- FMA
- The Fabricator
- FABTECH
- Canadian Metalworking
The soaring highs and turbulent lows
A look at aerospace machining.
- By Nate Hendley
- February 2, 2015
- Article
- Metalworking
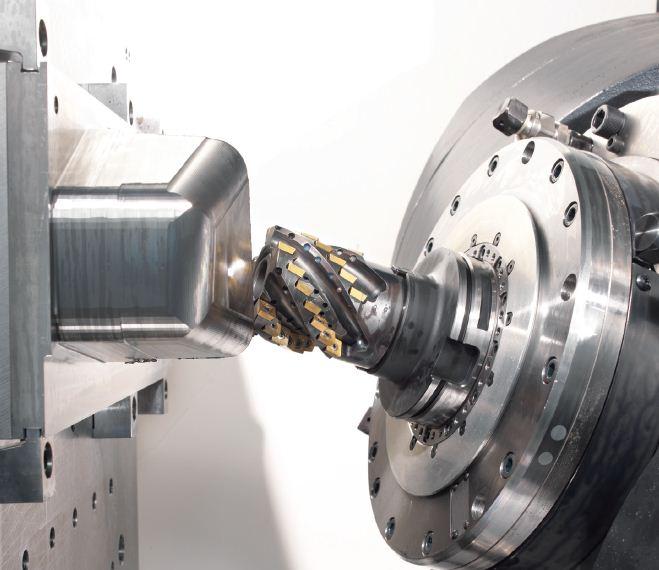
Makino’s new T2 5-axis horizonal machining center with ADVANTiGE, designed for mid-size titanium aerospace part production. PHOTO COURTESY OF MAKINO.
Aerospace OEMs such as Airbus, Boeing and Bombardier forecast enormous global demand for new planes over the next two decades. There is particular interest in airplanes that have lighter frames, more efficient engines and use less fuel. So, how will these developments impact aerospace machining?
We ran some questions by a group of experts to find out. Here’s what they had to say:
IS FIVE-AXIS ALWAYS THE BEST WAY TO GO WHEN DOING AEROSPACE MACHINING?
“There are large numbers of simple parts that go into an airplane and into other aerospace applications where a three-axis machine can more than adequately satisfy the requirement. That being said, a simpler machine limits manufacturers’ ability to do a variety of parts, of which some may need five-axis. A five-axis machine can do three-axis parts but unfortunately not the converse,” says Tom Dolan, vice-president sales and marketing at Mitsui Seiki in Franklin Lakes, New Jersey.
“If I was going to go into business on my own and start a company doing aerospace work, yes, I would absolutely have a five-axis machine. People say ‘five-axis’ and their mind goes immediately to very complicated contouring work…the majority of aerospace parts do have five-axis contouring work on them, but that’s usually the finishing operation…to get there, there’s a lot of three axis or three plus two axis work that are roughing operations only,” adds Wade Anderson, technical centers and product specialist manager, Okuma America Corporation, based in Charlotte, North Carolina.
“Really, the selection of machine is based on the parts to be produced. For many structural components, a three-axis solution is adequate. However, today parts are becoming increasingly complex and many times a five-axis solution is the only way to process the part efficiently and within tolerance,” echoes Ray Buxton, general manager at Mazak Corporation Canada, based in Cambridge, ON. “Five-axis machining can eliminate multiple set-ups for the machining of multi-sided parts, thereby improving efficiency and reducing cycle time. Five-axis machining can also improve quality since the part stays in the fixture from start to finish which eliminates alignment issues associated with multiple set-ups,” notes Adrien Roubenne, North American sales director for Fives Liné Machines Inc., in Granby, Quebec which in turn is part of Fives Machining Systems of Hebron, Kentucky.
ARE HIGH TOLERANCES ALWAYS A PREREQUISITE WHEN MACHINING AEROSPACE PARTS?
“No, absolutely not…there are many, many aircraft components that require extremely tight tolerances and there are many, many aircraft components that do not,” says Dolan.
“Aerospace parts in the manufacturing world are very diverse. You can have simple low tolerance brackets all the way to very high tolerance components for geared turbofans,” adds Buxton.
WHAT IMPACT WILL ADDITIVE MACHINING HAVE ON AEROSPACE MANUFACTURING?
“This will continue to grow and grow in new ways as technology changes. I believe one impact of any change in technology is it opens up new areas of business for companies and entrepreneurs alike,” says Anderson.
“At the JIMTOF [Japan International Machine Tool Fair] in Japan last year Mazak demonstrated our new i400AM combination additive/reductive machine. Mazak is working at the forefront of this emerging technology and we feel that it will eventually have a major impact on manufacturing not only in aerospace but also in automotive, oil and gas etc.,” says Buxton.
“Additive technologies will deeply change [the aerospace maintenance, repair, overhaul] sector in the next few years…replacing worn out parts with a new ones using additive technologies,” suggests Roubenne.
“At some point in time, will there no longer be a need for machining? Fortunately, for people of our industry, I don’t think that’s going to be the case in the short-term. But in the long-term, the honest answer is, ‘Who knows’?” says Dolan.
“If I was going to make a prediction, I would say the strengths and lightening characteristics of material is one area where I think additive manufacturing gives possibilities. I think [additive machining] will produce a lot more weight-effective components,” says Anderson.
SPEAKING OF WEIGHT-EFFECTIVE COMPONENTS, WHAT IMPACT WILL THE TREND TOWARDS LIGHTWEIGHTING HAVE ON AEROSPACE MACHINING?
