- FMA
- The Fabricator
- FABTECH
- Canadian Metalworking
Punching out profits
Various punching strategies can bring success to your business.
- By Nestor Gula
- March 23, 2015
- Article
- Fabricating
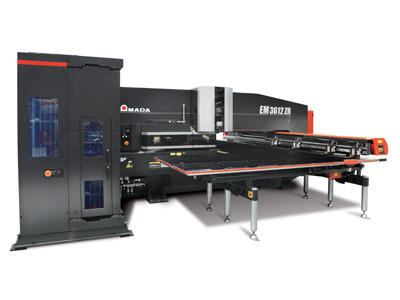
The Amada EM 3612 ZRT offers features like punching drive with energy recovery capabilities, dual AC servo drives, and a high-speed automatic tool changer. WWW.AMADA.CA
While new technologies are regularly introduced in order to speed up manufacturing processes, making them simpler and more productive, punching remains the most efficient and least expensive method for putting holes into sheet metal.
But making simple holes in sheet metal parts is only one of the processes modern punching machines can perform, as the capabilities of automated systems begin to integrate multiple applications to increase the functionality of these tools.
“With the latest technologies, punch machines can complete far more operations on the machine, eliminating second handling of parts,” says Dan Caprio, punching sales manager for LVD Strippit Inc, who explains that these operations include formings, louvers, knockouts, tapping, shear cut edges, deburred edges, bending flanges up to one-inch high and
much more.
Many punches
To add flexibility many high-end automated machines switch their dies to apply more than one procedure, be it punching a hole, making a louver or bending the sheet metal. These machines can, in most instances, replace some stamping machines. “Stamping presses use very expensive and often complicated dies to stamp out a part in one cycle of the press, or in the case of a progressive die, perhaps several cycles of the ram. Once in operation, a stamping press basically makes a complete part with every cycle of the ram,” explains Timothy Brady, punching and combi product manager for Amada America, Inc. Stamping presses can make dozens or even hundreds of parts per minute. Yet, tooling can be very expensive due to the complexity of the design and can take some time to build. Brady says that tooling can range from as low as $10,000 to upwards of $100,000. What is more, the tooling requires a fairly high degree of skill to set up in the press. “On the other hand, a turret punch press uses a multitude of standard tools [in the turret] which are rapidly selected and used to ‘nibble’ complete parts out of a large sheet.” Turret punch presses range in terms of how long they take to produce a part, anywhere from several seconds to several minutes per part.
The turret punch press offers several advantages, but one of its greatest features is its versatility. Brady explains that it is its ability to make an unlimited number of different parts using the same set of tools that sets the turret punch press apart. What is more, the press offers the ability for quick and easy changing of tools using relatively unskilled operators.
Modern CAD/CAM systems can allow rapid programming of parts making it possible to design, program, and produce parts in a very short time. “[It can be as quick as] same day or same hour,” says Brady. “Design updates or part rev changes are not a problem, and the ability to economically make small quantities of parts to meet ‘just-in-time’ demands are the forte of the turret punch press.”
The tool storage capacity in a turret-style punching machine gives it great flexibility. “Most turret tools do not require specialized measurements and data entry by the operator,” says LVD’s Caprio. “Tools for several different jobs remain in the turret for reduced set up for job changeover. Very rugged, mechanically simple designs are possible since tooling remains held and fully guided within the turrets.”
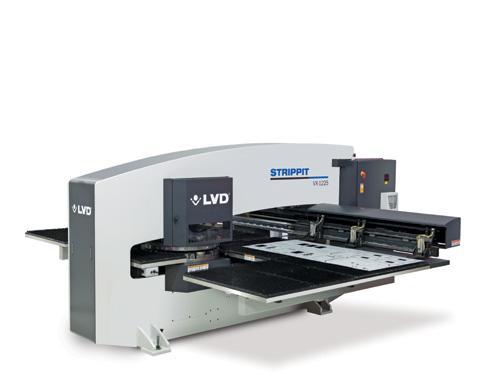
LVD’s VX-Series combines a 20 metric ton hydraulic ram with a large 48-station turret. This system comes in two models, VX-Series 1225 and VX-Series 1525. WWW.LVDGROUP.COM
Although turret punches are one way to have multiple punching tools on hand, not all manufacturers chose this system to bring many tools into play. “TRUMPF offers punching machines with a single head punch technology system which allows for auto tool rotation of all tools, less wearable components, faster tooling set up times, and tooling rail changeover times in less than three minutes,” says Mike Kroll, TruPunch product manager for TRUMPF. He explains that this equates to an average machine uptime (the time the machine is actually punching) of 70 per cent, compared to 35 per cent uptime seen in the latest turret machines offered.
The tools held in these systems can be standard or customized as the application calls for. The amount of tools held varies by manufacturer giving virtually unlimited capabilities to these punching systems.
Punching Plus
A relatively new aspect in the manufacturing world is the combination of a punching system with a laser cutting machine. “Combining a laser with a turret creates the ultimate fabricating machine with the ability economically punch and form parts while having the lasers ability to cut unlimited shapes with excellent edge quality,” says Brady. Adding a punch machine to a laser there can give a manufacturer several benefits.
