P.R. Project Manager
- FMA
- The Fabricator
- FABTECH
- Canadian Metalworking
Redesigning precision tooling with AM
Additive manufacturing creates new designs, reduces weight for tooling
- By Patricia Hubert
- July 11, 2019
- Article
- Metalworking
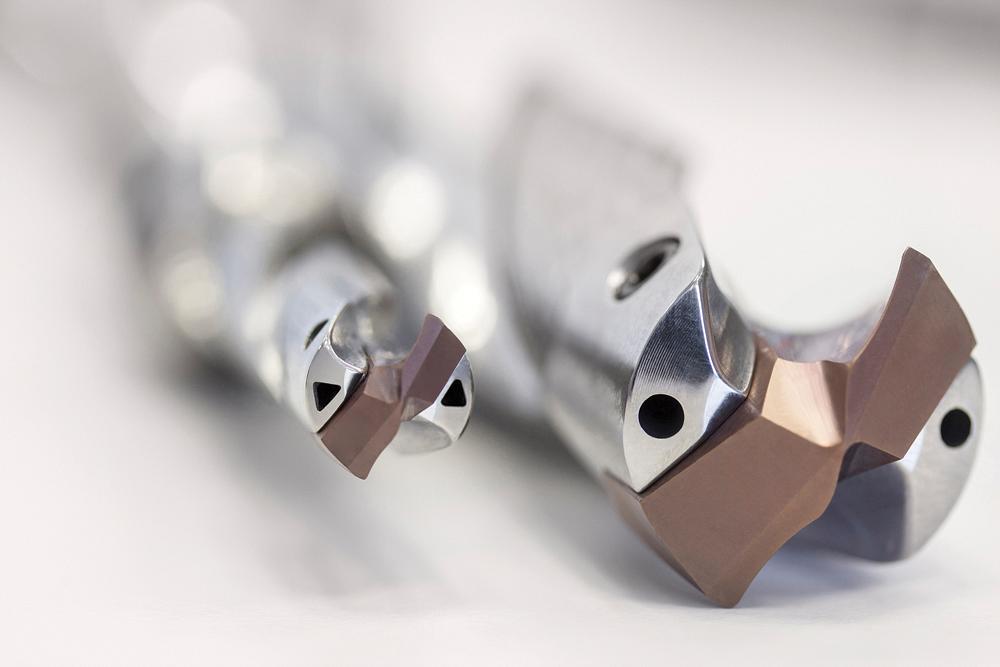
The QTD indexable insert drill is a hybrid model, produced using a combination of conventional and additive manufacturing.
Metal additive manufacturing (AM) creates the kind of design freedom that conventional manufacturing designers can only dream about, and the possibilities that it opens up are things that many people find fascinating.
As long ago as 2013, management at Mapal was convinced that 3D printing offered enormous potential for manufacturing precision cutting tools. More than five years has passed since then, and the company has developed and launched many products for series production that previously were inconceivable.
“At first we didn’t have any specific ideas of how AM would be useful in the production of tools,” said Dr. Jochen Kress, president of the Mapal Group, Aalen, Germany. “But what we did have were the ingenuity and the motivation required to research an entirely new technology.”
Consequently, in 2013 the company invested in its first 3D printer, a system for selective laser melting from Concept Laser. The result came a year later.
In 2014 Mapal’s first additively manufactured product was ready for series production: the QTD indexable insert drill for 8 to 13 mm diameters.
“For this tool, we made good use of the design freedom that AM offers,” said Kress.
The tool’s twisted design and the geometry of the cooling channel bores are impossible to manufacture using conventional means. According to the manufacturer, this new design significantly improved coolant flow.
The company now is researching how AM can improve its existing products for reaming, fine boring, drilling, milling, and clamping. However, Kress added that the company will use AM to make tools only if doing so will very clearly offer added value.
Redefining external reaming
The company’s second AM product was an external reamer that is lighter than its conventionally made counterpart. External reamers, which are used for fine machining of outer surfaces, often work better the lighter they are.
A specially developed ribbed structure inside the tool, which cannot be made by conventional means, reduced the tool’s weight by more than half. The tool can work at much higher speeds and with much greater accuracy.
