Editor
- FMA
- The Fabricator
- FABTECH
- Canadian Metalworking
Managing the talent crunch at Raglan
Trailer and truck box manufacturer invests in machinery to maintain and boost production
- By Rob Colman
- January 16, 2023
- Article
- Fabricating
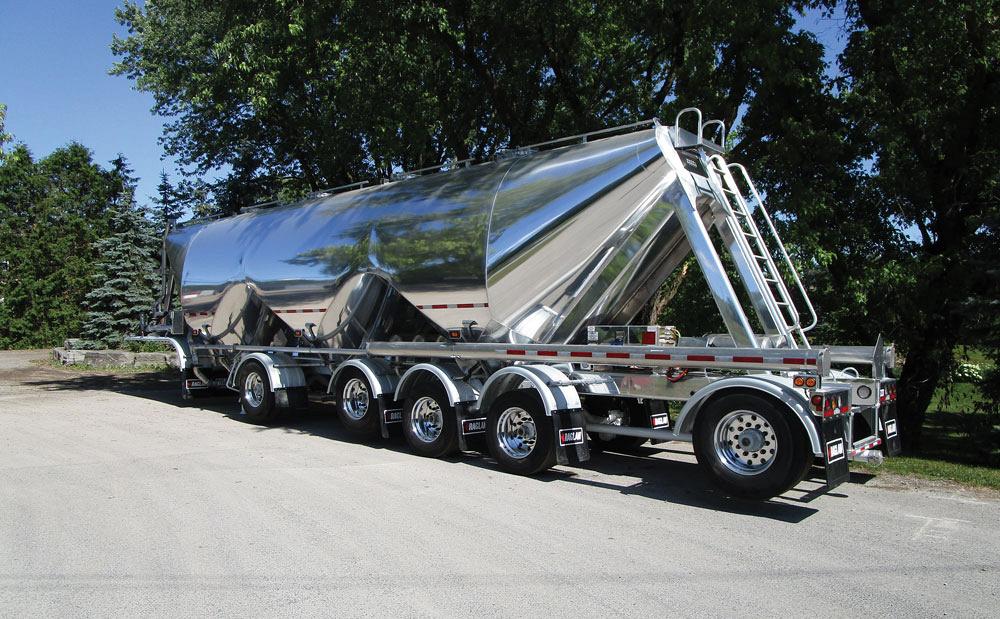
This aluminum dry bulk tank’s body was rolled in one piece, meaning took one seam to weld the body together. Raglan’s investment in new laser and plate rolling technology has made this possible. Image: Raglan Industries
Raglan Industries, Oshawa, Ont., has been in business 63 years now. That longevity has been built on strong management by the Michel family and the ability to adapt to market pressures. Second-generation owner John Michel has seen these changes first-hand.
“In 2000, we had 180 people on our shop floor,” he recalled. “In 2010, through efficiencies, we had that down to about 100 people. In 2022, we have 35.”
Michel said it’s been a challenge to find employees, but through investments in new technologies, the company has been able to maintain the same output as it had in 2019.
“You change your designs, you change your processes, change everything just to accommodate that lack of skilled labour,” he said. “You’re forced to do it and find ways you never dreamed you’d have to.”
Beginnings
Raglan was established in 1959 by John’s father, Bert, as a welding shop primarily to serve the local farming community. All seven of Bert’s boys eventually joined the company. In 1970, Raglan built its first gravel hopper, a bottom-discharge road-spreading trailer. The company had been repairing trucks, so when a local business owner asked if they could build the hopper, it wasn’t a huge departure. In this way, as local family farms started to disappear in the area, Raglan found a new niche to expand upon.
By 1980, Raglan was producing its trademarked U-Body dump trailers, a shape that simplified removal of materials from the truck. Now the company not only does all its own fabrication work, but also has several finishing bays for hydraulics, pneumatics, wiring, washing, and painting.
Beyond its fabrication operations, it also maintains a busy repair bay.
“The repair bay is very busy right now because, with the cost of everything going up, people are keen to repair trailers that they already own,” said Michel. “Some people are fixing trailers that might have been sitting around for eight years. Our repair department requires our skilled employees, and in our fabricating operations we have to ensure that we are as streamlined as possible.”
Lean Processes Revisited
As he struggled to find new employees a number of years ago, Michel streamlined fabricating processes through the use of jigs and fixtures. The shop is designed such that one person is responsible for all the work on a single stage of a project.
“One man fits it up, one person welds it, and another finishes it,” he said. “On the whole, it’s much more efficient to have jobs staged so each person is working alone.”
The jigs and fixtures take a great deal of the measuring work out of the equation, a skill Michel found many were struggling with anyhow.
Even with these changes, however, the talent crunch remained. Michel realized that he had to invest in new machinery that would remove some of the prep work required with plasma-cut parts. He also had to consider how to reduce the number of welds on each assembly to speed throughput.
Laser Efficiencies
To improve the initial cut profile on its materials, Raglan invested in a Durma HD-F 8525 Megacut 8-kW fibre laser from Access Machinery. It has an IPG laser source, a Precitec ProCutter F150 cutting head with automatic nozzle cleaning, and CAD/CAM software with automated nesting. The machine has an 8- by 32 ft. cutting area.
