- FMA
- The Fabricator
- FABTECH
- Canadian Metalworking
Precise pipe production
Laser systems simplify cutting, drilling and marking pipes and tubes.
- By Nestor Gula
- September 16, 2014
- Article
- Fabricating
Assembling tubes and pipes has always been a tricky proposition. The cuts and angles have to be precise, otherwise the structure is compromised. Back in the day, this work was performed by skilled craftspeople but was labour intensive and occasionally inaccurate.
Modern CNC machines revolutionized the cutting process and new laser systems have added greater precision, speed and convenience. The laser tube cutting systems can combine several processes. “It gives you the opportunity of cutting holes without drilling.
It is more accurate because it is CNC based,” said Dru Schwartz, Laser Technical Center Manager with Amada. What would take hours for a skilled craftsperson to create, can now be done in minutes with flawless repeatability.
The main advantage of laser cutting tubes is the simplicity of the cutting without the need for hard tooling, according to Frank Arteaga, Head of Product Marketing for Bystronic Inc. “Any profile that can be designed in the flat can be cut and wrapped around the perimeter of the tube. Macro programming systems include the ability to create transition cuts, which allow tube-to-tube mating for structural or flow applications.”
When cutting with a laser, the ends can be cut off at any angle that you want. Schwartz also added that there is an ease of use when using a laser system; you can put some location tabs if you have multiple tubes to simplify the lineup that you are welding.
The ability to reduce subsequent manufacturing steps is one area where the technology supports the cost of investment. “By laser cutting profiles, a fabricator not only simplifies the welding fixture design process but also the welding process itself,” said Stefan Fickenscher, Product Manager TruLaser Product Group at TRUMPF North America.
“In addition, the superior edge quality produced by the laser frequently eliminates time-consuming post-processing steps compared to conventional technologies.”
As manufacturers demand streamlined production, more cut features are added to a tube or pipe part design. Laser cutting allows for features like slots of cuts spanning both sides of the tube, which can be difficult with other methods. Not only that, but a laser can cut these features with speed, usually up to 10 times faster than other methods, according to Mark Mercurio, Applications Manager at Mazak Optonics Corporation. “In addition to faster process, many of our customers say that the greatest benefit of the tube laser is in assembly. Laser-cut parts are typically more accurate and more repeatable than any other process. So assembly, bolting, welding or other fixturing processes are much easier because the laser cut part fits better and are always the same. Also, with Mazak’s self-centring chuck design, structural materials like angle iron, C-channel and I-beam can very easily be loaded into the machine and processed, without requiring a setup change.”
This technology is not only suitable for precise manufacturing of high-end products. As we are in the midst of barbecue season, take a look at a humble gas grill. Mine has several through holes either punched or drilled in the square tubing. The tubes are connected by cross-members that, on closer inspection, are quite sloppily hand welded. Besides the bending of the square tube, there must have been at least four processes performed after the tube had been cut.
All of these processes could have been performed by a laser tube cutter in the time it took to cut the pipe and transfer it to the first processing station. “Whenever tubes or profiles are used, the tube laser is a cost effective and fast way to process parts,” said Fickenscher.
Many industries, big and small rely on tubing for structural applications. “Construction, playground, oil, and steel suppliers are adding value to tubes they are selling,” said Mercurio. “Exercise equipment, agriculture, and transportation are also industries that consume large amounts of tubing. We also see these types of laser in very specialized racing and military applications.
The possibilities for using a tube laser are endless. Many products that you see made in fabrication shops feature many sheet metal panels. Most of these sheet metal panels are covering tubes that have made the structure of the assembled component.”
Smaller shops will see benefits to converting to a tube laser cutting system due to the machine’s flexibility, speed and accuracy. “A lot of job shops that make frames or product displays, where they are building a custom display and are using angle iron or square or rectangular tubing, [a tube laser system] makes it very easy to program up the parts needed, cut them, put them together and then weld them,” said Schwartz.
The laser tube and pipe systems can be processed with either CO2 or fibre laser technologies. Using CO2 or fibre for metal applications makes little difference unless it is copper or brass. These metals cut much better with a fibre laser, according to Artega. Both systems are available in the market but CO2 technology systems are a more popular sell.
“The big advantage is the accessibility of the system most customers really appreciate,” explains Fickenscher. “This open concept can only be realized with a CO2 laser, as a fibre system has to be completely closed for safety reasons. Another topic is the maximum achievable cut speed. When you compare a tube laser to a flatbed machine the lengths of the cuts are relatively short. Therefore, the laser cannot, in most cases, reach the max possible cut speed even if the laser source would be capable of going faster over a longer distance. This considered, the speed advantages of a fibre system, as compared to a CO2, cannot be utilized in the way they can on a flatbed machine.”
