- FMA
- The Fabricator
- FABTECH
- Canadian Metalworking
Excitation Isn't Just for Photons
Job shops are getting excited about solid-state laser technology
- By Sue Roberts
- August 22, 2013
- Article
- Fabricating
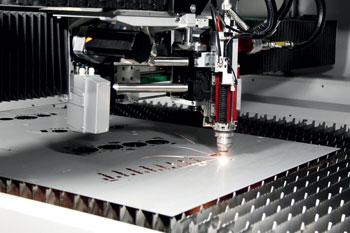
Solid-state laser technology, with its flexibility and speed, is working its way onto job shop floors. Photo courtesy of Salvagnini.
About a decade ago solid-state fiber lasers began zipping through thin metal primarily on OEM shop floors. Since then equipment manufacturers have challenged the initial material thickness limitations and are engineering ways to expand capabilities. Add the broader material cutting capability to the speed, ease of operation, low maintenance, low operating costs, and ability to cut exotic and coated materials, and fiber lasers are making their way into job shops producing low numbers of parts from a high mix of materials.
Although beam generation varies depending on the laser type, a laser is a laser, according to Tracey Ryba, laser product manager for TRUMPF’s Laser Technology Center in Plymouth, Mich. “You have four basic components: a pump source, an active medium, a rear optic, and an output coupler. The main difference with solid-state laser technology is that all four basic components are fused together unlike in CO2 lasers. They are 1-micron-wavelength lasers that allow you to plug in a delivery fiber and route through your system, delivering laser power to the workpiece much like a garden hose delivers water where needed. This eliminates the need for beam delivery optics.”
Low-wattage laser diodes excite an ytterbium-doped glass fiber to generate the beam. “Within that active fiber is a small optic fiber, in the vicinity of 20 microns, and the rare-earth element ytterbium,” said Jason Hillenbrand, laser product manager for Amada America, Buena Park, Calif. “When the concentrated power from the laser diodes interacts with the ytterbium that is doped into the smaller fiber-optic cable, it generates photons of light in a similar fashion as to what happens in a CO2 laser.”
Pierandrea Bello, project manager for Salvagnini America, Italy, explained. “According to the power of the source, there can be several laser diode modules, each with an active doped fiber. Power from each module is routed into a combiner to achieve the power output. From the combiner you have an external fiber to bring the beam to the work area.”
Confined in the fiber, the 1.07- to 1.08-micron beam is precisely guided and can be focused on a very small spot. The density of power concentrated in the thin beam cuts different thicknesses of material without the need to change cutting lenses. Comparing a 4-kW CO2 to a 4-kW solid-state, cutting speed of the solid -state laser can be two to five times that of the CO2 laser for materials up to about ¼ in. From 30 to 50 percent of the solid-state incoming power is converted to cutting power, compared to about 10 percent from a CO2, which is good for power consumption. Since less power is converted to heat, cooling is more efficient.
Through Thin and Thick
“A solid-state laser beam is perfect,” said Hillenbrand. “It’s a TEM00, transfer electromagnetic mode, which is a perfect Gaussian-shaped bell curve. That means that all the power is concentrated in one point or area. When this power is focused through a cutting lens, the wattage per square inch is extremely high because the kerf or cut width is extremely small.
“When cutting thicker material, the TEM00 in a fiber or solid-state laser doesn’t open the kerf very much, so assist gas has difficulty entering the cut. There are more pockets of heat and, generally speaking, more striations on the edge of thick materials. But with cut quality being subjective, the somewhat rougher edge finish may not create a problem,” Hillenbrand said.
It gets down to absorption. “The 1-micron wavelength absorbs faster. This means you can’t cut the thick material as fast. The energy is absorbed before it gets through thick plates when cutting at the faster speeds, and less energy is left to finish the cut,” said Ryba. “So the proc-ess needs to be slowed to allow the energy to move through thicker material.”
Brett Thompson, sales engineer, TRUMPF laser product group in Farmington, Conn., further explained. “The better absorption of the 1-micron beam in some materials is highlighted in the thinner range. In the thicker range, a cutting speed reduction that is very linear to the thickness of the material is seen. We find that at around ¼ in. the speed and cut-quality advantage diminish. In material over ¼ in., the edge won’t be quite as pristine as with a CO2, although with various TRUMPF proc-essing functions, quality in oxygen is comparable, up to around 5⁄8 in.”
Bello said, “We have worked to cut thicker materials in two ways. One is by increasing power. We started with 2-kW fiber lasers in 2008 and were up to 4 kW by 2012. The other is by developing our own cutting head to have better quality using the fiber.”
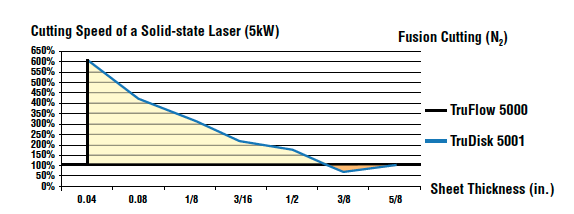
Solid-state lasers can drastically increase cutting speeds in thin-gauge material using nitrogen as an assist gas. As material thickness increases, speed advantage decreases. Above, cutting speeds of TRUMPF’s TruDisk® solid-state laser are compared with its TruFlow® CO2 laser. Graph courtesy of TRUMPF
Nitrogen as an assist gas provides the fastest cutting speeds and eliminates buildup of oxide along the cut edge that occurs when using oxygen.
