- FMA
- The Fabricator
- FABTECH
- Canadian Metalworking
World class fabricating: products
World class fabricating: products
- June 11, 2011
- Product Release
- Metalworking
Amada
With models varying in capacity from 55-600 tons, Amada’s new HD NT press brake series can handle a full range of applications in bend lengths from 79 to 276 in. (2000 to 7010 mm). This series features a Hybrid Drive system engineered for low energy consumption and requires less hydraulic fluid than conventional machines. In addition to being eco-friendly, the Hybrid Drive system maintains a high rate of repeatability (± .00004 in./0.001 mm).
Available on most models, Amada’s patented variable slit crowning feature ensures consistent angle accuracy. Larger models are equipped with an auto-crowning feature that provides precise results based on calculations created by the AMNC-PC control. Additional features of the new HD series include:
•High speed, high precision bending sensor that eliminates test bends.
•Increased distance between tooling and greater stroke length provides for a larger processing area.
•Expanded processing area enables deep box bending.
•Increased distance between punch and die allows for safe and easy processing of heavy materials.
To maintain bending accuracy while processing materials that vary in type, thickness and grain direction, the HD series is equipped with BI (Bend Indicator) sensors that utilize probe and laser technology. BI-S (probe type) or BI-L (laser type) result in trial-free bending. Bend angles are measured and adjusted on the fly to provide the correct angle on the first bend and to monitor and adjust angles throughout the run. BI technology boosts bending repeatability and reduces QA inspection and rework.
Fabricators processing thin sheets will benefit from the HD’s consistent accuracy and ease of use. The combination of an eco-friendly, Hybrid drive system and BI sensor technology ensures precision bending even if the operator lacks experience. Fabricators processing medium and thick sheets will profit from consistent angle accuracy, fewer trial bends, reduced material handling and the ability to perform deep box bending. Additionally, fabricators processing thick and large sheets will welcome safe and easy processing of heavy materials, easy to adjust angles plus simplified tool changes.
A wide variety of part geometries can be accurately processed thanks to a high precision (± .0004 in./0.010 mm) tapered backgauge. For precise bending control, the backgauge provides continuously updated feedback to the AMNC/PC NT-based control where exact positioning can be viewed at any time.
To provide maximum productivity, the HD’s intelligent control digitizes the bending process and delivers offline programming. Enhanced network functions within the AMNC control allow operators to call up complete sets of bending data from the server. In addition, the AMNC control can create 3D images from DXF, DWG and IGES files. Programming bending data using 3D images makes programming a more intuitive process. More importantly, 3D simulation enables the identification of problems before they can occur.
Bystronic
Bystronic’s enhanced version of the Xpert press brake incorporates a high speed ram positioning system and the new Fast Bend+ safety system for reduced bending cycle times. The high speed ram positioning system is capable of reducing bend cycle times by 15 to 35 per cent, approach speeds of up to 600 ipm and bending speeds up to 47 ipm without sacrificing accuracy. The company claims it is the only press brake on the market that introduces no angle errors itself with a ram positioning accuracy of .00015 in./0.0038 mm.
The Fast Bend + safety system allows the machine to draw extremely near the sheet at high speed, so that slow movement is only necessary during the actual bending process. This cuts the time required by approximately 20 per cent. Furthermore, the new safety system adapts itself automatically after each tool change and moves the machine to the correct tool height without any additional intervention. If a tool is not recognized by the system, the machine stops, making it nearly impossible to use an incorrect tool, which increases the safety even more.
Low energy consumption, less machine noise, and less heat characterize the Energy Saver. As soon as the upper beam has reached the top dead centre position after a bend, the main motor of the Xpert switches off automatically until the next bend process is started. This does not change the operational flow and the process speed remains as high as usual. However, it saves up to one third of the energy, produces less noise, and does not produce any excess heat.
The Bystronic Xpert adjusts ram position and crowning during the bending process in response to material properties. With the touch of a single button, the bending sequence and the positioning of the backstops are determined, the tool plan is created, and the process data is generated, all automatically.
Cincinnati
The MaxForm hydraulic press brake from Cincinnati Inc. combines state-of-the-art forming speeds and part processing productivity with “smart” controls that speed and simplify programming, setup and part handling. An industrial PC-based touchscreen control and Windows software eliminate two thirds of the programming steps with conventional CNC controls, while advanced hydraulics and control technologies deliver cycle-eating ram speeds—up to 700 ipm—for more strokes per hour and parts per shift.
The high speed precision forming machine is available in 90 to 350 ton models and lengths to 14 ft (4.3 m). Exceptional ±0.0002 in. (3 Sigma) repeatability delivers consistency for bending of complex parts without deviation, drift or error stacking. Cincinnati backs the MaxForm with industry-best five-year parts and one-year labour warranties.
