- FMA
- The Fabricator
- FABTECH
- Canadian Metalworking
RWP’s Components Spark Production
Machining the tough parts for resistance welding
- By Sue Roberts
- March 2, 2017
- Article
- Made In Canada
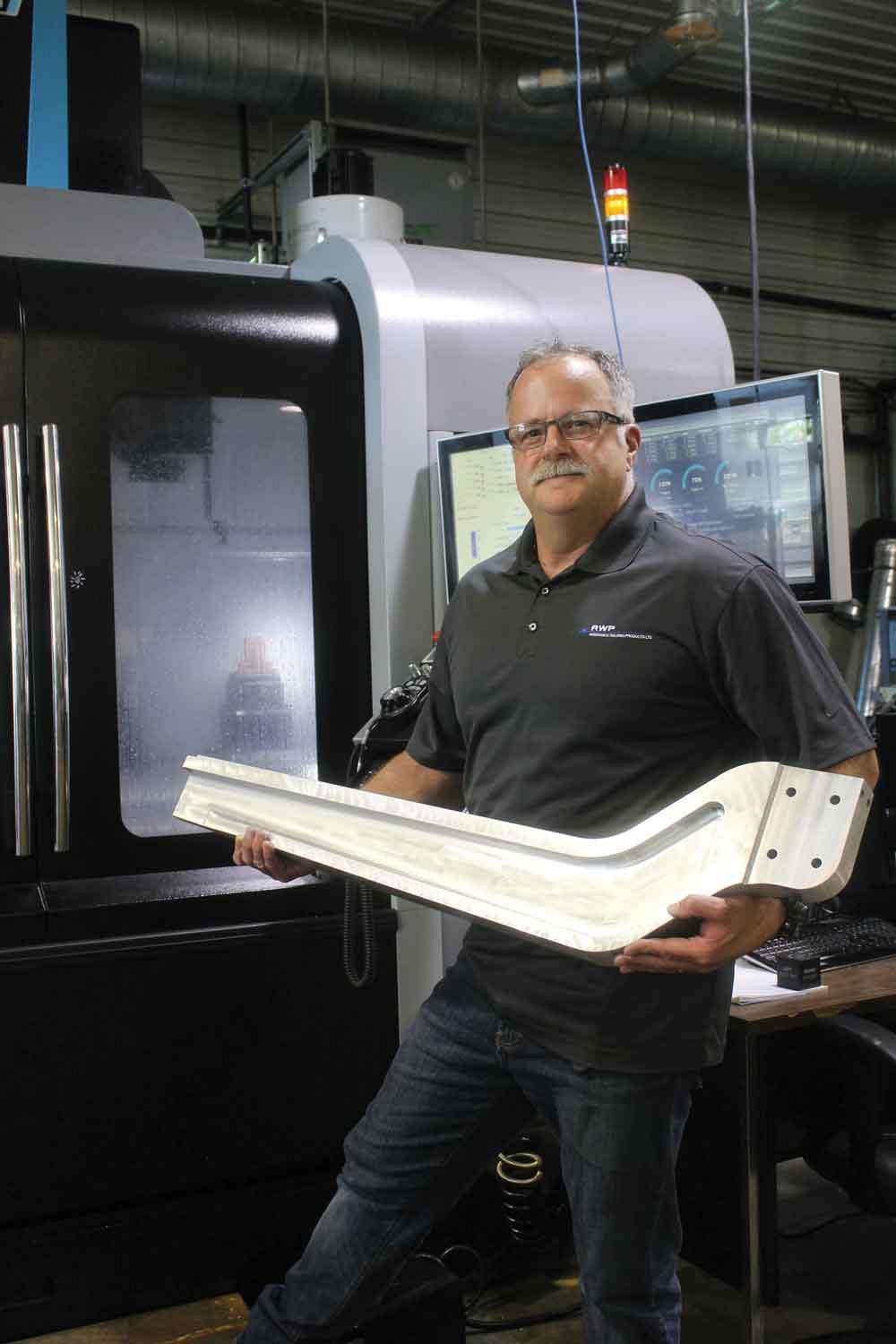
Alan McGuigan, operations manager at Resistance Welding Products Ltd. in Blenheim, Ont., holds an aluminum arm for a robotic welder. Photo by James Gervais.
