- FMA
- The Fabricator
- FABTECH
- Canadian Metalworking
Laser/punch heats up production at KeepRite Refrigeration
Brantford, Ont., shop invests to manage extra capacity flexibly
- May 16, 2017
- Article
- Fabricating
National Refrigeration and Air Conditioning Products Canada Corp. is a North American manufacturer of commercial refrigeration products marketed under the KeepRite Refrigeration brand name. The company’s product line includes specialized food storage and processing equipment; industrial process cooling equipment, including evaporator coils, condensing units, and condensers; heat transfer and recovery; and air-conditioning components.
Located in Brantford, Ont., for nearly 70 years, KeepRite Refrigeration products have been manufactured and distributed to grocery stores, convenience stores, gas stations, restaurants, and commercial facilities from small warehouses to large distribution terminals of over 1 million square feet of cool space. Today the company operates with 200-plus employees and over 150,000 sq. ft. for product design, engineering, manufacturing, sales, and after-market support.
Several years ago the company began its search to update its sheet metal fabrication equipment.
“Back in the early 2000s, we purchased several press brakes and a Finn-Power (now Prima Power) Shear Genius punch/shear combination machine to add capacity,” explained Chris Brohman, plant manager. “The punch/shear provided the flexibility we were looking for and has served us well over the years. By 2015 we were interested in finding another flexible workhorse like the punch/shear to add to our equipment list. We needed the extra capacity because of the company’s steady growth since 2004.
“We were courted by all the machine builders,” continued Brohman. “I was initially nudged into considering a laser by our sister company that was investigating laser machines. Our designers had invented all these new, complex profiles on products that adjusted to market demand ... and the laser began to make sense. However, we did not want to invest in a CO2 laser with the large maintenance and operating costs. We set our sights on a fibre laser machine with the power to blast through copper, aluminum, and stainless steel in the thicknesses we needed. We had a strong relationship with Prima Power as a result of an earlier purchase of the company’s punch/shear and several press brakes. This relationship played a major role in our ultimate purchasing decision in 2016, along with Prima Power’s ability to supply the right machine for us.”
Integrated Laser/Punch
In late 2015 the decision was made to purchase the Prima Power LPef8 laser/punch machine and it was installed the next August. The laser/punch combines servo-electric punching and fibre laser technology in a system aimed at providing flexibility, speed, accuracy, and productivity to fabricate challenging products.
The inherent benefit of integrated punching and laser cutting is high versatility; the company can use the turret punch press where it is easier or faster and the laser where it is most flexible. Depending on the manufacturing task at hand, the manufacturer can always choose the most productive method.
The fibre laser source has low energy consumption and eliminates the need for laser gases.
Very fast reaction times are expected in modern production. The machines need to be flexible and extremely fast for a quick response to production orders, often for very small quantities. That is why a combination machine like this is popular among some manufacturers. This lean manufacturing style reduces cost per part; parts will be made fast, easily, and accurately on one machine by one operator using only one operating and programming system.
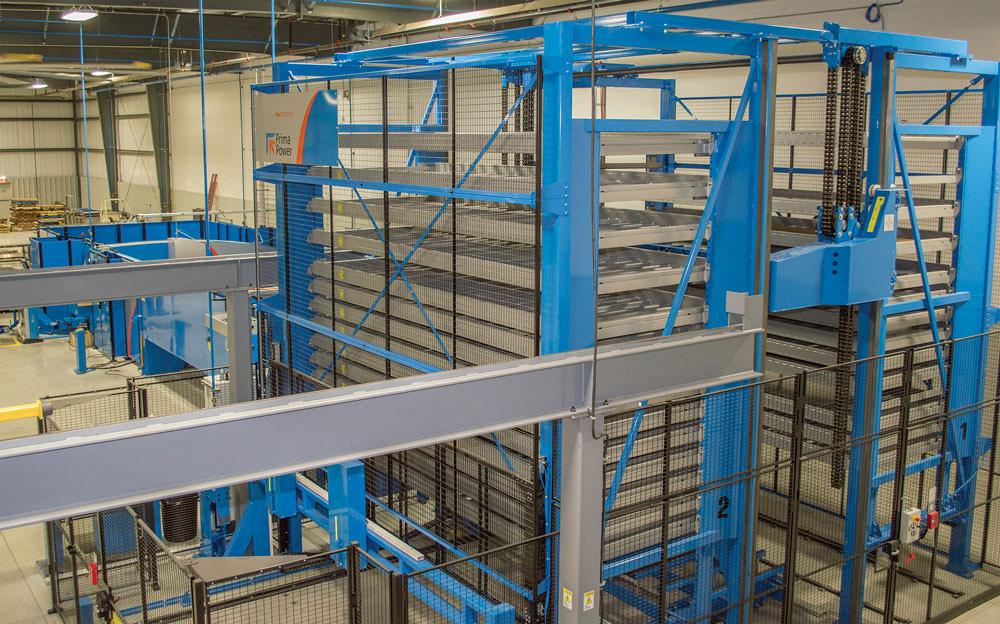
The COMBO FMS handling system has a double tower of 24 stations - 10 stations for finished goods and 14 for raw material storage.
