- FMA
- The Fabricator
- FABTECH
- Canadian Metalworking
Maximum turns
Experts weigh in on the best ways to handle today’s advanced turning machines to maximize process performance
- June 3, 2011
- News Release
- Metalworking
In 2000, Yamazaki Mazak Corp. introduced its “mother machine,” a futuristic machine tool it envisioned would be available in 2019 on the company’s 100th anniversary.
With a spindle speed of 100,000 rpm and spindle acceleration of eight gs, this machine of the future would have the ability to achieve cutting speeds approaching Mach 2. A magnetic rotary table with turning speeds of 8000 rpm would have the ability to index at 1/10,0008. It would be capable of simultaneous five axis control, turning, milling, ID and OD grinding, laser hardening and in-process measurement in a single setup.
“Our machines today are getting to look and function more and more like that every year,” says Rick Ware, vice president of sales and marketing for Mazak Corp., Florence, KY. (Mazak’s Canadian headquarters are in Cambridge, ON).
In fact, the company’s turning centres have advanced so much that Ware says they’re now defined as “machining centres with turning capabilities.”
Bob Allington, applications engineering for turning at Hardinge Inc., Elmira, NY, concurs with Ware. Hardinge’s top selling machines are the single turret, dual spindle turning centres—Allington estimates 30 to 40 per cent of Hardinge’s customers purchase this style of machine tool.
When you get into multi-spindle turning machines (or turning centres/machining centres, depending on a company’s definition and the number of functions on them), you introduce more complexity into the machining process. And when you’re machining complex parts, software and controls become an integral component of the machine tool.
“Many of today’s machines have built-in computers which allow the machines to go faster, be more flexible, safer and more reliable,” says Allington. “The computer allows the machine to run somewhat unattended, which allows the operator to multi-task, a key requirement of our customers.”
Dan Silberhorn, runoff engineer at MAG, says turning technologies have come a long way and lists today’s “state-of-the-art” changes.
“Four axis turning [main spindle with two turrets—upper and lower—with the ability to cut at the same time, reducing cutting operations], live tooling, right angle live tooling, tool probing, part probing, grinding capabilities and gear cutting.”
Not surprisingly, these advanced turning machines come with a higher price tag, so ensuring you’re optimizing machine performance is critical.
What’s the best way to do that? To some extent, this is dependent on the design and make of the machine because every builder has distinct features and functions built into their machines to help customers maximize machine performance. There are, however, some common tricks and tips customers can employ that suppliers shared with Canadian Metalworking.
Controlling the process
One of the best ways to optimize turning performance on your machines is automation, says Mazak’s Rick Ware.
“Simple automation is a big area where you can make a difference [and improve performance] on two and three axis machines. Take bar feeders as an example. You can incorporate automatic bar feeders that continually feed parts into the machine and you can cut ten pieces off of one bar and run it unattended. The next step in this type of simple automation that could help improve the performance of the turning process is pick and place robotic loaders. We have gantry loaders which pick up parts from a carousel of raw material and load them into the machine and then offload after machining. This gives you a lot of capability to increase parts per hour because you’ve introduced a level of automation into the turning process.”
Another area of automation that can improve machine tool performance is on-machine measurement of parts, says David Bozich, machine tool products business manager for Renishaw, Hoffman Estates, IL. In Canada, Renishaw (Canada) Ltd. is based in Mississauga, ON.
“Tough economic times force manufacturers to look for ways to improve efficiency while reducing costs. Automating process control, through on-machine probing, can be critical to reducing manning levels, machine downtime, scrap and rework, and even inspection costs.”
He says on-machine probing brings “predictable productivity” to turning operations.
“Much of the non-conformance in many processes arises from human intervention. Automation can make possible intelligent process control to minimize staffing levels, human error, cost burdens and the drags on machine utilization/equipment efficiency from manual intervention.”
MAG’s Dan Silberhorn says part probing can “drive up throughput and quality” because the process can “check for tool wear and measure the workpiece,” providing critical data that allows operators to monitor potential issues before they become a problem leading to tool breakage and machine tool shutdowns.
“A machine tool “crash” can be devastating to a production environment,” says Hardinge’s Bob Allington. “Many operators and programmers take it personally when a machine they run crashes. The good news is that 99 per cent of machine crashes can be avoided. The key here is to be alert and just pay attention to what is going on in your environment.”
To reduce such crashes, Allington suggests operators double check all tool offsets, make changes to the program and confirm the changes, use “set-up mode” and “distance to go,” which are control safety features, and set rapid traverse to low when in set-up. He also advises that operators use graphics to confirm accurate program codes before running the machine, “and always inspect and ensure the integrity of the part workholding fixture.”
Tooling
While not specifically part of the turning machine, tooling plays an important role in turning process optimization.
