Editor
- FMA
- The Fabricator
- FABTECH
- Canadian Metalworking
Palcam Makes AM a Canadian Advantage
CEO Walter Palisca believes the sweet spot for a new industrial revolution will be in metallurgical expertise
- By Rob Colman
- July 3, 2016
- Article
- Metalworking
Palcam Technologies Ltd. founder and CEO Walter Palisca is a great believer in what Canadian industry could and should be.
He demonstrates this through example, attracting and hiring the best young talent, investing in the best equipment and machining technologies available, and always looking for innovative ways to deliver the most value and quality to his customers.
Small wonder then that Palisca is investing heavily in additive manufacturing (AM) technologies. But rather than simply buying AM systems and producing parts, Palisca is pushing the boundaries of what's currently available in the marketplace and reinventing the technology to offer greater and more robust process controls, which in turn is leading to capability breakthroughs in tool steels such as H13.
Deep Manufacturing Roots
Newmarket, Ont.-based Palcam has proven itself over the past 20 years by delivering quality products to the automotive, aerospace, medical, and industrial sectors. The company’s core product offerings include precision components (both sample and production quantities) and fully engineered tooling systems and components.
The shop is like a showroom of the latest and greatest machining capabilities available, such as 5-axis and multispindle turning/milling centers, wire and sink EDM, Swiss-style lathes, CMM with integrated laser scanning, and reverse engineering technology, to name only a few.
Palisca, a toolmaker by trade, launched Palcam when offshoring had already become a huge concern for domestic manufacturers. It was something that did and does frustrate him.
Speaking to the offshore justification, Palisca said, “It’s an illogical rationale. If you just focus on the needs of the people involved, it doesn’t add up. The professional in India or China has the same needs as the professional working here; he needs to eat and take care of his family. Offshoring becomes cheaper due to compromises on environmental regulations, worker safety, and other attributes that we value in Canada. So it becomes irrational when we can purchase and consume offshore products that subvert these values we’ve chosen to hold.”
So regarding offshore competition: “No problem, just make the playing field even. In the meantime we’ll just need to innovate faster.”
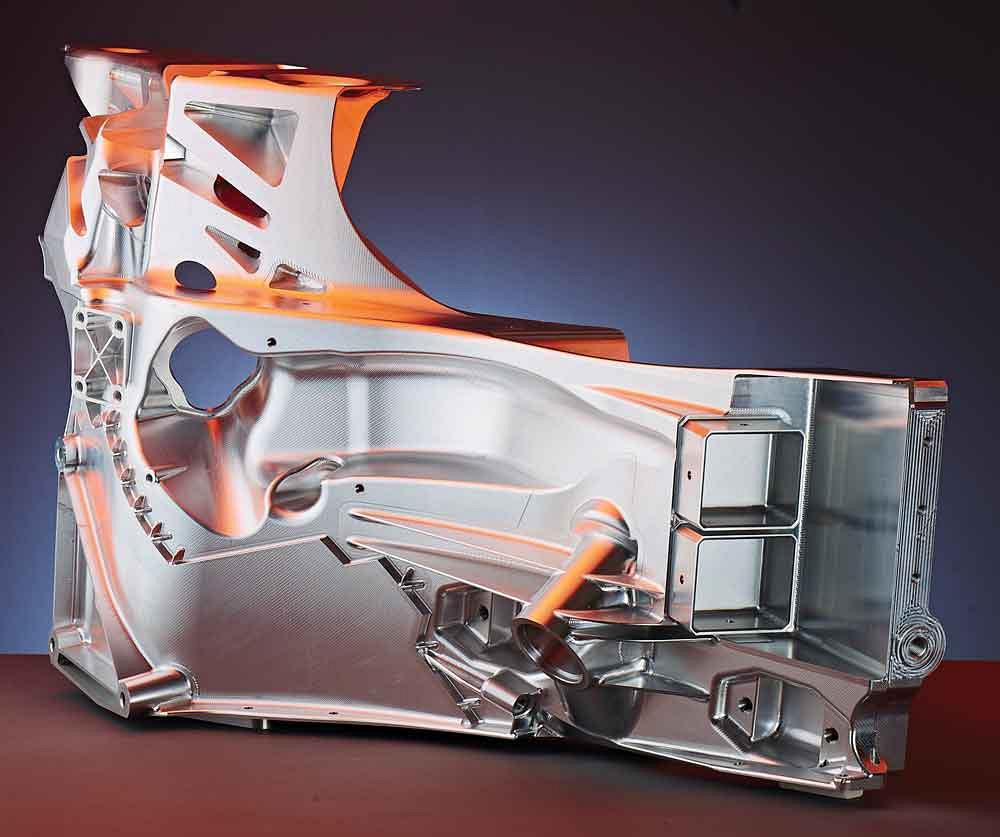
Palcam Technologies also specializes in the production of highly complex machined parts such as this aluminum automotive structural component, which was completed in just four operations.
