- FMA
- The Fabricator
- FABTECH
- Canadian Metalworking
Punching up Forms
Upforming quickly creates simple or high and complex forms on a turret
- By Sue Roberts
- August 22, 2013
- Article
- Fabricating
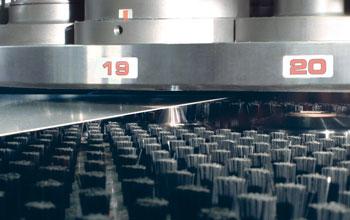
During upforming in a Prima Power turret, the servo-electric control raises the lower die in increments of 0.001 in. Photo courtesy of Prima Power.
From producing fairly simple tapping extrusions to bends to tabs, and from tall louvers to complex special shapes, upforming can enhance a turret’s multitasking capabilities and reduce multiple processes to one pass. Press brake bending, drilling, and other downstream processes often can be bypassed.
Forming dies protruding above the die line were an initial drawback to forming on a turret. Material risked being scratched or distorted during repositioning, and form heights were restricted due to the reduced machine gap. Upforming avoids these issues because the die rests below the standard die line, and the forming portion of the die rises above that line only during the forming process.
“We discovered the benefits of upforming technology as we went along,” said Lutz Ehrlich, punching and automation product manager, Prima Power North America, Arlington Heights, Ill. “The initial benefit was to become scratch- and mark-free for cosmetically sensitive materials. As the technology advanced and servo-electric was incorporated to control the lower stroke in increments of 0.025 mm [0.001 in.], processing options increased without compromising process stability.”
An added advantage of the retracted upform die is that it can remain in the station when not in use. Since it does not interfere with other processes in this position, setup time is reduced.
Extra Tooling Height
Traditional rules of thumb apply to material thickness when upforming. From 1.02 to 2.05 mm (18 to 12 ga.), where the bulk of fabrication occurs, the material is thin enough to punch and form easily but thick enough for the material to flow into a form without fracturing or tearing.
“Various machines have different capabilities as to when they move the lower die and how much pressure they have to move that die,” said Glen Shuldes, applications engineer at Wilson Tool International, White Bear Lake, Minn. “The tool has to be designed to work along with the machine. Typically, an upforming die is taller because of the springs that have to be built in.
“We can form higher because the die is moving up. Bringing the punch down first to put pressure on the sheet before the lower die starts moving provides good sheet control.”
Using the Gap
Joe Schneider, vice president of marketing for Mate Precision Tooling, Anoka, Minn., explained, “Upbending takes advantage of the extra turret feed gap so you can do higher bends, higher forms in general. You want a few millimeters’ safety when determining your height, so if you have a 19-mm [0.75-in.] feed gap and 1-mm [18-ga.] material thickness, you may be able to bend a 17-mm [0.67-in.] -high tab. In traditional forming, this same 19-mm feed gap might yield only an 11-mm -high tab.”
Pressures for upforming, punching, and standard forming are typically similar. The tonnage of the machine or the properties of the material determine the limitations, not the upforming process. Dimensions of the form are limited only by the standard station range.
“We run into tonnage issues with the forming tools, but we run into that with our regular tools,” said Shuldes. “You have the material flow, but you have less shearing action. That makes up for the additional pressure for the material flow.”
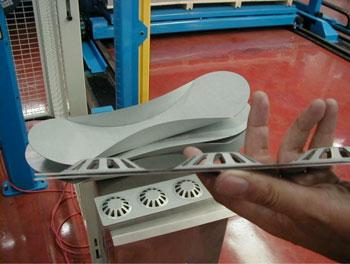
Upforming avoids scratching and distorting material as it is repositioned and allows forming of higher features. Photo courtesy of Mate Precision Tooling.
A Profitable Angle
The time, tooling, and setup savings that go along with indexable tooling, not available at the beginning stages of upforming, are adding to the process’s productivity today.
“Our upforming stations have the ability to index a shape or form tool with no tonnage constraint, with a diameter up to 8.89 mm [0.35 in.], creating a form height up to 15.75 mm [0.62 in.],” said Ehrlich. “This provides tremendous savings because one punch and die can be used to create an asymmetrical feature at any angle without additional tooling investment or setup time.”
The index upforming station also allows for the use of wheel and rollerball tools and can be used for second hits to complete a complex feature within the turret.
“You can raise a form or punch die into a created form to accomplish a secondary operation on the machine,” said Shuldes. “For example, if we created an emboss up, we could come back in with another forming tool and create a downform in the embossed up feature. If we can, we build those capabilities into the same tool, but some more complicated features have to be done with two hits.”
Special programming considerations come into play when upformed features are part of an application.
“There can be spacing issues. If a form is higher or the material is drawing more than usual, the material might be weakened and a hole might be distorted. Or if you have two forms together, you want to be sure the process for the next form doesn’t collide with the neighboring form,” said Shuldes. “When we design an upforming tool, we try to learn as much as possible about the application. The more information we get, the more we can account for material flow as we design the tool.”
Taking Care
“Maintenance of an upforming tool is generally the same as for standard tooling, but because there is usually less sliding motion within the forming tool itself, the need to take it apart for cleaning and degreasing is reduced,” said Shuldes. “Keep the tool sharp, and use appropriate shims after it has been sharpened.”
“There are a lot of tolerances built into a machine and tooling. These must be maintained to ensure proper punch and die alignment,” said Ron Windingstad, product engineering manager at Mate Precision Tooling. “Alignment features, keyways, pins, bores, and outer diameters of punches are very important when dealing with an asymmetrical feature. Pay attention to machine maintenance and alignment. The shape needs to be punched in the center of the opening of the die for the best quality results and to avoid premature wear on the tool.”
Storage can be a bit of a challenge unless a cabinet is designed to accommodate the odd shapes and sizes that come along with an upforming tool. The dies can be taller and thicker than standard dies.
subscribe now
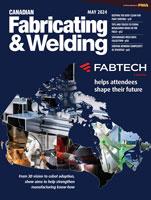
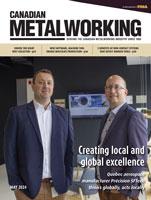
Keep up to date with the latest news, events, and technology for all things metal from our pair of monthly magazines written specifically for Canadian manufacturers!
Start Your Free Subscription- Trending Articles
- Industry Events
CTMA Economic Uncertainty: Helping You Navigate Kitchener Seminar
- May 2, 2024
- Kitchener, ON Canada
Automate 2024
- May 6 - 9, 2024
- Chicago, IL
ANCA Open House
- May 7 - 8, 2024
- Wixom, MI
17th annual Joint Open House
- May 8 - 9, 2024
- Oakville and Mississauga, ON Canada
MME Saskatoon
- May 28, 2024
- Saskatoon, SK Canada