Editor
- FMA
- The Fabricator
- FABTECH
- Canadian Metalworking
Automation acceleration at Inscape
Holland Landing, Ont., manufacturer leans out operations with new punch/laser combo machine
- By Rob Colman
- July 7, 2022
- Article
- Fabricating
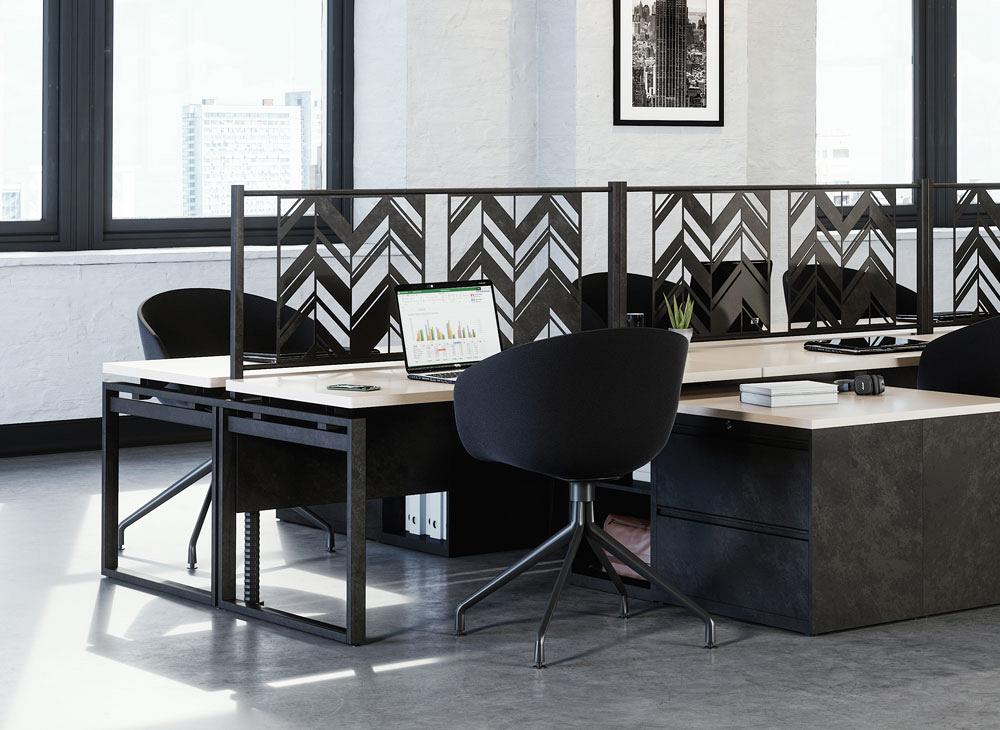
Inscape designs, manufactures, and distributes cubicles, movable walls, filing cabinets, bookcases, and other furniture. It recently invested in a new punch/fiber laser cutting machine. The panels above the work surface in this product are cut on the new machine. Inscape
Capacity often grows in a shop with the incremental addition of faster, more powerful equipment that runs alongside a fabricator’s older workhorses. At some point, however, technological developments are such that a greater leap forward into automated systems is required to make investment worthwhile. This is what Holland Landing, Ont.-based Inscape faced when shopping for its latest cutting requirements.
Just-In-Time Thinking
Inscape has been a fixture in the community since the 1890s, when it was known as Office Specialty. The company designs, manufactures, and distributes cubicles, movable walls, filing cabinets, bookcases, and other furniture. Some of the larger projects it has installed included work for the likes of Penguin Random House, Starwood Capital Group, and WB Games. One of its products, the RockIt bench, was awarded Architectural Record’s Best Products of 2019.
The fact that the company has remained in business as long as it has is a testament to its ability to adapt to industry needs. It now has showrooms in Toronto, New York, Washington, and Chicago, as well as a U.S. headquarters in Jamestown, N.Y.
Dennis Dyke, vice-president, manufacturing and supply chain, has been a part of the company’s growth since 1979. He describes their approach to innovation as being “a fast follower.”
“We see the challenges other companies have with processes and technologies and learn quickly to build a better approach in our organization.”
In many cases, the company was very close on the heels of its most innovative contemporaries. For instance, one of the principal owners of the company in the 1980s visited Japan and toured 30 different factories there.
“He had seen the future of manufacturing and it was cellular just-in-time manufacturing,” said Dyke. “We started implementing that here at a time when only the automotive industry had started to adopt it. We still have one workcell that we designed in 1988 and it works exactly the same way because we have never found a better way to do it since. Most other cells are on their third or fourth generation, but we still use the same methods as we did then. We don’t stock parts; we make everything to customer orders. This has helped us stay successful even as competitors who were carrying large inventories during lean times went out of business.”
CNC Beginnings
The company began investing in CNC machinery in the 1980s, when it bought its first turret punch press.
“My first job on the shop floor was as a coil feed operator,” said Dyke. “The turret presses gave us more flexibility and I began working with those machines.”
