Editor
- FMA
- The Fabricator
- FABTECH
- Canadian Metalworking
Technology Spotlight: Large 5-axis Machining
Advancements enable manufacturers to create large, highly complex parts
- By Joe Thompson
- January 5, 2017
- Article
- Metalworking
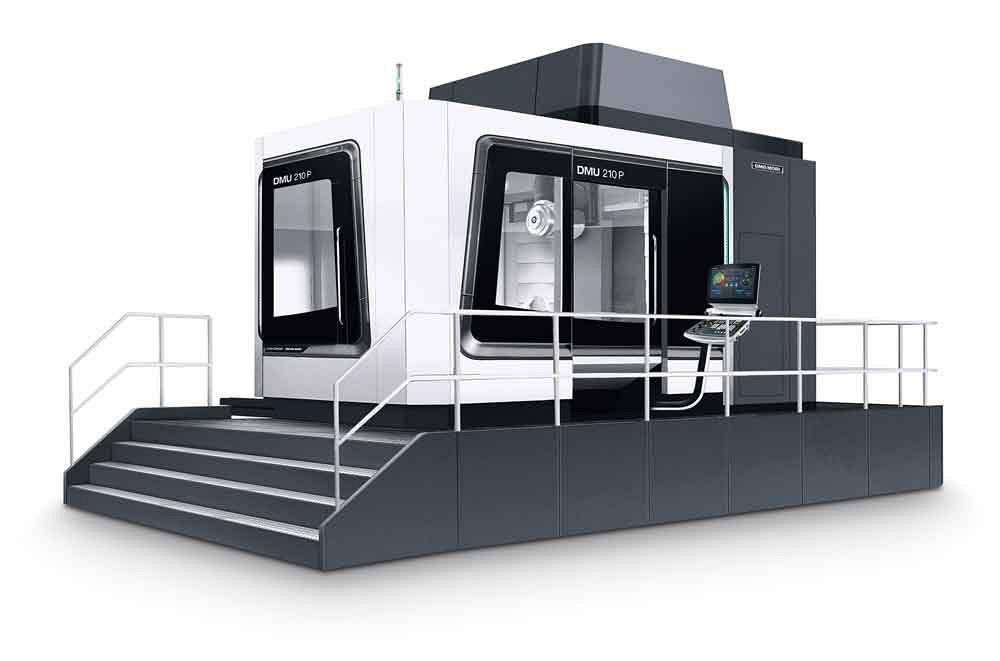
The DMG Mori second-generation DMU 210 P allows 5-axis applications with travel distances of up to 2,100 by 2,100 by 1,250 mm.
No matter if your work is in tool and mould construction, the aerospace industry, or the energy sector, a clear trend in all of these production environments is the creation of highly complex, high-quality workpieces with large dimensions.
These large parts typically are feature-rich, and the features themselves can also be large. To handle these challenges, DMG Mori has released a new generation of its DMU 210 P and DMU 600 G linear machines.
“The range of applications is exceptionally broad and is changing constantly. Take the aerospace industry, for example, where larger integral components are being milled from the solid, or the tool and mould construction sector with its gigantic moulds for automobile construction. This requires an equally broad product portfolio [of machines],” explained Alfred Geissler, CEO of DMG Mori’s Deckel Maho Pfronten operation.
While the second-generation DMU 210 P gives companies an entry point into large-part machining, Geissler stated the DMU 600 P is what can handle very large components. The smaller machine has travel paths of 2,100 by 2,100 by 1,250 mm and the larger machine has at least 6,000 mm in the X axis and 4,800 by 1,500 mm in the Y and Z axes, respectively.
“Where component weight is concerned, we are talking about at least 8,000 kg for the DMU 210 P,” said Geissler. For the 600 series machine the table load can be as much as 40,000 kg, he added.
But how can such large machines meet the demand for both flexibility and quality? It’s what’s inside that counts.
Machines in the company’s XXL program include a range of modules that enable application-specific configurations. For example, spindle choice can be based on what type of work the machine will be doing. The spindle offer for the DMU 210 P can be one of three options. The first option is the powerMASTER® motor spindle, which has a maximum 1,000 Nm. The next option is the torqueMASTER® gear spindle with up to 1,800 Nm, and the third option is the speedMASTER® spindle that can achieve speeds of up to 30,000 RPM.
These machines also work with an automatic system for exchangeable heads. This allows the use of gear spindles with up to 1,445 Nm as well as motor spindles with up to 30,000 RPM. This flexibility makes the machines suitable for both heavy-duty machining as well as high-precision, high-speed cutting. The options also include exchangeable heads with C/A or C/B kinematics for complex machining as well as mill/turn tables and needs-based tool magazines with 300 tools or more.
