- FMA
- The Fabricator
- FABTECH
- Canadian Metalworking
Bend It Like Bernard
Quebec fabrication company thrives thanks to investment in technology, implementation of lean principles
- By Joe Thompson
- December 20, 2012
- Article
- Fabricating
When the owners of Metal Bernard, Saint-Lambert-de-Lauzon, Que., a fabrication job shop with the ability to laser-cut, bend, punch, roll, weld, and machine many types of metal, decided it was time to add capacity to their shop floor, they did so in a very big way.
This past October during an open house event to showcase its newest equipment and capabilities, more than 200 guests visited the plant, guided by the company's team leaders and members of the management team. These visitors were shown how incoming work is now divided into dynamic workcells, and also how a newly adopted daily management system quickly identifies any problem so the root cause may be identified and the problem eliminated before creating downtime or costing money.
This was, in part, the result of a reorganization of the plant's layout, during which time most machines were moved and placed into these workcells. This reorganization was made necessary because of the addition of a new 8- by 26-ft. Bystronic laser cutter; a 20-ft., four-roll DAVI plate roller; and a 1,500-ton, 30-ft. Cincinnati CNC press brake, which the company is touting as the largest in the country.
A 12,000-sq.-ft. addition to the facility was needed to house this new equipment, bringing the company's total footprint to 62,000 sq. ft.
Mario Ferland, Éric Chrétien, and Louis Veilleux—who purchased the company eight years ago from founder Bernard Cartegnie—invested heavily to make these upgrades—a total of $5.5 million.
"This was an act of faith in our team and our customers, who are among the best in Quebec, to take us through this difficult economic period. We follow the latest economic numbers, and see the world economy slowing, and with it, manufacturing jobs disappearing, but we believe there is always a place for the strongest in any market," said Ferland, the company's executive vice president.
Over the course of the last eight years, the company's staff has doubled in size, and it has added two laser cutters and five press brakes, including these recent additions.
It is, however, the company's newest press brake that is garnering a lot of attention.
The eight-axis, digitally controlled press brake was added to the existing 10 press brakes in operation at the plant to create more business opportunities. The company now can bend 30-ft.-long metal parts up 1 in. thick.
The company's laser cutters and most of its press brakes are kept busy on three shifts. The new, large press brake is currently being run on two shifts.
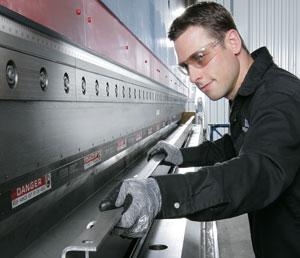
The eight-axis, digitally controlled press brake was added to the existing 10 press brakes in operation at the plant to create more business opportunities. The company now can bend 30-ft.-long metal parts up 1 in. thick.
While the company works mainly with steel, aluminum, and stainless, creating parts for the transportation, mining, and energy industries, it continues to seek new clients outside the province and the country, and it is always on the lookout for further investment opportunities that will enable it to remain a leader in the market and reinforce its position as a global outsourcing shop.
"Our orders have more than tripled, and our turnaround has melted to a day on most orders," explained Veilleux, who acts as the company's CEO. "Keeping our delays to a minimum has proved to be a major factor in increasing our business, even in these hard times. But the key factor has been the ability of all team members to work as a team to achieve customer satisfaction."
Changing With the Times
The changing face of manufacturing is evident on the floor of Metal Bernard. The company has thrived with the introduction of CNC manufacturing to the shop, and it has embraced the best practices of the industry through manufacturing resource planning (MRP), offline programming, and by implementing an andon-style manufacturing notification system.
The Metal Bernard team has been sharing their regional leadership in lean manufacturing processes by organizing shop visits to demonstrate their processes and customer-oriented operations. During the past two years, approximately 800 separate improvements have been made to the manufacturing processes at the shop to align the company more closely with the tenets of lean manufacturing.
"We no longer see ourselves as managers, but rather coaches," explained Operations Manager René Tremblay. "We inverted the management pyramid such that we now support all the team members and they, in turn, are at the service of our clients."
Individual team members are now empowered with greater decision-making authority and freedom to act on their own initiatives.
"The manager becomes a facilitator, spearheading a team effort, and the overall organizational performance becomes faster, more adaptable, and more effective," said Tremblay.
Even with the new capacity and floor space, challenges still exist for a modern Canadian fabrication shop, said Veilleux.
In Canada, especially in Quebec, it is the exodus of OEM companies to other countries, the high value of the Canadian dollar, and the challenge of finding people willing to work in manufacturing that are the most daunting.
"To make matters worse, we have recently had a change of government, which scared most businesspeople. Even if it was for a very short time, it did not help," said Veilleux. "Some see those as a catastrophe; we see it as a challenge."
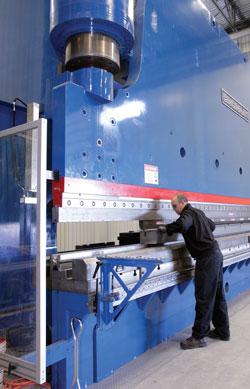
A 12,000-sq.-ft. addition to the facility was needed to house the company’s new equipment, which includes this 30-ft., 1,500-ton press brake.
Metal Bernard is a division of the Mundial Group, which has four other plants that process sheet metal, perform custom and high-volume machining, do silicone molding, and fabricate rubber parts and devices.
subscribe now
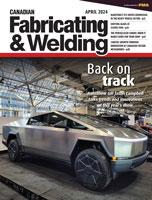
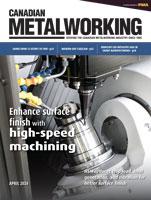
Keep up to date with the latest news, events, and technology for all things metal from our pair of monthly magazines written specifically for Canadian manufacturers!
Start Your Free Subscription- Trending Articles
- Industry Events
MME Winnipeg
- April 30, 2024
- Winnipeg, ON Canada
CTMA Economic Uncertainty: Helping You Navigate Windsor Seminar
- April 30, 2024
- Windsor, ON Canada
CTMA Economic Uncertainty: Helping You Navigate Kitchener Seminar
- May 2, 2024
- Kitchener, ON Canada
Automate 2024
- May 6 - 9, 2024
- Chicago, IL
ANCA Open House
- May 7 - 8, 2024
- Wixom, MI