Simulation software enables easy offline part programming, while advanced “see and do” 3D graphics and automatic processing intelligence compensate for varied operator experience levels. A Bend Simulation Module, standard on the machine, allows programs to be created quickly offline or at the machine and proved out step-by-step in realistic 3D views to avoid trial bending. Smart controls automatically calculate and apply adjustments for ram reversal position, bottom bending tonnage, gage allowances, and material springback.
The machine comes standard with bolt-on Cincinnati Quick Clamp ram nose designed for hardened, sectionalized American tooling. It maximizes ram protection by doubling load capacity from 15 to 30 tons psi.
The versatile press brake offers as options Wilson’s Power Express hydraulic clamping and a Euro-style Ram Nose for European punch holders.
Haco
The Euromaster CNC press brake line comes standard with an easy-to-use colour graphical 2D Fastbend control (also available with touchscreen). The Syncromaster line has recently been upgraded with a new Linux-based controller line. Both controls can work with the same offline software (available with network connection).
The Syncro system of both lines of machinery works with the highest accuracy. The backgauge fingers from both lines have been upgraded and are easier to use.
Each can be equipped with different type of tool holders: North American Wila Tools and European style of tooling. The controls can work with different safety systems as LaserSafe, Akas Fiesler, Light Curtains, and DSP Laser. Machine construction conforms with North American and European safety standards.
The Syncromaster machine can be equipped with three axis capability. The Euromaster machine can be easily equipped with a six axis backgauge system. It can also easily be upgraded with a robot system. The robot and press brake are controlled by the Graphic 3DFastbend control. It offers a unique approach to robotized bending: seamless fusion of hardware and software that results in fast and accurate production.
LVD
PPS Series of cost effective press brakes offer the precision and reliability of LVD bending technology in a value-minded package. Available in six models from 55 to 220 tons and bend lengths from 78 in. (2000 mm) to 157 in. (4000 mm), the PPS press brake is offered in CNC configurations and is equipped with an easy-to-use touch screen control.
The touch screen control employs the same reliable infrared screen technology used on several LVD products. The 10 in. screen features large buttons that can be seen from a distance and which can be operated using work gloves.
Software developed by LVD allows for fast and simple programming with minimal training thanks to a “spread sheet” program layout in which each row is a bend and each column is a parameter. The user friendly format eliminates the time consuming effort of moving back and forth from page to page when making and reviewing part programs.
The system is ideal for quick programming of all parts and is suitable for all levels of users. It provides a number of user friendly features, including:
• Unlimited tool library for use of any tool, any name and any quantity
• Automatic angle calculation eliminates the need to manually assess ram reversal position
• Automatic bend allowance calculation eliminates manual assessment of bend allowance or back gauge setback
Prima Power
Prima Power has introduced the EBe servo-electric bending machine designed for each customer’s production requirements to achieve maximum productivity and product quality. It offers complete automation of the bending process. The bending operation cycle is fully automated; from the loading of the flat parts to unloading of the components.
This EBe bending cell has a maximum bending length of 84.65 in. (2150 mm) and maximum opening height of 8 in. (200 mm). The system is operated by CNC control and exchanges information and synchronization with the PLC through digital communication. All machine main functions and all axes involved in the bending process are numerically controlled.
The new construction features actuation of the bending blade movements (vertical and horizontal) by servo NC axes instead of hydraulic cylinders. The upper tool movements are also made by another NC servo axis.
Prima Power EBe provides the high bending quality required in demanding applications such as component production for design products. This is achieved through precise control of bending axes, fast and smooth bending, open programmability, and the construction that is immune to variation in thermal conditions.
New Bending Principle: A fundamental characteristic of the EBe bending technology is the movement of the blades. For optimum product quality, a new bending principle has been applied for the EBe. With this new principle, when the “rolling mode” is used, there is a wider contact surface between the blade and the sheet but no relative friction. Part marking and tooling wear is minimized.
New Industrial Design: Prima Power EBe has also been designed for the modern manufacturing facility to meet the high ergonomic standards through integrated safety covers. The EBe featuring Prima Power’s E-technology offers:
• Reduced labour cost
• Reduced set-up time
• Increased speed/productivity
• Reduced tooling cost
• High component quality
• Off-line programming
• Programmable bending blade crowning
• Energy savings (-50 per cent compared to all hydraulic solutions)
• Low maintenance cost
• Reduced noise level
• Reduced vibrations
• No influence by thermal conditions
Safan
The E-Brake from Safan produces the pressing force with synchronized electric motors and transfers via belts and pulleys to the beam. This unique drive principle brings many advantages: No problems with hydraulic oil, low energy consumption as well as higher productivity.