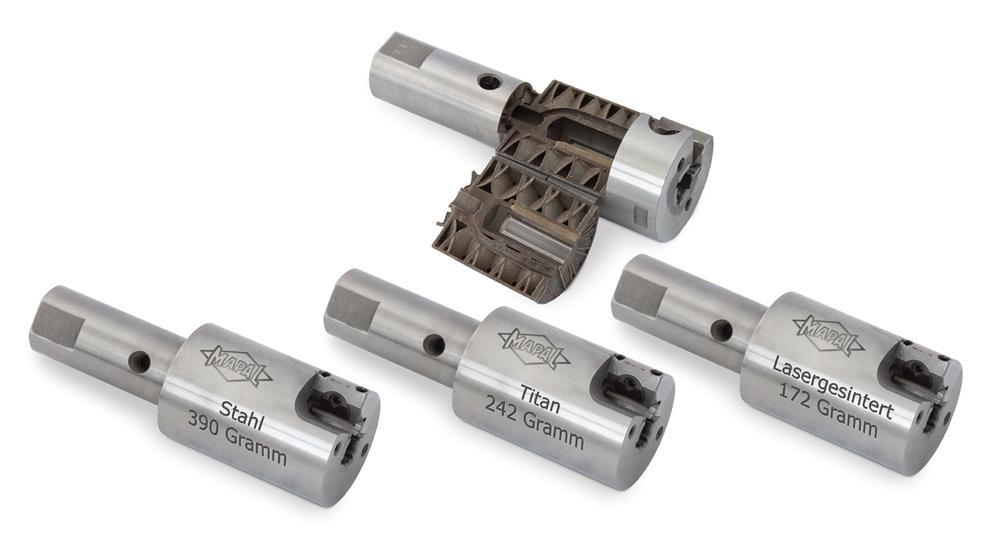
Thanks to their ribbed internal structure, the additively manufactured external reamers are less than half the weight of their conventionally manufactured counterparts.
This lightweighting option is available in other tools as well. For example, the company is currently making sophisticated tools for transmission housings with ribbed internal structures.
“Not only does this save weight, but AM means that there is a lot less work involved in making this type of tool,” said Dr. Dirk Sellmer, vice president of R&D at Mapal.
Pushing boundaries in clamping
Mapal manufactures hydraulic chucks essentially as a single piece, without a brazed joint between the tool body and the expanding sleeve. This used to be something of a limiting factor and was responsible for the fact that, for the most part, hydraulic chucks could be used only at operating temperatures of 70 degrees C or lower. The additively manufactured HTC hydraulic chucks are able to be used in temperatures up to 170 degrees C.
The operating temperature range is not the only improvement resulting from AM. In addition, the benefits of the hydraulic clamping technology now can be combined with the back taper of 3 degrees that is common in shrink chucks. These narrower contours make these chucks suitable for all machining when contours are critical.
Thanks to 3D printing, it is possible to carry out various adjustments for chucks. Hydraulic chucks can be made much longer, thinner, and more stable.
Integrated cooling circuit
The new possibilities that have opened up in tool clamping technology also can be applied to “exotic” applications. During friction stir welding, for example, the rotating tool is immersed in the material and then moved between two aluminum workpieces to be joined. The high process temperatures cause the material to plasticize, forming a strong, vacuum-tight joint when it cools. However, the process heat is carried via the tool and clamping tool to the spindle, which can result in the spindle expanding. This creates a situation in which the SK connections are not axially secured to slide.
Cooling presents an additional problem when the spindle resecures the clamping tool, which may have slipped, and creates a connection that can no longer be removed. The costs from this scenario can be significant.
For this application, Mapal has made a tool chuck with integrated cooling circuits and a Weldon connection. The internal air supply is routed via the spindle and can be fine-tuned. The entire system remains stable during friction stir welding.
The future of AM tools
Amid all the euphoria and the seemingly unlimited possibilities, and despite the technology being ready for mass production, AM with metallic materials does have its limits.
One definite constraint comes in the form of the costs. The prices of the powders used and the methods themselves make the process more costly than conventional methods of tool manufacturing. Accuracy is also limited, meaning that to be totally successful, the tools should be machined.
Patricia Hubert is P.R. project manager for Mapal, Obere Bahnstraße 13, 73431 Aalen, Germany, 49-7361-5850, www.mapal.com.
About the Author
Related Companies
subscribe now
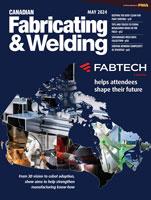
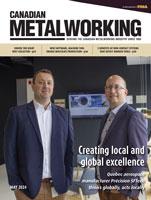
Keep up to date with the latest news, events, and technology for all things metal from our pair of monthly magazines written specifically for Canadian manufacturers!
Start Your Free Subscription- Trending Articles
Modest manufacturing growth appears likely
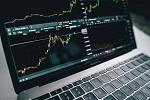
There’s no business like show business
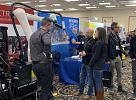
Tighitco, DCM Group Aerospace join forces on Airbus A220 program
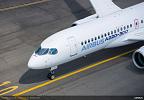
Software automatically identifies vulnerable production assets
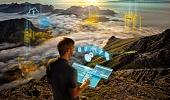
NAIT names Sandvik Coromant the 2024 Distinguished Industry Partner

- Industry Events
MME Saskatoon
- May 28, 2024
- Saskatoon, SK Canada
CME's Health & Safety Symposium for Manufacturers
- May 29, 2024
- Mississauga, ON Canada
DiPaolo Machine Tools Open House 2024
- June 4 - 5, 2024
- Mississauga, ON Canada
FABTECH Canada
- June 11 - 13, 2024
- Toronto, ON Canada
Zoller Open House & Technology Days 2024
- June 12 - 13, 2024
- Ann Arbor, MI