Editor
- FMA
- The Fabricator
- FABTECH
- Canadian Metalworking
Marking an electric shift
Columbia Marking Tools preps support for electric vehicle supply chain changes
- By Rob Colman
- September 3, 2021
- Article
- Fabricating
At this year’s Fabricators & Manufacturers Association's virtual Annual meeting, Bernard Swiecki, senior automotive analyst in the Center for Automotive Research’s (CAR’s) industry labour and economics group, gave attendees a snapshot of the automotive industry. The really interesting data in the presentation was the growth in electric vehicle sales. According to Swiecki’s data, EVs made up 5.2 per cent of U.S. vehicle sales in 2020, and it was the only segment to grow in both unit sales and market share. In January 2021, meanwhile, EVs accounted for 7 per cent of U.S. sales, which is a rise of about 33 per cent over January 2020.
The first half of this year was packed with announcements about greater investments by automotive companies and their suppliers on EV technology. For instance, Lincoln recently announced it will debut its first global fully electric vehicle next year, the first step toward electrifying its entire portfolio of vehicles by the end of the decade. By mid-decade, the automaker expects half of its global volume will be zero-emissions vehicles and plans to electrify its portfolio of vehicles by 2030. This is part of the Ford+ plan and Ford Motor Co.’s planned investment of more than $30 billion in electrification by 2025.
Meanwhile, Sweden-based Northvolt announced in June that it will expand its first gigafactory, Northvolt Ett, from an earlier plan of 40 GWh to 60 GWh of annual production capacity to meet the increased demand from key customers, including a $14 billion order from Volkswagen. The factory will commence production later this year.
Columbia Marking Tools Inc., Chesterfield Township, Mich., has reacted to this market shift by establishing a new Advanced Part Marking Division to provide marking tools, processes, machines, and equipment to the electric and autonomous vehicle industry. The team includes two regional managers and three dedicated engineers to assist customers. Owner Michelle Krembel explained that this is a drive to help manufacturers right-size their marking requirements.
“The expense of the components that go into building these vehicles means that if there is an issue in the manufacturing process, you want to be able to identify that,” she explained. “Where is that process failing? We aim to educate our customers on how best to address that. The electric vehicle field is so competitive, you want to make sure you are tracking and tracing parts to precisely identify where things might have gone awry so that QC can better identify and correct the situation.”
Marking Models
Krembel said that one of the issues that the new division hopes to help manage is helping customers understand what marking approach makes most sense for their application.
“Most shops want the latest, greatest technology, but you have to balance that desire with economic conditions, leaning out your manufacturing process, and staying competitive at different levels,” she said. “So as much as a company may want to go out and buy a big laser marker for everything they do, that isn’t going to be the right fit if the shop is simply placing a Julian date code or a part number that doesn’t change. We walk through a company’s process, address the application, look at the company’s economic restraints, and match all that with a variety of approaches.”
Krembel insists that in many situations, the easiest approach makes the most sense.
“In some situations, it may be that you need to determine from which of six CNC machines a particular part originates,” she said. “In that case, you may just want a simple station ID where each part is marked with an A, B, C, D, E, or F, depending which machine it came from, using a pneumatic cylinder. Another method might be to mark parts with a simple weld spot to ID which station it was welded on.”
The key is to look at the cycle time required, the variability of the mark, the traceability requirements, and the depth required. From there, the options become clearer.
Not Always Laser
The challenge that Krembel finds is that a lot of companies automatically leap to the idea of using a laser for their marking needs because of its market visibility and a false perception of requirements.
“A lot of people say, ‘I have to trace my parts to the second,’ which simply isn’t true in most cases,” she said. “Most part tracking is done by station identification or with a ship code. That can be managed using a die standard.”
The other issue is how long the mark has to last.
“The laser marks that most people use are not considered permanent,” she said. “You have to ask yourself, is this something I want my customer to see after 50,000 miles? Then I probably don’t want to use a laser. If you are using it on a tag that’s internal to the dashboard, that’s fine because no one is scrubbing it down and no dirt and grime is gathering in it, but it’s important to consider these environmental impacts.”
One reason that companies like lasers is because they have a very quick cycle time.
“Companies might have six or seven CNC machines and they want parts coming from them all to go through the same marking machine, so that requires a high cycle time,” said Krembel. “However, if you integrate the marking into the individual station, suddenly you don’t have to have that cycle time. Perhaps you go from something like a normal dot peen or scribe over the laser and save yourself lots of money. It’s just getting customers to step back and look at the big picture and not come at it with a pre-conceived idea of what they should be using.”
Novel Approaches
Of course, marking tool companies have unique techniques that they bring to the table.
“In our case, one of those is an adaptation of static part numbers that are commonly used in automotive throughout the world, what they call retainer die sets,” said Krembel. “Basically, they are incorporated as part of the primary metal forming process, so it is very cost effective. The problem is that they aren’t easily changed for something like a Julian date code. So we have developed an in-die numbering tag, which is basically like an old-fashioned odometer in a car that turns, so you don’t have to change the die, you just have to turn a wheel to change the date.”
Another tool developed at Columbia Marking Tool is its patented Square-Dot process.
“The big push in laser traceability is the 2D code,” said Krembel. “The dot peen process is limited because it’s a single carbide pin that makes a checkerboard for the 2D code. You have a conical point putting a single dot in there, and to get a good read on that 2D code you have to build the square perfectly. The best 2D mark is an ink mark because it just colours the squares in the way you want. Our process uses a scribe that actually draws the squares. Because it draws the squares over the conical carbide dot peen, you actually get a very bold imprint.”
Krembel noted that 20 years ago the expression “the customer is always right” is what the industry lived by. Now, it’s better to ask, “Are you sure?”
“The point is that we have to make sure the technology is going to deliver what the customer needs,” she said. “A customer may have a product in mind, but if it doesn’t meet the depth of mark and cycle time requirements, we can’t in good conscience sell them that. I encourage anyone looking for new marking tools to come to the table with an open mind and a clear idea of the necessary outcomes.”
Editor Robert Colman can be reached at rcolman@canadianfabweld.com.
Columbia Marking Tools, columbiamt.com
About the Author
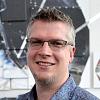
Rob Colman
1154 Warden Avenue
Toronto, M1R 0A1 Canada
905-235-0471
Robert Colman has worked as a writer and editor for more than 25 years, covering the needs of a variety of trades. He has been dedicated to the metalworking industry for the past 13 years, serving as editor for Metalworking Production & Purchasing (MP&P) and, since January 2016, the editor of Canadian Fabricating & Welding. He graduated with a B.A. degree from McGill University and a Master’s degree from UBC.
subscribe now
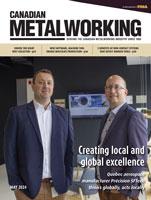
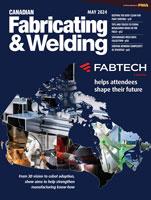
Keep up to date with the latest news, events, and technology for all things metal from our pair of monthly magazines written specifically for Canadian manufacturers!
Start Your Free Subscription- Industry Events
Automate 2024
- May 6 - 9, 2024
- Chicago, IL
ANCA Open House
- May 7 - 8, 2024
- Wixom, MI
17th annual Joint Open House
- May 8 - 9, 2024
- Oakville and Mississauga, ON Canada
MME Saskatoon
- May 28, 2024
- Saskatoon, SK Canada
CME's Health & Safety Symposium for Manufacturers
- May 29, 2024
- Mississauga, ON Canada