- FMA
- The Fabricator
- FABTECH
- Canadian Metalworking
The Cutting Tool Edge: Tapping Overview
Tapping Overview
- March 7, 2012
- News Release
- Cutting Tools
There have been a few big developments on the tapping front, with new taps designed specifically for the renewable energy sector, the return of a once discontinued tap and the launch of what’s being billed as the industry’s first general purpose, high-performance tap.
There is disagreement however, about the future of tapping, with some pundits predicting that thread milling will increasingly encroach on tap territory.
“I think for 80 percent of applications, thread milling is more advantageous than tapping,” says David Vetrecin, holemaking product manager for Iscar Tools, the Oakville, Ontario-based branch of an Israeli parent company.
Vetrecin does concede that, “in the deep, small diameter holes, it`s probably more advantageous to tap than thread because of the rigidity.”
The issue of rigidity, however, also triggers strong opinions.
“Rigidity is not as important for tapping applications as in other machining processes. A tap must be able to follow an existing hole and extremely rigid systems may put undue side pressures on the tap leading to failure,” says Alan Miller, engineering manager and product manager of tooling systems at Big Kaiser, headquartered in Hoffman Estates, Illinois.
While there’s a noticeable trend towards solid carbide taps, carbide too “has its limitations,” says Tom Guilfoyle, regional application specialist for Precision Dormer, in Crystal Lake, Illinois.
Among other things, “solid carbide taps are relatively expensive,” says Guilfoyle, who is based out of Detroit Michigan.
Faster tapping—something Canadian Metalworking has referred to as “the Holy Grail of machining”—is also on the radar
“The key to successful high-speed rigid tapping is reducing the forces applied to the tap. A compensating system will allow the tap to follow the existing drilled hole and not re-cut the thread on the way back out,” says Miller.
As for the future, most pundits play down the thread milling threat.
“Tapping will always be faster than thread milling and it’s user-friendly with respect to the operator of the machine,” says Frank Joswig, Guelph, Ontario-based district manager of tool giant Emuge’s Canadian operations.
“Thread milling will always take longer and there’s limitations on [penetration] ... the maximum depth practically with a thread mill is two times diameter of the thread ... with tapping, I can go three, four times depending on the material we’re cutting,” Joswig continues.
Here is what’s new and/or noteworthy in tapping:
Precision Dormer Attempts a Re-launch
Precision Dormer is re-releasing the Applix high performance tap line.
“The Applix tap was very popular years ago ... this is the re-launch of a product that had been discontinued ... a lot of people are excited that this tool is making a re-entry into the machining marketplace,” says Guilfoyle.
Among other details, the new version features some “improvements in coating” he adds.
In fact, taps in the Applix series (which are made from premium quality powered metal) boast an array of coatings: TiCN (Titanium Chromium Nitride) for low heat applications and TiALN (Titanium Aluminum Nitride) for abrasive materials or materials that generate heat.
“We also have a roll-form tap to roll the threads as opposed to cut the threads—and the coating we use there is Titanium Nitride (TiN),” says Guilfoyle.
There are several variations within the Applix family, including the Spiral Flute MXL line for blind hole operations and the Spiral Point MXP line for through hole operations. For anyone who wants to machine both through and blind holes and boost their productivity or speed, Precision Dormer offers the MXR line of threadforming taps. The HMD series, meanwhile, is recommended for machining hardened materials (up to 45 Rc).
“Historically people have bought one high performance tap for steel, another for stainless steel and another one for super alloy material ... this tool that we’re unveiling, will be able to do all those materials with one tap,” says Guilfoyle.
Asked if the Applix is suitable for small firms, he says, “You can use it in small shops. Of course, the people doing higher volume production are going to probably see [more] benefits, because the concept we sell is not really the price of the tap but how much mileage and how many parts you get out of the tap.”
Precision Dormer sells its taps to an array of industries, including medical, aerospace, oil, automotive and energy—“pretty much anybody drilling holes or threading holes, we’re in that industry,” says Guilfoyle.
http://www.precisiondormer.com/
Emuge – Two New Major Taps
Tool giant Emuge, the self-described “leader in tapping technology for more than 90 years” has two major offerings: the MultiTAP is the industry’s first general purpose, high-performance tap, says Emuge, while the Rekord DZBF series of taps tackles the pesky problem of ‘bird nesting’.
Based in West Boylston, Massachusetts, Emuge is a subsidiary of German company Emuge-Werk Richard Glimpel GmbH & Co. Emuge released the MultiTAP in 2010 and the Rekord DZBF Series last year.
MultiTAP is made from a “proprietary grade” of HSS-E high speed steel, says Joswig.
MultiTAP’s surface has been Nitrided with a Ne2 treatment and is designed to produce threads within both 2B and 3B classes of fit. The tap is geared towards job shops and manufacturers who do short and medium-run threading applications. MultiTAP will improve thread quality, boost output and reduce production costs as it eliminates the need to stock up on different taps in the tool crib, promises Emuge.
Asked if MultiTAP can handle long-chip materials such as carbon steel and or alloy steel, Joswig says “absolutely.”
“We have two designs—a spiral flute for blind holes and a spiral point for through holes. It’s designed for long-chip materials, short-chip materials, cast-iron, ductile-iron, cast aluminum, etc,” says Joswig.
The MultiTAP can also cut stainless steel, copper, brass and bronze, among other materials. The tap is not so good on heat resistant materials such as Titanium and Inconel.