Schwartz said that the Amada systems use CO2 as their laser source. “The CO2 lends itself to a wider range of materials with better edge quality than fibre currently. The advantage of fibre is speed and what you are cutting is not dependent on speed. You are not trying to cut 1,800 inches per minute.”
Typically, the accuracy of a laser is within .002 inch for cut profiles, but Artega stressed that with tubing you have to also consider the influence of the tube itself and how accurate it is over its length. Precision in pipe and tube cutting largely depends on how precise the tube is made. “It is a difficult thing with tubing because it is so all over the place,” said Schwartz. When a tube is measured it can be off only a millimetre, but this makes a big difference. “It is a difficult thing with accuracy because you are dealing with tubing that is inaccurate to start with.”
[gallery type="slideshow" link="none" ids="105655,105656"]
Depending on the system, pipes up to 16 inches in diameter can be cut. Angle iron, square and rectangular tube, c-channels can also be cut on these machines. “Lasers can cut up to one inch thick,” said Mercurio.
“Mazak’s tube lasers can cut from one half inch diameter all the way up to 16 inch diameter tubes. These machines can carry very heavy weights so heavy wall tube that is typically difficult and dangerous to do in other methods of fabrication are actually quite easy on a tube laser.”
These tube and pipe laser cutting systems tend to be dedicated machines and can’t be used for cutting flat stock. However, systems can now combine both flat sheet and tube cutting in one unit. “Some flatbed machines can be equipped with a rotary axis and can therefore be used for sheet metal and tube cutting,” said Fickenscher. “The fully automated systems are pure tube and profile cutting systems.”
To get the full advantage of the laser system, the system needs to be designed for processing tubes. “A real rotary axis requires that you have a CNC controlled tube axis and a chuck that can be accurately positioned and controlled during cutting,” said Arteaga who explained that the design of the machine is also critical for accessing the tube. Typically, a quality machine will provide good access to the tube for loading and unloading.
While some lasers have chucks associated with them and are capable of producing some parts, processing tubes with flat lasers can be difficult with these chucks.
“The operator needs to think about fixturing again. Tubes are not normally straight. They typically have some bow to them and square tubes are not always square,” said Mercurio. “Without proper fixturing, the raw material will affect the outcome of the part. On a machine such as this, it is difficult to accurately place a hole on a tube location... Typically, flat machines are limited to eight-12 feet bed sizes. Indexing tubes on 2D can be difficult and presents accuracy challenges. Also, tube stock normally comes in lengths longer than the standard 2D bed sizes, which means that tubing may have to be cut into smaller sizes before processing on a 2D machine. On a tube laser, the raw material is held very accurately on the centre line of the machine with up to four chucks.
This ensures that the machine knows the exact location of the raw material. In addition we always cut very close to one of the chucks. This ensures accuracy because we are cutting very close to the clamp.”
The cost effectiveness of a tube and pipe laser system is found in the speed of producing parts without the requirements for hard tooling. “Hard tooling is specific to the tube and shape that you are cutting. The laser adapts to the shape and tube based on the program,” said Arteaga. You have one process if your tubes have holes or cut-outs.
“If you are doing it in a conventional method, first you have to take the tube to a saw and cut, and then to a drill press or a milling machine and put it in and mill the part or drill the part where the holes have to be,” said Schwartz. “On a laser it is one process.”
Time and money are saved by eliminating secondary processes and the cost advantage is significant even taken into consideration the capital investment. “As stated earlier, you will be cutting a faster, more accurate and repeatable part,” said Mercurio. “This will all be done in one set up and without any fixturing. It will also benefit downstream in assembly to have a more accurate, repeatable part.”
About the Author
subscribe now
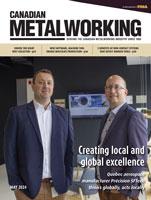
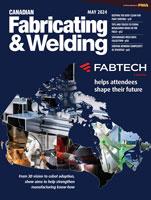
Keep up to date with the latest news, events, and technology for all things metal from our pair of monthly magazines written specifically for Canadian manufacturers!
Start Your Free Subscription- Industry Events
Automate 2024
- May 6 - 9, 2024
- Chicago, IL
ANCA Open House
- May 7 - 8, 2024
- Wixom, MI
17th annual Joint Open House
- May 8 - 9, 2024
- Oakville and Mississauga, ON Canada
MME Saskatoon
- May 28, 2024
- Saskatoon, SK Canada
CME's Health & Safety Symposium for Manufacturers
- May 29, 2024
- Mississauga, ON Canada