MAG’s Dan Silberhorn “tricks of successful turning” includes tooling advice: “keep your cutting tools sharp and as short as possible. Make sure the cutting tool is in line with the centre of the chuck. Also check cutting tool clearances, calculate the proper feed and speed for each tool and material being machined.”
Hardinge’s Bob Allington also points to cutting tools as being an important part of the machine tool optimization equation.
“While running any machine, eventually tools will wear and the parts being produced will be out of tolerance. The operator needs to monitor parts and adjust the tool based on blue print requirements. In some cases, if the tool wear gets excessive, the tool may physically break and the operation of the machine stops. The good news is that with a little care, the cutting tool issue is very manageable.”
A Common Sense Approach
The most important step you can take to optimize performance? Maintenance. It seems like an obvious statement to make, but experts say they can’t stress it enough because time and time again they see shops that neglect to do the checks and balances a preventive maintenance schedule entails and ultimately end up dealing with more tool wear, faster tool breakage and machine downtime.
Bob Allington says machine tool failure—due to lack of maintenance—is one of the top problems he sees while machines are in operation.
“Today’s machines are very reliable, but eventually hardware can wear and failure is inevitable. One key to minimize failure is to have some sort of preventive maintenance program. This could be as simple as the operator doing a walk around—looking for leakage of any sort or just listening for an unusual noise. The maintenance may be left to the person who cleans filters, adds oils and lubricants or applies grease to moving parts. Many machine tools actually alert or remind the operator/maintenance person to service the machine. Either way, simple preventive maintenance goes a long way.”
Machine tool builders have attempted to address the issue by developing software and control packages that make it easier to monitor turning processes.
Mazak’s Rick Ware says his company has developed numerous controls for its family of “machining centres with turning capabilities.”
“You can do a lot of monitoring with controls and customers are doing more maintenance monitoring on controls. There are up to 70 different tasks we can program into the machine control with the capability to monitor the machine via maintenance.”
A significant advancement in this area according to Ware is MT Connect. Mazak is on the board of the MT Connect Institute. MT Connect is a machine-to-machine communication software program that provides a common communication platform for different machines from different builders.
“We are providing the MT Connect capability in all of our machines. It’s an inexpensive option to have this connection capability between different machine tools in the shop and monitor processes. Once you have this in place it’s to the point where the machine can now tell you when it needs to be fixed. It’s sort’ve like the mother machine of the future that Mazak developed; that’s what’s happening with machine tools today.”
Asked what he thinks the top problems are with turning machines and how operators can address the issues, Richard Parenteau, director of applications development and Nakamura-Tome product manager at Methods Machine Tools Inc., Sudbury, MA, says “way lube contamination—using way lube that is not the proper grade or not clean, which means it’s usually not stored properly, like a drum left open—coolants with high levels of chlorine which will destroy most of the rubber products in the machine, and high pressure coolant with the use of a mist collector. The mist will soak through the machine guarding and cause corrosion.”
His advice to avoid these problems? “By simply using good maintenance practices. Store the way lube properly, check the coolant MSDA sheet for chlorine and use a mist collector for high pressure applications.”
Every machine shop wants to reduce costs. Optimizing your turning machines is the best way to achieve that. CM
To see product report click here.
subscribe now
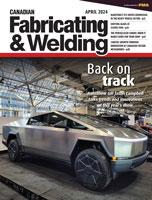
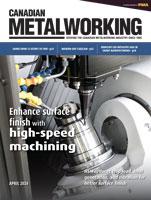
Keep up to date with the latest news, events, and technology for all things metal from our pair of monthly magazines written specifically for Canadian manufacturers!
Start Your Free Subscription- Trending Articles
Automating additive manufacturing
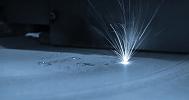
Sustainability Analyzer Tool helps users measure and reduce carbon footprint
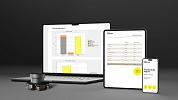
CTMA launches another round of Career-Ready program
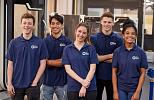
Sandvik Coromant hosts workforce development event empowering young women in manufacturing
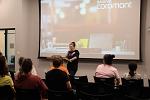
GF Machining Solutions names managing director and head of market region North and Central Americas
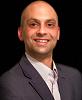
- Industry Events
MME Winnipeg
- April 30, 2024
- Winnipeg, ON Canada
CTMA Economic Uncertainty: Helping You Navigate Windsor Seminar
- April 30, 2024
- Windsor, ON Canada
CTMA Economic Uncertainty: Helping You Navigate Kitchener Seminar
- May 2, 2024
- Kitchener, ON Canada
Automate 2024
- May 6 - 9, 2024
- Chicago, IL
ANCA Open House
- May 7 - 8, 2024
- Wixom, MI