Editor
- FMA
- The Fabricator
- FABTECH
- Canadian Metalworking
Planting the seeds for greater efficiency at Green Theory
Vancouver manufacturer takes production to a new level with laser, brake innovations
- By Rob Colman
- December 16, 2021
- Article
- Fabricating
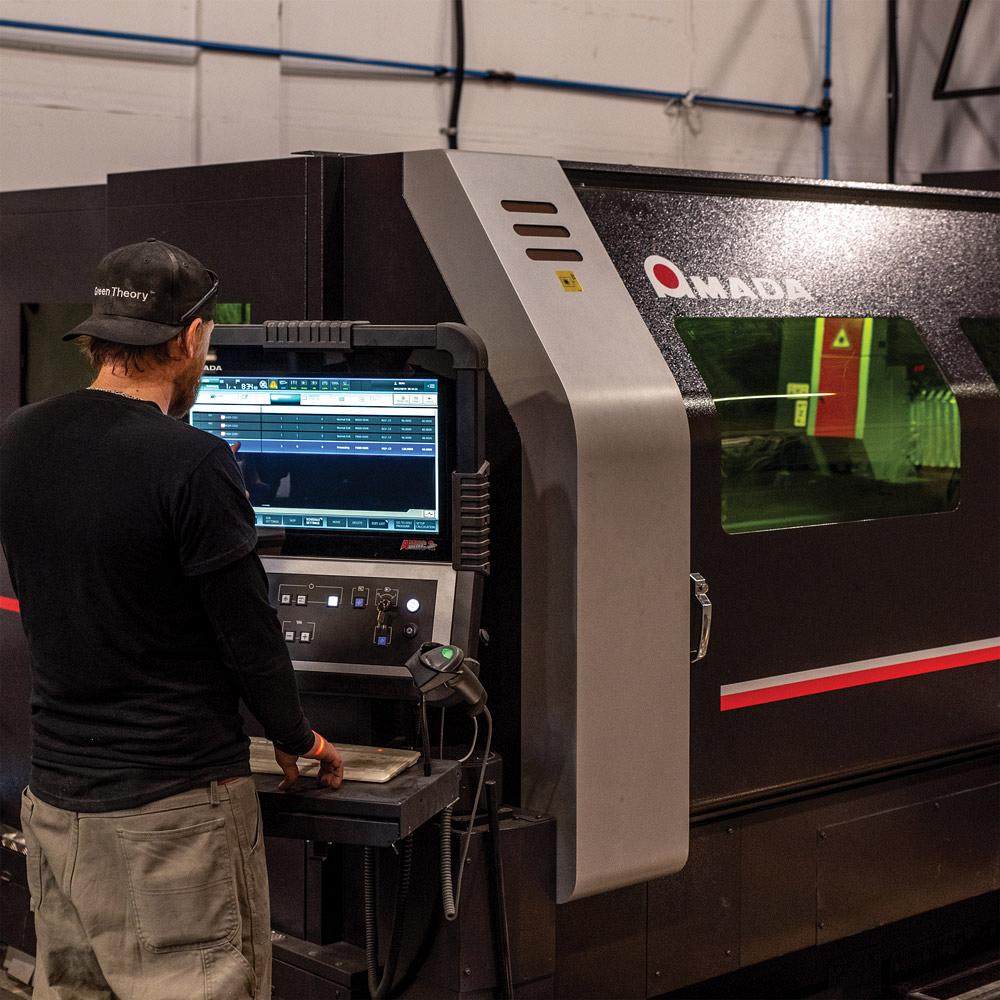
When Green Theory realized it would require a fibre laser to keep up with its cutting requirements, it purchased an Amada Ventis 3015 AJ fibre laser with an accompanying six-shelf tower. Images: Green Theory.
Choosing to introduce any form of advanced fabricating equipment to a shop can have a natural cascade effect – once your cutting process speeds up exponentially, your bending has to keep up. Higher throughput in cutting and forming ultimately means more demand for welding talent and efficiency.