A sign in the production manager’s office at Resistance Welding Products Ltd. (RWP) in Blenheim, Ont., confirms the belief of RWP and Tuffaloy, its parent company, in investing in the latest technology and continually upgrading processes. It reads, “You can’t do today’s job with yesterday’s methods and be in business tomorrow.”
Investment in manufacturing technology, training, and systems has kept RWP at the forefront of the resistance welding industry and explains the demand for its products throughout automotive, consumer, and industrial markets in North America.
RWP manufactures a diverse range of products, from small, intricate, threaded electrodes to large weld gun arms for some of the largest and most demanding customers in the automotive sector.
About two dozen employees produce these specialty products from non-ferrous materials such as aluminum, brass, bronze, copper alloys, and stainless steel and insulation materials including nylon, Nylatron®, and Micarta™.
Reaching the Global Market
RWP evolved from a two-man company that began in Troy, Ont., that distributed resistance welding products and produced copper cable. The company began manufacturing its own brand of a limited number of welding products in 1963. The brand was so well received that by 1971 the company moved to a larger property in Blenheim, expanded its manufacturing capabilities, and began offering RWP components for virtually everything needed for the resistance welding process.
Today RWP is part of an international group of companies that primarily focus on resistance welding technologies. Tuffaloy Products Inc., the parent company, has headquarters in South Carolina. Entron Controls, with locations in the U.S., Europe, and Mexico, produces weld controls, Advanced Cylinder Products-brand hydraulic and pneumatic products, and consumable metal alloys.
CMW, located in the U.S., manufactures the high-volume resistance welding products, including electrodes, holders, seam welding wheels, rings, bushings, and special dies. When it became part of the Tuffaloy group in 2015 half of its equipment was shipped to Canada and the other half to South Carolina, increasing production capabilities in both locations.
Alan McGuigan, RWP operations manager, said, “Joining the Tuffaloy group of companies in 2008 was the best thing that could have happened to RWP. All the companies that are part of the group are at the forefront of resistance welding and we fit right in.”
Sean Simmons, Tuffaloy president, has a strong desire to support each company and make it stronger.
“RWP may look fairly small, but we are a growing part of a global company. Our niche within the organization is providing customers with the difficult, low-volume products,” McGuigan said. “We are heavily involved with product development for our customers.”
Staying Responsive
A good percentage of RWP’s business is generated by automotive integrators that work with manufacturers in North America, Europe, Japan, and China. That’s good business but it can be difficult to manage.
“We get a lot of peaks and valleys that can be challenging because we have to be responsive. We have a steady business through a standard consumable product line that has a continuous flow, but we are driven by the integrators who work on the new lines going into the automotive plants. For example, new lines that are going into the Chrysler and GM plants will provide a large volume of business for us for three to six months,” McGuigan said.
“A lot of upfront planning and predictions come out of our customer contracts. We do our best to plan ahead, but we don’t really know what is coming until we get the purchase orders.” In many cases, orders are received, processed, and dispatched within 24 hours.