Complete Machining in One Setup
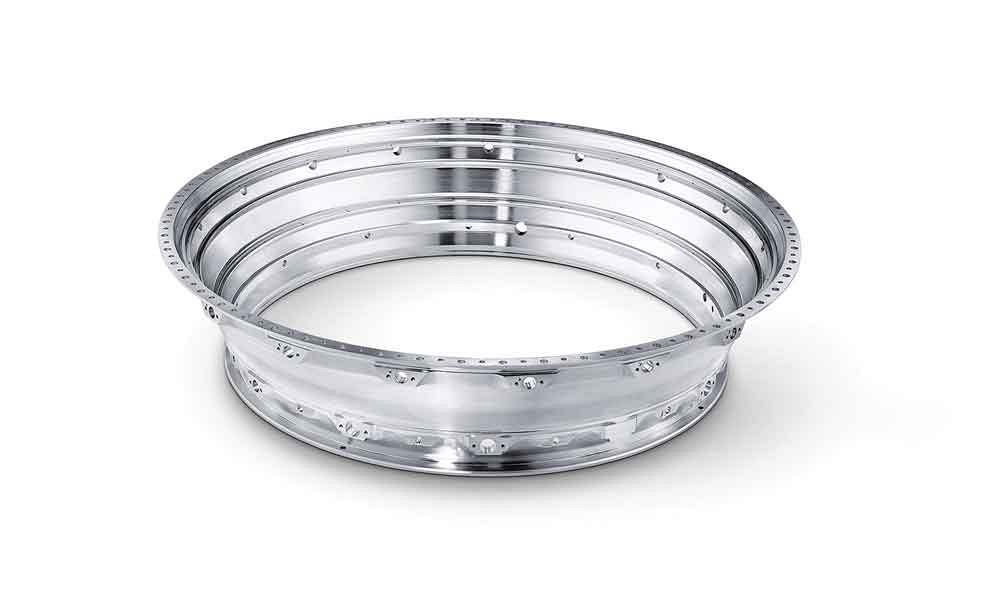
Large, feature-rich parts are becoming more and more common in North American manufacturing, causing machine tool manufacturers to produce equipment that can handle both large sizes and heavy weights.
These types of setups enable complete machining for nearly every application.
“Reclamping processes and setting up operations would push up idle times to such an extent that such production would no longer be worthwhile. So 5-sided and 5-axis machining is essential in this segment to ensure that the large workpieces can be machined profitably at all,” said Geissler. “Options such as a mill/turn table or pallet changer therefore boost productivity even further. Complete machining is also vital where quality is concerned, because reclamping processes would also be counterproductive.”
No matter if the part is a small bone screw or a large die plate, quality is important and must be maintained. Machining precision and surface quality have to be within acceptable limits. The basis for this lies in a stable machining platform.
Construction of these machines includes EN-GJS-600-3 (GGG60) cast-iron parts, which help ensure rigidity, allowing accurate yet dynamic machining.
“This eliminates the need for any reworking processes, thus boosting productivity even further. The results are so good because the linear motors have a direct, rigid connection with the machine structure. Plus, there are no gear meshing frequencies or backlash from the drivetrain. Added to this are a high control bandwidth and improved axis parameters compared to conventional drive technology,” said Geissler.
To handle thermal deviations that can wreak havoc on accuracy, the DMU 210 P has an intelligent cooling system that encompasses the drive motors, guides, ball screws, and the gears of the rotary axes. In addition, the rear side of the external control cabinet has been insulated, the machine has a spindle growth sensor, and cooling of the machine bed has been incorporated. Temperature control of the machine structure is also available as an option.
Editor Joe Thompson can be reached at jthompson@canadianmetalworking.com.
DMG Mori, 905-795-2891, www.dmgmori.com
About the Author
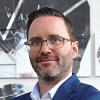
Joe Thompson
416-1154 Warden Avenue
Toronto, M1R 0A1 Canada
905-315-8226
Joe Thompson has been covering the Canadian manufacturing sector for more than two decades. He is responsible for the day-to-day editorial direction of the magazine, providing a uniquely Canadian look at the world of metal manufacturing.
An award-winning writer and graduate of the Sheridan College journalism program, he has published articles worldwide in a variety of industries, including manufacturing, pharmaceutical, medical, infrastructure, and entertainment.
subscribe now
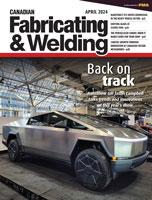
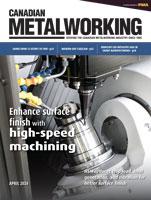
Keep up to date with the latest news, events, and technology for all things metal from our pair of monthly magazines written specifically for Canadian manufacturers!
Start Your Free Subscription- Trending Articles
Automating additive manufacturing
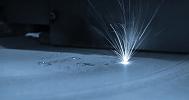
CTMA launches another round of Career-Ready program
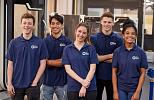
Collet chuck provides accuracy in small diameter cutting
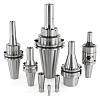
Sandvik Coromant hosts workforce development event empowering young women in manufacturing
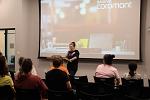
GF Machining Solutions names managing director and head of market region North and Central Americas
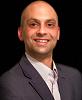
- Industry Events
MME Winnipeg
- April 30, 2024
- Winnipeg, ON Canada
CTMA Economic Uncertainty: Helping You Navigate Windsor Seminar
- April 30, 2024
- Windsor, ON Canada
CTMA Economic Uncertainty: Helping You Navigate Kitchener Seminar
- May 2, 2024
- Kitchener, ON Canada
Automate 2024
- May 6 - 9, 2024
- Chicago, IL
ANCA Open House
- May 7 - 8, 2024
- Wixom, MI