- FMA
- The Fabricator
- FABTECH
- Canadian Metalworking
Easy Does It
Press brake controls and software smooth out wrinkles for new operators
- By Sue Roberts
- September 18, 2013
- Article
- Fabricating
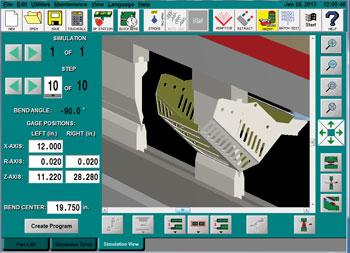
3-D simulation shows the steps involved in the bending process before production starts. Photo courtesy of Cincinnati Incorporated.
Historically, press brake operators have been handed a setup sheet with a lot of numbers identifying everything from materials and quantities to part numbers. Usually the skilled press brake operator would have to figure out the tooling. Three things were needed to convert those numbers into completed parts: a solid understanding of the machine and tooling functionality; a base of experience to understand how the machine, tooling, and material interact; and time to set up and test the run.
Over the past few years those requirements have changed due to the ever-present need to increase productivity coupled with a growing shortage of knowledgeable, experienced operators. The human-machine interface (HMI) has evolved, making interactions among the operator, the control, the programming, the tooling, and the machine easier and substantially reducing setup time.
Experience gleaned from seasoned operators has joined technical advances embedded in sophisticated software and displayed on user-friendly controls to ease operators through tool selection, placement, and part orientation. The human aspect of HMI today requires less operator training and less time to go from print to production.
Three-dimensional simulations and drawings to efficiently guide operators from bend to bend are replacing blueprints on the shop floor. Keyboards at the control are taking a back seat to screens that translate a simple human touch into part programs and press brake movements. Controls themselves have progressed from working only from their own files to reading floppy disks to accessing and sharing programs created offline via Ethernet or downloaded from a USB flash drive. All move toward keeping the operator engaged in actual production.
“A customer of ours has 21 of our newest-generation press brakes running three shifts a day,” said Casey Schlachter, press brake national sales manager for MC Machinery Systems, Wood Dale, Ill. “They put the money into the machinery, but they have a shortage of good operators. The operators were programming their own parts at the machines, each wasting valuable time that could be spent on production. Time was wasted on training, retraining, and setup.”
An Easy Touch
Some new controls and software allow programming at the brake as well as offline.
Cincinnati’s control is one example. A job setup page with part drawing capabilities and 3-D part views graphically steps the operator through creating a program using a variety of built-in parameters.
Matt Garbarino, marketing manager at Cincinnati Incorporated, Harrison, Ohio, said, “Whether it begins with a CAD file that has only the part geometry or a complete solid model, programming at the control using the touchscreen is graphically intuitive. The software takes the operator through the steps needed to incorporate the bend angles, flange dimensions, materials, and thicknesses, all information needed for the program. An experienced operator has the option of bypassing some of the automated features such as tooling selection in favor of entering his own choices.”
With MC Machinery’s 3-D bend and simulation software all programming can be done offline. It includes automatic tooling assignments based on either the 2-D or 3-D model to generate a collision-free bend sequence. Its bend simulator provides the programmer with a configurable simulation of the entire process and displays any collision points between parts, tools, punch holder, and machine so corrections can be made before the program reaches the shop floor.
Offline Has Advantages
Creating a program somewhere other than at the control is quickly becoming commonplace. It removes programming tasks from the operator and gives that time to production, saves setup time, and helps bring an inexperienced operator up-to-speed quickly by graphically showing how to produce the part. A company may have a server where information for a brake is kept offline, kind of a hub, and the operator can access the programs through Ethernet or by using a USB stick.
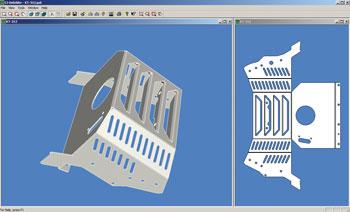
Working from a CAD/CAM file, software will provide the operator with a 3-D image of the completed part along with the flat image. Photo courtesy of Cincinnati Incorporated.
Once a program is loaded, the operator has immediate access to all the information needed to produce the part. The program has been proven and optimized in the virtual world so, in theory, there should be no reason to change it.
“With offline programming a design engineer in an office can use an existing CAD/CAM system to design in 2-D or 3-D, push some keys, and a program with 3-D graphics and movie simulations will appear at the press brake. An operator with limited skill can walk up to the control, open the program that’s waiting for him, and watch a 30-second movie on how to form the part. He can stop the movie, slow it, zoom, rotate the view, or do whatever he has to do until he is comfortable. Then he can push a button and get a series of 3-D still images that tell him step-by-step how to set up; how to flip, rotate, and turn the material through the bends; all of the gauge moves; everything needed, all in high-resolution graphics,” Schlachter said. “The operator can watch the video, look at the 3-D images, analyze it, and run with it. It answers all the questions and takes the operator’s nonproductive time away from the floor.”
How do seasoned operators react? Garbarino said that more times than not he has seen them opt for the setup speed, efficiency, and accuracy of offline programming when given the option.
Housing program files in an offline location also offers the flexibility of moving production from one brake to another, compatible brake and makes file management easier than having islands of programs scattered across a number of pieces of equipment.
Retrofits Increase Productivity
“We have machines in the field that may be 20 years old but from the features standpoint are still very accurate. They have good repeatability and functionality, but today’s control is leaps and bounds different,” said Garbarino. “If a model is eligible for an upgrade, it can be almost like getting a new press for the cost of the control and software upgrade.”
Some customers purchasing new machines bring their older models up-to-date with new controls so the brakes can share programs. This also allows anyone trained on the new equipment to work on the older machines without additional training.
“Customers tell me that once their press brake operators retire, it is very difficult to replace and educate new people. In the old days you’d hire a craftsman who knew what to do. Knowledge was gained by trial and error,” said Nigel King, product manager at Cincinnati distributor Elliott-Matsuura Canada Inc., Oakville, Ont. “The new controls and software eliminate the need for that kind of experience, so an inexperienced operator will have better success and an easier time bending parts and reducing scrap than just a few years ago.”
Can It Get Easier?
“There is so much functionality in the new control that often times people don’t know how to get the full benefit. Nobody can walk away from training remembering 100 percent. We are trying to fill that gap,” Garbarino said. “We are working on producing one- to two-minute how-to videos to be available on the machine control via the Internet. They will show how to do things like adding a tool to the library and importing a CAD file—little procedures that might not have been picked up in training.”
Schlachter said MC Machinery Systems is focusing on enhancing the 3-D environment software so it is easier for the programmer and making the brakes more economical for operation: “Make it simple so an operator can just walk up to the machine and make good parts.”
subscribe now
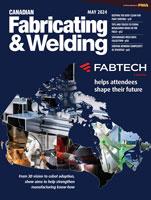
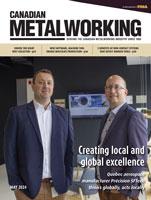
Keep up to date with the latest news, events, and technology for all things metal from our pair of monthly magazines written specifically for Canadian manufacturers!
Start Your Free Subscription- Trending Articles
- Industry Events
Automate 2024
- May 6 - 9, 2024
- Chicago, IL
ANCA Open House
- May 7 - 8, 2024
- Wixom, MI
17th annual Joint Open House
- May 8 - 9, 2024
- Oakville and Mississauga, ON Canada
MME Saskatoon
- May 28, 2024
- Saskatoon, SK Canada
CME's Health & Safety Symposium for Manufacturers
- May 29, 2024
- Mississauga, ON Canada