Attracting Young Talent
In this respect, Palisca aims to be a model employer, creating an environment that is beyond just safe, but is somewhere employees want to come every day and be part of a team that's building a better future for the Canadian manufacturing industry. You can see and feel this initiative throughout the facility, whether it's the state-of-the-art equipment, dynamism of the young people, spotless floors, modern lunchroom, fresh fruit, and pool table, Palisca is not only innovating on the shop floor, he’s innovated and developed an environment that attracts and inspires the best possible employees.
Palisca explained, “Innovation on the investment side is one thing, but you wouldn’t get anywhere without the people. We try really hard to get engagement from all levels, as much as possible.”
Palisca also believes in developing local talent. He is very involved with Georgian College’s machinist program and often hires students straight out of the school.
“We usually get the first pick of students coming out of the colleges because they want to work here,” said Palisca. “We have designed our environment to appeal to the youngest, brightest minds coming from any school. My goal is that when I retire, I want to see that manufacturing-related careers are vibrant here in Canada, and that it is not only a legitimate career choice for students entering post-secondary, but it's the best choice.”
Palcam certainly has created a loyal team. Several of the top people in the company were recruited directly from school. More than half the team has been with the company for more than 10 years, and about a quarter for over 15 years.
Additive Manufacturing Investment
Palisca describes his role at Palcam as “the front end of the dreaming,” assessing technologies and deciding on the next steps for growth.
“It's vital to select a path on which both Palcam and Canada are well-positioned to succeed globally,” he said.
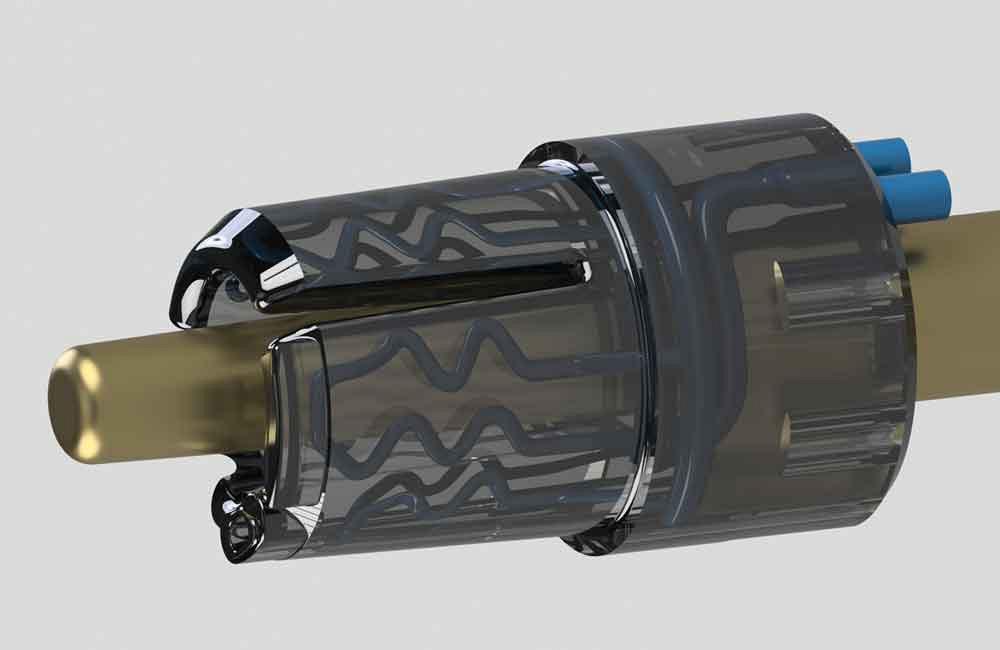
Parts with additive manufactured conformal cooling can last up to five times longer than those made by conventional means.
AM has turned out to be a logical next step for Palcam.
Last year the company launched an AM initiative focused on the development of tooling components for the high-pressure aluminum die-casting sector. According to Palisca, additive technologies have been in the works for a few years, but nobody had addressed tool steel manufacturing. The purpose was to introduce efficiency gains through additive design to the high-pressure casting industry. Palisca believes AM technology can expand the capabilities of the die-casting process itself, leading to more components being cast, which in turn increases aluminum content per vehicle, resulting in lighter, more fuel-efficient vehicles.
Palcam’s investment in AM technology is budgeted at $30 million over the next five years, and Palisca estimates it will create 100 high-technology manufacturing positions in southern Ontario. The investment will likely affect all sectors of manufacturing in which Palcam works.
Since the launch of this initiative last year, Palcam has developed and proven processes for manufacturing additive tooling inserts using H13 grade tool steel as opposed to maraging steel, which is the norm for the additive industry. According to Palisca, Palcam is the only company in the world currently producing H13 additive-manufactured tooling components for the high-pressure aluminum die-casting sector.
These H13 components have a five-fold increase in life when compared to maraging steel, and because of the additive design features, such as conformal cooling, the tools are outlasting conventional tooling manufactured from premium H13 billet material.
Because of the dramatic increase in thermal control, which reduces thermal fatigue, part quality is improved and tool life extended.
Additive-manufactured tooling -- or “smart” tooling as Palisca describes it -- can provide a multitude of benefits to the casting process, but the most immediate benefit has been advances in cooling through conformal cooling design.
