Contributing Editor
- FMA
- The Fabricator
- FABTECH
- Canadian Metalworking
Canadian sculptor wins Metal My Way competition
Kevin Stone’s fire-breathing dragon awes judges for grand prize
- By Rafael Guerrero
- February 2, 2023
- Article
- Welding
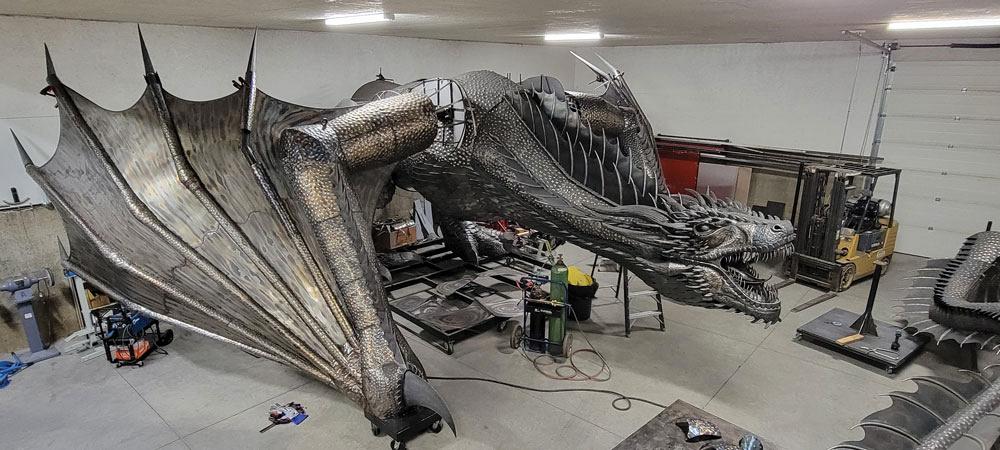
Canadian sculptor Kevin Stone’s metal sculptures tend to be large in scale and ambition, attracting attention from people everywhere. One example is his contest-winning “Game of Thrones” dragon. Images: Kevin Stone
Metal Supermarkets recently announced the six winners of its 10th Metal My Way contest.
Showcasing the versatility and craftmanship of metalworking, fabricating, and design, the competition recognized winners in five categories along with one grand prize winner. The contest was open to both professionals and hobbyists alike, with entrants invited to submit a photo or video of their innovative metal-made projects for the opportunity to win prizes and have their projects recognized. The five categories included vehicle projects, artistic and design projects, furniture and home projects, industrial or shop projects, and knife projects. The winning submissions were chosen based on criteria such as complexity, detail, intricacy, uniqueness, creativity, craftmanship, quantity of metal used, and ingenuity.
This year, 1,193 submissions were received internationally from Canada, the U.S., and England. This year’s grand prize winner was Chilliwack, B.C.-based metal sculptor Kevin Stone for his recently completed “Life-Sized, Fire-Breathing Dragon,” or what he calls his “Game of Thrones” dragon.
“Once again, we are in awe of the talent and creativity exhibited by Metal My Way submissions,” said Stephen Schober, president and CEO of Metal Supermarkets. “Our grand prize winner, Kevin, went above and beyond with his life-sized dragon and was awarded an EV 88 portable benchtop KAMA bandsaw. The other winning projects in their respective categories were remarkable as well. We love putting on this contest every year to showcase the skill of the local craftspeople that visit Metal Supermarkets and turn ordinary metal into something incredible.”
Stone built his first metal sculpture, a 6-ft.-tall gargoyle, in 2003.
It was the first project that shifted his focus away from commercial stainless steel fabrication.
“I left the ferry industry and got into commercial stainless. I was doing food and dairy equipment and breweries and mostly sanitary stainless fabrication,” Stone said. “Through one of the companies I was doing my stainless work with, they asked me to build a sculpture. I started my first sculpture using just scrap around the shop.”
In the two decades since, Stone, 53, has improved upon his skills and built several metal sculptures, with each one challenging size, scope, and ambition. Take, for example, three sculptures either recently completed or in the works: a 55-ft.-long Tyrannosaurus rex; his competition-winning dragon; and a 6-ft.-tall aluminum bust of billionaire Elon Musk.
Much of his work happens at his 4,000-sq.-ft. shop, where he likes to use Miller Electric welding machines, KMS Tools products, English wheels, power hammers, metal shrinker/stretchers, and planishing hammers.