Vancouver-based architectural planter designer and fabricator Green Theory Design has witnessed this first-hand with the introduction of an advanced laser and press brake at its facility. When the company opened a new facility in Tillsonburg, Ont., this year, not only did it replicate its laser and press brake purchases, management started considering what else would be necessary to increase throughput elsewhere in the shop. All of this is helping it to serve its many and varied customers across Canada and the U.S. better.
Niche Needs
Green Theory founder/managing partner Joel Franske was the owner and operator of autobody shops in the Vancouver area 12 years ago when a customer asked if he could paint a couple outdoor planters so that they would match the colour and metallic sheen of his Porsche.
“They were just fiberglass planters, and we charged a price that made it worth our while to do the job of making them look like metal,” Franske said. “The customer absolutely loved it. The same contact led to other jobs, including doing a similar paint job for a boutique hotel. Meanwhile, I was asking, ‘Why isn’t anyone making these out of metal?’”
Franske started playing around with designs and gradually became a supplier of outdoor planters for several restaurant chains. At that point it was still a side gig, though. It wasn’t until about six years ago that it became a full-time business under the name Green Theory.
“We farmed all the work out to other shops at the beginning,” said Franske. “When we started, we had a 4,000-sq.-ft. shop and subbed everything out. Essentially, we were acting as a metal fab contractor. Within a year we were working with three metal shops and three powder coating facilities. But it got to the point where we would promise a delivery to a customer, but we couldn’t really guarantee delivery because we didn’t have control of the workflow.”
At that point the company took on a 17,000-sq.-ft. facility where it could develop its own fabricating capabilities.
“I thought we’d have a factory and a hockey rink, the space was so big,” joked Franske. “But within a year it was full.”
Like a lot of shop owners starting out, Franske bought used machinery to get started with - a shear and a press brake.
“We sheared, hand-notched, and broke everything,” he said. “There was no CNC equipment. I had a background in autobody work, so I understood the welding side of the business, but the fabricating process was new to me.”
