- FMA
- The Fabricator
- FABTECH
- Canadian Metalworking
Getting a fix on fixturing
Modular fixturing can add flexibility and process improvement to your welding operations
- June 13, 2011
- News Release
- Metalworking
Where does your company stand when it comes to producing quality weldments? The Wall Street Journal reported in 2006 that the average age of the North American welder was 54 years. When these people retire, they take with them years of experience in welding parts with simple hand tools, along with a wealth of technical knowledge and a great deal of process skill.
And though the faces doing the welding may change, the basic welding process does not. In an age where newer generations are more familiar with USB ports, joy sticks and computer-aided design (CAD) than they are with framing squares, chalk and tape measures, producing a quality weldment can still be a challenging task.
For this reason many companies still use “tack” tables (see Figure 1), a steel plate that has been ground flat that rests on its own legs or on saw horses. The locations for the stops are scribed on the surface and then the stops are tack welded. When the job is finished, the stops are broken free and the surface is cleaned with a hand grinder. After a period of time, the flat surface resembles the surface of the moon. If you were able to make a good part with this old technology, making an identical part at a later date would be extremely difficult and equally time consuming.
At the other end of the spectrum are dedicated fixtures. Properly conceived and constructed, repeatable quality is all but assured. However, at the prototype stage, dedicated fixtures can be a very expensive exercise. Imagine trying to make a fixture for a part whose design has not yet been finalized.
Along with that comes the challenge of guessing where and how far the part will move during the welding process. Any change to the part design usually requires a similar modification to the dedicated fixture, which can be expensive and time consuming. Furthermore, imagine investing in a dedicated fixture for a product that never gets beyond the prototype stage before the project is canceled!
As an alternative, consider modular fixturing for welding. A modular system includes all of the free-form flexibility of a “tack” table with all of the precision and repeatability of a dedicated fixture. The only difference is that when the job is done, all of the components can be disassembled and reused for the next job. Being modular makes it possible to use CAD to create (see Figure 2) and document the fixture. Out on the shop floor, the welder constructs the fixture according to the instructions prepared by engineering.
A typical system features a five-sided table with a regular pattern of bores located across the top and around the sides. Table sizes range from 1000 mm x 1000 mm (40 in x 40 in) to 2000 mm x 4000 mm (61/2 ft x 13 ft). These tables are hardened so that spatter will not stick to them. A wide variety of components assemble to the table to create a precise fixture. Where the part envelope exceeds the table surface, angles can be mounted to the sides to act as outriggers that extend the capacity.
This modular fixture (see Figure 3) serves as the first in-process quality check for all of the loose pieces. Before the first arc is struck, you will know whether the guy on the saw cut it correctly. Occasionally, when engineering oversights are uncovered, corrections can be made before things get out of hand. During welding, any changes in the fixture that are needed to compensate for weld pull can be made easily. When the part geometry is correct, data can be extracted from the modular fixture and given to a tool designer to have a dedicated fixture made with the exact same clamping locating points that made the good part.
For large parts, there are efficient and precise elements of the modular system that are more appropriate. For example, rails with the same pattern of bores as the tables are lagged to the floor, precisely spaced and leveled. A combination of tables with special spacer frames and narrower bridges with the same pattern of bores as the tables can be used to hold and locate the large parts (see Figure 4). The relationship of bores from one end to the other is assured by the precise bore locations in the rail surface. The same positioning and clamping bolts that hold together and locate the modular element of the system are also used to fasten the bridges and frames to the rails. This eliminates past worries about tape measure sag when measuring for a setup. By using two positioning and clamping bolts in the system bores, one universal stop and a spacer set incremented down to 0.5 mm (0.040 in) locators can be set precisely and repeatedly.
The term robot and the phrase “short run” are rarely used in the same sentence. Since robotic welding requires more precision and repeatability in fixturing than manual welding, fixtures are an absolute necessity. However, dedicated fixtures can often cost more than the robot itself. In applications where the parts are simple but the lot sizes are low, it is possible to physically build a fixture and then teach the robot how to weld that part.
When the welding program is approved by the setup technician, the remaining 99 pieces of a 100-piece lot can be run by the robot operator. The setup technician moves to the second station and repeats the same process sequence. All day long they trade places setting and welding. Modular fixturing makes all of this possible (see Figure 5). Where larger parts are being considered for robotic welding, gantry robots (see Figure 6) are one solution. The fixturing used in this case consists of a square spacer block with a full pattern of system bores on three sides and the two ends. Mounted between a headstock and a tailstock, the robot is able to access all sides of the part.
Fixturing elements are mounted to the sides of the spacer block using the outrigger approach discussed earlier. The mounting of the spacer block incorporates an adapter that allows the center of gravity to be adjusted to handle a number of part sizes and configurations.
Modular fixturing brings the accuracy, repeatable quality and the speed of the robot to a whole new range of part configurations. If any of these examples have encouraged you to look further, contact a modular fixturing supplier and challenge them to tackle your problems. Let them design a fixture for you to help you prepare your justification. If you want to see your part mounted and welded in a modular fixture before purchasing a system, challenge your supplier to do it for you in their validation center. If your budget is short but your need is urgent, ask if they have a rent-to-own or short-term rental program.
Before you make your commitment, make certain that the supplier has sufficient hardware in stock to support your project. And, because using modular fixturing for welding is a different way of doing business, be sure to include the right people in your plans to implement a system. Once you get started, you will wonder how you ever got along without
a system. CM
Robert Ellig is the president of Bluco Corporation, Aurora, IL.
subscribe now
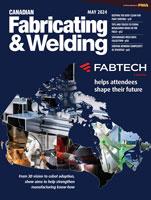
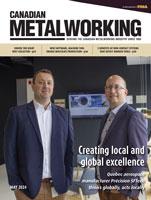
Keep up to date with the latest news, events, and technology for all things metal from our pair of monthly magazines written specifically for Canadian manufacturers!
Start Your Free Subscription- Trending Articles
Modest manufacturing growth appears likely
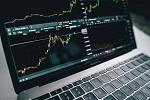
There’s no business like show business
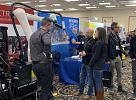
Tighitco, DCM Group Aerospace join forces on Airbus A220 program
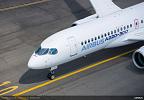
Software automatically identifies vulnerable production assets
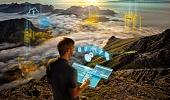
NAIT names Sandvik Coromant the 2024 Distinguished Industry Partner

- Industry Events
MME Saskatoon
- May 28, 2024
- Saskatoon, SK Canada
CME's Health & Safety Symposium for Manufacturers
- May 29, 2024
- Mississauga, ON Canada
DiPaolo Machine Tools Open House 2024
- June 4 - 5, 2024
- Mississauga, ON Canada
FABTECH Canada
- June 11 - 13, 2024
- Toronto, ON Canada
Zoller Open House & Technology Days 2024
- June 12 - 13, 2024
- Ann Arbor, MI