- FMA
- The Fabricator
- FABTECH
- Canadian Metalworking
Understanding the cut
Factors that affect the cost of cutting
- By Canadian Metalworking
- November 18, 2014
- Article
- Fabricating
Cutting metal with a band saw sounds easy.
Install the blade on the machine, vise the material and let the machine rip. Still, the actual process is much more of a science than an art. It begins with selecting the correct blade to achieve your goals while balancing variables such as material, machine style and condition, and even operator skill level.
Making the proper blade selection takes careful consideration and should be done with guidance from your blade partner.
However, prior to blade selection, it’s necessary to understand the anatomy and physics of a cut in order to affect the efficiency of the cutting process. There are several factors that affect band sawing efficiency, including tooth design, band speed, feed rates, vise loading, lubrication, the capacity and condition of the machine, and the material you are cutting.
This guide is intended to help you get started by understanding the basics.
HOW CHIPS ARE MADE
If you were to look at a blade cutting metal under a microscope, you would see the tooth tip penetrating the work and actually pushing, or shearing, a continuous chip of metal. The angle at which the material shears off is referred to as the “shear plane angle.” This is perhaps the single most important factor in obtaining maximum cutting efficiency.
Generally, with a given depth of penetration, the lower the shear plane angle, the thicker the chip becomes and the lower the cutting efficiency. The higher the shear plane angle, the higher the efficiency, with thinner chips being formed.
Shear plane angle is affected by material, band speed, feed, lubrication and blade design.
[gallery type="slideshow" link="none" ids="106994,106995"]
GULLET CAPACITY
Gullet capacity is another factor that impacts cutting efficiency. The gullet is the space between the tooth tip and the inner surface of the blade. As the teeth cut away the material during a cut, the chip curls up into this area.
A blade with the proper clearance for the cut allows the chip to curl up uniformly and fall away from the gullet. If too much material is cut away, the chip will jam into the gullet area causing increased resistance. This loads down the machine, wastes energy and can cause damage to the blade.
[gallery type="slideshow" link="none" ids="106996,106997"]
FEED
Feed refers to the depth of penetration of the tooth into the material being cut. For cost effective cutting, you want to remove as much material as possible as quickly as possible by using as high a feed rate/pressure as the machine can handle.
However, feed will be limited by the machinability of the material being cut and blade life expectancy.
The measured chip thickness will often be greater than the depth of tooth penetration.
[gallery type="slideshow" link="none" ids="106999,106998"]
This difference is known as “chip thickness ratio” and it will change depending upon the shear plane angle. The shear plane angle is a function of both the properties of the material you’re cutting, and the tooth tip rake angle. As the rake angle is increased, the shear plane angle will also increase. A dull tooth tip, or built up edge can have the effect of changing the rake angle.
Chip thickness will vary inversely with changes to the shear plane angle. For example, as rake angle is reduced (and, consequently, the shear plane angle is decreased) the measured chip thickness will increase.
How can you tell if you are using the right feed rate? Examine the chips and evaluate their shape and color.
BAND SPEED
Band speed refers to the rate at which the blade cuts across the face of the material being worked. This is usually stated as FPM (feet per minute) or MPM (meters per minute).
Faster band speeds can lead to faster cutting rates. However, band speed is restricted by the machinability of the material and ultimately heat produced by the cutting action. Too high a band speed or very hard metals produce excessive heat, resulting in reduced blade life.
How do you know if you are using the right band speed? Look at the chips; check their shape and color. The goal is to achieve chips that are thin, tightly curled and warm to the touch. If the chips have changed from silver to golden brown, you are forcing the cut and generating too much heat. Blue chips indicate extreme heat, which will shorten blade life.
[gallery type="slideshow" link="none" ids="107001,107002,107003"]
BEAM STRENGTH
When resistance grows due to increased feed rate or the varying cross section of the material being cut, tension increases on the back edge of the blade and decreases on the tooth edge. This results in compression, forcing the blade into an arc, producing cuts which are no longer square.