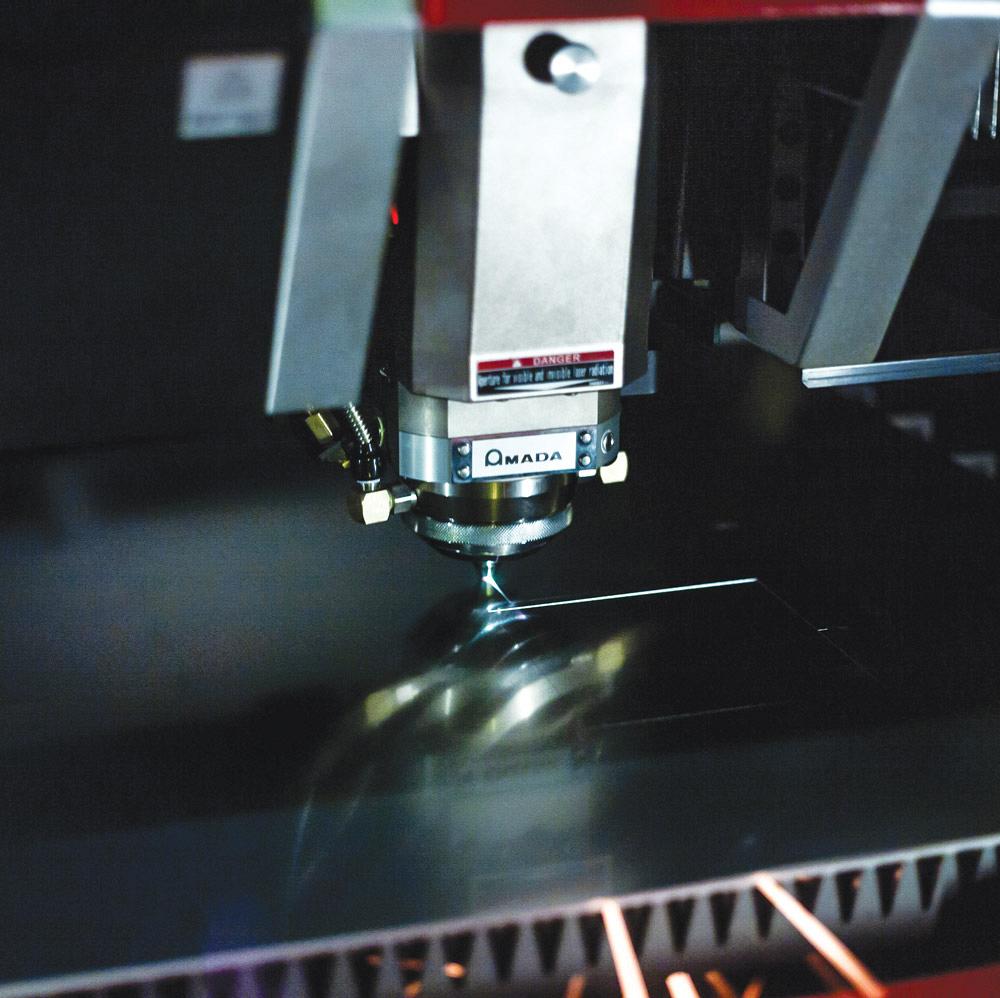
The Ventis uses Amada’s locus beam control to achieve infinite locus patterns. What this means is that the beam shape can be adjusted rapidly to optimize the cutting parameters for whichever material and thickness is on the machine.
Building Capacity
Green Theory is very particular about the type of materials it uses; marine-grade 5052 aluminum in thicknesses between 1/8 and ¼ in. is its go-to.
“People try to make planters with mild steel, but even when they are primed and powder-coated, once an installer moves that planter an eighth of an inch, it gets scratched and will start the rusting process,” said Franske. “In Vancouver, if you see planters made of mild steel, within six months you’ll see them rusting out at their bases. We refuse to do jobs in mild steel.”
The other benefit of aluminum is that it doesn’t heat up in the sun the same way mild steel does.
“You have to consider that you’re working with soil and live plants,” said Franske. “You can’t have those overheating.”
With the majority of the shop’s work being made in aluminum, Franske soon was considering cost-effective ways to upgrade their cutting processes. Planters may look like simple boxes, but as Franske explained, there’s much more to it.
“We have developed our own gusset systems and bracing to ensure that the products remain solid and reliable,” he said. “We have a team of five full-time engineers to handle these designs. They consider the load that the planters will include and design accordingly. There are many little tricks the team comes up with to keep our quality high and customers satisfied – things like hidden reinforcements built in under the lip of planters so the top doesn’t split. It’s attention to detail that our customers appreciate.”
Franske’s first CNC cutting purchase was a MultiCam Apex3R router for cutting aluminum.
“We had that for 19 months and ran it non-stop,” said Franske.
However, soon the company was getting more requests for planters in weathered steel, which can’t be cut on a router. In response, the shop purchased a plasma table.
“We had the plasma table in for about four weeks when we realized that we needed to upgrade to a laser for all of our cutting needs,” said Franske. “In that short time, our business had grown sufficiently that to keep up we would have had to buy several routers to manage the workflow.”