“When using plasma, especially with aluminum, you have to grind the joints to clean the material; otherwise, you get intrusions in the welds,” said Michel. “With the laser you don’t need that secondary cleaning, and cut time is way faster.”
The laser can handle material up to ¾-in. sheet.
“Next, I’m planning on installing a 10-ft. by 40-ft. laser, so I can produce a one-piece frame rail,” said Michel.
The larger the pieces Raglan can produce from a machine, the fewer welds necessary. But those pieces have to be formed.
Plate Roll Preferences
The next key investment for Raglan in its process streamlining was a 26-ft. DAVI plate rolling machine.
“We had a 12-ft. roll that worked fine, but with a smaller machine you’re forced to do sectional production—you are seaming and fitting,” said Michel. “Now we can go longer with no seams, no joints, and therefore less welding. Our short dump bodies are now seamless, as are our stone slinger bodies, of which we make one every four days. It takes a lot of fitting and precision requirements away from the person working on it. With fewer people doing fewer welds, we can shift more product.”
The machine was installed with a number of modifications to suit the work Raglan does.
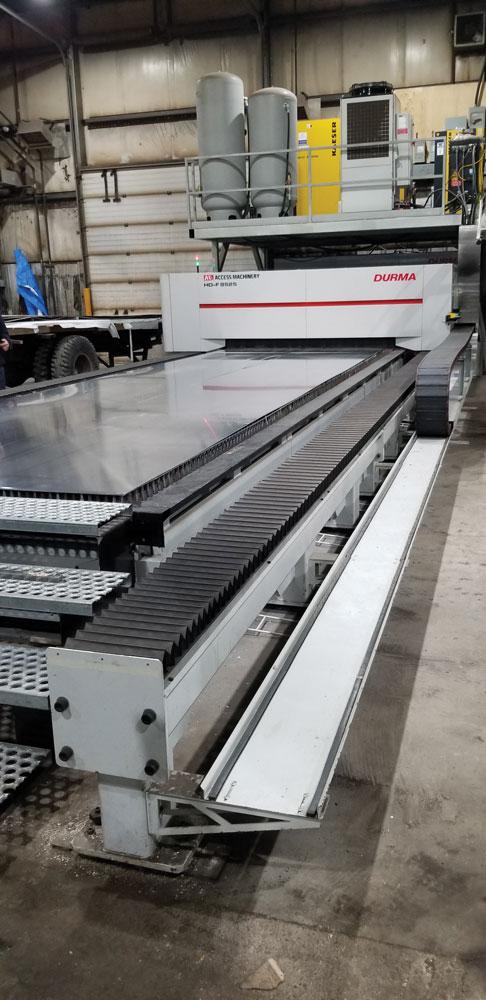
To improve the initial cut profile on its materials, Raglan invested in a Durma HD-F 8525 Megacut 8-kW fibre laser from Access Machinery.
“The corners that Raglan needs for its trailers require small connection radii,” said Steve Bonnay, business development manager (Canada) and special projects, DAVI Inc. “This meant the normal design of the machine would require too big a top roll to hit those radii. To adjust it, we added a top roll beam, which strengthens the top roll and fights deflection forces.”
Bonnay notes that an alternative method for fighting deflection is to use a prestressed machine.
“That extends the roll on both ends by placing hydraulic cylinders on them to fight deflection,” he said. “Because they weren’t forming full shells, that top roll beam didn’t create interference issues. If you were a pipe manufacturer and had to do a full circle on a small diameter, then we’d either have to go with the prestressed design or we’d actually attach that top roll beam to two hydraulic cylinders to allow the beam to rotate out of the way. For Raglan, that wasn’t an issue.”
The second thing DAVI had to add, because it is such a long machine, was technology that would help fight deflection in the other three rolls.
“Underneath the centre roll, we fairly commonly include what we call HDC, hydraulic dynamic crowning,” said Bonnay. “This places one or two cylinders, depending on the size of the machine, right in the middle of the pinch roll, the one directly below the top roll. Hydraulically we can push up or lock it to keep it from coming down, so it performs double duty: it can be used to prevent that pinch roll from deflecting, but if we’re going to do something very light, we can add positive pressure to that pinch roll to adjust the crown and keep the edges of the plates straight. If you put very thin material into a heavy machine, you get more rolling in the centre than the edges because you don’t deflect as much of the crown, and you don’t get that straight seam that everyone is looking for. Having that HDC doesn’t make the range of the roll unlimited, but it increases the window of what you can roll. With this machine, we also had to put HDC on the two side rolls. In 27 years of selling rolls, I think I’ve worked with two machines with HDC on the side rolls. But again, because of what Raglan was looking to do, we either had to make those side rolls much larger so they wouldn’t deflect or put HDC on the side rolls. If we’d make the side rolls 5 or 6 in. bigger, doing large diameters could become problematic because the rolls would sit up higher.”
Michel is pleased with how the new DAVI is working; he only wishes he had invested in an even longer machine.