Space limitation is just one example of why a combination system would beneficial. Having limited space, having a separate punch and laser machine might not be possible. “This [is when a] combination [system] will work well,” says Kroll. He explains, “the part geometry can allow for internal punched holes and form, but the outside edge may have contours not suitable for punching, or laser cut quality of the edge is needed. If automation is being used, part separation and sorting can save hours of sorting time with a combination machine.”
However, these benefits come at a price. According to Brady, adding laser capabilities to a turret can nearly double the cost of the turret punch press. “It’s a no-brainer that a combo machine will have an advantage over a punch only machine, but budgetary considerations often rule it out,” he says.
There is a challenge when it comes to combination machines. In the industry, there is an ongoing conversation over efficiency. Combining a turret punch press with a laser results can mean that half the machine is idle while the other half is working. According to Brady, “having a separate turret punch press and laser machine means they both can be 100 per cent utilized.” This is only a real problem when parts must be produced that require both punch and laser features. “Programming and coordinating these parts to run through two machines is much more difficult and problematic.”
Capabilities
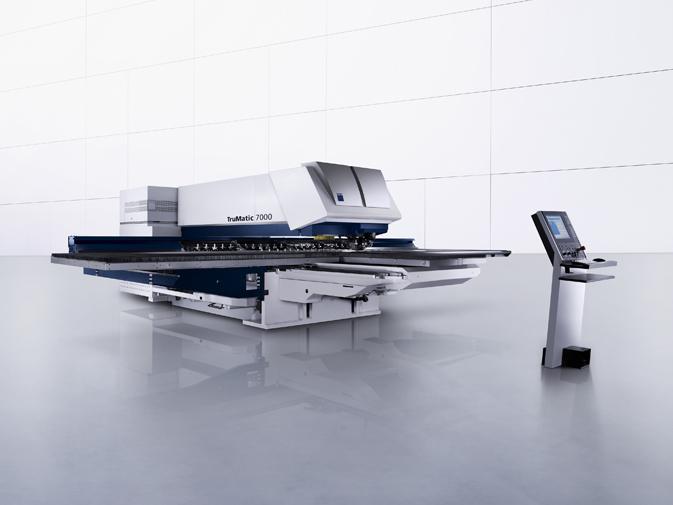
TRUMPF’s TruMatic 7000 gives you the best of both worlds. Offering scratch-free punching and high speed laser processing, the TruMatic 7000 features a 4kW laser and a punching head with a max stroke rate of 1200 1/min in the medium format. WWW.US.TRUMPF.COM
Systems are limited by the thickness of material that can be punched. However, modern punches can perform many functions in one machine that used to be done in multiple stations. “A turret punch system can do forming and special shapes, rolling, ribbing, offset, cutting, pincher wheel, and tapping,” says Caprio.
It’s all in the value added features, explains Brady. “Besides just punching and nibbling of flat parts out of sheet metal, the turret punch press is capable of producing many…features in sheet metal parts such as, part marking [logos and lettering], embossments, extrusions and tapping of holes, louvers and much, much more.”
SINGLE PUNCH SOLUTION
There is still a place for simple punch systems for shops requiring a dedicated punching tool to perform specific functions. “They are small and compact. They are less expensive. And furthermore, for the right type of application, medium sized light gauge runs, they do as good or better job,” says Todd Bryson, vice president of operations for Multicyl Inc.
The company manufactures air over oil presses used in punching applications among others. “So when you get into very high volume runs, or heavy stuff, ours might not be the right ones suited for it. But if you have medium volumes, light duty, there are all kinds of advantages to it. Ours would be good for long runs only if it is dedicated.
With volumes you are not going to do 10,000 parts a day, or two shifts per day with our punching machines. It is great for short runs because it is small and compact and inexpensive, so you’re not tying up a large expensive press.”The punching tool in the punches can be changed to suit the part being manufactured.
“It depends on what type of die you are using for your applications,” he says. “We certainly do have an option for quick changing. If we use unitized tooling for example. If you have a C-frame styled tooling, that can be changed out. That is the most common type tooling.”
About the Author
subscribe now
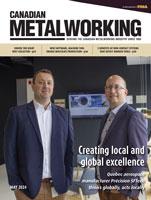
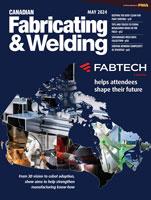
Keep up to date with the latest news, events, and technology for all things metal from our pair of monthly magazines written specifically for Canadian manufacturers!
Start Your Free Subscription- Industry Events
Automate 2024
- May 6 - 9, 2024
- Chicago, IL
ANCA Open House
- May 7 - 8, 2024
- Wixom, MI
17th annual Joint Open House
- May 8 - 9, 2024
- Oakville and Mississauga, ON Canada
MME Saskatoon
- May 28, 2024
- Saskatoon, SK Canada
CME's Health & Safety Symposium for Manufacturers
- May 29, 2024
- Mississauga, ON Canada