- FMA
- The Fabricator
- FABTECH
- Canadian Metalworking
Additive in Flight
Metal 3D printed parts gaining aerospace acceptance.
- By Doug Picklyk
- February 15, 2016
- Article
- Metalworking
Each fall in Las Vegas design software giant Autodesk holds a massive user-group conference, Autodesk University, bringing together some 10,000 attendees from various industries to share knowledge and reveal new developments. At the 2015 event a unique-looking metal structure was rolled out onto a stage, demonstrating the potential for a major shift in aerospace manufacturing. The tall semi-circular lattice-type object is part of structural partition wall destined for an Airbus A320 airplane, and when pieced together it is the world’s largest metal 3D printed airplane component.
The project was a collaboration among Airbus, Autodesk, APWorks (an Airbus subsidiary dedicated to additive manufacturing) and The Living, a New York-based design studio. Called the “bionic partition,” the “organic” part design mimics cellular structure and bone growth.
“This is not just an interesting hypothetical experiment—this is a fully functioning component we can expect to see being deployed in aircraft in the very near future,” said Jeff Kowalski, chief technology officer of Autodesk. The partition had already completed its first phase of testing and is due to be involved in test flights this year.
The parts were “printed” using EOS M400 and Concept Laser M2 machines, and 122 of the 162 parts were made of Scalmalloy, a patented aluminium-magnesium-scandium alloy created by APWorks.
The remaining 40 parts are titanium.
The 3D printed part is 45 per cent (30 kg) lighter than the current A320 component, and according to Airbus the new design, when applied to an entire airplane cabin and the current backlog of A320 planes, will save up to 465,000 metric tons of CO2 emissions per year.
This is not the first time Airbus has endorsed 3D printed parts in weight reduction strategy, and there is a cost savings component as well. A common term in the aerospace component industry is the buy-to-fly ratio—the weight ratio between the raw material purchased to make a component and the part’s final weight. Machining blocks of titanium and other expensive super alloys return large ratios, up to 90 per cent, with a lot of chips heading to recycling. When these components can be printed from metal powders, the ratio is closer to 1:1.
In 2014 Airbus made news about an additively manufactured titanium cabin bracket being used on board the new Airbus A350 XWB test aircraft. The bracket weighs 30 per cent less than the traditionally cast or milled parts, and the brackets are expected to enter serial production as early as this year.
Using 3D printing to replace machining in part development and prototyping alone is an obvious time saver. Peter Sander, head of emerging technologies and concepts with Airbus has noted “Previously we budgeted around six months to develop a component—now it’s down to one month.”
Of course design and development is one thing—getting parts through qualification and testing to get a component into production is another story. Last fall at the first Advanced Manufacturing Canada Conference and Exhibition, held at the Palais des Congrés in Montreal (Nov. 18-19), Julien Chaussée, engineering specialist in the core structures team at Bombardier product development, spoke about an ongoing project to introduce a 3D-printed metal part into a future Bombardier aircraft.
“Our philosophy is changing a lot,” said Chaussée, with respect to 3D printing. He was tasked with doing the research to prove the technology can deliver savings in both weight and cost. “The technology must justify itself,” he said, noting there was still the requirement to separate the hype from reality.
In selecting a test component, his team partnered with Montreal-based additive manufacturing shop FusiA (because of its previous aerospace experience). The team elected to optimize the design and 3D print a 6- x 5- x 3-inch door hinge bracket made of titanium.
Following multiple design iterations, in his projected cost analysis, Chaussée believes that over time they can get to a final 3D-printed part that will weigh less and cost less to produce than existing machined parts.
He noted that having a printed sample to show management went a long way in securing approval to proceed with the project. Still in the R&D phase, “We’re close to prototype production,” noted Chaussée, who added that in the next four to five years he anticipates a metal 3D printed product will show up on a Bombardier aircraft.
GE Aviation claims to be the largest user of additive technologies with metals, and 2016 is expected to mark the introduction of its 3D-printed metal fuel nozzles taking flight in a commercial aircraft engine. Each CFM LEAP engine (CFM is a joint venture between GE and SAFRAN of France) will have 19 3D-printed fuel nozzles. These parts are 25 per cent lighter, consolidate 18 parts into 1 and introduce more intricate design and supports resulting in 5x higher durability than conventional manufacturing.
With several thousand orders for new LEAP engines (Airbus A320neo and Boeing 737MAX) GE Aviation anticipates producing more than 100,000 metal 3D-printed parts by 2020.
As adoption begins on commercial aircraft, true large-scale additive manufacturing production for more than a few parts remains years away. The supply chain to feed into the industry is developing slowly, and questions remain concerning process, quality and inspection practices.
Of course aerospace is not alone in pioneering metal additive manufacturing. Dental and medical device manufacturing has been qualifying and implementing the technology for years, and the mold and die industry is embracing additive for high-value low-run projects. And the possibilities for broader automotive parts manufacturing, along with every other industrial sector, will continue to emerge as build rates and envelope sizes of the metal-based additive technologies continue to increase.
For now, developments going on at major aerospace OEM’s are being closely guarded, but as more revelations like the bionic partition continue to emerge the real disruption that metal 3D printing will introduce to manufacturing will become apparent.
About the Author
subscribe now
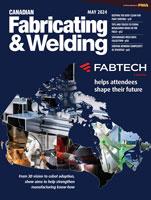
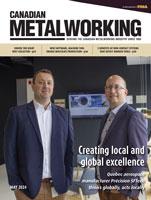
Keep up to date with the latest news, events, and technology for all things metal from our pair of monthly magazines written specifically for Canadian manufacturers!
Start Your Free Subscription- Industry Events
MME Saskatoon
- May 28, 2024
- Saskatoon, SK Canada
CME's Health & Safety Symposium for Manufacturers
- May 29, 2024
- Mississauga, ON Canada
DiPaolo Machine Tools Open House 2024
- June 4 - 5, 2024
- Mississauga, ON Canada
FABTECH Canada
- June 11 - 13, 2024
- Toronto, ON Canada
Zoller Open House & Technology Days 2024
- June 12 - 13, 2024
- Ann Arbor, MI