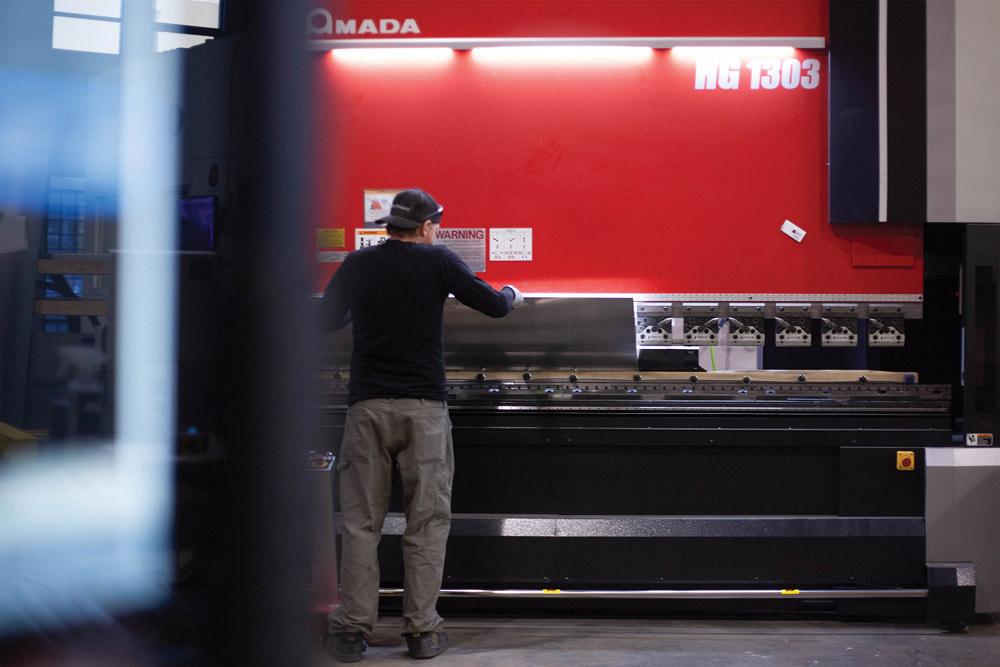
The other investment was the concurrent purchase of an Amada HG1303 130-ton press brake equipped with bend indicator technology that ensures high-speed and high-precision bending, and a sliding floor pedal that simplifies multi-stage bending along the length of the brake.
Automation Augmentation
Green Theory purchased an Amada Ventis 3015 AJ fiber laser with an accompanying six-shelf tower.
“We originally were going to run it without a tower, but once we realized how quickly it processed the sheet, we knew that would be too labour-intensive,” said Franske.
The Ventis uses Amada’s locus beam control to achieve infinite locus patterns. What this means is that the beam shape can be adjusted rapidly to optimize the cutting parameters for whichever material and thickness is on the machine. It is also equipped with a high-brightness fiber laser oscillator to maintain optimal quality of the high-energy density laser beam. These two technologies are designed to improve both quality and cutting speed.
The difference moving from a router and plasma table to a laser was, of course, extreme.
“On the router we could maybe cut 30 sheets a day,” said Franske. “Now, with no intervention, we can process between 100 and 200 sheets. Mostly our work involves profiling, so the laser rips through it very fast at any thickness. It changed the game for us in terms of accuracy and speed.”
The other big change was the concurrent purchase of an Amada HG1303 130-ton press brake equipped with bend indicator technology that ensures high-speed and high-precision bending, and a sliding floor pedal that simplifies multi-stage bending along the length of the brake. It can handle bend lengths from 55 to 169.3 in. and is equipped with the company’s latest control system.
“We had purchased another CNC-equipped press brake, but it never gave us the accuracy we were looking for,” said Franske. “All that has changed with this brake.”
Design and Weld Adaptation
What Franske sees with the addition of this new equipment is the ability to adapt designs to suit the precision that is now possible.
“We can now cut out trellis panels and custom signage easily, for one thing,” he said. “I can see it changing the way we design parts in the future, certainly. We are getting some advanced training from Amada soon to learn about tips and tricks for getting the most out of both the laser and the press brake. Sometimes you don’t know what you don’t know. There may be some techniques that could make immediate changes to how we do things. Figuring out how to do jobs better is how we’ve grown as a company.”
But the welding department is where the most immediate impact has been made beyond the cutting and forming department.