Recently, Stone discussed his latest projects, why he loves working with stainless steel, and his artistic influences.
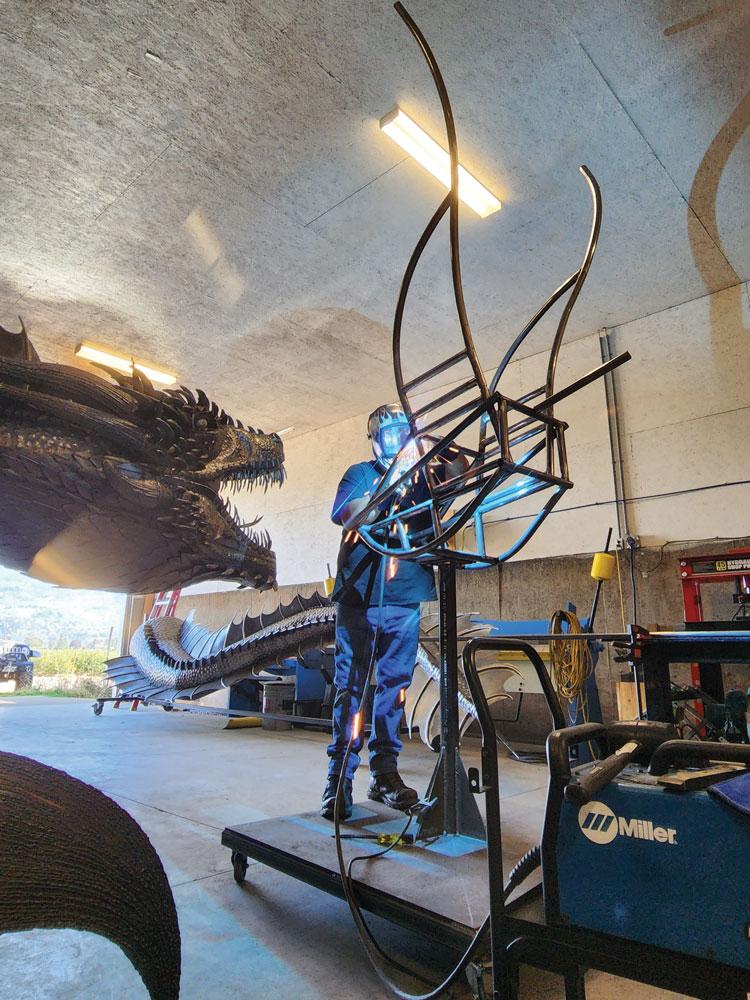
Stone has been in the trades for about 30 years. Along with metal arts, Stone has worked in the ferry and commercial stainless steel industries and on hot rods.
Canadian Fabricating & Welding: How big are some of these sculptures of yours?
Stone: An older coiling dragon, head to tail, was 85 ft., made in mirror-polished stainless steel. He was 14 ft. wide with the coils; 14 ft. tall; and coiled, he stood just under 40 ft. long. That dragon weighed about 9,000 lbs.
The “Game of Thrones” dragon is 55 ft. long from head to tail. Its wings are folded, but if its wings were unfolded it would be over 90 ft. It also shoots fire as well. I have a propane puffer system that I control with remote control and a small remote-controlled computer to actuate all the valves inside. It can shoot about a 12-ft. ball of fire about 20 ft. from his mouth. It’s a pretty cool fire system. The wingspan, folded, is about 40 ft. wide. His head is only about 8 ft. off the ground, but his tail goes up 35 ft. in the air.
The T. rex is 55 ft. long and weighs about 17,000 lbs. It’s mirror-polished stainless steel. The dragon is made of steel but has been heat-treated and coloured with heat. The colouring is done with a torch, so it has lots of different dark colours and a little bit of rainbow colours because of the torching.
CFW: How did this “Game of Thrones” dragon originate?
Stone: I got asked, “I want one of these eagles. Can you make me one?” And I said, “Sure.” He goes, “I want it this big; I want it in my roundabout.” When we got to talking, I told him, “I can build you anything you want.” He thought about it, then got back to me. “Can you build a big dragon? Like a big ‘Game of Thrones’ dragon?” And so, that’s where the “Game of Thrones” dragon idea came from.
I was posting about that dragon on social media. Then a rich entrepreneur in Miami saw a dragon of mine on Instagram. He called me saying, “I want to buy your dragon.” I told him, “Well, it’s actually a commission and it’s not for sale. However, I have a big falcon I've been sitting on. You could buy that if you want.”
