Associate Editor
- FMA
- The Fabricator
- FABTECH
- Canadian Metalworking
Salto’s business heats up
Northern Ontario heat treater services mining, agriculture, and forestry sectors
- By Lindsay Luminoso
- January 4, 2023
- Article
- Metal Finishing
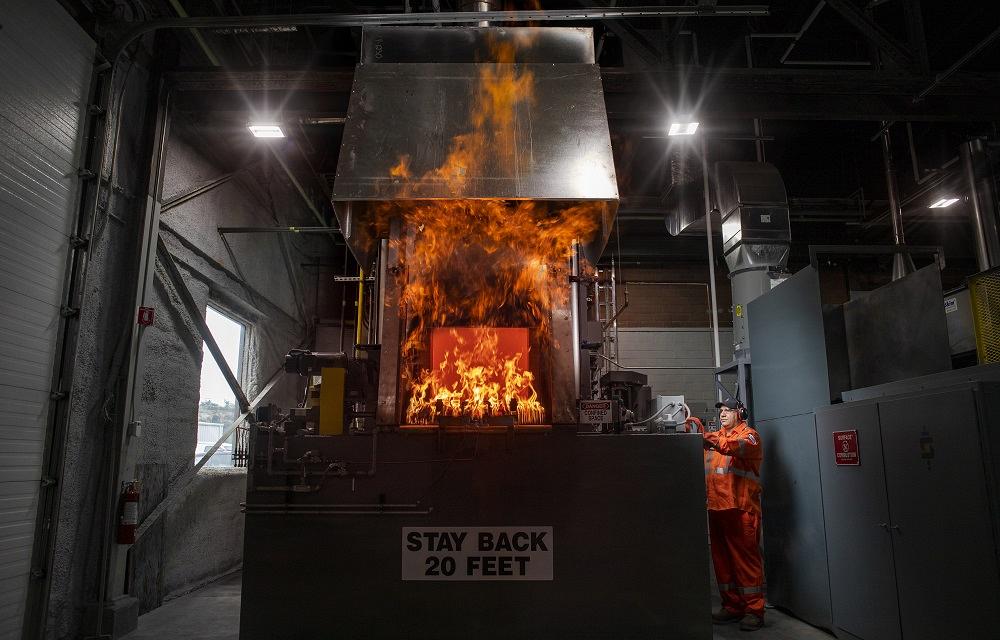
Salto’s custom-designed, fully automated IQ line is a furnace that can reach temperatures of 1,850 degrees F to surface harden drill rods for mining exploration. Images: Salto Heat Treating
You wouldn’t think that launching a new business in the middle of the pandemic would be a recipe for success, but Salto Heat Treating is proving this wrong.
The northern Ontario shop, located in Coniston just outside of Sudbury, opened its doors on May 4, 2020, and has been successfully providing heat-treating services to customers across Canada ever since.
“While Salto has only been open for the last 2 ½ years, I’ve been in the heat-treating industry for 30 years,” said Christophe Mehanna, general manager, Salto Heat Treating. “It’s always been my dream to run my own shop, and when I realized a great opportunity presented itself, I reached out to a good friend of mine, Felix Lopes Jr.”
Lopes Jr., president of Lopes Ltd., a Coniston-based steel fabricator, was approached by Mehanna to invest in a new heat-treating company in the city.
“Felix saw that this opportunity made a lot of sense,” said Mehanna. “So, he invested and that’s how it started. With my experience in heat treating and his vast experience running many successful industrial businesses, we spent over a year on the road looking for equipment and planning and designing a fully automated, state-of-the-art heat-treating facility.”
The Facility
Located in an industrial park, Salto employs eight people, including Mehanna; six are on the shop floor and two are in the office. It has 24,000 sq. ft. of floor space that has been meticulously designed with eight furnaces, including the shop’s custom-built, fully automated Integral Quench (IQ) line.
“It was very important for us to go after the latest technology to be able to provide the best production and quality standards that our customers have come to expect from us,” said Mehanna. “Felix was adamant that we have the best equipment with the latest technology. That’s why we decided to custom build our furnaces rather than just buy what was available on the market.”
The shop was able to custom build its IQ line in part because of the team’s extensive heat-treating experience.
Accuracy and uniformity are essential for good heat-treating practices and having equipment that could perform both to a high degree was necessary. The IQ line is highly automated and includes digital equipment and controllers. To meet surface smoothness requirements, the shop added probes and pyrometers inside the furnace to monitor the temperatures.
