- FMA
- The Fabricator
- FABTECH
- Canadian Metalworking
The Future of CNC Is Now
New control technology enables better communication among different systems, including robots
- April 18, 2013
- Article
- Automation and Software
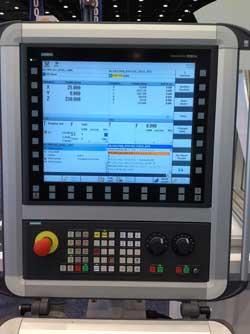
By reducing the number of programming languages and control panel layouts that employees need to be familiar with, both start-up and changeover times can be reduced, which will directly improve productivity.
Smart machining. Intelligent controls. Adaptive manufacturing. The buzzwords of yesterday are finally becoming reality.
The world has become "computerized," and so too has the job shop. Today's machine tools are complicated, complex, and very rarely stand alone. They almost always are connected to something, be it automation, an enterprise resource planning (ERP) system, or in situ measurement equipment. And, the more systems that are connected together, the more likely a communication problem becomes.
However, CNC developers, machine tool builders, and robot suppliers are beginning to join forces to make communication easier and streamline the programming process.
Several years ago machine tool builder Okuma, Charlotte, N.C., started Partners in THINC, a manufacturing industry collaboration based on its open-architecture, PC-based THINC®-OSP control. Today more than 40 well-known technology companies are sharing their knowledge and experience to make it easier for their separate technologies to work together.
"It's imperative that we make these systems easier to use, and one way to do that is by combining all of the control functions into one common language, in one control," said Jeff Estes, director of Partners in THINC.
It's becoming critical that these manufacturing cells are easy to operate, especially at a time when shops are struggling to find qualified, skilled labor.
"A lot of talent has left the manufacturing industry both from attrition and also for the so-called greener pastures of other industries," said Estes. "That talent is needed more than ever today because the technology of the manufacturing sector is becoming more advanced and complex.
"Also, today's generation of workers has grown up with technology. They don't remember what it was like to live without computers, and they expect technology to work easily together. Unfortunately in the manufacturing sector, we are just starting to create the plug-and-play technology that is so common in personal computing."
Real-world Applications
One of the collaborations between Okuma and robotics manufacturer ABB has produced an interface to streamline the programming of robotic machine tending.
Seeing a robot and CNC machine paired together is not an uncommon sight. Robots typically are used to load/unload parts or perform a dedicated operation either inside or outside of the machine's work envelope.
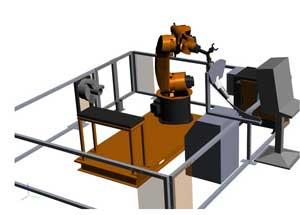
Once the robot is integrated directly through a single control, it is treated as an extension of the machine tool itself, not a separate entity.
The benefits of this type of automation include increased spindle utilization and lower costs per part. Robots also free up workers from dangerous or repetitious tasks.
In the past robots and CNC machines needed separate programming software and separate control panels. Now the Okuma/ABB interface makes it possible to operate and observe both systems with one control panel.
"There is more than just the machine tool and the robot involved as well," said Estes. "There are grippers, workholding, high-pressure coolant systems, conveyors, gauging, and many other technologies that must work hand-in-hand to make any operation successful."
While the Okuma/ABB interface is new, Okuma also has similar interfaces with robotics suppliers FANUC and KUKA.
"It's about making these technologies communicate better and work easily together. And, at the same time, it's also about getting these technologies operational in manufacturing facilities faster," said Estes.
Two main features of the new interface help simplify programming and operation. The first is the graphical interface, which now allows the operator to control the robot's movements, as well as monitor and organize the display of all input and output signals from both the robot and the machine tool. The system also tracks errors and advises the operator on how to fix them.
The second feature is an extendable programming setup that allows the operator to create code faster and easier.
"The faster a manufacturing company gets its staff up to speed on a new system, the faster they are making parts, and the faster they are making money," said Estes.
By reducing the number of programming languages and control panel layouts that employees need to be familiar with, both start-up and changeover times can be reduced, which will directly improve productivity.
Working Together
At last year's International Manufacturing Technology Show (IMTS), CNC developer Siemens and robotic supplier KUKA also leaped into this area by integrating KUKA's mxAutomation with the Sinumerik CNC platform.
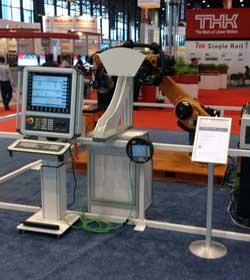
CNC developers and robot suppliers are joining forces to make communication easier and streamline the programming process.
With this system, the operator of the machine can run both the machine tool and robot from the single control panel.
"The reasoning behind this integration was that anyone who has experience with our CNC system can program the robot without the need to learn a new control setup," said Jason Dube, applications engineer with Siemens.