Palcam has successfully tested and deployed several conform-designed components into high-pressure aluminum die-cast production tooling, with more on the way. This has not only drawn interest locally in North America, but throughout Europe as well.
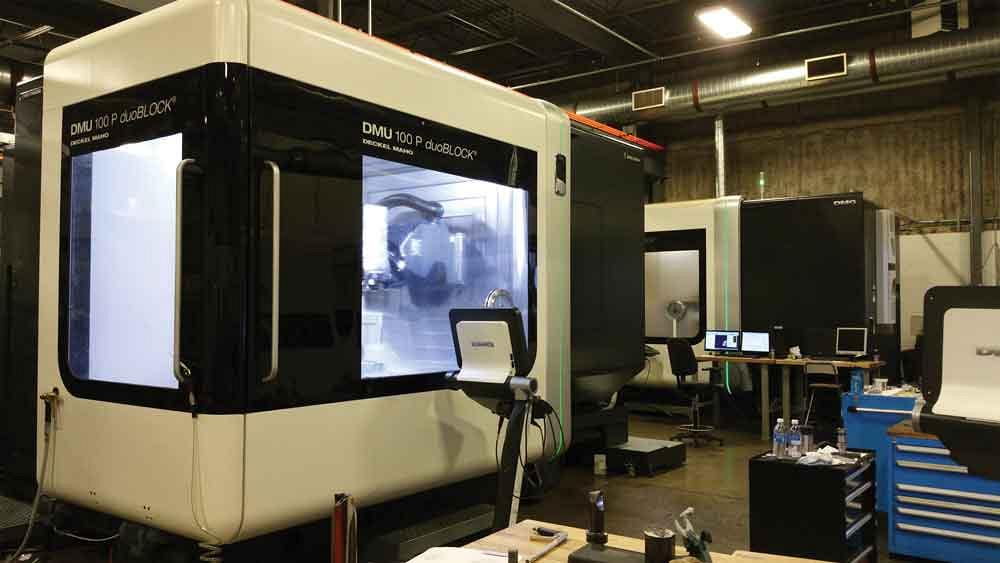
The company uses complex, 5-axis milling machines like this one to create parts for its customer base.
“By the end of this year we hope to have 20 chambers running, which would be the largest additive manufacturing facility in North America, which will allow us to become global leaders in AM tooling,” said Palisca.
Ultimately, Palisca believes that the AM process itself will become a commodity, so the true value will be in the engineering and process control.
“I think leadership in the sciences behind additive design and materials development should be the strategic focal point of Canadian manufacturing efforts,” said Palisca. “This in itself will offer Canada a secure, long-term platform for manufacturing leadership globally. The AM opportunity truly allows for IP protection, and the rewards will come back home to fund next levels of R&D.”
Palisca wants to see Canada really take this opportunity to thrive and is engaging universities here to push AM opportunities further.
“We need to enable our universities to become the focal point of material innovations,” he said.
With efforts already bearing fruit at Palcam, it may just be a matter of time before Palisca’s hopes become reality.
Contributing Editor Robert Colman can be reached at rcolman@canadianfabweld.com
Palcam Technologies Ltd., 905-835-1675, www.palcam.com
About the Author
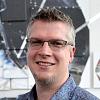
Rob Colman
1154 Warden Avenue
Toronto, M1R 0A1 Canada
905-235-0471
Robert Colman has worked as a writer and editor for more than 25 years, covering the needs of a variety of trades. He has been dedicated to the metalworking industry for the past 13 years, serving as editor for Metalworking Production & Purchasing (MP&P) and, since January 2016, the editor of Canadian Fabricating & Welding. He graduated with a B.A. degree from McGill University and a Master’s degree from UBC.
subscribe now
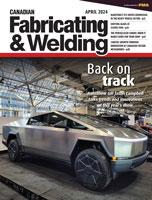
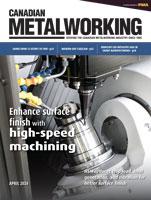
Keep up to date with the latest news, events, and technology for all things metal from our pair of monthly magazines written specifically for Canadian manufacturers!
Start Your Free Subscription- Trending Articles
Automating additive manufacturing
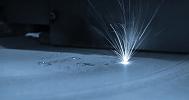
CTMA launches another round of Career-Ready program
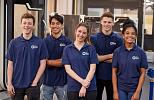
Collet chuck provides accuracy in small diameter cutting
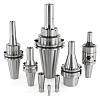
Sandvik Coromant hosts workforce development event empowering young women in manufacturing
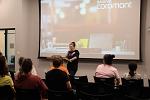
GF Machining Solutions names managing director and head of market region North and Central Americas
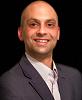
- Industry Events
MME Winnipeg
- April 30, 2024
- Winnipeg, ON Canada
CTMA Economic Uncertainty: Helping You Navigate Windsor Seminar
- April 30, 2024
- Windsor, ON Canada
CTMA Economic Uncertainty: Helping You Navigate Kitchener Seminar
- May 2, 2024
- Kitchener, ON Canada
Automate 2024
- May 6 - 9, 2024
- Chicago, IL
ANCA Open House
- May 7 - 8, 2024
- Wixom, MI