- FMA
- The Fabricator
- FABTECH
- Canadian Metalworking
Right-size your folding machine
Ferric Machinery’s Koen Verschingel talks benefits and features of folding machines
- November 20, 2023
- Article
- Fabricating
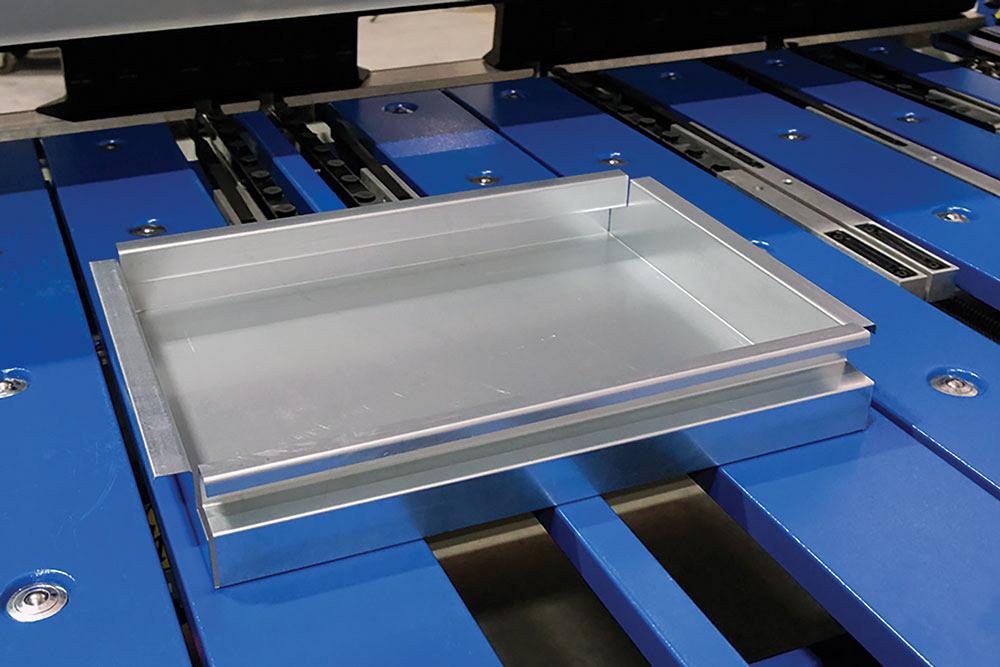
Consider the material you work with. If you don’t work with long materials or you need to bend thicker than ⅛ ga., a folder may not be suitable. Images: Ferric Machinery
Are you looking to invest in a new folding machine? Canadian Fabricating & Welding spoke with Koen Verschingel, owner of Ferric Machinery, Cambridge, Ont., about when a folding machine makes sense and how to right-size your investment for your applications. Here are some questions to help you get started.
Canadian Fabricating & Welding: When does it make sense to use a folding machine?
Koen Verschingel: If you manufacture parts for HVAC, roofing, siding, or cladding industries, folding machines will be a great addition to your shop. They excel at working with large sheets of light-gauge materials, which are commonly used in these industries. Since the sheets are able to rest on the table, unlike on a press brake, single operators can effectively work on large sheets without needing additional assistance.
CFW: What challenges or misconceptions do fabricators need to consider before investing in a folder?
Verschingel: Before investing in a folder, consider the material you work with. If you don’t work with long materials or you need to bend thicker than ⅛ ga., a folder may not be suitable.
Also, take note that not all folding machines are equal. Beam geometry plays a big role in what parts you will be able to make—some are steeper or shallower than others and this varies between machines and manufacturers.
Another important factor to consider is operator training and machine support. Choosing a good machinery supplier will help with this as they will provide you with training, routine maintenance, repairs if needed, and support to ensure a long, profitable lifespan for your machine.
CFW: With so many options available, how do fabricators right-size to ensure they are getting what they need?
Verschingel: When deciding which configuration your shop needs, the first thing to take into consideration is whether you want a manual or automatic machine. This decision mostly comes down to the material thickness you wish to bend, speed of production, budget, and desired size of machine.
Manual folders are great for working with very thin materials and are often used by roofers who bring them to job sites. They are the cheapest option, from upfront cost to maintenance, and are less prone to breaking down due to their lack of motorized parts. They are not only affordable, but reliable as well. The trade-off, however, is that they are less efficient and require more physical labour to operate. Every adjustment you need to make from the backgauge to folding beam height must be done manually, as well as the bends themselves.
