- FMA
- The Fabricator
- FABTECH
- Canadian Metalworking
Shop floor secrets revealed
Improving productivity in cutting tools.
- By Nate Hendley
- January 19, 2015
- Article
- Cutting Tools
“Anybody can produce a cutting tool. But there are many secrets to making it work at optimum performance,” notes Cullen Morrison, business development manager of threading at KOMET of America, headquartered in Schaumburg, Illinois.
A wise observation, indeed.
Here are some of those secrets, revealed through interviews with industry experts:
IF SPEED IS THE SINGLE BIGGEST FACTOR IMPACTING CUTTING TOOL LIFE, IS THERE A SINGLE BIGGEST FACTOR IMPACTING TOOL PRODUCTIVITY? WOULD IT BE SPEED, FEED OR SOMETHING ELSE?
“I wouldn’t really say it’s one main thing. It’s kind of a combination of different things. The overall performance of your cutting tool depends on speed, feed and depth of cut and also the material you machine. Those would be the main factors in my opinion,” says Steve Geisel, senior product manager, Iscar Tools in Oakville, Ontario.
“Speed, feed and depth of cut. They’re all related in how the parameters of cutting tools work, but the biggest factor impacting productivity to me is the tool path itself—the programming. [There’s new CAM technology] where even using the same tool you can dramatically improve your productivity by changing your cutter path and choosing new strategies,” says Daniel Kennedy, who works for Walter Canada, a branch of Walter USA, headquartered in Waukesha, Wisconsin.
AS A GENERAL RULE-OF-THUMB, IS IT POSSIBLE TO GET LONG TOOL LIFE AND HIGH PRODUCTIVITY FROM THE SAME CUTTING TOOL?
“If the tool is properly designed for the job, then yes this is possible. Often we find shops using tools designed for another purpose and they usually will not be able to achieve long tool life and productivity relative to a specialty tool,” says Morrison.
“The answer is, ‘it depends.’ It depends on the machine type, torque curve of the spindle and type of fixturing to name a few things. But if the capability is there, increasing the feedrate and/or speed can sometimes increase both tool life and productivity,” says Scott Etling, director of global product management in indexable milling at Kennametal in Latrobe, Pennsylvania.
WHAT ROLE DOES THE SHAPE OF THE INSERT PLAY IN TERMS OF CUTTING TOOL PRODUCTIVITY?
“Basically, the shape of the insert that people are going to use is really dependent on the type of workpiece they are trying to machine. So can it play a factor? Yes, it definitely can. When you talk about turning, sure you can still use high speed turning tools that can drastically reduce machining time. But then again, you can only use those tools if the workpiece you’re machining allows it. You can’t just apply any type of cutting tool to any type of workpiece and think, ‘Oh, I’m going to get awesome productivity!’” says Geisel.
“This is one of the key factors for any machining process. The shape of the chip formed is critical for evacuation from any machining process, but you also have to account for how the tool engages the material. For example, in cast iron materials we can approach the part with a neutral or even negative rake angle which creates a very strong cutting edge but a poor shearing action. However the properties of cast iron cause it to break into a powdery chip when machined so a shearing action is not really needed. With materials like stainless steel a positive cutting angle is usually needed to get the chip to form and break without creating too much heat and work hardening the part. The shape of the insert including topography of the cutting edge and chip breaker as well the coating and substrate material all have key roles in chip formation and evacuation,” says Morrison.
“We always recommend going with the strongest geometry. If you look at ISO standards, the round insert is going to be your strongest geometry by the nature of its shape,” says Chad Miller, product manager for turning and advanced materials at Seco Tools in Troy, Michigan.
ARE THERE ANY COMMON MISTAKES MACHINISTS MAKE THAT ARE DETRIMENTAL TO PRODUCTIVITY?
“Yes. They choose the wrong insert for the type of machining they want to do. You have to understand, when you’re machining, you’ve got to select the proper cutting tool. If you don’t, you’re [not] only sacrificing productivity, you’re sacrificing tool life and could be sacrificing part quality,” says Geisel.
“Not using their spindle to its full potential. It’s a common one that I walk into. I’ll use turning as an example: when in a roughing operation, there are people out there who won’t use all the horsepower (hp) they have available. If you’re not roughing close to your peak hp, my first question is ‘Why not?’…when you’re using every single hp you have and you can’t push that tool any farther, you change your [insert] shape. Now you can affect the amount of power that the tool draws to increase productivity yet again,” says Kennedy.
“On the first signs of premature wear—chatter or chipping—many machinists will turn down the override controlling the feedrate. Depending on the situation, most times it is better to increase the feedrate,” says Etling.
“Under utilizing the tools. Our tools are designed to run as fast and productive as possible. If they are not used that way, they might not generate enough heat at the cutting edge for the coating to work properly, causing a built up edge and/or changing how the chip is formed. For example, feeding a drill too slow in carbon steel will result in a long stringy chip that the flute design of a high performance carbide twist drill is not designed to handle. By increasing the feedrate and cutting speed to the parameters the drill was designed to run, usually good chip formation and evacuation happens…this is also commonly seen with taps. Out of fear, a lot of shops run them too slowly causing the chips to not form correctly,” says Morrison.
