Application Engineer
- FMA
- The Fabricator
- FABTECH
- Canadian Metalworking
The right kind of grind
High-mix, low volume grinding is made possible with the right technology, mindset
- By David Goetz and Taqwa Gilani
- April 23, 2019
- Article
- Metalworking
Today’s manufacturers must produce complicated parts that are higher in precision, but lower in quantity. This is especially true in industries such as aerospace, medical, energy, and power generation.
Now this manufacturing trend is beginning to migrate to grinding operations, and as large markets like the automotive industry evolve and incorporate new and different components, this trend likely will continue.
A company’s operators need to understand the grinding process and how to quickly adjust machines to ensure top performance for the abrasives and grinder. An operator needs to be able to change over and set up the machine without making a lot of scrap. The also operator has to know that the production run is fixed to a specific number of parts. Getting the grinder dialed in and in production quickly is very important.
The main influences driving production to a high-mix, low-volume (HMLV) grinding model are the principles of lean manufacturing and the general desire to be profitable.
Lean manufacturing has evolved many times, but it always strives to improve efficiency, reduce waste, and maximize profitability for the company employing its concepts. One of the biggest wastes in traditional high-volume production grinding is the creation of work-in-process (WIP).
When the production run is large, it typically involves multiple production steps that cannot always be completed systematically or in a timely manner. In other words, WIP tends to accumulate. One way to reduce WIP is to decrease the batch sizes manufactured.
When the batch sizes are decreased, parts take much less time to go from the design stage to shipping. Lead and production times are reduced, which shows up as a savings because holding costs are reduced or oftentimes eliminated, because the finished products are shipped to the end user as soon as they are completed.
For a just in time system, this can be a significant benefit to the manufacturer and its customer.
HMLV requires efficiency
Another factor driving manufacturers to a HMLV model is the desire to keep machine-related costs down.
In traditional high-volume processes, the cost of running multiple machines is offset by the demand for the component. As the demand for the part is reduced, however, those costs can climb. Using an efficient grinding process to diversify and increase the number of different parts being produced, manufacturers can take on work even at lower volumes.
This can keep grinding operations running at a high capacity and can help reduce manufacturing costs to remain profitable.
Understand the process
Seven factors must be considered to understand the grinding process. They are:
- Material
- Severity of operation
- Required finish and form
- Area of contact
- Wheel speed
- Coolant use
- Horsepower
Although some of these are fixed by the grinding machine that is being used, others are not and can be very different from workpiece to workpiece. As long as the mix of parts that need to be ground have the same or similar material properties, stock removal needs, form, geometries (or sizes), and finish requirements, the same abrasives potentially can be used, eliminating the need for multiple setups and decreasing wheel inventories.
However, if the mix is more diverse, then each part likely requires very different abrasive products, resulting in a new grinding wheel, and different setup for each part.
Having to perform many setups or work changeovers contradicts a major concept of lean manufacturing. By increasing the non-production-related time needed to change over machinery for each part type, waste and additional cost is introduced. Waste also is introduced if different grinding wheels need to be kept in inventory to suit each different part being ground. This also can open the door to supply chain issues, if wheels are not managed properly.
Products exist that are capable of grinding numerous materials with little change in performance.
Abrasives such as Norton Quantum have proven to be capable of grinding many types of metals both ferrous and non-ferrous, and several alloys. The new Norton Vitrium bond also is suitable for form holding and longer life. Having a premium wheel allows manufacturers to potentially use a single wheel for multiple part types.
Superabrasives also can be an option if there are fewer wheel/part profile changes required when changing from part to part.
Reduce changeover time
It is very important to reduce changeover time in HMLV grinding. Labour usually constitutes an average of 31 per cent of the overall cost per part.
Changeovers always takes time and increasing the number of setups increases labour costs. Related downtime also is another source of waste, so limiting the time required to change part types and resume production quickly, minimizes costs. And, the more parts that can be made from a single abrasive product, the better.
By manufacturing parts with similar size, shape, finish requirements, fewer setups and changeovers are required, saving time. If the wheel profile doesn’t need to be changed or significantly altered, it will not only reduce changeover time, but also make the abrasive product last longer because it will not require extensive truing and dressing to change wheel geometry.
Dressing and truing
Routine dressing during a production run typically doesn’t take too long. But truing and dressing a wheel to change over a grinder for a different part can require a large amount of time. Whether truing in a new or different wheel when the part changes, or changing the profile on an existing wheel to accommodate a part change, the less time that is spent truing and dressing, the more time one can spend grinding parts.
Reducing the number of dressing cycles outside of production also reduces dresser and wheel wear, improving operating costs.
Dressing time can be reduced by using the proper wheel type or specification.
Using premium abrasives that hold form and require less dressing during production means more time is spent in production and less in dressing, resulting in reduced grinding time per part.
The dressing time can also be eliminated or reduced based on the batch size.
If the number of required parts is less than the required dress rate for the wheel, it would only need to be trued and dressed as part of the setup. The entire run of parts would be ground without the wheel being dressed until the next setup or changeover.
Dressing time also can be reduced or eliminated through continuous dressing. In continuous-dress, creep-feed grinding (often used in the aerospace industry), wheel truing and dressing is performed continuously while the wheel is grinding, eliminating the need for a separate dressing cycle.
By continuously dressing while the component is being ground, dressing-related cycle time is completely eliminated.
Automation in grinding
Automation also is having an impact on grinding and its associated downtime.
Some grinding machine manufacturers have started making grinders that are highly automated. These machines can run production with the help of robotics and are equipped with multiple automatic tool changers.
The operator changes the wheels on the different spindles in the tool changer and load spindle set ups for several different parts as the machine is running. When the part type changes or a different operation is required, the machine automatically changes to the proper wheel. There also are some grinders that adjust the coolant nozzles based on the programming for a particular wheel/work setup. It’s an industry trend that is seeing manufacturers acquire more of these types of machines to eliminate time wasted in setups.
There are also automated systems available that can detect part types and make subtle changes to a grinder, as long as the parts aren’t too different (as is the case with some automotive component manufacturers).
These manufacturers run a few different sizes or styles of parts on a single grinder. The parts are identified using RF or other identifiers, which are read by the grinder to identify the appropriate grind program for that particular part.
Load/unload automation is difficult to use, unless the part mix is comprised of similar parts. It is difficult for conveyor systems or material handling equipment to adapt or adjust to a diverse part mix.
Taqwa Gilani and David Goetz are application engineers with Norton | Saint-Gobain Abrasives, 1 New Bond St., Worcester, Mass. 01606, 254-918-2313, www.nortonabrasives.com.
About the Authors
subscribe now
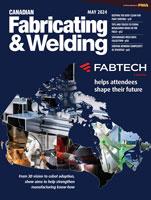
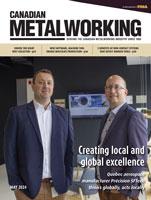
Keep up to date with the latest news, events, and technology for all things metal from our pair of monthly magazines written specifically for Canadian manufacturers!
Start Your Free Subscription- Industry Events
MME Saskatoon
- May 28, 2024
- Saskatoon, SK Canada
CME's Health & Safety Symposium for Manufacturers
- May 29, 2024
- Mississauga, ON Canada
DiPaolo Machine Tools Open House 2024
- June 4 - 5, 2024
- Mississauga, ON Canada
FABTECH Canada
- June 11 - 13, 2024
- Toronto, ON Canada
Zoller Open House & Technology Days 2024
- June 12 - 13, 2024
- Ann Arbor, MI