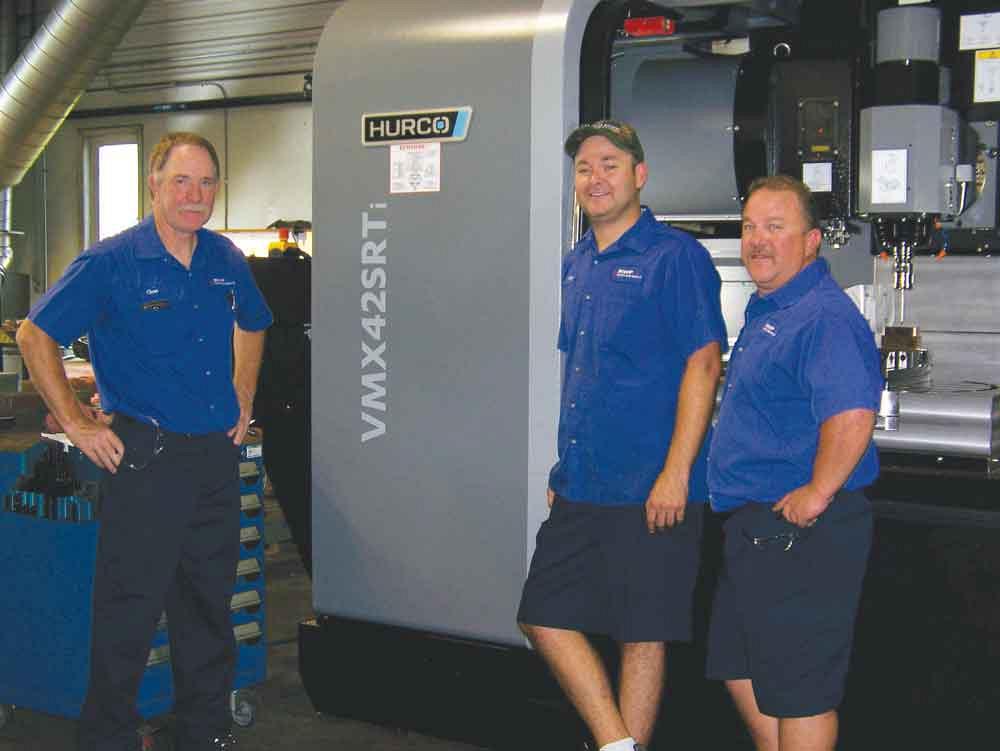
Machinists Marty Wysman, Paul Montgomery, and Clare Malott researched 5-axis machining centres prior to the company’s Hurco purchase.
RWP products are supplied across the globe in a variety of ways. RWP handles most of the Canadian distribution from Blenheim, selling through a number of companies in Windsor and the Greater Toronto Area. A network of distributors take care of the U.S. customers. Feeder plants supply the Japanese automotive builders.
“A lot of our production goes into the robots that weld cars—electrodes, copper and aluminum arms, bend adapters, shunt blocks--basically everything that goes into the weld guns. But we also supply smaller companies that are doing spot welding with some of the smaller guns or stand-alone units,” McGuigan said.
He cited an unusual application for one of RWP’s shunts. It was produced for use in a European nuclear plant.
Repair of resistance welding equipment is also one of the company’s services.
Improving Processes
A white board in McGuigan’s office helps keep a focus on continual process improvement. It lists the operations involved in moving a product from the raw material stage to out-the-door. For example, for one family of components it may show cut-turn-drill-heat treat-layout-mill-clean-inspect-ship. All processes are completed in-house.
Process improvements come from paying close attention to two areas. One is streamlining existing procedures within the cells dedicated to specific product lines. The other is keeping up with new technology, whether it’s designing and building its own equipment to incorporate new capabilities or purchasing equipment with advanced technologies.
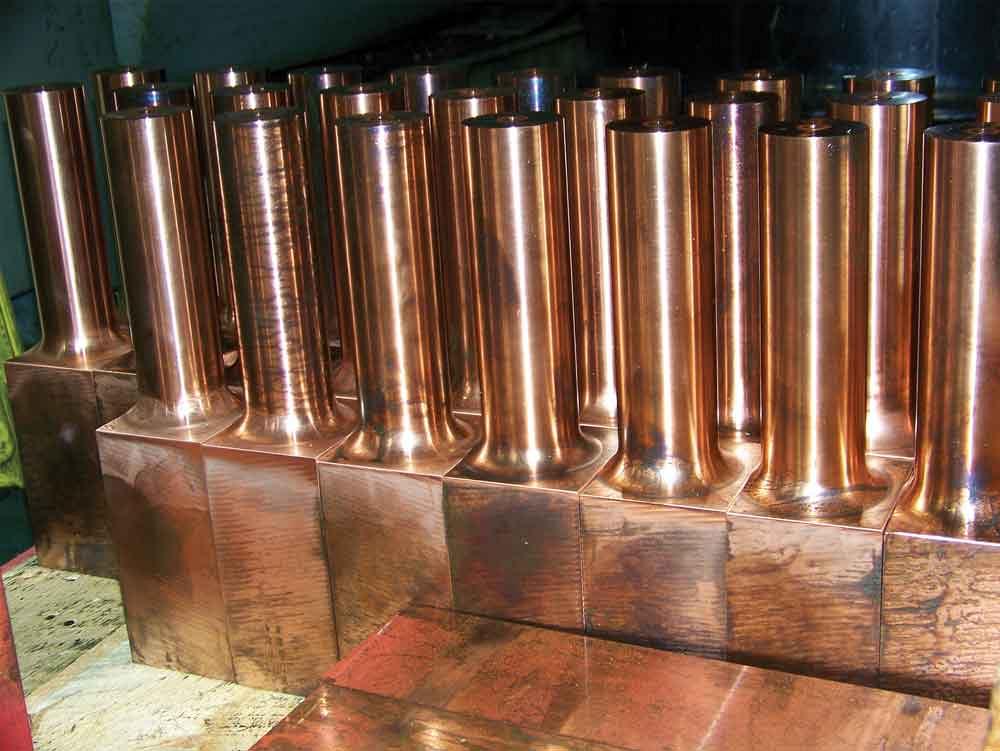
Copper adaptor blocks used on aluminum gun arm for robotic welding are ready for secondary machining.
