Editor
- FMA
- The Fabricator
- FABTECH
- Canadian Metalworking
Drilling stainless steel: Tools and conditions for drilling steel
Using the correct cutting conditions, tool geometries can dramatically affect hole quality, tool life
- By Joe Thompson
- Updated January 13, 2023
- November 12, 2012
- Article
- Cutting Tools
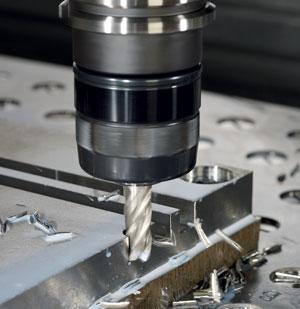
The mechanical properties of stainless steels, including heat resistance and high ductility, make them challenging to cut.
Stainless steel is a difficult material to chip. It is simply the nature of the beast.
While the corrosion resistance of these metals makes them popular in many industries, some of the mechanical properties of stainless steel, including heat resistance and high ductility, also make them challenging to cut.
Some stainless steels also have a tendency to work-harden more than others—304 and 316 are two examples.
While improper to group all stainless steels together under one banner, these materials typically share similar properties that give them a different machinability when compared to carbon steel. Perhaps the greatest difference is the high ductility of austenitic and duplex stainless steels. These materials also tend to work-harden easily and form built-up edges (BUE) on the cutting tool. Induplex stainless steels in particular, chip forming is difficult because of their high strength.
When the heat stays in the drill, the tool itself will begin to break down. In high-speed steel (HSS) drills, this heat will cause the tool to lose its hardness. In solid-carbide drills, microcracks can form on the cutting edges, which will eventually cause the drill to fail.
"When you machine stainless steel, you are generating high temperatures," explained Scott Turner, marketing manager—holemaking, Seco Tools. "But, because this material has been designed to handle high-temperature environments, it is difficult to cut and hard on cutting tools."
It is the metal's high modulus of elasticity—the nonpermanent deformation of material when force is applied—that makes it hard to break. Stainless steel actually is designed to bend a little bit before it breaks.
This characteristic makes it challenging to break the chip, which is especially important in a drilling operation because the chips need to be broken and evacuated from the hole as quickly as possible to reduce the chance of recutting.
And, as the hole gets deeper, the material continuously work-hardens, becoming even more difficult to cut.
"It's a simple fact that the heat generated by the cutting process will work-harden the material," said Turner. "This work hardening occurs at the bottom of the hole and along the hole's edge, and this work-hardened zone will follow the cutting edge along the hole to the bottom as it is created."
One way to reduce the amount of work hardening that occurs is to increase the back taper of the tool, which reduces the amount of contact between the tool and the part.
Geometry Matters When Drilling Stainless Steel
In addition to tailoring the back taper angle, other variables in the tool's design can make drilling stainless steels easier.
"A lot of the changeable variables in cutting stainless steels are trade-offs," said Turner. "You can make the cutting edge sharper, but then you weaken it and it breaks away. With a tougher [thicker] edge, you will get better tool life. You can change the angle of the cutting tip on the drill, but when you do this, you also give up some strength at the cutting edge."
Tool design for cutting stainless should include:
- A sharper angle at the cutting edge.
- Reduced width of the land margins.
- Increased back taper.
In addition, the design of the tool should incorporate through-coolant capability.
Coolant is important both for chip control and to extend tool life. Coolant delivered through the tool also aids chip evacuation.
"Proper coolant usage is very important in any drilling operation," said Turner. "Specific to stainless, we recommend that the coolant's lubricity be 8 to 10 percent. Also, a good flow of coolant to the tool tip is important. Getting the chips out of the hole quickly means the hole can be finished faster, which also reduces work hardening since less time is spent with the tool cutting in thehole."
Ensuring adequate coolant supply to the cutting zone means monitoring the pressure. This will vary depending on the depth-to-diameter ratio.
