completely free sheet movement, eliminating scratched or jammed sheets. Special tooling is also important to Wesgar. The company has 120 different types of specials to emboss, lance, form, countersink, counterbore, knockouts, etc. The C5's new HNC100 digital servo ram controls allows Wesgar to punch 0.25 in. HRS right down to 0.020 in. polycarbonate materials with fully M2 guided punches as small as 0.031 in. in diameter.The C5's large trap door was another important feature for Wesgar. Finn-Power's Catch and Carry work chute allows the reception of several components to 19.7 in. x 19.7 in. (500 mm x 500 mm) and subsequent stacking. "A large percentage of our parts can pass through the trap door, thereby eliminating the entire shaker part process," explains Thwaites. With the stringent cosmetic requirements of its customers, Wesgar purchased the vacuum slug remover option along with the fully guided Multi-Tools and their solid one-piece stripper plates, and the brush tables in order to reduce part marking to an absolute minimum.And how have the two C5's performed since their installation? "Before the addition of the C5s, we were running 24/7," explains Thwaites. "Today, we are running 24/5 and sales are up 10%...basically running fewer shifts and producing more. In essence, we've gained 28% capacity and increased throughput 35-40%."finnpower.com
subscribe now
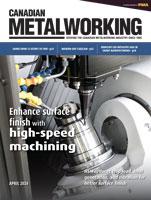
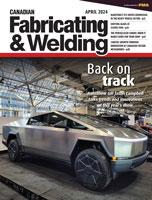
Keep up to date with the latest news, events, and technology for all things metal from our pair of monthly magazines written specifically for Canadian manufacturers!
Start Your Free Subscription- Trending Articles
Aluminum MIG welding wire upgraded with a proprietary and patented surface treatment technology
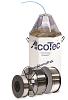
Achieving success with mechanized plasma cutting
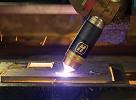
Hypertherm Associates partners with Rapyuta Robotics
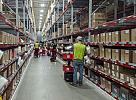
Gema welcomes controller

Brushless copper tubing cutter adjusts to ODs up to 2-1/8 in.
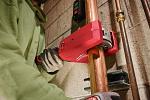
- Industry Events
MME Winnipeg
- April 30, 2024
- Winnipeg, ON Canada
CTMA Economic Uncertainty: Helping You Navigate Windsor Seminar
- April 30, 2024
- Windsor, ON Canada
CTMA Economic Uncertainty: Helping You Navigate Kitchener Seminar
- May 2, 2024
- Kitchener, ON Canada
Automate 2024
- May 6 - 9, 2024
- Chicago, IL
ANCA Open House
- May 7 - 8, 2024
- Wixom, MI