Servo-electric Punching
The system’s turret punch press has automatic tool length measurement, optimization of stroke length, and easy adjustment of the punching stroke. The punching stroke is numerically controlled.
“The fibre laser, the operating system, and the servo-electric punching combine to make the speed of the punch/laser a big plus,” said Brohman. “It is also very quiet, even when we punch 10-gauge material. It can accommodate all materials within reason. While stainless steel is the most difficult to process on the other machines, it is our favorite on the LPef.”
Fibre Laser Cutting
The fibre laser used in the system can be 2-kW, 3-kW, or 4-kW. Cutting speed increases in proportion to power. It has a totally closed cabin design for eye safety and noise reduction.
With the integrated fibre laser, the machine can cut a range of material, including copper and brass. A significant reduction in operating cost is achieved because the laser has few maintenance requirements, no laser gas is needed, and energy consumption is low. Further benefits are:
- No expensive beam manipulation is needed to control beam divergence.
- Cutting head collision protection results in long lens and nozzle life.
- Efficient dust collection.
- Easy integration of a robust protection device around the cutting head.
- Sheet vibration damping when cutting thin material.
- Prevention of scattered radiation.
Automation Is Key
Another key factor in KeepRite Refrigeration’s purchasing decision was automation that the machine builder could provide.
“The competition’s automation was either way too automated or not automated enough,” explained Brohman. “We chose the Combo double tower 24 stations - 10 stations for finished goods and 14 for raw material storage.”
COMBO FMS® is a material system with the COMBO storage as the key module in automating the material flow. It makes different materials available at the working point quickly and practically, and it also serves as intermediate storage for ready components and as a buffer.
The storage system allows processing of components from a variety of materials, which can be changed, as programmed, automatically. The sheets are automatically transferred into machines and cells of the system.
KeepRite Refrigeration chose a portal-type loading and stacking robot (LSR) to be integrated with its laser/punch system. The robot provides a fully automatic process from loading to picking and stacking of parts. Skeletons are unloaded with the unloading device. The operator is free for other tasks while machine productivity and use increase.
The LSR includes an unloading device for raw material pre-centering and skeleton unloading.
“Our laser/punch can run lights-out up to 10 hours per night,” said Brohman. “The robot does all the work between the tower and the laser/punch machine – the sheet unloading, parts cassette loading, and skeleton pullout.”
A Machine With Benefits
“This laser/punch machine gave us the best balance between flexibility and lights-out operation. Punching was paramount for us. And we have so many forms in our products that the forming tools and special tools we could use was another strong selling point. If we run out of punches in the turret, we can always cut the hole. So now we can have one pre-pierced hole and do any size or any shape we need.”
Service was another important factor to KeepRite management. “From the time we initiated the purchase order to the final signoff the installation of the laser/punch was the smoothest project that I was ever involved with,” said Brohman. “As the machine was being set up and the installation crews came in one after another, that was one of the best experiences I ever had with this size project.
“The laser/punch has given us the extra capacity that we needed, increased our flexibility with the laser, and the sheer volume of parts it can process is very impressive,” concluded Brohman. “A job that would take us three day shifts and two night shifts in the past can now be done in two eight-hour day shifts.”
KeepRite Refrigeration, 800-463-9517, http://k-rp.com
Prima Power, 800-344-7143, www.primapower.comsubscribe now
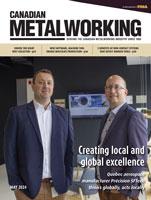
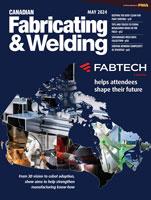
Keep up to date with the latest news, events, and technology for all things metal from our pair of monthly magazines written specifically for Canadian manufacturers!
Start Your Free Subscription- Trending Articles
FMA Annual Meeting: Ingenuity still key with tech innovations
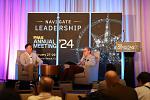
Messer Canada hosts anniversary event
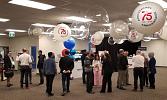
Welding jacket designed for protection, comfort
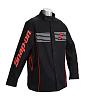
Gang punching press system accommodates different parts quickly
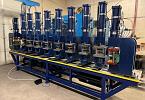
Compact swing chamber shot blast machine features robotic workpiece handling
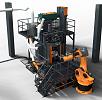
- Industry Events
MME Saskatoon
- May 28, 2024
- Saskatoon, SK Canada
CME's Health & Safety Symposium for Manufacturers
- May 29, 2024
- Mississauga, ON Canada
DiPaolo Machine Tools Open House 2024
- June 4 - 5, 2024
- Mississauga, ON Canada
FABTECH Canada
- June 11 - 13, 2024
- Toronto, ON Canada
Zoller Open House & Technology Days 2024
- June 12 - 13, 2024
- Ann Arbor, MI