About five years ago the company took delivery of a CNC multitasking machine that helped reduce the number of processes involved in some of the more complex components. “When we installed the machine, there were only four of them in North America,” McGuigan said. “Its first project was an aluminum bar that went in a directional bore machine to hold electronics. It was a pretty complex piece of work for the oil industry. We put the material in the multiaxis milling/turning machine, ran the program, opened the door, and the part was done.”
The machine provided more speed and capabilities for complicated parts but didn’t replace the other mills. Depending on the job, how it flows through the shop, and how many components are needed, it may bypass the multiaxis machine and be completed on one of the other mills.
Adding Technology
An uptick in industry demand for aluminum arms for welding robots plus RWP’s dedication to becoming the supplier of choice for those arms led to the recent purchase of a Hurco VMX 42 HSRTi 5-axis machining centre.
“The arms typically have a lot of complex shapes and angles that need to be machined. We were producing some large aluminum arms before adding the Hurco, but we recognized that we needed 5-axis capability to speed up our processes, become more competitive, and capture more of that business,” McGuigan said. “We did a test trial and the pricing showed us that a 5-axis machine would put us right where we needed to be to produce those arms economically.”
Three team members formed a search committee to investigate equipment options. As part of their research they visited companies with various 5-axis machines in production. Machinist Marty Wysman explained that they went back and forth on whether to purchase a vertical or horizontal centre, and one of the deciding factors for the Hurco was that it offers both capabilities.
The machine has a swivel head and an embedded, 50-in. by 24-in., C-axis rotary table that can handle parts up to 1,100 lbs. Up to 40 tools can be loaded into the swing-arm automatic tool changer. Room in the work envelope makes it possible to use a vise to position a component for sixth side machining. X- and Y-axis travel is 1,378 IPM; Z-axis is 1,181 IPM.
When parts don’t require 5-axis machining, the machine’s design configuration allows the full 42-in. by 24-in. work envelope to be used in 3-axis mode.
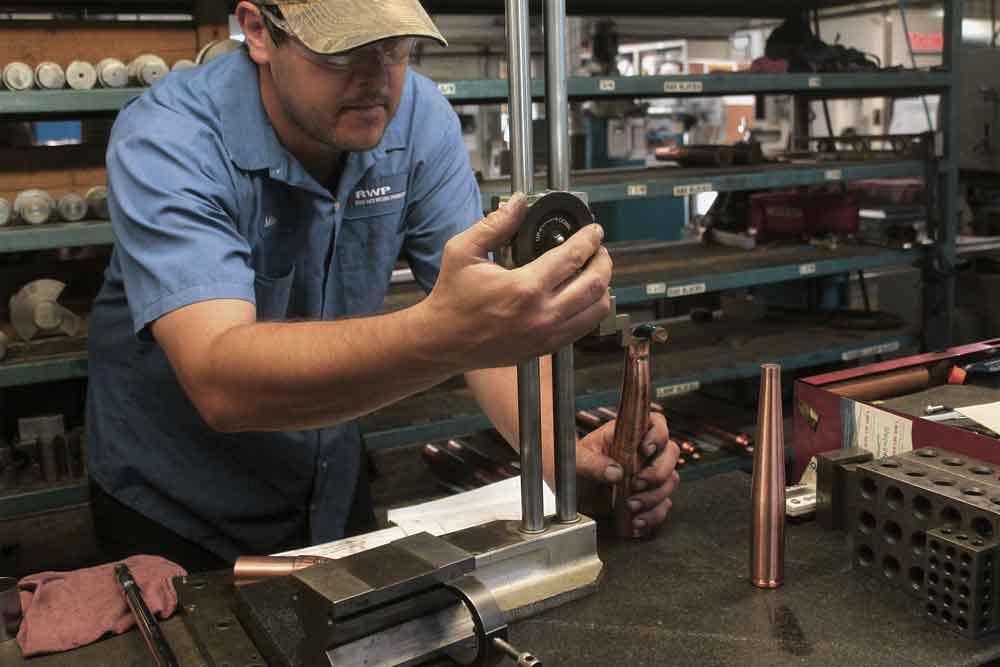
Mike Cylwa verifies dimensions on an adaptor following the bending operation. Photo by James Gervais.