“The advantage of going digital is that we can remotely monitor everything about the system,” said Mehanna. “If there’s any error, the burner goes down, or the furnace troubleshoots, I get notifications on my phone. We couldn't do that with some of the other equipment on the market. I can receive emails updating me about our furnaces and I can fix or troubleshoot right from my laptop. I can have our automation engineers go in and fix any problems rather than having to go onto the shop floor in many cases, which makes fixes much quicker and more efficient.”
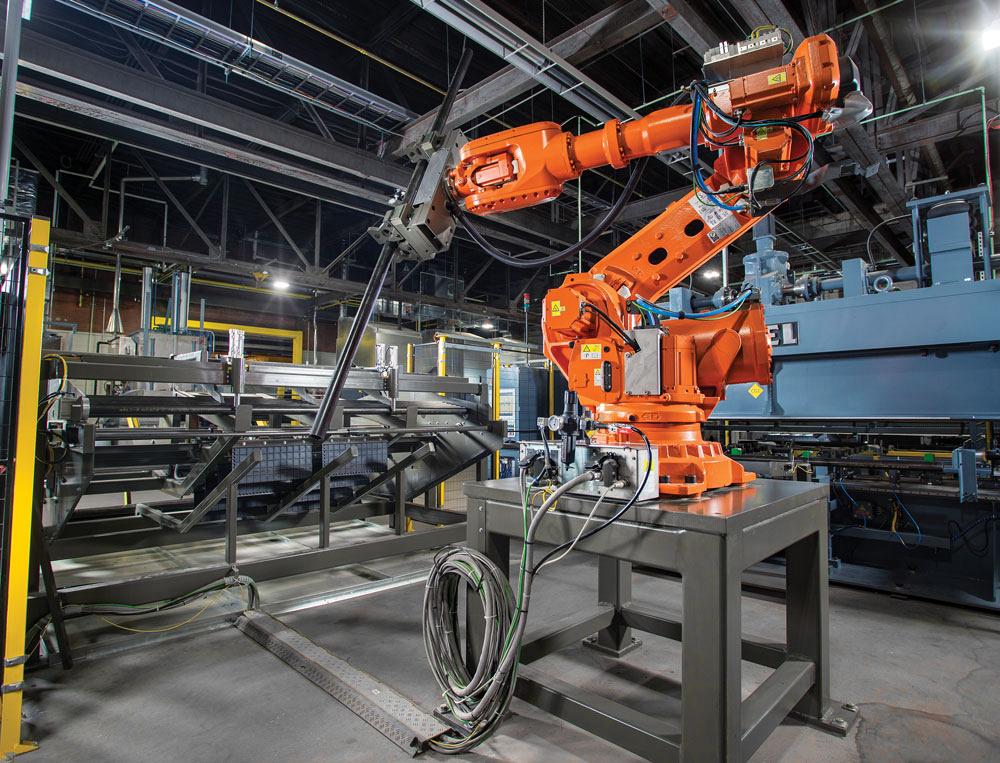
Mehanna and his team spent over a year on the road looking for equipment, planning, and designing a fully automated, state-of-the-art heat-treating facility.
The fully automated line serves its customers well and allows the shop to take on projects that its competitors might not be able to do.
“Our IQ line is very unique because of the customization we were able to put into it,” said Mehanna. “There are furnaces out there that are a lot bigger than ours, but most standard furnaces that shops are working with are a lot smaller than what we have.”
Salto is ISO 9001:2015 certified and a member of the Metal Treating Institute. Additionally, all of the company’s furnaces and probes are calibrated and certified. Mehanna noted that not all other heat treaters calibrate their furnaces, but at Salto, they ensure that when they say the furnace is 1,500 degrees F, that’s exactly what is it.
Heat-treating Services
The shop provides various heat-treating processes, including annealing, through hardening, case hardening, carburizing, air hardening, normalizing, stress relieving, high- and low-frequency induction hardening, along with cutting services and a metallurgy lab with a digital hardness tester and metallurgical analysis.
“There is a lot of variety in terms of what we can offer,” said Mehanna. “Upwards of 85 per cent is focused on the mining industry with the remainder in agriculture and forestry. With low-frequency induction hardening, our scanners can go up to 7 ft., whereas most can only do up to 3 ft. We are one of very few companies in Ontario that can do this.”
More recently, the company invested in a high-frequency induction scanner after a globally recognized customer requested it. While the team had no experience using the high-frequency scanner initially, they were able to lean on Mehanna’s experience with low-frequency scanners and learn with the help of metallurgists and the customer how best to use this new heat-treating device.