By the mid-‘90s, the shop invested in its first combo turret punch press/CO2 laser machine. For many years this machine, in combination with five turret punch presses, served the shop well. But about four years ago, the company knew it was time to invest again.
“Fiber lasers are just so much faster,” said Dyke. “Also, there are a number of people in the shop that have worked there as long as I have, so we knew there would be some natural attrition on the floor as people retired. Because fiber laser technology has been out there a while now, we could see the options available to us very clearly.”
Fiber Power
When it was time to upgrade to a newer, faster alternative to its older CO2-powered laser/punch, Inscape added a two-tower load/unload setup and a fully robotic part picking system to its purchase.
Inscape chose the AMADA EML 2515 AJ punch/fiber laser combination machine to invest in. The fiber engine uses an array of 200-W diodes to generate 3 kW of power, making it three times more energy-efficient than AMADA’s former CO2 model. This allows for faster cut speeds and higher wall-plug efficiency. The fiber laser cutting capabilities can handle endless geometric patterns to accommodate a variety of parts.
The tower system connected to the punch/fiber machine is the AS3015NTK + ULS3015NTK system. This system is composed of two storage towers for material/parts and a part remover.
It is equipped with 8 pallets (3 tons each) for raw material and 8 pallets (3 tons each) for finish product or skeleton. The second tower for finished product can be configured as single or double shelves.
The part remover picks parts from the processed sheet via vacuum suction cups and stacks them on the unload pallet. The part remover also uses unloading clamps to remove processed skeletons and micro-jointed sheets.
“When we started looking at the laser technology available in the market, we quickly came to realize that a combo laser/turret punch press made the most sense for us,” said Dyke. “We work in cold-rolled steel and galvanized, most of which is in the 20- to 22-ga. range. The thickest material we’ve cut, just recently, is 7 ga. Many of the parts we make require round holes or slots in them, and punching those out is far faster than laser cutting them. We also have a number of special features in our parts that we purchased special forming tools for that allow us to more efficiently form them.”
The company invested in an accompanying nitrogen generator from AMADA also, to ensure gas supply consistency and cut quality.
Early Gains
Automation was important for Inscape so that it could run the machine lights-out.
“We are already running more than 1,000 different parts on the EML,” said Dyke. “And we’ve still got more that we’re loading onto it. We run it routinely into a second shift and sometimes through a third. The automation has served us well in that regard.” The rest of the factory runs only one full shift.
Inscape has been affected by supply chain crunches in the past year just as everyone else has, but the punch/fiber laser combo has helped them deal with it.
“There was a specific drawer slide we couldn’t source, so we redesigned a drawer end to use a different slide,” said Dyke. “We also had a supplier that could no longer supply us with name holders – an aluminum extrusion that hangs off a panel on a workstation into which you slide a name plate. We designed a new product to replace this made of metal and painted. We got this into production on the EML quickly and it was actually a cost savings.”
Operator Refocus
The EML has essentially replaced five turret punch presses and a shear. The number of required operators has been reduced from six to one. Again, this has meant attrition through retirement rather than letting people go. But it also has changed the nature of the job for the operator left on the machine.
“Before, this same person was running our other combo machine,” said Dyke. “His role was to load the sheet onto the machine and then remove the finished parts. Now his role is to load up the raw stock into one tower and take the laser-cut parts out of the other tower and move them downstream to other departments. He troubleshoots the machine as necessary and sharpens all of his own tools out of the turret. The machine alerts him when a tool needs to be sharpened based on the number of hits it has produced. We have moved the sharpener to be right by the machine so he can take on that responsibility. With all the manual work he had to do before loading and unloading, he wouldn’t have had time for that work.”
In terms of part sorting, the Inscape team has tried to organize its nesting process so that most if not all parts cut in a certain grouping can be placed in the same skid at once for common distribution downstream.
“This helps us avoid complicated sorting processes,” said Dyke. “The guys on the floor figured out a process that we use to simplify it. Parts are designated into ‘families’ based on the downstream operations we have to perform on them. We arrange nests and skids so that these are grouped together. It means that once they are all completed, the operator can easily remove that skid from the completed parts tower for further processing while the machine continues to cut more parts.”
Efficient Use of Square Footage
Inscape hasn’t removed all of its old equipment yet, but it is close.
“We have just one last form tool that is unique to us that we are working to reconsider,” said Dyke. “Once we’ve done that, everything will be off the turret punch presses. We will likely keep the other combination machine just as a backup; the EML is our main machine, so once we nest our parts and start running, we don’t want to break for a repick or a part that gets damaged at another station. We will also likely adapt the older machine for other uses, such as tapping holes, where that can be of use.”
The company is actually in the process of shrinking its footprint to lease out part of its building.
“With the EML and other efficiencies we have achieved in the past few years, we know for sure that we can free up at least 80,000 sq. ft. while still producing as much product or more.”
