- FMA
- The Fabricator
- FABTECH
- Canadian Metalworking
Speed to Market One Layer at a Time
Efficiently produce metal prototypes and low-volume parts using additive manufacturing
- By Mark Barfoot
- July 16, 2014
- Article
- Made In Canada
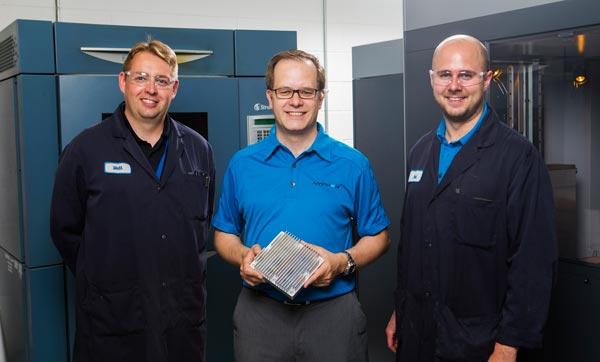
(left to right) Matthew Yates, Managing Director Mark Barfoot, and Paul Hojan stand in front of a few of the company’s additive manufacturing machines used to produce metal prototypes and low-volume parts. Photo by Jon Evans Photography.
It can be costly, time-consuming, and challenging to create a metal prototype that is representative of the final part, particularly if you are trying to simulate casting or another production process. A variety of techniques can improve on traditional methods to reduce design cycle time, producing prototypes or low-volume parts to introduce products to market quickly. These processes offer efficiency gains while also proving to be cost-effective.
When Plastic Is An Option
For early prototypes, a plastic representative model may be sufficient to review the shape and see how pieces fit together. If plastic is a viable option, various additive manufacturing methods can produce a part within a shorter time frame than traditional machining. In fact, between two to three iterations of a design can be completed within the time it would take to make the first metal prototype.
Plastic materials in additive manufacturing have vastly improved from 20 years ago and, in some cases, may be strong enough for the end application. Ultem is one material used in fused deposition modeling (FDM) because of its high strength and resistance to chemicals. Some of the selective laser sintered (SLS) nylonfilled materials also have increased strengths that may be a fit. Even stereolithography (SLA) technology can be used with new, ceramic-filled materials that increase part strength and durability.
But regardless of the material you choose—plastic, nylon, composite, or metal—various additive manufacturing options can help you to create the first part quickly.
Investment Casting Using Additive Manufacturing
Using additive manufacturing, a plastic or wax master for use in investment casting can be printed within 24 to 36 hours. The master is then encapsulated in sand to create a mold. The mold is used to produce a part from standard cast materials (such as aluminum, steel, stainless steel, or brass) using a traditional investment casting process. The most prevalent additive manufacturing process to use for investment casting is SLS. This process builds the master by depositing layer after layer of powdered material. A laser process solidifies each layer. A similar method, often used for small castings such as jewelry or medical components, uses an inkjet process to create a master with a more precise geometry.
Additive manufacturing can create a casting with similar process tolerances as regular investment castings. However, most parts will still need to be postmachined for critical tolerances, so it is important to include touch points and/or sacrificial mounts in the part design to allow for easy postmachining. Another consideration is adding material to the model if you plan on postmachining. This method often can produce a casting from start to finish in less than 10 days.
3-D-Printed Casting Molds
Using additive manufacturing to print a mold is another efficient option. This process spreads a layer of sand and then sprays a binder that solidifies the material. Once the mold is printed, it is removed from the excess sand and sintered to increase its strength. The 3-D-printed mold is then ready to be used to produce a casting by traditional methods. When using this process, take into account the shrinkage effects of the sintering process with the sand mold.
The sand mold technology has the advantage of speed. It can build the entire volume area (over 1 m3) in under 24 hours. This is significantly faster than other additive manufacturing methods. This same type of machine can be used to additive-manufacture an actual part in steel, but because of the sintering process, it is less accurate. It is mostly used for large castings that are simply impractical to build using other additive methods.