Westway Machinery Ltd. is the exclusive Canadian distributor for Safan equipment.
When a product requires several bends it is common practice to operate the machine at its fastest beam speed. Between the bends, the component is turned and inserted as required for each fold. Most time is lost between the bends by handling, the change over time between fast and slow points of the beam and the back gauge positioning speed. With safety on the one hand and the well-known inertia of Hydraulic systems on the other hand being the major limiting factors. Safan’s solution is the E-Brake Mechatronic press brake.
The control of the electric motors in the machine are the basis of this innovative system. The principle of the system is a pulley-block, which pulls the Top beam of the press against the effect of laterally arranged return springs into the die and applies the pressing force evenly along the length of the machine. In 98 per cent of cases no crowning table is required.
When rolling the belt up the driving motor pulls the beam downward into the die. The return springs strained during the bending procedure return the beam to its initial position.
The E-Brake is available from 35 to 300 ton pressing force and lengths from 1250 to 4100 mm. The drive is provided by Lenze electric motors. The 4 m machine with 200 ton pressing force requires a total output of 22 kw. The force is distributed evenly over 36 roles attached to the upper beam.
Safan’s electronic control system ensures very short response and delay times resulting in bending speeds of up to 20 mm/sec. The high acceleration and other servo motor characteristics mean not only very fast approach speed but also a seamless change over to bending speed.
The absence of hydraulics means no seals, and no pressure valves, resulting in less downtime and lower maintenance costs. As well, the press brake uses less energy than hydraulic machines because the motors operate only when the beam is actually moving.
TRUMPF
TRUMPF’s TruBend Series 7000 precision press brake is a compact machine that offers a high quality, efficient solution for the production of small bent parts up to 40 in. (1,016 mm).
Typical applications include sheet metal parts used in the production of vending machines and electrical equipment as well as in the telecommunications and aerospace industries. Bending such parts with large, heavy press brakes is typically inefficient because of the space and energy requirements involved.
A feature of the TruBend Series 7000 includes the ability to increase its bending speed simply by making adjustments to the machine parts relevant to the bending process: the back gauge and the beam.
The back gauge is made with lightweight carbon fiber, and the surfaces on which the bent part contacts the fingers of the back gauge are made of hardened steel. These design features enable the TruBend Series 7000 to set new standards for achieving accurate results.
In addition, the torque motor, which drives the beam, can deliver power even at low speeds. It ensures rapid axis movements and is low maintenance, since it has no gears and, therefore, needs no gear oil.
The TruBend Series 7000 also features enhanced ergonomics. Optimum working conditions and user friendly operating elements are integrated into the machine design. The operator can control the machine while sitting down and work without becoming fatigued, which helps ensure the quantity and quality of the fabricated parts. Gas spring supported pedals allow the height and angle of the foot rests to be adjusted. The arm support is also adjustable in height, so that every operator can set up his or her workplace individually.
In addition, the monitor for the TASC 6000 control system of the TruBend Series 7000 can be adjusted electronically and set to the appropriate angle.
Optional TRUMPF LED lighting illuminates the area in front of and behind the beam, ensuring correct lighting conditions precisely at the bend, without heat radiation. A laser diode also projects the bend line onto the surface of the sheet metal, simplifying the accuracy of guiding the workpiece into the back gauge.
To read related article click here.
subscribe now
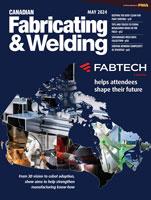
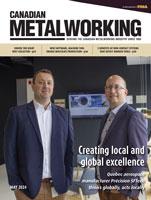
Keep up to date with the latest news, events, and technology for all things metal from our pair of monthly magazines written specifically for Canadian manufacturers!
Start Your Free Subscription- Trending Articles
Modest manufacturing growth appears likely
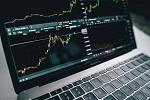
There’s no business like show business
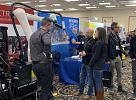
Tighitco, DCM Group Aerospace join forces on Airbus A220 program
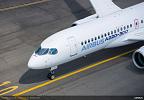
Software automatically identifies vulnerable production assets
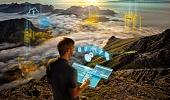
NAIT names Sandvik Coromant the 2024 Distinguished Industry Partner

- Industry Events
MME Saskatoon
- May 28, 2024
- Saskatoon, SK Canada
CME's Health & Safety Symposium for Manufacturers
- May 29, 2024
- Mississauga, ON Canada
DiPaolo Machine Tools Open House 2024
- June 4 - 5, 2024
- Mississauga, ON Canada
FABTECH Canada
- June 11 - 13, 2024
- Toronto, ON Canada
Zoller Open House & Technology Days 2024
- June 12 - 13, 2024
- Ann Arbor, MI