The motion sequence of the robot is entirely engineered within the Sinumerik CNC, then transferred by its PLC function to the mxAutomation interpreter of the robot. All program changes are input on a second channel of the CNC. According to Dube, this scenario provides the ability not only to run a machine tool's automation sequence more efficiently, but also to make faster changes on-the-fly to minimize machine downtime, with no special knowledge of robot programming language needed. During the operation of the machine tool, all changes made can be visualized directly on the CNC screen, further minimizing operator actions.
"From a Siemens standpoint, we had a lot of the infrastructure already in place to allow this to happen. We essentially just added an extra layer of control capability that enables input coming from the HMI to be transferred through the CNC to the robot," said Dube.
The Importance of the HMI
With any control, easy, intuitive interactivity through the HMI is important. It may seem like adding a robot would make this interaction more difficult, but Dube said this is not the case.
"Once the robot is integrated directly through a single control, it is treated as an extension of the machine tool itself, not a separate entity," said Dube. "It is essentially another axis grouping of the machine tool, and that's how the control treats it."
The robot can be positioned motor by motor and jogged into position, or it can be moved based on the tool point. Any alarms that are raised during positioning or during the machining process are shown on the control's screen in a single location.
"We've eliminated the need for the operator to work at the robot," said Dube. "All of the work is performed at the common interface. From this location, the operator can diagnose problems with the machine tool and also diagnose problems with the robot as well."
Maintenance staff, operators, and programmers can work faster and need less training to operate and troubleshoot both the machine tool and the robot because of the comfort level they have with a single control.
Programming Changes
While making changes to robot or machine tool performance at the machine is a time-waster that should be eliminated whenever possible, it still occurs, especially during the beginning stages of a new setup. Robot programming at the CNC reduces the time it takes operators to perform these on-the-fly changes.
"We have programming cycle support interface screens to help the operator edit the part programs directly at the CNC," said Dube. "You can even observe both the cycles of the machine and the robot on a single screen to make sure the programs are synced properly. If you have part programming knowledge using the Siemens control, you can now use that same knowledge base to program the movement and operation of the robot."
According to Dube, this eliminates the need for the programmer to have a background in robotics.
The Fab Five
In order for automation to be successful, five parts of the process need to be addressed and perfected.
1. The process. Everything starts with a good machining process, explained Jeff Estes, director of Partners in THINC.
"The process needs to be proven out before automation is ever brought into the equation," he said. "It also needs to be repeatable."
2. Chip control. Like any other machining operation, chips need to be properly created and evacuated. When long, stringy chips are created, there must be a way to get those chips away from the part and turret and onto the conveyor, or into the chip collection area.
3. Tool management. Tool management becomes even more important in an automated system. Automation will double spindle utilization rates, which means more tools will be necessary. Shops need to have the correct tools loaded in the machine for the job or jobs that will be run, as well as have redundant tools loaded for when they are needed. A presetter should also be used, said Estes.
4. Measurement. A truly automated system also includes part inspection. In an automated system, no person is dedicated to examining parts and making changes to the process on-the-fly. An automated system needs to make adjustments automatically if the statistical process control (SPC) starts showing a trend that eventually will lead to a nonconforming part.
5. Workholding. In an automated cell, there are two workholding locations, one within the machine that holds the part during machining, and the second on the automation system. The workholding needs to be flexible enough that it doesn't require an excessive amount of time to set up during part changeovers.
"If you have a firm grasp on these areas, you are likely going to double your spindle utilization, and your process will run perfectly day in and day out for a long time," said Estes. "There also is a misconception that these systems are only for high volumes, but that is not necessarily the case. It can be for a volume of one if you think through the process and have the correct process, tool strategy, chip creation, inspection, and workholding."
subscribe now
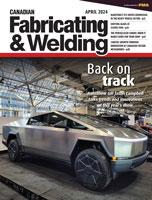
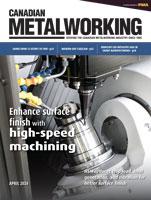
Keep up to date with the latest news, events, and technology for all things metal from our pair of monthly magazines written specifically for Canadian manufacturers!
Start Your Free Subscription- Trending Articles
Automating additive manufacturing
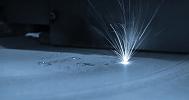
Sustainability Analyzer Tool helps users measure and reduce carbon footprint
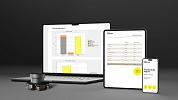
Sandvik Coromant hosts workforce development event empowering young women in manufacturing
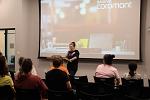
GF Machining Solutions names managing director and head of market region North and Central Americas
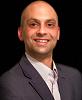
Mitutoyo updates its end-user portal
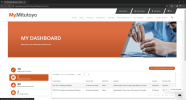
- Industry Events
CTMA Economic Uncertainty: Helping You Navigate Kitchener Seminar
- May 2, 2024
- Kitchener, ON Canada
Automate 2024
- May 6 - 9, 2024
- Chicago, IL
ANCA Open House
- May 7 - 8, 2024
- Wixom, MI
17th annual Joint Open House
- May 8 - 9, 2024
- Oakville and Mississauga, ON Canada
MME Saskatoon
- May 28, 2024
- Saskatoon, SK Canada