CNC-machined Prototypes and Parts
While the CNC machining process may require longer and higher-cost programming cycles, there are benefits to machining prototypes and lowvolume production parts. Five-axis machining is useful not only for creating complex shapes, but also to speed up production by reducing setup time. To take advantage of machining benefits, it is important to find a shop that specializes in prototyping. CNC machining can provide highaccuracy parts, and it is a well-understood and readily available technology.
Two Types of Metal Sintering
Metal sintering is an additive manufacturing process that uses powdered metal materials in the sintering process. There are a variety of companies and technologies on the market, but the process typically involves one of two primary methods:
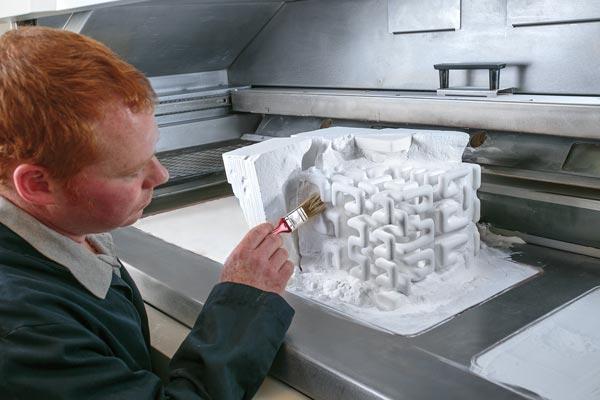
Powder support material is easily brushed away from a prototype produced using a selective laser sintering process.
1. A layer of powdered metal is spread out in the machine bed and a laser solidifies layer upon layer to create the part.
2. Powder is fed through a tube and exits right at the focal point of the laser, solidifying it in place. This method is not widely commercially available at this time.
One point that is often overlooked while building a part by metal sintering is including support material for internal features, overhangs, and so forth. The same material used to create the part is used for the support material. Once the part build is complete, you remove the support material. In some cases, it can be easily popped off, but CNC or EDM technology will probably be needed to completely remove the support material to eliminate any residue. Parts with intricate internal geometry may not allow you enough access to adequately remove the support material, making other processes more desirable.
In the method where the powder is fed through a tube and solidified at the focal point, the part can be rotated during the build process, which minimizes the need for support material.
Metal sintering most likely will require a change in part geometry to reduce the support structure needed and make production easier. An example is to use oval holes that don’t require internal support as opposed to perfectly round holes. If this method can create the desired geometry, it can offer the benefit of making final parts that require no postmachining. Complex geometries that cannot be machined also can be created.
Part builds should be stressrelieved before and possibly after you remove them from the build platform to ensure they don’t warp or deform.
Advances in Hybrid Processes
As additive manufacturing technology continues to evolve, OEMs are introducing hybrid machines. These machines use the metal sintering additive manufacturing process to build the part and CNC machining to improve the accuracy of the sintered part. The geometry and application of a part will determine which additive manufacturing process will save the most production time and money, and whether the technology will be brought inhouse or provided by a service bureau.
Benefits to working with an additive manufacturing service bureau before adding the process to in-house capabilities include the opportunity to test a variety of processes to determine which is most appropriate. A service bureau will also provide guidance for selecting the best process for specific applications. Having a choice of multiple additive manufacturing processes—rather than being tied to a single process— can also encourage innovation and efficiency in part development and design.b Photos courtesy of Hyphen unless otherwise noted.
subscribe now
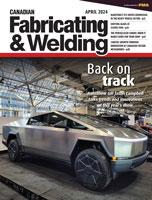
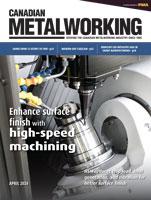
Keep up to date with the latest news, events, and technology for all things metal from our pair of monthly magazines written specifically for Canadian manufacturers!
Start Your Free Subscription- Trending Articles
- Industry Events
MME Winnipeg
- April 30, 2024
- Winnipeg, ON Canada
CTMA Economic Uncertainty: Helping You Navigate Windsor Seminar
- April 30, 2024
- Windsor, ON Canada
CTMA Economic Uncertainty: Helping You Navigate Kitchener Seminar
- May 2, 2024
- Kitchener, ON Canada
Automate 2024
- May 6 - 9, 2024
- Chicago, IL
ANCA Open House
- May 7 - 8, 2024
- Wixom, MI