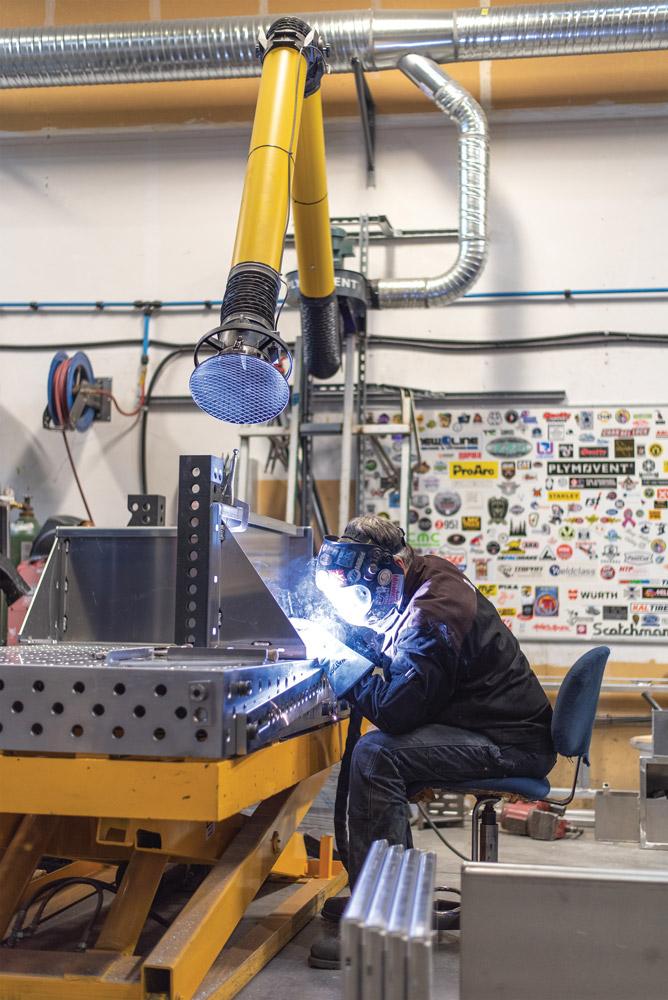
The welding department is where the most immediate impact has been felt because of the fit-up welders can now get on parts, thanks to the precise cutting and bending on the Amada machines. Every welding booth is also equipped with a table that can be adjusted so that employees can do their work in an ergonomically safe way.
“Our output probably doubled just because of the fit-up our welders can now get on parts,” Franske said. “It’s also making us reconsider the welding machines we have on hand. You think you’ll never need more power than you have, but our welders have gone from welding five to 10 boxes a day to as many as 30. They need to have the duty cycle to handle that, so we’re looking to upgrade a lot of our welding equipment.”
CNC Sophistication Grows
The laser and brake purchases have opened the floodgates to more investments at Green Theory. For instance, both of the company’s facilities just took delivery of a Faccin 4HEL 4-roll plate bending machine equipped with a CNC top support that guides the material so that the machine can be run by one person. Again, these machines replace less sophisticated rolling technology that was in the Vancouver shop.
“We do lots of modular designs that require large, rolled sections,” said Franske. “We might be making a 90-in.-diameter cylinder for someone in three sections. This new machine allows us to do that very accurately while also opening up the ability to do other jobs like creating benches using custom radiuses. We also weren’t able to do a tapered cylinder with our old equipment. This new machine opens up opportunities for whole new product lines.”
Tillsonburg Benefits
Green Theory began looking at expansion early this year.
“We were going to expand in Vancouver, but between the price of rent in the area and the fact that we have a lot of business in New York and other points east, we thought it made sense to at least consider a second location,” said Franske.
Tillsonburg ended up ticking most of the boxes Green Theory was looking for in a location: good access to the 401 highway, a building that was the size the company needed, and a supportive community willing to work with them to make the expansion happen.
When they took possession of the building, the team gutted it, replacing the roof and pretty much everything inside. Amada had a laser and tower system already on the water when Green Theory called to make that purchase, so they rerouted it to ensure it arrived at the Tillsonburg location as soon as possible.
“Our timing was fortuitous,” said Franske. “Also, my right-hand man here in Vancouver and our fifth hire, Jaimy Panagiotidis, agreed to run our Ontario facility. If he hadn’t been willing to make that move, we wouldn’t have gone ahead with it.”
The grand opening of the facility took place Sept. 23.
The new location has opened equipped with all state-of-the-art equipment, but Franske knows that the only constant is change.