Work hardening can be more pervasive when drilling a deep hole because there is a tendency to "peck" drill—drilling into the workpiece for a distance, retracting the drill to remove the chips, and then drilling further. The bottom of the hole then becomes a work-hardened zone.
Pecking is not recommended because of this.
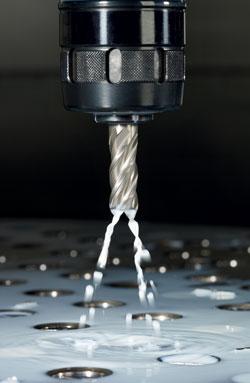
Coolant is important both for chip control and to extend tool life. Coolant delivered through the tool also aids chip evacuation.
Drilling Stainless Steel Requires Combating Deflection
Because some stainless materials have a high tensile strength, the tool may deflect on contact. Using a pilot hole is one way to prevent this from happening.
"Using a successful spotting or piloting strategy can overcome deflection," explained Pat Nehls, product manager, Walter USA. "On shallow holes where piloting is not needed because the drill is sufficiently stable, proper drill point geometry may be all that is needed to overcome deflection issues."
Whether or not a pilot cycle needs to be employed, it is important to control the speeds and feeds of the drilling operation.
If the speed is too slow, the drill will just rub the material, creating a work-hardened zone. Eventually this will cause the drill to fail faster.
"If the speed is too fast, too much heat will be generated, and this will also lead to a failure of the drill, especially extreme wear at the outside corners of the point," said Nehls.
Feed rate control is critical to ensure proper chip breaking.
"The feed has to be high enough for the cutting edge to cut, or enter into, the workpiece," said Nehls. "If it is too low, the drill will only rub against the workpiece, which again can cause a work-hardened zone. It also will prematurely wear out the drill. When the feed is too high, the chip form can become an issue, and very heavy chips that don't break may be produced. In addition, a feedrate that is too high can compromise the drill, leading to premature failure or breakage."
The best first step is to employ the speed and feed recommended by the manufacturer of the drill, added Nehls.
About the Author
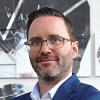
Joe Thompson
416-1154 Warden Avenue
Toronto, M1R 0A1 Canada
905-315-8226
Joe Thompson has been covering the Canadian manufacturing sector for more than two decades. He is responsible for the day-to-day editorial direction of the magazine, providing a uniquely Canadian look at the world of metal manufacturing.
An award-winning writer and graduate of the Sheridan College journalism program, he has published articles worldwide in a variety of industries, including manufacturing, pharmaceutical, medical, infrastructure, and entertainment.
Related Companies
subscribe now
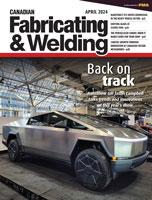
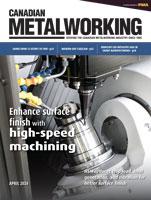
Keep up to date with the latest news, events, and technology for all things metal from our pair of monthly magazines written specifically for Canadian manufacturers!
Start Your Free Subscription- Trending Articles
Automating additive manufacturing
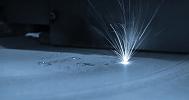
CTMA launches another round of Career-Ready program
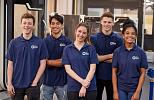
Collet chuck provides accuracy in small diameter cutting
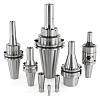
Sandvik Coromant hosts workforce development event empowering young women in manufacturing
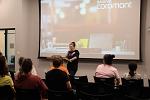
GF Machining Solutions names managing director and head of market region North and Central Americas
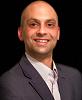
- Industry Events
MME Winnipeg
- April 30, 2024
- Winnipeg, ON Canada
CTMA Economic Uncertainty: Helping You Navigate Windsor Seminar
- April 30, 2024
- Windsor, ON Canada
CTMA Economic Uncertainty: Helping You Navigate Kitchener Seminar
- May 2, 2024
- Kitchener, ON Canada
Automate 2024
- May 6 - 9, 2024
- Chicago, IL
ANCA Open House
- May 7 - 8, 2024
- Wixom, MI