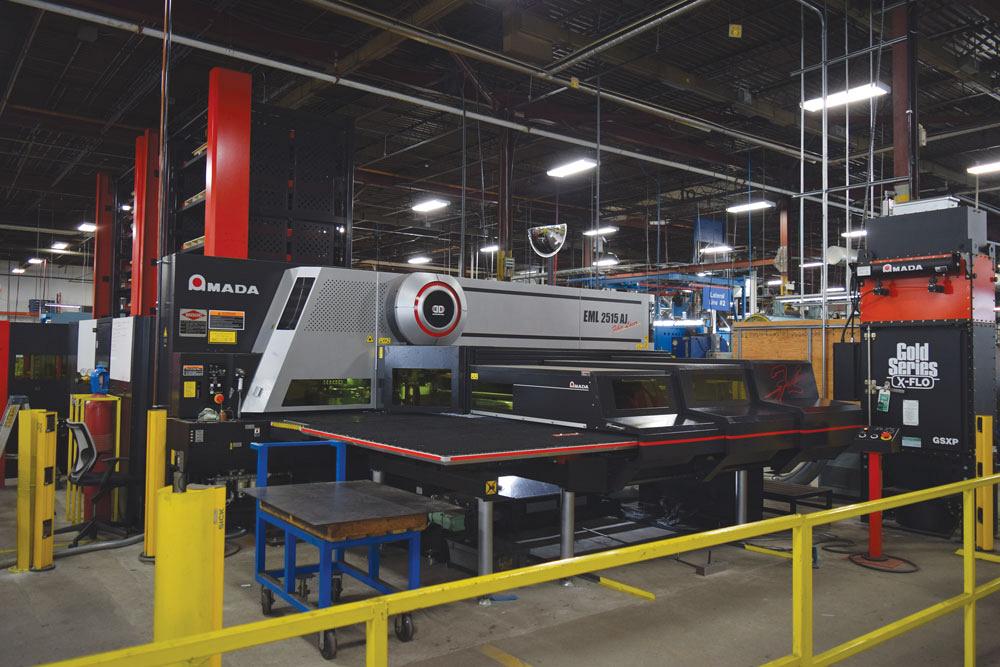
The AMADA EML 2515 AJ punch/fiber laser combination machine has a fibre engine that uses a 200-W diode array to generate 3 kW of power, making it three times more energy-efficient than AMADA’s former CO2 model.
External Savings
Inscape justified the cost of the new combination machine based on three or four uses it planned for the system. But most of those were internal. Now that the machine is in operation, the company is starting to see its benefits in several other ways.
“For instance, we now have a product that will be our first to have all of its parts produced on the EML,” said Dyke. “When the product was originally designed, 67 parts would have come off the turrets and seven would have been produced on our older combo machine. Everything being channelled through the one machine will be much more efficient.”
It is also changing the way in which the shop purchases steel.
“We used to buy a lot of cut-to-size steel – about 600 different-sized blanks,” said Dyke. “We’ve since determined that 500 of those can be cut on the EML without affecting our production.”
A good example of such cut-to-size parts is cubicle tiles – tiles that snap into a cubicle’s frame to create its “wall.” While Inscape works with 67 different sizes of these tiles, only 10 sizes are high-volume items. The remaining 57 can be cut in-house to save time, costs, and inventory space.
“We didn’t anticipate those savings when we purchased the machine, but once you get a machine like that into operation, the opportunities present themselves.”
Now the Inscape team is thinking of ways to design products differently based on what the punch/laser combo is capable of doing, and considering what other tools added downstream might further benefit them.
“We are already starting to look at panel bending, automated press brakes, and automated welding,” he said. “Once you see the benefits of advanced automation, the opportunities for efficiency and growth become very clear.”
Editor Robert Colman can be reached at rcolman@canadianfabweld.com.
Inscape, myinscape.com
AMADA CANADA, www.amada.ca
About the Author
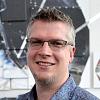
Rob Colman
1154 Warden Avenue
Toronto, M1R 0A1 Canada
905-235-0471
Robert Colman has worked as a writer and editor for more than 25 years, covering the needs of a variety of trades. He has been dedicated to the metalworking industry for the past 13 years, serving as editor for Metalworking Production & Purchasing (MP&P) and, since January 2016, the editor of Canadian Fabricating & Welding. He graduated with a B.A. degree from McGill University and a Master’s degree from UBC.
subscribe now
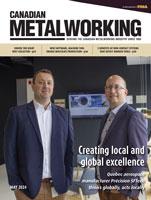
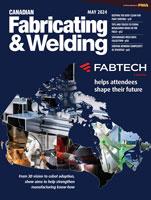
Keep up to date with the latest news, events, and technology for all things metal from our pair of monthly magazines written specifically for Canadian manufacturers!
Start Your Free Subscription- Industry Events
Automate 2024
- May 6 - 9, 2024
- Chicago, IL
ANCA Open House
- May 7 - 8, 2024
- Wixom, MI
17th annual Joint Open House
- May 8 - 9, 2024
- Oakville and Mississauga, ON Canada
MME Saskatoon
- May 28, 2024
- Saskatoon, SK Canada
CME's Health & Safety Symposium for Manufacturers
- May 29, 2024
- Mississauga, ON Canada