- FMA
- The Fabricator
- FABTECH
- Canadian Metalworking
Get the most out of HMLV grinding
Reducing non-productive time results in more throughput, better profits
- April 25, 2019
- Article
- Metalworking
High-mix, low-volume (HMLV) grinding is becoming more popular in Canadian manufacturing shops. Canadian Metalworking (CM) asked Hans Ueltschi, vice-president of sales, cylindrical division at United Grinding North America, for his advice on this type of production. Here’s what he had to say.
CM: What influences are leading to the need for HMLV grinding?
Ueltschi: I would say that the biggest drivers of this type of production environment are constant consumer demands for new and different products and product variations and the ever-shortening time-to-market product cycles. To compete and succeed in such an environment, today’s manufacturers must be lean and always strive to reduce WIP as well as target single-part-flow production to provide just-in-time delivery.
CM: Why is HMLV manufacturing more difficult in grinding than other types of machining?
Ueltschi: Unlike other machining operations that use cutting tools and inserts that are easily changed out, grinding, in most instances, involves profiled grinding wheels as the cutting tools.
When parts or part shapes change, so too must the profiles on a grinding wheel, meaning the wheel needs to be redressed or changed out to another. This can be a time-consuming task. Add to this the fact that grinding is a much higher precision process, and as such, programming and setups must be precise and performed carefully. But the features and capabilities of today’s universal grinding systems do help shops quickly switch from one job to the next.
CM: How important is reducing changeover time in HMLV production?
Ueltschi: Fast changeover times are critical in an HMLV production environment.
While there are several grinding system advancements that help shorten part changeovers per se, an even more effective time-saving approach is to process parts as close to complete as possible in one grinding machine setup.
CM: How important is reducing dressing times?
Ueltschi: In the grinding operation, wheel dressing is non-cut/non-machining time, so the faster it is completed, the faster a machine can get back to producing parts. Additionally, wheel changeovers are non-productive time as well, so multiple-wheel wheelheads significantly shorten change time as compared to single-wheel machines.
United Grinding, 2100 United Grinding Blvd., Miamisburg, Ohio 45342, 937-859-1975, www.grinding.com.
subscribe now
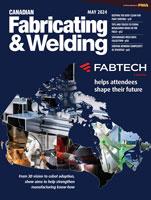
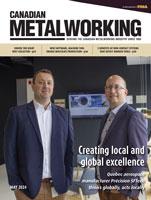
Keep up to date with the latest news, events, and technology for all things metal from our pair of monthly magazines written specifically for Canadian manufacturers!
Start Your Free Subscription- Industry Events
MME Saskatoon
- May 28, 2024
- Saskatoon, SK Canada
CME's Health & Safety Symposium for Manufacturers
- May 29, 2024
- Mississauga, ON Canada
DiPaolo Machine Tools Open House 2024
- June 4 - 5, 2024
- Mississauga, ON Canada
FABTECH Canada
- June 11 - 13, 2024
- Toronto, ON Canada
Zoller Open House & Technology Days 2024
- June 12 - 13, 2024
- Ann Arbor, MI