So, I sent him pictures of the falcon I had built, and he loved it. We negotiated a price, and he purchased my falcon and made arrangements to have it shipped out to his gallery in Miami. He has an amazing gallery. It was really an awesome opportunity for me to have my sculpture in an amazing gallery for an amazing client.
CFW: How long does it take to do these projects?
Stone: The “Game of Thrones” dragon, I worked on it for a year solid. And then it was in limbo for eight to 10 months. I did a little bit here and there to have some progress going. But now we’re just finishing it up. The total time it took to build that dragon was about 16 to 18 months.
CFW: Why is it that so many of your projects are animals and creatures?
Stone: It's what people want. I'll build anything, from an Elon Musk face to a dragon to a bird to an abstract sculpture. I think I'm capable of meeting any challenge. I like to be challenged. It seems the more difficult the sculpture is, the more interested I am in making it.
CFW: What is it about stainless steel that has made it your go-to for most of your sculptures?
Stone: Obviously, the beauty of it. It looks like chrome when it's finished, especially a polished stainless steel piece. My initial idea when building all these sculptures was to have them in casinos and big, outdoor commercial spaces where they could have water fountains. I envisioned these sculptures to be on display in water and where they wouldn’t rust and last forever.
The other thing is scale. I'm trying to build on a scale that is larger than anyone else's. Make those monumental outdoor pieces that garner people’s attention and become a focal point. I wanted to do larger-than-life stainless steel pieces that are beautiful and have them as landmark pieces in the outdoors.
CFW: What's something that might surprise people about your work?
Stone: A lot of people ask if these are all designed on computers. No, it's all coming out of my head. I just look at pictures and I design the engineering aspect of it; the structural strength of it based on my experiences. My experience in the trade has given me an in-depth knowledge of how to engineer things.
When people ask me if I have a computer table or [CNC] plasma table or something for cutting, I say, “No, everything is cut uniquely by hand.” I think that is what makes my work unique.
I recommend anyone interested in getting in the metal arts to get into the metal shaping aspect of the auto industry; learn how to make panels and beat panels into shape and things like that. That's life-changing knowledge when you learn how to shape metal.
Also, learn how to draw. Drawing not only teaches you how to look at things and draw the lines and figure out what you’re going to build, it also helps you visualize 3D shapes. It's going to help with your vision of shaping metal and figuring out the complicated pieces.
Contributing Editor Rafael Guerrero can be reached at rguerrero@thefabricator.com.
Kevin Stone, www.metalanimation.com.
Other Metal My Way contest winners include:
- Best Vehicle Project: “Tom Thumb Locomotive Reproduction,” by Richard Weber, Indianapolis, Ind.
- Best Artistic and Design Project: “Saskatchewan-inspired Metal Headdress,” by Jennifer Phillips, Edmonton, Alta.
- Best Furniture and Home Project: “Tudor Wall Lights,” by Eric Moebius, Waukesha, Wis.
- Best Industrial or Shop Project: “Model Steam Engine,” by Rick Redfield, Waukesha, Wis.
- Best Knives Project: “Spartan Sword,” by John Simons, Indianapolis
Alongside title sponsor Metal Supermarkets, the contest is sponsored by Cosen Saws, Swift-Cut, Space Aid Manufacturing, and OMAX.
For photos of the winning submissions and additional information on Metal My Way, visit metalmyway.com. Details for next year’s contest will be available soon.
About the Author
subscribe now
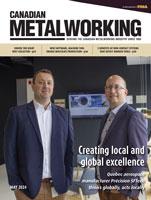
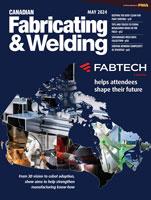
Keep up to date with the latest news, events, and technology for all things metal from our pair of monthly magazines written specifically for Canadian manufacturers!
Start Your Free Subscription- Industry Events
Automate 2024
- May 6 - 9, 2024
- Chicago, IL
ANCA Open House
- May 7 - 8, 2024
- Wixom, MI
17th annual Joint Open House
- May 8 - 9, 2024
- Oakville and Mississauga, ON Canada
MME Saskatoon
- May 28, 2024
- Saskatoon, SK Canada
CME's Health & Safety Symposium for Manufacturers
- May 29, 2024
- Mississauga, ON Canada