The Rekord DZBF Series, meanwhile, is made from premium cobalt high-speed steel. The tap surface is treated with Titanium Nitride (TiN) for improved thread finishes and increased tool life. The Rekord DZBF Series utilizes CBTZ (Chip Breaking Tapping Technology) developed by Emuge.
“CBTZ technology features a newly developed cutting face geometry and spiral flute form, which combine to optimize chip flow, curl and length ... this innovative technology produces short, broken, controllable chip formations that eliminate flute clogging and potential failure of the machine tap due to chipped cutting teeth or breakage,” explains the company.
CBTZ technology offers improved tool life, increased operator safety, better surface finish and “eliminates the problem of ‘bird nesting’— when the chips wrap around the tap shank,” says Joswig.
Also called ‘chip nesting’, this phenomenon often occurs when tapping carbon steels, alloy steels and austenitic stainless steels.
The Rekord DZBF Series taps can be used in both horizontal and vertical machining applications and is ideal for machining in the energy sector, says Emuge.
Big Kaiser’s Mega Synchro Tapping Holder
Big Kaiser Precision Tooling released the appropriately named Mega Synchro Tapping Holder in 2010.
“The system was designed from the ground up specifically for rigid tapping. The system uses a steel taper adapter, an integral tap collet with various lengths and is held together with a screw that uses a special polymer bushing as a cushion,” says Miller.
Big Kaiser says the Mega Synchro Tapping Holder can compensate for synchronization errors during rigid tapping with any tap.
“The polymer bushing allows just enough give to compensate for the stack up of synchronization errors (machine feed, spindle rotation and tap pitch),” explains Miller.
By reducing thrust loads caused by synchronization errors up to 90 percent, Mega Synchro improves thread quality and boosts tool life.
Big Kaiser will be introducing a smaller Mega Synchro system at the upcoming International Manufacturing Technology Show (IMTS) scheduled this September in Chicago, says Miller.
Komet – Morex line
Komet presents the Morex-R roll form tap series with a flexible HSS-E shank and replaceable carbide inserts.
“The body of the tool is HSS-E but we have carbide strips inside ... this gives the flexibility of the HSS-E shank but the hardness of the solid carbide ... you are getting more tool life out of it because of the flexibility,” says Wolfgang Ruff, vice-president of Engineering at Komet.
Based in Schaumburg, Illinois, Komet of America is a subsidiary of the Komet Group from Germany, a global leader in metal cutting tools.
According to Komet, the combination of a flexible HSS-E shank and hard-thread profile allows the Morex-R to outmatch conventional carbide roll form taps, particularly when it comes to steel materials. The flexible HSS-E shank compensates for small alignment errors while the carbide and hard forming edges are designed to offer maximum tool life. The tip of the Morex-R can be refurbished up to three times.
“Customers send us their tool back and we can re-tip it ... we take the carbide plate out, put a new carbide plate in,” says Ruff.
The Morex-R can reduce tool costs by 20 – 40 percent, depending on tool dimensions and applications, promises Komet. These roll form taps are available with either a central internal coolant supply for machining blind hole threads or a side coolant outlet for use with through threads and blind hole threads.
Komet also sells the Morex-S roll form tap which is made from solid carbide with a TiN coating and inner cooling lubricant supply. The Morex-S can be used in applications, particularly in small dimensions, where previously it wasn’t feasible to use solid carbide taps. Long tool life and short cycle times due to high cutting speed are also prominent features.
Kennametal – Gone With the Wind?
Kennametal of Latrobe, Pennsylvania, is jumping onto the renewable energy bandwagon with its new high-performance, large-size HSS-E-PM “Wind Energy Taps”.
Said taps acquired their unique name because they’re designed specifically for machining important wind turbine components such as hubs, rings and gearbox housings. The Wind Energy Taps are intended to be used with conventional, non-rigid and CNC-synchronous tapping machines. The taps come in different styles, for use in through hole tapping and blind hole tapping and will boost productivity, says Kennametal.
“The precision h6 shanks of these taps enable their use in either conventional tap holders with square drive or in precision round tool holders,” adds Kennametal corporate material.
subscribe now
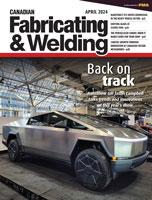
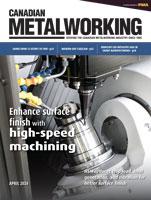
Keep up to date with the latest news, events, and technology for all things metal from our pair of monthly magazines written specifically for Canadian manufacturers!
Start Your Free Subscription- Trending Articles
Automating additive manufacturing
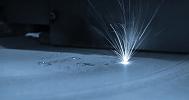
Identifying the hallmarks of a modern CNC
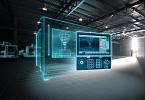
CTMA launches another round of Career-Ready program
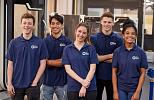
Collet chuck provides accuracy in small diameter cutting
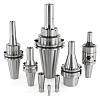
Sandvik Coromant hosts workforce development event empowering young women in manufacturing
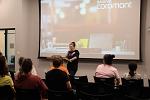
- Industry Events
MME Winnipeg
- April 30, 2024
- Winnipeg, ON Canada
CTMA Economic Uncertainty: Helping You Navigate Windsor Seminar
- April 30, 2024
- Windsor, ON Canada
CTMA Economic Uncertainty: Helping You Navigate Kitchener Seminar
- May 2, 2024
- Kitchener, ON Canada
Automate 2024
- May 6 - 9, 2024
- Chicago, IL
ANCA Open House
- May 7 - 8, 2024
- Wixom, MI