- FMA
- The Fabricator
- FABTECH
- Canadian Metalworking
Reimagining knee replacements with additive technology and AI
- August 13, 2020
- News Release
- Metalworking
Medical implant manufacturer Rejoint, Bologna, Italy, is introducing mass customization and therapy personalization through a combination of electron beam melting (EBM) and computerized analysis of intraoperative and post-operative data collection through IoT-connected wearables.
The market for knee implants is now estimated at around 5 million per year worldwide. The knee arthroplasty market until recently solely consisted of standard prosthetic systems, with a limited range of sizes available. Correct and precise sizing and positioning is one of the critical factors for the success of this type of intervention, which is now clinically routine but still variable in terms of success.
Knee joints have to withstand point loads that can reach levels of over 300 kg. Even minimal dimensional changes between the patient’s bone elements and an implant can cause pain and inflammation. For the patient, over- or undersizing means constant awareness of the presence of an artificial joint, as well as leading to muscle and ligament decay.
Additive Tech and Data-driven Customization
Rejoint, founded in 2015 by a team with many years of experience in the orthopaedic sector, recently entered the knee arthroplasty market. It aims to offer customized medical parts, and both additive manufacturing and AI are integral to its growth strategy.
“When it came to additive manufacturing, we were initially undecided about the most suitable solution for personalized cobalt-chrome prosthetics and were evaluating DMLM [direct metal] and EBM. Both modalities in fact offer a good level of resolution and quality, but we ultimately opted for the GE Additive Arcam EBM Q10plus system. The knowledge and industrialization support that GE was able to provide us and the professional experience of their local team here in Italy also informed our decision,” said Gian Guido Riva, CEO at Rejoint.
To produce the additively manufactured prosthesis, the company starts by 3D modelling the patient’s CT scan. AI algorithms are then used to analyze the images and identify the most suitable size for each specific case.
AI is used to compare the unique anatomy of a patient on several thousand prosthetic dimensions, each with as many dimensional variables in specific areas of the implant.
The surgeon is then offered the optimal configuration for positioning both the prosthetic components and for simulating the operation. This analysis forms the basis for the production of the prosthesis.
Rejoint is working with GE Additive to reduce powder-based production costs, focusing on the reduction of cycle times and the optimization of parameters -- including through the development of remote production control stations.
subscribe now
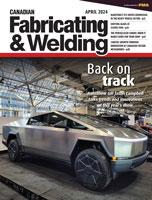
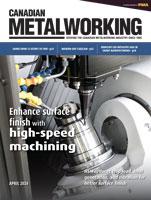
Keep up to date with the latest news, events, and technology for all things metal from our pair of monthly magazines written specifically for Canadian manufacturers!
Start Your Free Subscription- Trending Articles
Automating additive manufacturing
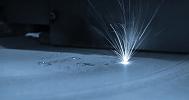
CTMA launches another round of Career-Ready program
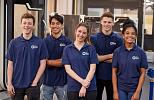
Collet chuck provides accuracy in small diameter cutting
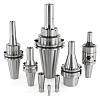
Sandvik Coromant hosts workforce development event empowering young women in manufacturing
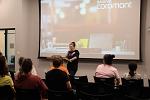
GF Machining Solutions names managing director and head of market region North and Central Americas
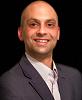
- Industry Events
MME Winnipeg
- April 30, 2024
- Winnipeg, ON Canada
CTMA Economic Uncertainty: Helping You Navigate Windsor Seminar
- April 30, 2024
- Windsor, ON Canada
CTMA Economic Uncertainty: Helping You Navigate Kitchener Seminar
- May 2, 2024
- Kitchener, ON Canada
Automate 2024
- May 6 - 9, 2024
- Chicago, IL
ANCA Open House
- May 7 - 8, 2024
- Wixom, MI