Beam strength is a blade’s ability to counter this resistance during the cutting process. A blade with greater beam strength can withstand a higher feed rate, resulting in a smoother, more accurate cut.
Beam strength depends on the width and gauge of the blade and the distance between guides, machine type, blade tension and the width of the material being cut. From a practical standpoint, use no more than ½ of the saw machine’s stated capacity. For harder materials, it is safer to work closer to the 1/3 capacity.
[gallery type="slideshow" link="none" ids="107004,107005"]
INCREASE BEAM STRENGTH – REDUCE COST/CUT
Here’s an example of how increasing beam strength can improve cutting economy. A customer needed to cut 3¼” squares of 4150 steel on a 1¼” blade width machine. The operator, trying to cut efficiently, placed three pieces side by side. The three squares measured 9¾” wide—well within the 14” machine capacity.
[gallery type="slideshow" link="none" ids="107006,107007"]
BEAM STRENGTH – RULE OF THUMB
Blade Width | Maximum Cross Section | ||
1” | 27mm | 6” | 150mm |
1-1/4” | 34mm | 9” | 230mm |
1-1/2” | 41mm | 12” | 300mm |
2” | 54mm | 18” | 450mm |
2-5/8” | 67mm | 24” | 610mm |
3” | 80mm | 30” | 760mm |
SEVEN WAYS TO MAXIMIZE BEAM STRENGTH
- Calculate the real capacity: A practical limit is ½ of the manufacturer’s stated machine capacity. Restrict harder materials to ⅓ capacity.
- Use a wider blade: A wider blade with a thicker gauge will withstand bowing, allowing for greater pressure and, therefore, higher feed rate.
- Reposition machine guides: Bring guides in as close as possible. The farther apart the guides, the less support they provide to the blade.
- Reduce stack size: By cutting fewer pieces, you can increase speed and feed rates for an overall improved cutting rate.
- Reposition odd-shaped material: Changing the position of odd-shaped material in the vise can reduce resistance and improve cutting rate. Remember, the goal is to offer the blade as uniform a width as possible throughout the entire distance of cut.
- Check for blade wear: Gradual normal wear dulls a blade. As a result, you cut slower, use more energy, and affect the accuracy of the cut.
- Check other limiting factors: Use the SAWCALC by LENOX computer program to determine the correct feed, band speed, and tooth pitch for the work you are cutting.
VISE LOADING
The position in which material is placed in the vise can have a significant impact on the cost per cut. Often, loading smaller bundles can mean greater sawing efficiency.
All machines have a stated loading capacity, but the practical level is usually lower,
½ to ⅓ as much, depending on the material being cut (harder materials are best cut at ⅓ rated capacity).
When it comes to cutting odd-shaped material, such as angles, I-beams, channel, and tubing, the main point is to arrange the materials in such a way that the blade cuts through as uniform a width as possible throughout the entire distance of cut.
The following diagrams suggest some cost effective ways of loading and fixturing. Be sure, regardless of the arrangement selected, that the work can be firmly secured to avoid damage to the machine or injury to the operator.
About the Author
subscribe now
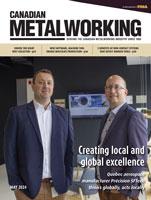
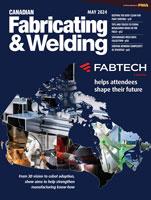
Keep up to date with the latest news, events, and technology for all things metal from our pair of monthly magazines written specifically for Canadian manufacturers!
Start Your Free Subscription- Industry Events
Automate 2024
- May 6 - 9, 2024
- Chicago, IL
ANCA Open House
- May 7 - 8, 2024
- Wixom, MI
17th annual Joint Open House
- May 8 - 9, 2024
- Oakville and Mississauga, ON Canada
MME Saskatoon
- May 28, 2024
- Saskatoon, SK Canada
CME's Health & Safety Symposium for Manufacturers
- May 29, 2024
- Mississauga, ON Canada