Hillenbrand said, “When we look at a 4,000-watt fiber laser and a CO2 both cutting with oxygen assist gas, the speeds are almost identical up to about ¼ in. When we put nitrogen on both, the fiber optic will cut four or five times faster in thin material than the CO2.
“When you get to about ¼ in., you can no longer cut with nitrogen because the material is getting too thick. There might be a little dross or a burr occurring. Using oxygen on a CO2 and the wider beam kerf that occurs with CO2 technology allow more gas to enter the cut, creating higher cutting speeds than the fiber.”
Easy Flexibility
There is very little maintenance to a solid-state laser because the engine or generator does not include any moving parts or mirrors. The beam path is also simplified because the laser beam is delivered via fiber-optic cable. A few optics can be included in the cutting head, but due to the simple design and the fact that the distance of the optics from each other is fixed, there are no beam alignments or focus adjustments to interfere with consistent operation or for the operator to deal with when changing materials. The reduction in machine variables makes it easy to switch from one thickness or material type to another.
“Our equipment is field-repairable, but repairs are rare,” said Ryba. Everything is sealed, and expected lifetime is comparable with competitive systems. That extends to our disk technology that is about the same as the fiber technology, except that our diodes reflect the energy onto a disk before it goes to the fiber. This creates an insensitivity to back reflection, which is very important when cutting copper, brass, or aluminum. And with the disk laser, it is not possible to damage the laser due to a back reflection.”
“Most machines today have automatic nozzle exchangers and will know to change nozzles when materials are switched or to clean the nozzle if it is having problems cutting the material. The laser will try to fix itself. If there is a loss of cut or a problem it cannot fix, it will stop and send out an alarm. The fiber-optic machines are so fast you have to automate these processes to get the maximum green-light time,” said Hillenbrand.
Justifying the Cost
A solid-state laser can have a higher price tag than a CO2 partly because a full enclosure is needed to ensure safety. High-end fiber lasers with linear drives are available to take full advantage of positioning for the cutting speeds, as well as low-end solid-state lasers that rely on more mechanical drive systems like rack and pinion and ball screws.
“These machines are higher-cost than CO2 lasers,” said Thompson, “but unless it is a very clear CO2 application, our customers frequently lean toward a solid-state laser because the overall cost to produce parts is less, and it is easier to work with. They cut consistently from day to day, cut faster in many circumstances, and operation costs are less. In most scenarios, the more expensive machine is cheaper over the payback period. However, a CO2 laser is still clearly the machine of choice in many applications, such as when the customer is primarily cutting ½-in. stainless or if there is a very limited amount of production such that the additional equipment cost is simply not justifiable.”
“We are seeing that after the first investment in a fiber laser, a customer will quickly invest in a second. That means they are getting a very good payback,” said Bello. “Even when cutting speeds are similar to the CO2, the cost per hour is lower with the fiber.”
Considering solid-state fiber technology?
Ask material questions:
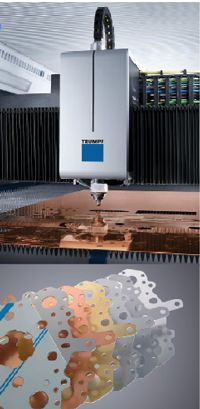
Solid-state lasers expand cutting capabilities to include exotic and coated materials. Photo courtesy of TRUMPF.
- What is my material type?
-
If copper, brass, or other exotics are included in the mix, solid-state technology is the choice.
- What is the typical material thickness?
-
If a lot of ¼-in. and thinner materials flow through the shop a solid-state can substantially increase productivity.
- What are my quantities?
-
If small batches of dissimilar parts are common, solid-state technology offers flexibility to quickly change cutting parameters for different materials and thicknesses.
subscribe now
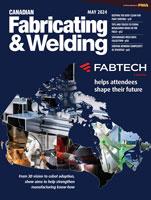
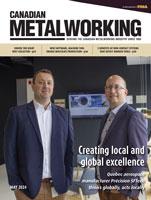
Keep up to date with the latest news, events, and technology for all things metal from our pair of monthly magazines written specifically for Canadian manufacturers!
Start Your Free Subscription- Trending Articles
- Industry Events
Automate 2024
- May 6 - 9, 2024
- Chicago, IL
ANCA Open House
- May 7 - 8, 2024
- Wixom, MI
17th annual Joint Open House
- May 8 - 9, 2024
- Oakville and Mississauga, ON Canada
MME Saskatoon
- May 28, 2024
- Saskatoon, SK Canada
CME's Health & Safety Symposium for Manufacturers
- May 29, 2024
- Mississauga, ON Canada