ARE THERE ANY CUTTING OR MACHINING TECHNIQUES THAT ARE GREAT FOR ENSURING HIGH PRODUCTIVITY BUT DESTRUCTIVE FOR CUTTING TOOLS AND INSERTS?
“Probably not one particular technique applies. But in general, too much speed and/or too much feed is detrimental to tool life but good for productivity,” says Morrison.
“One example would be placement of the milling cutter on the workpiece—thinking that using the entire diameter of the milling cutter would improve productivity. What can go wrong is the entry angle of the insert entering the workpiece can be at the weakest point of the inserts/cutter pocket combination. Sometimes it is best to move the centerline of the cutter body off of the workpiece in order to lead the insert into the workpiece with less entry force,” adds Etling.
DOES DIRECT CONSISTENT COOLING USUALLY EQUAL HIGH PRODUCTIVITY?
“Generally, I’ll go with ‘yes’ on that. Again, it’s application specific. I mean, you wouldn’t cut stainless steel dry. At the same time I wouldn’t advise running coolant on an indexable milling cutter in steel … but as a general rule of thumb, I would say direct, consistent cooling does improve your productivity,” says Kennedy.
“In milling steel, cast and some stainless steels we always recommend cutting dry. However, the addition of coolant in these areas can help chip evacuation and surface finish so it is sometimes more productive to use coolant. In heat resistant super alloys and aluminum, coolant is a must,” says Brian MacNeil, milling products and applications specialist at Sandvik Canada in Mississauga, Ontario.
“Productivity is directly related to coolant pressure. For example, if you have a low pressure system, you are definitely not going to be as productive as somebody that’s got a 1,000 psi coolant pump. With higher pressure in the coolant, you’re cooling the chip faster, lubricating the cut better and reducing the amount of heat generated in the cut. There’s so much volume and so much pressure going through the heat being generated, it will cool much more rapidly. Because of that, you can technically run a much faster spindle speed or increased speed rate or a better depth of cut. Because you’re cooling it so drastically, you can increase your parameters and get the part done quicker,” says Geisel.
“Select the proper coolant for the application you’re doing. The coolant you’re going to use on a lathe is not the same coolant you’re going to use on a mill. They have completely different properties. Make sure you’re using the proper coolant for the type of machining you’re doing. If you’re doing a lot of tapping on your machine then obviously you’re going to have additives inside the coolant that will facilitate better performance for tapping. If you’re doing hole-making, you’re going to have different properties in that type of coolant that will provide you with better performance for drilling and reaming,” he continues.
IN YOUR EXPERIENCE, DO MACHINISTS CARE MORE ABOUT TOOL LIFE THAN CUTTING TOOL PRODUCTIVITY?
“Yes, up until we come in and show them what productivity they are capable of … our rule of thumb is, your tooling costs should be five per cent of your input costs…when you’re concerned about that five per cent at the expense of the other 95 per cent, the focus needs to shift. Yes, the cost of tooling does need to be a consideration, but it shouldn’t be the main consideration. The main consideration should be how much productivity you can get out of that tool before you need to replace it,” says Kennedy.
“Depends on what type of industry. If you go into automotive, it’s high volume, with lots of deadlines—‘We’ve got to get ‘x’ number of parts through the door each day.’ They’re really concerned about productivity. You see them running inserts a bit faster in both speed and feed than typically what’s recommended…just because they are more concerned about productivity. Now, on the flipside of that, go into aerospace. Say they’re machining a jet engine component. Productivity is important to them but not nearly as important as the quality of that component. So we see them running parameters that are a bit more conservative, so they get longer tool life. The reason being, they want to make sure that insert completes the part. When machining jet engine components, they can’t have an insert break,” says Miller.
ANY PARTING THOUGHTS?
“For one of my customers, we did almost a full conversion in their shop. Initially, their tool spends went up for the first couple months, but after they had been up and running for six months, they were putting 50 per cent more product out the door, for about 10 per cent more tool expenditure per month. The tooling was more expensive, but they were putting out that much more product. It was making them money,” says Kennedy.
About the Author
subscribe now
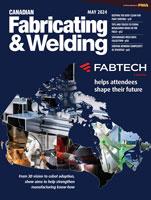
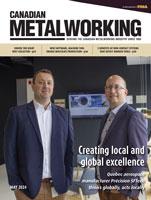
Keep up to date with the latest news, events, and technology for all things metal from our pair of monthly magazines written specifically for Canadian manufacturers!
Start Your Free Subscription- Industry Events
MME Saskatoon
- May 28, 2024
- Saskatoon, SK Canada
CME's Health & Safety Symposium for Manufacturers
- May 29, 2024
- Mississauga, ON Canada
DiPaolo Machine Tools Open House 2024
- June 4 - 5, 2024
- Mississauga, ON Canada
FABTECH Canada
- June 11 - 13, 2024
- Toronto, ON Canada
Zoller Open House & Technology Days 2024
- June 12 - 13, 2024
- Ann Arbor, MI