- FMA
- The Fabricator
- FABTECH
- Canadian Metalworking
Hand Held Deburring
Exploring options for efficiently cleaning up flat parts.
- By Doug Picklyk
- October 13, 2015
- Article
- Metal Finishing
There are many deburring, rounding and polishing options available to manufacturers for cleaning up metal parts. Options range from bead blasting and tumbling to belt grinding, abrasive machining, mechanical deburring and more.
When it comes to finding the most efficient hand held methods for deburring flat metal parts, shops often have operators using angle grinders to do the job. In deburring applications, the objective is to remove the sharp remnants left behind following cutting or punching operations, and the challenge—especially in flat part deburring where tolerances may be very tight—is removing the burrs without affecting the base material.
Most abrasive suppliers measure the effectiveness of their abrasive products by using the G Ratio, a measure of grams of the abrasive consumed (or wheel wear) versus the grams of base material removed.
Walter Surface Technologies also conducts a “Productivity Report” in which its products are tested and compared with competitors. “Factors we report on include removal rate and the efficiency of the wheel,” notes Stéphane Drainville, international product manager - tooling & power tools, with Walter Surface Technologies. “Productivity gains are measured by the lifespan of the product and the time it takes to finish the job.”
Ultimately cost savings add up when the lifespan of the abrasive is longer (fewer replacements required) and more material is being removed, both leading to time savings and reduced labour costs.
While these measures work well for abrasive grinding and cutting applications, deburring is a delicate task demanding burr removal without affecting the part’s dimensions.
“Effective time and consistent performance are the real issues with this application,” says John Thompson, national technical sales manager with PFERD USA.
“With the application of burr removal on flat stock material there are several factors that are different from simple stock removal. As this is an on-hand operation the human factor must also be considered,” says Thompson.
He adds that to test performance requires a consistent technique of the operator. “Consistent pressure, rate of travel and angle of surface contact is often more important than grit type. The proper procedure is pulling the deburring product.
“Directing a circular disc in a pulling direction, with rotation from the parent material over the burr and off the edge allows more control with less potential for kickback and risk of operator injury,” notes Thompson.
As for the best products to use for deburring operations, most recommend staying away from bonded abrasive wheels altogether. Designed for material removal, the wrong pressure, or a slip of the tool, by the operator can easily gouge or mar a metal surface. The common recommendation is to opt instead for a wire or nylon filament disk or brush.
And while G ratios are an effective way to analyze effectiveness of abrasives, it’s more difficult to get an accurate G ratio for a wire or nylon brush.
“Unlike a coated abrasive product, a wire brush by nature performs like a bead blast, removing impurities and burrs off of the surface without removing the base material,” notes Rick Hopkins product manager for welding and fabrication with Weiler Corp. He suggests a crimped wire brush for many deburring applications. These brushes allow for flexibility, and can be made more or less aggressive by altering trim length and/or gauge of wire used. The user should always select the proper brush based on the size and nature of the burr. “Because finish and tolerances are often critical, it is important to always choose the least aggressive brush required to do the job.”
Hopkins is familiar with a shop that manufactures custom knee braces and uses an automated machine for polishing and finishing flat metal parts, but it also has manual deburring applications. The lightweight frames are made from aluminum, so a wire brush solution was recommended because the size of the burrs was minimal and an abrasive would have been too aggressive.
Thompson at PFERD recommends the use of a wire bevel brush in a 4.5- or 5-inch diameter at a recommended maximum of 4,500 to 5,000 RPM. “The speed of the brush is critical,” he points out. “The correct speed recommended gives the best control for the operator with excellent burr removal and minimum surface adjustment.”
His second suggestion, which he recommends be used on stationary machine, although it can be used in an on-hand operation with care to speed and procedure, is the PFERD M-BRAD product that contains abrasive grain impregnated on a non-metallic filament.
Another common deburring product Hopkins points to is the carbide bur, a metal tool used in a handheld die grinding application, not likely used for flat part deburring.
“We’ve had end users who have converted from a carbide bur to one of our Bobcat Mini Flap Disks [an abrasive wheel that can be used for deburring and blending steel],” notes Hopkins. He cites one application that involves the bottom lip of a lawn mower deck—a relatively large part that’s punched, then stamped and formed, and the operator needed to remove the burr from the bottom edge.
“The client was using carbide burs and as a result was experiencing operator fatigue and the tools are more difficult to control, leading to a higher rate of failure,” says Hopkins. “In that specific application we went in and demonstrated our Bobcat Mini Flap Disk, and those absolutely did the trick.”
In the end, it’s the nature of the burrs being removed that will dictate the tools required. For most hand held flat part deburring the experts recommend wire or nylon filament products that will effectively remove burrs with the greatest user comfort and the least risk of damaging the final part.
About the Author
subscribe now
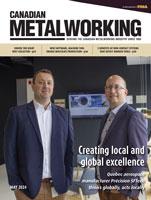
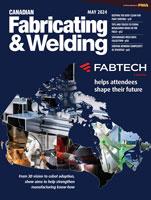
Keep up to date with the latest news, events, and technology for all things metal from our pair of monthly magazines written specifically for Canadian manufacturers!
Start Your Free Subscription- Industry Events
MME Saskatoon
- May 28, 2024
- Saskatoon, SK Canada
CME's Health & Safety Symposium for Manufacturers
- May 29, 2024
- Mississauga, ON Canada
DiPaolo Machine Tools Open House 2024
- June 4 - 5, 2024
- Mississauga, ON Canada
FABTECH Canada
- June 11 - 13, 2024
- Toronto, ON Canada
Zoller Open House & Technology Days 2024
- June 12 - 13, 2024
- Ann Arbor, MI