- FMA
- The Fabricator
- FABTECH
- Canadian Metalworking
Don’t overlook critical machining center features
Below are some features you should consider that will help you make the right long-term decision.
- By Canadian Metalworking
- June 29, 2015
The traditional 40x20 vertical machining center (VMC) may be the most popular machine platform of all time. After all, it’s the direct descendent of the manual knee mills that dominated the market for most of the 20th century. Today, demand for this platform continues to be strong. Just stroll around IMTS and you’ll quickly realize the staggering number of machine tool builders competing for your business in the 40x20 market! All these choices can make for a very difficult purchasing decision. What machine features should you weigh more heavily? Which machine provides the best combo of performance and durability? What about service and support? Below are some features you should consider that will help you make the right long-term decision.
Critical Machining Center Features
Mass – The casting is literally and figuratively the foundation of the machine tool. There is no substitute for mass, which directly influences things like tool life, surface finish, machine longevity, and thermal stability. In difficult cuts, some machines vibrate so loudly you can’t hear yourself think, whereas a machine with sufficient mass is often so quiet that you can only hear chips hitting the glass. This means the casting is absorbing the energy instead of your workpiece, your workholding, your carbide, your spindle bearings, etc.
Design – Does the casting design look strong and robust? A base casting with a symmetrical and rugged design is ideal.
Footprint – Floor space is valuable in machine shops and compact machine footprints are a high priority. Many vertical machining center builders provide tables that move in both X & Y, creating a lot of table overhang and a large machine footprint. However it is possible to find a VMC with a very compact machine package. Consider a VMC construction where the table moves only in Y, which leads to a more compact machine package.
Productivity – Most economy vertical machining center builders require tools be changed only through the spindle nose, a process that inhibits production and is an ergonomic burden on the operator. There is a better way to do this, such as separate tool cabinet separated from the work envelope with its own separate access door. This means operators can check inserts and change tools without ever stopping the spindle!
Spindle – This component is the heart of every machine tool. It’s wise to request a demonstration of high speed machining on tough materials, to ensure your spindle has the strength to handle whatever you might throw at it. It’s also a good idea to find out how you’ll be supported in case a catastrophic event occurs (a bump, nudge, kiss, or crash). These nasty surprises are never pleasant, but a pre-planned system of service backups will help reduce your downtime pain.
The moral of the story? Don’t overlook the intangible machine features which directly impact the true cost of ownership over time.
This blog originally appeared on www.okuma.com. It has been republished on Canadian Metalworking’s website with permission from the Okuma America Corporation.
subscribe now
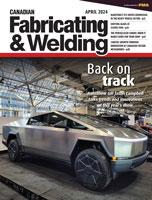
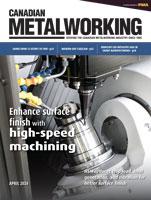
Keep up to date with the latest news, events, and technology for all things metal from our pair of monthly magazines written specifically for Canadian manufacturers!
Start Your Free SubscriptionAbout the Author
- Trending Articles
Automating additive manufacturing
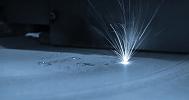
CTMA launches another round of Career-Ready program
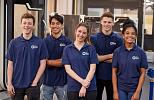
Collet chuck provides accuracy in small diameter cutting
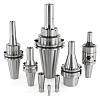
Sandvik Coromant hosts workforce development event empowering young women in manufacturing
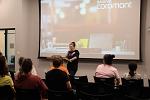
GF Machining Solutions names managing director and head of market region North and Central Americas
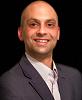
- Industry Events
MME Winnipeg
- April 30, 2024
- Winnipeg, ON Canada
CTMA Economic Uncertainty: Helping You Navigate Windsor Seminar
- April 30, 2024
- Windsor, ON Canada
CTMA Economic Uncertainty: Helping You Navigate Kitchener Seminar
- May 2, 2024
- Kitchener, ON Canada
Automate 2024
- May 6 - 9, 2024
- Chicago, IL
ANCA Open House
- May 7 - 8, 2024
- Wixom, MI