- FMA
- The Fabricator
- FABTECH
- Canadian Metalworking
New technology addresses insert wear resistance, toughness dilemma
A new methodology developed by Seco Tools, Fagersta, Sweden (secotools.com) addresses the long-standing dilemma of increasing both the wear resistance and toughness of a cutting insert at the same time.
- June 16, 2008
- News Release
- Cutting Tools
Achieving greater productivity and improving competitiveness is
important across all of manufacturing. Within the metalcutting
industry, research and development efforts continue to be focused on
developing increasingly productive technologies. Successes have come
over the years with frequent incremental increases in machine tool,
toolholding and cutting tool capability.
For example, advancements in machine tools have been noticeable and
numerous. Today’s equipment is capable of higher speeds, machining in
multiple axes, quick tool change, multi-spindle capability and much
more.
Toolholding, the critical connection between machine and tool, can be
accomplished using a number of methods and continues to improve,
providing accuracy and runnout in the tenths of thousandths. And,
cutting tools continue to evolve for all materials and intended
applications.
In the past, advancements in cutting tool technology have typically
been incremental. A new geometry, a new grade, a new coating on a
cutter body… all designed to improve quality, productivity or reduce
cost.
However, a recent introduction in the world of indexable carbide that
is much more than a slight improvement has been pioneered by Seco. The
tool is a coated cemented carbide grade developed for steel turning
that is providing results that are more revolutionary than evolutionary
for this significantly large and important market segment. However, the
real development was in the process used to develop the coating.
Metallurgists at Seco Tools have developed a methodology that
dramatically increases both the toughness and wear resistance of a
cutting insert-two features that have always been diametrically
opposed. In the past, in order to achieve improvement in one of these
properties you had to sacrifice at least some of the other. The ability
to increase both simultaneously virtually defied science.
Historically, aluminum oxide has been a consistent and proven coating
for steel turning applications. There are two different forms or phases
of aluminum oxide used for coatings: kappa and alpha. The difference
between the two forms is the crystal structure; the way the atoms are
arranged in the material.
When developing cutting tool (coating) materials, it is preferable to
use the alpha form of aluminum oxide for most applications. However, it
is much easier to deposit the kappa form. Consequently producers have
deposited the kappa form and then heat-treated it to transform it to
alpha. Unfortunately, this heating process results in a contraction in
volume, resulting in the formation of cracks in the coating.
There are a number of approaches to improving the performance of coated
products. Fine adjustments to the chemistry in the coating furnaces,
more careful structural control of the individual coating layers (as
there are numerous layers typically applied in both CVD and PVD
coatings), top and bottom grinding of the coated inserts and even
polishing the edges after coating. All are designed to provide
potential productivity and/or reliability gains to the end user.
For example, one reason that cutting tool manufacturers polish insert
edges on certain grades is to remove modest defects that naturally
occur during the coating process. This process is generally thought to
improve the smoothness and residual stress state of the cutting edge as
well as to reduce chip drag.
However, Seco’s new coating technology has made the polishing process
unnecessary. By carefully modifying the coating process, Seco has
learned how to control the crystal growth to improve both toughness and
wear resistance. This new methodology has been coined the Duratomic
process. This coating is more durable than other forms and provides the
user with a new level of toughness and wear resistance.
Essentially, this is a structural alteration of the aluminum-oxide
layer to create a coating that offers both long life and increased
cutting capability. Although these modifications are microscopic, the
results are impressive. Conventional aluminum oxide coatings have a
hardness of about 27.5 (GPa). Duratomic hardness is closer to
30.5(GPa), nearly an 11% increase. This translates directly to an
increase in abrasion resistance and, therefore, tool life. The coating
also runs cooler providing a full 35° centigrade reduction in a typical
application, enough to substantially reduce the tendency for the insert
to crater.
This article was supplied by Seco Tools, Fagersta, Sweden.secotools.com
subscribe now
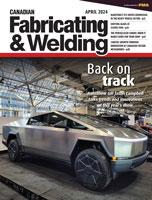
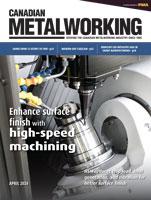
Keep up to date with the latest news, events, and technology for all things metal from our pair of monthly magazines written specifically for Canadian manufacturers!
Start Your Free Subscription- Trending Articles
Automating additive manufacturing
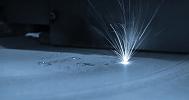
Identifying the hallmarks of a modern CNC
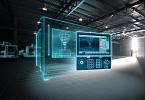
CTMA launches another round of Career-Ready program
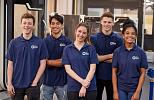
Collet chuck provides accuracy in small diameter cutting
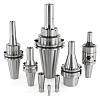
Sandvik Coromant hosts workforce development event empowering young women in manufacturing
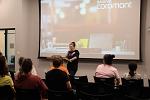
- Industry Events
MME Winnipeg
- April 30, 2024
- Winnipeg, ON Canada
CTMA Economic Uncertainty: Helping You Navigate Windsor Seminar
- April 30, 2024
- Windsor, ON Canada
CTMA Economic Uncertainty: Helping You Navigate Kitchener Seminar
- May 2, 2024
- Kitchener, ON Canada
Automate 2024
- May 6 - 9, 2024
- Chicago, IL
ANCA Open House
- May 7 - 8, 2024
- Wixom, MI