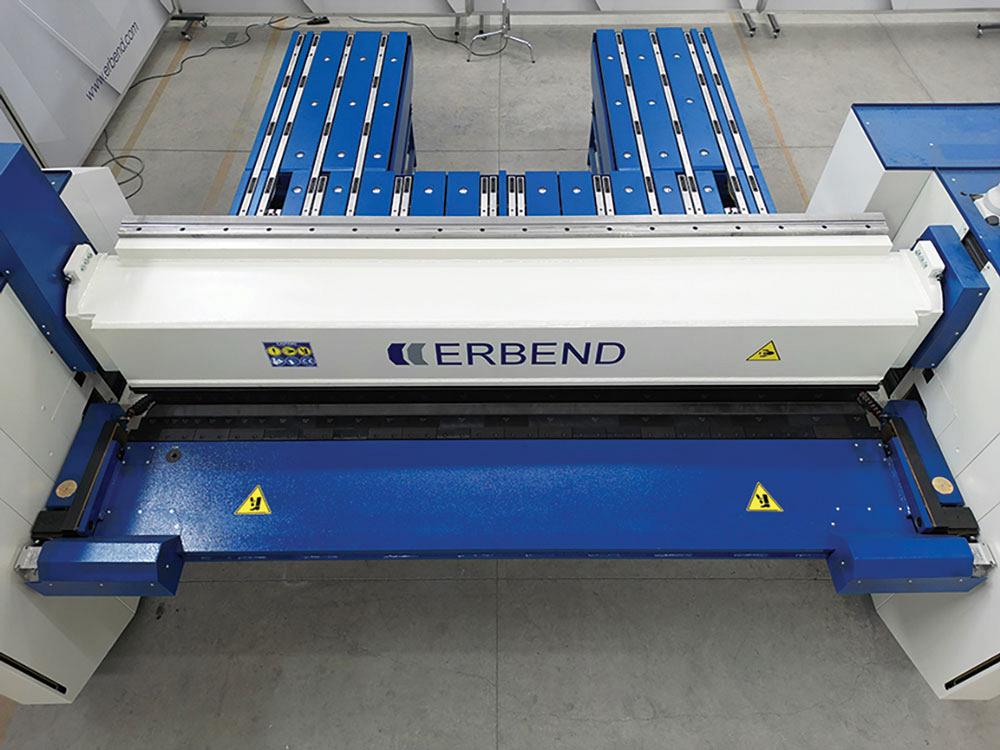
Combi up-down machines can rotate between tooling, but they also allow you to perform upward and downward bends without needing to flip your sheet each time.
Automatic folders improve on their manual counterparts with extra power to bend thicker materials and introduce the ability to program repeatable parts with CNC programming. They increase the speed of your production, can perform complex bends, and reduce the physical labour required by your operators. You will pay more for these machines from the initial purchase to maintenance, but for most shops, the efficiency outweighs the cost.
When purchasing an automatic folder, you will have another decision to make. Will you need a single-station, combi, or combi up-down variant? Combi machines offer the ability to quickly rotate between tooling setups, which can allow you to fold long profile parts and also box panel parts at the same time without changing tools. Combi up-down machines can rotate between tooling as well, but they also allow you to perform upward and downward bends without needing to flip your sheet each time.
CFW: What questions should fabricators ask themselves when exploring different options?
Verschingel: When looking at various options, the first questions you should ask are:
1. What is my budget?
2. What are my bending requirements like material thickness, length, angle, opening height capacity, and speed?
Everyone's needs are different and may require different tools. Determine what material thickness, length, and angles you need to fold and consider which features would be useful to your shop. For example, if you frequently perform both upward and downward bends on your parts, a combi up-down configuration may be beneficial to you.
3. What features are useful to me?
There are many features you can configure on your folding machine, but you may not need all of them. For example, you can choose to get a larger backgauge, sheet support tables, additional CNC software, etc. Before making a purchase, make sure you have researched what features you actually need so that you can make an informed purchase.
CFW: What features or specifications do fabricators need to pay attention to?
Verschingel: There are many features and specifications fabricators should pay attention to when purchasing a folding machine, these include the following:
- Rated capacity.
- Table size.
- Backgauge size.
- CNC control.
- Pneumatic quick-tool clamping systems for rapid tool setup.
- Up-down folding ability.
- Additional sheet support.
- A1 and A2 beam height adjustment.
- Servo clamping or eccentric cam shaft.
- How many rows of fingers you need for depth.
Ferric Machinery, www.ferricmachinery.com
subscribe now
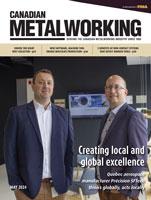
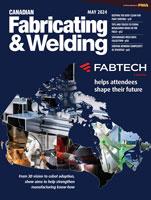
Keep up to date with the latest news, events, and technology for all things metal from our pair of monthly magazines written specifically for Canadian manufacturers!
Start Your Free Subscription- Industry Events
Automate 2024
- May 6 - 9, 2024
- Chicago, IL
ANCA Open House
- May 7 - 8, 2024
- Wixom, MI
17th annual Joint Open House
- May 8 - 9, 2024
- Oakville and Mississauga, ON Canada
MME Saskatoon
- May 28, 2024
- Saskatoon, SK Canada
CME's Health & Safety Symposium for Manufacturers
- May 29, 2024
- Mississauga, ON Canada