“It’s not just aerospace, it’s automotive too. All the innovations that we’re seeing both in aerospace and automotive are driven by the demand for performance and fuel efficiency,” says Anderson.
“If you look at commercial airlines, the biggest single cost today is fuel. Fuel price is driving more efficient or effective aerodynamic shapes of aircraft, lighter weight and more efficient aircraft engine technology … lighter weight or more [efficient] engines that use less fuel [means] the ability to carry more passengers or more cargo. All that is driving new technology in materials, shapes and configurations and electronics,” says Dolan.
DO YOU SEE ANY OTHER TECHNICAL TRENDS FOR AEROSPACE MACHINING IN THE FUTURE?
“People have to start seriously embracing automation. Automation doesn’t necessarily mean robots and sophisticated flexible manufacturing systems. It means being able to automate a manufacturing process even for small lot manufacturing which is typically what the aerospace industry does. Looking at automating processes means taking the most advantage of the machine capability as possible, to reduce manufacturing costs and reduce the effective capital cost on the workpiece itself,” says Dolan. “The materials in aerospace are getting more and more exotic…there’s new material coming out all the time, different alloys, different mixes…newer, lighter weight, stronger, tougher materials. As materials get more exotic, they tend to get harder to machine,” says Anderson.
ONE OF THOSE “EXOTIC” MATERIALS IS TITANIUM. WHILE TITANIUM IS BECOMING INCREASINGLY POPULAR IN AEROSPACE MANUFACTURING, IT IS REGARDED AS SOMEWHAT DIFFICULT TO WORK WITH?
“Generally, titanium machining demands a very rigid machine with high torque and horsepower. Mazak designs all of our machines with a very high level of rigidity.
For most of our models we also have high torque spindles as an option that successfully address the needs of the more demanding user,” says Buxton.
“The majority of manufacturing is just now getting into titanium machining. We design our machines to be very rigid, with a lot of dampening and thermal ability characteristics,” echoes Anderson.
COMPOSITE MATERIAL IS ALSO BECOMING MORE COMMON IN AEROSPACE. DO YOU HAVE ANY TIPS ON MACHINING COMPOSITES?
“Optional high speed spindles are the necessity for this material along with special considerations for dust control,” says Buxton.
DO YOU THINK THE USE OF TITANIUM AND COMPOSITE MATERIAL IN AEROSPACE MANUFACTURING WILL INCREASE IN THE NEAR FUTURE?
“Not a whole lot more than what’s being required as a percentage of each aircraft going forward. However, the volume of these materials will definitely increase as more aircraft are [being built]. At any of the major aircraft OEMs, the projection numbers are quite significant. If you look at the components that are required on an airplane for both aero-structure and propulsion, the volume of titanium is definitely going up … if you consider that Boeing and Airbus are each moving towards 60 commercial aircraft a month, the volume and mix of products they expect to deliver to their customers, the requirement for titanium components is going to increase dramatically over the next couple years. The same applies to composites,” says Dolan.
DO YOU HAVE ANY ADVICE FOR AEROSPACE SUPPLIERS ON HOW TO GET MACHINING CONTRACTS FOR THE LIKES OF BOMBARDIER, PRATT & WHITNEY, BOEING, AIRBUS, ETC.?
“Smaller companies will require more multi-axis capability—five axis machining. Although they may still have a wide variety of simple parts to make, they will not want to refuse work for five-axis that comes as part of a complete package. So machine versatility will be an important change or shift [for smaller manufacturers] … the major aerospace contracts that are being awarded now are for longer-term projects. Therefore, the ability of smaller companies to understand differences in machine tools, differences in machining requirements, is going to be of paramount importance,” says Dolan.
“Be capable. Have the equipment and processes capable of delivering more than you can promise,” adds Anderson.
OKUMA’S AEROSPACE CENTER OF EXCELLENCE
Last fall, Okuma America Corporation opened the Okuma Aerospace Center of Excellence at its company headquarters in Charlotte, North Carolina. Aerospace manufacturers can use the facility to test machining technology and productivity solutions. “Our primary goal is to offer our aerospace customers what they often don’t have—time, equipment and resources,” explains Wade Anderson, technical centers and product specialist manager with Okuma.
Encompassing nearly 10,000 square feet, the Aerospace Center houses nine CNC machines. The space also features a metrology room and a conference room. Two Okuma application engineers (AEs) are posted full-time to the Center to assist with R&D.
According to Anderson, the Okuma Aerospace Center of Excellence is an ideal incubator for research. If projects fail, “it’s okay, because we’re doing it in a controlled environment, so to speak. Our machines are not for production. They are strictly here for R&D, to try new processes…in a facility like this, we can push the boundaries. We accept the fact there’s going to be some risk involved,” he states.
About the Author
subscribe now
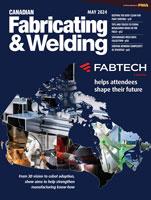
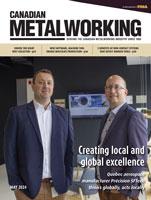
Keep up to date with the latest news, events, and technology for all things metal from our pair of monthly magazines written specifically for Canadian manufacturers!
Start Your Free Subscription- Industry Events
MME Saskatoon
- May 28, 2024
- Saskatoon, SK Canada
CME's Health & Safety Symposium for Manufacturers
- May 29, 2024
- Mississauga, ON Canada
DiPaolo Machine Tools Open House 2024
- June 4 - 5, 2024
- Mississauga, ON Canada
FABTECH Canada
- June 11 - 13, 2024
- Toronto, ON Canada
Zoller Open House & Technology Days 2024
- June 12 - 13, 2024
- Ann Arbor, MI