“A 40-ft. machine would have really changed the game with our tankers,” he said. “But I try to invest in a new machine every year, so that time will come.”
Michel also has invested in a double-up configuration of Baykal press brakes so that he can bend 26-ft. lengths in one setup. This, too, he hopes to expand upon.
Market Shifts
Just a few years ago, Michel’s concept of the future was that the shop would move away from doing so much custom work and produce more standard jobs. Although that is still something of an ideal for the company, market shifts are telling him that right now is not the time.
“The purchase of new equipment in the truck market has dropped somewhat, due to market conditions,” he noted. “However, customization has not. There are always instances where a specific company requires custom details. Between customization and repairs, there is a lot of business right now.”
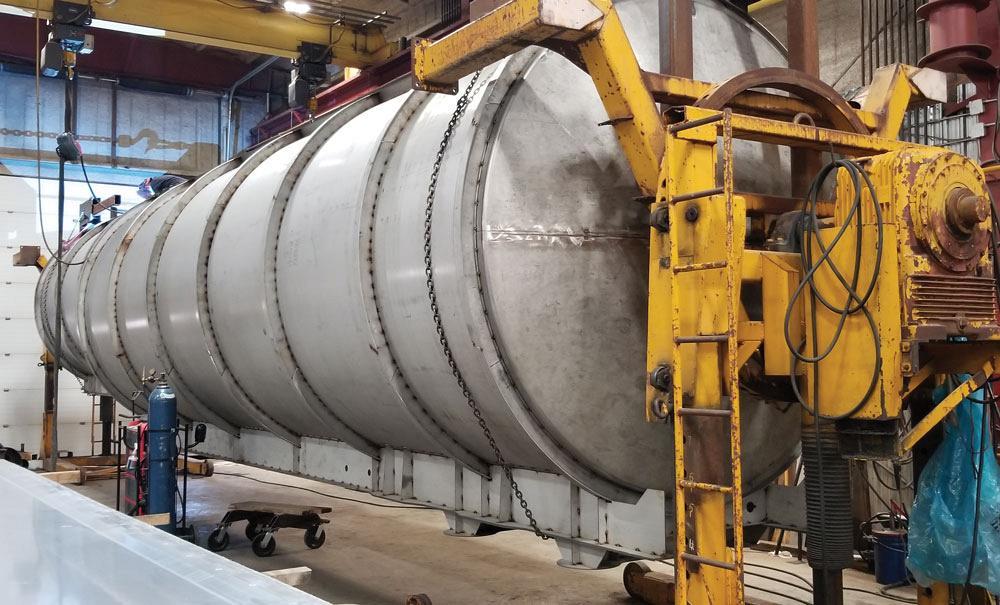
This stainless steel liquid tank went from requiring nine weld seams to just three, thanks to the shop’s new plate roller.
Still, with its reputation as a company that provides quality work at a competitive price, the construction of its standard models is by no means slowing down.
Family Longevity
John Michel is not slowing down, either. While his son Jonathan Michel, who runs the company’s fab shop, and daughter Erin Bowen, who manages finances and administration, are taking on more and more responsibilities, alongside nephews who are working elsewhere in the business, John Michel is still busy guiding the company into the future.
At the same time, he’s pleased to see the fourth generation of family chomping at the bit to start work at the company.
“My grandkids are still too young to work in the shop, but they help outside, cleaning up and doing other chores,” he said. “They are itching to get into the shop.”
By adapting to changing market needs, Michel is ensuring the business keeps on a steady path for the next two generations coming up.
Editor Robert Colman can be reached at rcolman@canadianfabweld.com.
Raglan Industries, raglan.ca
Access Machinery, accessmachinery.ca/
DAVI, www.davi.com
About the Author
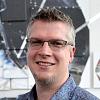
Rob Colman
1154 Warden Avenue
Toronto, M1R 0A1 Canada
905-235-0471
Robert Colman has worked as a writer and editor for more than 25 years, covering the needs of a variety of trades. He has been dedicated to the metalworking industry for the past 13 years, serving as editor for Metalworking Production & Purchasing (MP&P) and, since January 2016, the editor of Canadian Fabricating & Welding. He graduated with a B.A. degree from McGill University and a Master’s degree from UBC.
subscribe now
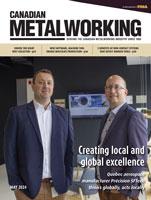
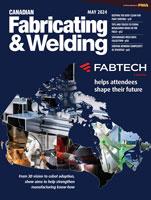
Keep up to date with the latest news, events, and technology for all things metal from our pair of monthly magazines written specifically for Canadian manufacturers!
Start Your Free Subscription- Industry Events
Automate 2024
- May 6 - 9, 2024
- Chicago, IL
ANCA Open House
- May 7 - 8, 2024
- Wixom, MI
17th annual Joint Open House
- May 8 - 9, 2024
- Oakville and Mississauga, ON Canada
MME Saskatoon
- May 28, 2024
- Saskatoon, SK Canada
CME's Health & Safety Symposium for Manufacturers
- May 29, 2024
- Mississauga, ON Canada