User-friendly controls were also important to the team, particularly since this was the first 5-axis machine in the shop. Hurco’s conversational programming, in addition to the NC programming mode and NC/conversational merge feature, made transitioning from 3-axis to 5-axis programming fairly intuitive.
“A lot of our operators already had knowledge and background in CNC programming, so the learning curve was short,” McGuigan said. “When it comes to choosing a machine, they know their business very well. They know what we need, take ownership of the decision, and will make it go. I trust them.”
Increasing Competitiveness
“We’re just a little place in Blenheim, but we see a lot, do a lot, and have a wide reach. We can pretty much guarantee that everyone who has driven a Chrysler product can say that one of our products has touched the car,” McGuigan said.
“We strive to look at everything, review everything, and use the best technologies available. Manufacturers in Canada are competing against companies overseas. A lot of times the overseas advantage is a combination of the dollar value and the labour costs. You can minimize that impact by being very efficient on this end.”
Then, of course, there is the quality. “RWP has always been known for providing quality products in tight delivery times. Our customers choose us because we work with them and are very responsive. When they have a need, they want it today. We do our best to deliver that quality on time.”
Associate Editor Sue Roberts can be reached at sroberts@canadianmetalworking.com.
Resistance Welding Products, 519-676-8173, www.rwpweld.com
About the Author
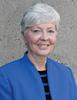
Sue Roberts
2135 Point Blvd
Elgin, IL 60123
815-227-8241
Sue Roberts, associate editor, contributes to both Canadian Metalworking and Canadian Fabricating & Welding. A metalworking industry veteran, she has contributed to marketing communications efforts and written B2B articles for the metal forming and fabricating, agriculture, food, financial, and regional tourism industries.
Roberts is a Northern Illinois University journalism graduate.
Related Companies
subscribe now
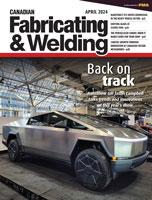
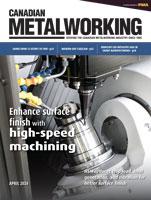
Keep up to date with the latest news, events, and technology for all things metal from our pair of monthly magazines written specifically for Canadian manufacturers!
Start Your Free Subscription- Trending Articles
Automating additive manufacturing
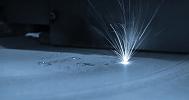
CTMA launches another round of Career-Ready program
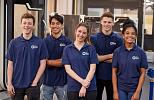
Collet chuck provides accuracy in small diameter cutting
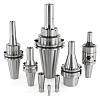
Sandvik Coromant hosts workforce development event empowering young women in manufacturing
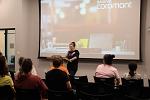
GF Machining Solutions names managing director and head of market region North and Central Americas
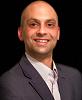
- Industry Events
MME Winnipeg
- April 30, 2024
- Winnipeg, ON Canada
CTMA Economic Uncertainty: Helping You Navigate Windsor Seminar
- April 30, 2024
- Windsor, ON Canada
CTMA Economic Uncertainty: Helping You Navigate Kitchener Seminar
- May 2, 2024
- Kitchener, ON Canada
Automate 2024
- May 6 - 9, 2024
- Chicago, IL
ANCA Open House
- May 7 - 8, 2024
- Wixom, MI