The rod induction systems are fully automated and outfitted with heat sensors to ensure that each rod reaches the exact same temperature.
“Uniformity is very important to provide quality heat-treating services,” said Mehanna. “With this we can ensure that from the first to the last rod, each is the same hardness.”
The shop’s custom-designed, fully automated IQ line is a furnace that can reach temperatures of 1,850-degrees F (1,010-degrees C) to harden different parts for mining exploration.
“While we have eight furnaces, the IQ furnace is the only one that does the hardening on all the different applications for us,” said Mehanna. “Once they are removed from the IQ furnace, we can put them in other furnaces for tempering and stress relieving, depending on part requirements.”
Most of the work that Salto undertakes is destined for through hardening, which is done in an atmosphere-controlled furnace, where parts are heated to an exact temperature and then quenched in oil, ensuring minimal warping and uniform properties to the parts. Through hardening is a process that hardens the part all the way through to the core. This process differs from case hardening, which tends to be a more cost-effective option with fast turnaround. Although it only provides hardening of the surface, it still delivers improved part or component wear resistance. What often dictates the type of hardening required is the material type. For example, through hardening only works on specific materials such as 4140 steel, whereas 8620 steel can only be case hardened.
Day-to-Day Operations
On any given day, Salto may have a variety of different parts coming through the doors, but one thing that remains the same is its commitment to a 24- to 48-hour turnaround. The day always starts with a safety talk and then the dedicated team begins loading parts into the baskets. Operating on the premise of organization and efficiency, the shop aims to create its schedule for the entire week ahead. However, with numerous tasks and jobs arising at various times, and to meet the tight turnaround and it’s own set standards, the team tackles whatever comes in right away.
“I can honestly say that in our few short years of operation, we have always been able to deliver on our promised time commitment,” said Mehanna. “And while it is challenging to find good employees, I’m blessed with the talented team we have here. Working in heat treating is my passion and I look forward to coming to work every day and seeing the team. Every day brings a new challenge and opportunity and that keeps us motivated.”
Working in the mining industry, Mehanna has seen significant changes in the parts that come in for heat treating over the years, and mining parts are often treated very differently than automotive or aerospace components. In recent years, there has been a push to make mining components that can be used more than once.
“The parts we see today are more advanced and are designed with a longer lifecycle, which means they need to be more durable,” he said. “Heat treating hardens the part so it can be used more than once while providing a longer life as opposed to being disposed of for not holding up to harsh conditions.”
While the shop has only been open for a few years, it has always expanded into new areas as customer demand dictates. “We are looking at investing in a pit furnace for drill rods that are used for blasting on highways rather than mining applications,” said Mehanna. “We see this as an area of opportunity and feel like right now, without the pit furnace, we are missing out on quite a bit of work. These furnaces are designed for longer rods, up to 12 ft. long, and right now, we just don’t have the capacity to handle something of this length. Fortunately, we are always growing and expanding so I anticipate this will be something we can offer in the future.”
Associate Editor Lindsay Luminoso can be reached at lluminoso@canadianfabweld.com.
Salto Heat Treating, saltoheattreating.ca
About the Author
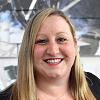
Lindsay Luminoso
1154 Warden Avenue
Toronto, M1R 0A1 Canada
Lindsay Luminoso, associate editor, contributes to both Canadian Metalworking and Canadian Fabricating & Welding. She worked as an associate editor/web editor, at Canadian Metalworking from 2014-2016 and was most recently an associate editor at Design Engineering.
Luminoso has a bachelor of arts from Carleton University, a bachelor of education from Ottawa University, and a graduate certificate in book, magazine, and digital publishing from Centennial College.
subscribe now
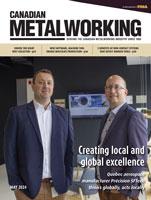
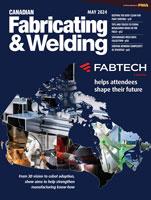
Keep up to date with the latest news, events, and technology for all things metal from our pair of monthly magazines written specifically for Canadian manufacturers!
Start Your Free Subscription- Industry Events
Automate 2024
- May 6 - 9, 2024
- Chicago, IL
ANCA Open House
- May 7 - 8, 2024
- Wixom, MI
17th annual Joint Open House
- May 8 - 9, 2024
- Oakville and Mississauga, ON Canada
MME Saskatoon
- May 28, 2024
- Saskatoon, SK Canada
CME's Health & Safety Symposium for Manufacturers
- May 29, 2024
- Mississauga, ON Canada