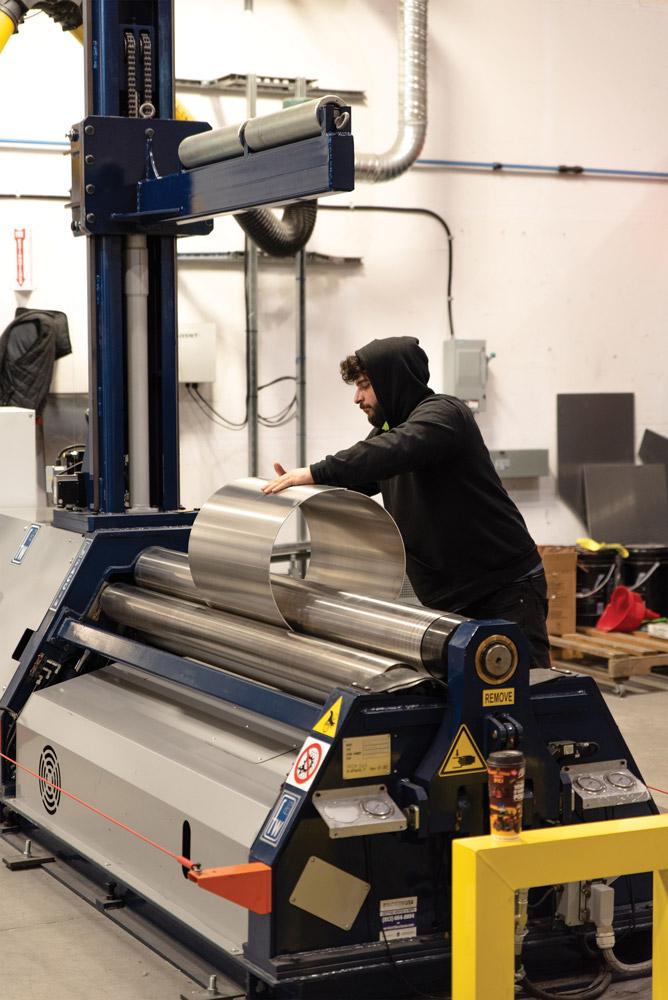
The laser and brake purchases have opened the floodgates to more investments at Green Theory, like a Faccin 4HEL 4-roll plate bending machine equipped with a CNC top support.
“We were down at FABTECH in Chicago and the RAPID + TCT show next door and saw a number of technologies that may take us that next step on our journey,” he said. “It’s really all about thinking how we can automate what’s next.”
Editor Robert Colman can be reached at rcolman@canadianfabweld.com.
Green Theory Design, greentheorydesign.com
Amada, www.amada.com
Faccin, www.faccin.com
MultiCam, www.multicam.com
Note: An image depicting a project that Green Theory worked on, a large rooftop deck in Brooklyn, N.Y., has been removed from this article due to infringement.
About the Author
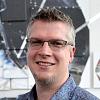
Rob Colman
1154 Warden Avenue
Toronto, M1R 0A1 Canada
905-235-0471
Robert Colman has worked as a writer and editor for more than 25 years, covering the needs of a variety of trades. He has been dedicated to the metalworking industry for the past 13 years, serving as editor for Metalworking Production & Purchasing (MP&P) and, since January 2016, the editor of Canadian Fabricating & Welding. He graduated with a B.A. degree from McGill University and a Master’s degree from UBC.
Related Companies
subscribe now
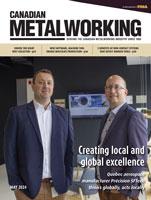
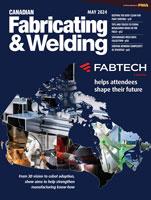
Keep up to date with the latest news, events, and technology for all things metal from our pair of monthly magazines written specifically for Canadian manufacturers!
Start Your Free Subscription- Industry Events
Automate 2024
- May 6 - 9, 2024
- Chicago, IL
ANCA Open House
- May 7 - 8, 2024
- Wixom, MI
17th annual Joint Open House
- May 8 - 9, 2024
- Oakville and Mississauga, ON Canada
MME Saskatoon
- May 28, 2024
- Saskatoon, SK Canada
CME's Health & Safety Symposium for Manufacturers
- May 29, 2024
- Mississauga, ON Canada